Аппарат для сварки сосудов
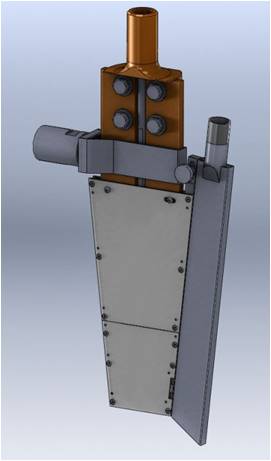
(стоимость зависит от характеристик и комплектации оборудования)
В стоимость оборудования входит:
– пуско-наладка
– отработка техпроцесса (по договоренности)
Гарантия на поризводимое оборудование 1 год.
Применение установки для сварки варочных сосудов :
Автоматическая установка ТОМ-85 предназначена для сварки емкостей объемами от 50 до 350 литров*. Сварка кольцевого шва проходит с применением разжимного подкладного кольца. Кольцо формируется из шести сегментов путём поочередного пневматического развода элементов. За счет пневматического усилия, значительно улучшается сварной стык обеспечивая равномерность горения дуги и глубину провара.
Принцип работы установки:
Данный сварочный вращатель включает в себя устройства, позволяющие полностью синхронизировать порядок включения (отключения) всех составных механизмов. Рабочему требуется только устанавливить заготовку выбрать типоразмер и нажать кнопку «Пуск».
Оператор надевает обечайку на специализированную оправку с пневматическими разжимами;
Оператор нажимает педаль для разжатия пневмоцилиндров и надевает донышко;
Подводит “заднюю бабку” и в ручном режиме настраивает горелку на нулевую отметку шва;
На пульте управления, выбирается автоматический режим и нажимается кнопка “Пуск”;
Начинается процесс сварки кольцевого шва;
После окончания сварки вращение прекращается, оператор отводит “заднюю бабку” и нажимает кнопку “Стоп” для сброса изделия.
Работа на установке позволяет полностью исключить влияние человеческого фактора на качество продукции.
Технические характеристики*:
Тип стационарный
Грузоподъемность, кг 50
Габариты свариваемых узлов, мм:
– диаметр 654…800
– длина 346…892
Частота вращения детали, об/мин: 0,03…0,5
Крепление деталей – специальные оправки и подвижная задняя бабка
Направление вращения шпинделя реверсивное
Токоподвод через вал патрона
Ход горизонтального перемещения задней бабки, мм 900
Регулирование скорости вращения шпинделя плавное
Перемещение задней бабки в ручном режиме
Крепление устройства для сварки специальная стойка со струбциной
Величина вертикального перемещения стойки, мм 450
Величина горизонтального перемещения стойки, мм 250
Напряжение питания, переменное, В 220
Потребляемая мощность, КВт, не более 0,5
Габариты установки, мм, не более:
– длина 3200
– ширина 1200
– высота 2000
Масса установки, кг, не более 690
*Представленные технические характеристики дорабатываются под конкретное техническое задание заказчика, возможны разные степени автоматизации процесса, характеристики сварочного оборудования, соответственно стоимость оборудования варьируется как в большую, так и в меньшую сторону.
Для получения технико-коммерческого предложения требуется составить техническое задание, направить чертеж изделия или связаться с менеджерами нашей организации. Адреса и телефоны указаны на нашем сайте в разделе Контакты.
Похожие прокты:
Источник
Комплекс для автоматической сварки сосудов
Информация об изделиях
Диаметр изделия, мм | 1000 – 2500 (3000) |
Максимальная масса изделия, тонн | до 60 |
Длина изделия, м | до 10 |
Толщина изделия, мм | 30-110 |
Процесс сварки | Плавящимся электродом под флюсом |
![]() Общий вид изделия |
Техническое описание оборудования
Модели оборудования, представленные в данном описании, являются предварительными. Окончательный вид оборудования может отличаться от представленного.
Общий вид сварочной установки
Комплекс оборудования для автоматической сварки внутренних и наружных кольцевых и продольных швов состоит из следующих основных единиц:
• Комплекс дуговой сварки на базе сварочной колонны ИТС КС 4х3 с оборудованием для сварки плавящимся электродом под флюсом;
• Опорный роликовый вращатель ОВРП-60Т (специального исполнения);
• Механический антидрейф (опция).
НПФ «ИТС» оставляет за собой право вносить технические изменения в оборудование, с гарантией обеспечения заявленных функциональных возможностей.
Более подробная информация и состав оборудования в соответствии с нижеследующим описанием.
Комплекс дуговой сварки на базе сварочной колонны ИТС КС 4х3
• Колонна сварочная ИТС КС 4х3
Колонна состоит из вертикальной стойки, горизонтальной балки, блока управления колонной, электрической тележки, электроповорота вертикальной колонны, пневмотормоза, блокировочного устройства.
Высокое качество материала, из которого изготовлено оборудование и точность изготовления гарантируют долгий срок службы.
Подъемное устройство расположено на верхнем конце вертикальной стойки, управляется электродвигателем переменного тока через редуктор с червячной передачей.
В крайнем нижнем и верхнем положениях горизонтальной балки включается механический ограничитель, обеспечивающий безопасную работу.
Также существует противоскользящее устройство, предотвращающее падение горизонтальной балки.
Перемещение горизонтальной балки, поворот вертикальной стойки осуществляется через пульт дистанционного управления, с помощью которого можно управлять скоростью перемещений, с отображением параметров на дисплее.
Вертикальная стойка установлена на опорно-поворотном подшипниковом узле таким образом, что горизонтальная балка располагается на одной оси с изделием.
Вертикальная стойка | |
Рабочий диапазон перемещения по вертикали, м | 4 |
Макс, высота горизонтальной балки А (с тележкой), мм | 5150 |
Мин. Высота горизонтальной балки А (с тележкой), мм | 1150 |
Общая высота D (с тележкой), мм | 6600 |
Скорость подъема, м/мин. | 0,7 |
Горизонтальная балка | |
Рабочий диапазон перемещения по горизонтали, м | 3 |
Макс. выдвижение G, мм | 3650 |
Мин. выдвижение G, мм | 650 |
Максимальная грузоподъемность, кг | 350 |
Макс нагрузка на конце балки, кг | 200 |
Скорость горизонтального перемещения, м/мин. | 0,15-2,5 |
Тележка c электроприводом | |
Расстояние между рельсами К (от центра до центра), мм | 2070 |
Длина, ширина, высота L, О, Н, мм | 2550x2500x630 |
Расстояние между колесами тележки М, мм | 2000 |
Скорость перемещения, м/мин. | 0,25-2,5 |
• Головка сварочная АДФ-1000 С6/3
Головка дуговой сварки кольцевых и продольных швов включает в себя:
• привод (мотор-редуктор) подачи проволоки;
• правильно-подающее устройство;
• правильное устройство;
• мундштук-токоподвод;
• кассетное устройство, установленное на тормозном устройстве (условно не показано);
• лазерный светоуказатель;
• исполнительные механизмы следящей системы тактильного типа;
• бункер для флюса с устройствами подачи и уборки флюса.
Технические характеристики | |
Номинальный сварочный ток (при продолжительности включения ПВ = 100%), А | 1000 |
Диаметр электродной проволоки, мм | 2…4 |
Регулирование скорости подачи проволоки | Плавное |
Минимальный диаметр изделия (при сварке внутри), мм | 1000 |
В комплект поставки включен сменный мундштук для сварки под флюсом изделий толщиной до 200 мм. Применение зауженной разделки (минимальный наклон 4° на сторону, 8° суммарно) позволяет существенно снизить время сварки и расход сварочных материалов. | ![]() |
• Система слежения по стыку
• Система видеонаблюдения (опция)
• Система подачи и сбора флюса с вакуумным насосом
Поставляемое флюсовое оборудование обеспечивает подачу флюса в течение длительного срока работы установки, что обеспечивает непрерывный процесс сварки.
Система подачи и рециркуляции флюса для данного комплекса состоит из: высокопроизводительного вакуумного насоса (ВН), фильтра сепаратора, с промежуточным бункером принудительной подачи флюса на головке и баком питателем на 90 литров.
Флюс засыпается в бак питатель (3). Вместимость бака составляет 90 литров. Флюсовый бак-питатель (3) представляет собой сосуд, работающий под давлением,
и служит для хранения, подогрева, а также подачи флюса в бункер (1). В нижней части бака-питателя встроен датчик уровня флюса и расположены два тепло электронагревателя, прикрытые опорой.
Тепло электронагреватели (ТЭНы) подогревают флюс, что препятствует его слипанию и способствует беспрепятственной подаче к месту сварки.
Диапазон температур нагрева флюса составляет 50…100°С, при этом максимальная температура нагрева ТЭНов составляет 250°С.
ТЭНы снабжены тепловой изоляцией и термометрами. Под давлением флюс поступает в промежуточный бункер (1) небольшого объема, который находится на головке. Во время сварки флюс высыпается под собственным весом в зону горения дуги.
Мощный ВН (2) создает разряжение в магистрали сбора флюса, и весь не расплавившийся флюс засасывается через сопло и поступает в сепаратор (4).
Когда уровень флюса в баке (3) достигает минимального значения (равное примерно 1 мешку флюса), у блока управления загорается сигнальная лампа.
Оператор открывает клапан сепаратора (4) и собранный флюс вновь поступает в бак питатель, где смешивается с новым.
Система включает в семя все необходимые шланги, клапана. Воздух, прошедший через систему поступает в пылевой фильтр (5) и выбрасывается в цех.
• Система подготовки (осушки) воздуха. (Опция)
• Источник питания MILLER SubArc DC 1250
• Единый пульт управления
• Обратные сварочные кабели
• Опорный роликовый вращатель ОВРП-60Т (специального исполнения)
Вращатели сварочные роликовые компании ИТС, предназначены для установки и вращения цилиндрических изделий (нефтяные резервуары, цистерны, котлы)
различных диаметров со сварочной скоростью при автоматической, полуавтоматической и ручной электродуговой сварке.
Плавная установка расстояния между роликами под требуемый диаметр свариваемого изделия осуществляется вручную, посредством ШВП.
Вращатель состоит из приводная и холостой секции. Максимальная нагрузка на вращатель (одна приводная + одна холостая) – 60 тонн.
Роликовые опоры установлены на рельсовые тележки для возможности быстрого регулирования в зависимости от длины свариваемого изделия
Технические характеристики | |
Грузоподъемность (общая), кг | 60 000 |
Диаметр изделия, мм | 800-3300 |
Размер роликов (диаметр х ширина), мм | 500 х 250 |
Скорость вращения, мм/мин | 100-1000 |
• Механический антидрейф (опция)
Роликовые опоры оснащены устройством фиксации опоры к головке рельса, что обеспечивает надежное крепление опор для предотвращения смещения во время сварки. | ![]() |
Источник
В этой статье мы разберемся что такое плазменная сварка сосудов и проведем ее сравнение с популярной TIG-сваркой. Для начала обратимся к истокам. Львиную долю продукции предприятий химического машиностроения и производителей оборудования для пищевой промышленности в том или ином виде составляют сосуды, работающие под давлением. К материалам, используемых для производства данных конструкций, часто предъявляются повышенные требования к коррозионной стойкости, часто при наличии агрессивных сред. В то же время вещества, что находятся в подобных сосудах, могут иметь рабочий диапазон температур от 200 до 600 °С.
Подбор подходящей стали
Исходя из таких требований, наиболее оптимальным является применение в качестве основного материала сосуда коррозионостойких хромоникелевых сталей аустенитного класса. На постсоветском пространстве наиболее распространенной маркой стали является 12Х18Н10Т, которая в западных странах более известна как AISI 304.
Сварка сталей аустенитного класса, как известно, может быть связана с определенными трудностями: при использовании неподходящей схемы нагрева способа сварки, возможно образование холодных (кристаллизационных) трещин. Также большой проблемой может быть выгорание легирующих элементов (хрома и никеля), что приводит к снижению коррозионной стойкости. Если срок эксплуатации конструкции более 20 лет, то выгорание легирующих элементов может привести к межкристаллитной коррозии через десятилетия после отгрузки с завода.
Требования к сварному шву
Исходя из всех вышеизложенных особенностей, способ сварки должен обеспечивать: высокие механические характеристики (как следствие, мелкозернистую структуру металла), отсутствие выгорания легирующих элементов. Также при изготовлении оборудования для пищевой отрасли есть специфические требования к геометрическим размерам сварного шва – обратный валик должен быть минимальным или отсутствовать. Это связано с тем, что процесс сварки обычно производится с внешней стороны сосуда, и как следствие, обратный валик находится внутри сосуда. В случае, если валик имеет большую высоту, пищевые продукты в небольших количествах могут сосредотачиваться и задерживаться возле него. В последствии, при промывке этой емкости, пищевые продукты в данном месте почти не удаляются, и по окончании своего срока годности, могут испортить уже новые загружаемые продукты.
Именно для обеспечения этих требований используют TIG Cold Wire – способ сварки (сварка неплавящимся способом с подачей присадочной проволоки — ИНп). Сварка этим способом позволяет обеспечить сварному шву оптимальный обратный валик, способствует минимизации выгорания легирующих элементов. Также с присадочной проволокой возможно введение дополнительных элементов-аустенизаторов структуры стали. Но у способа есть и недостатки: скорость сварки в таком случае достаточно низкая: 150-300 мм/мин, а из-за «мягкости» режима (соотношения вложенной энергии в объем металла и времени ее воздействия на него) размер зерен становиться большим (т. н. «крупнозернистая» структура), что несколько снижает механические характеристики сварного шва.
Плазменная сварка сосудов
В последнее время большое распространение плазменная сварка – способ, в котором источником тепла для процесса является плазменная дуга. Она позволяет нивелировать вышеизложенные недостатки ИНп способа сварки.
Основной технологической особенностью плазменной сварки является феномен, названный впоследствии процессом сварки «в замочную скважину» (англ. Key hole welding). Весь феномен состоит в том, что во время сварки поток плазменной дуги изначально образует в свариваемой заготовке сквозное отверстие, вокруг которого находится расплавленный металл. При последующем перемещении плазменной дуги расплавленный метал, который находится позади нее, под действием различных сил смыкается и образовывает единую сварочную ванну.
Сильные стороны
Аппараты для плазменной сварки имеют ряд полезных свойств и особенностей:
1. Обеспечение полного проплавления заготовок до 8 мм без разделки кромок, за один проход:
а) Плазменная сварка стали 12Х18Н10Т толщиной 8 мм, один проход без разделки
б) TIG- сварка стали 12Х18Н10Т толщиной 8 мм, четыре прохода с разделкой:
- угол раскрытия кромок 60°, притупление 3 мм.
2. Наличие значительно меньших остаточных деформаций вследствие меньшего тепловложения в заготовку
3. Большая производительность сварки
4. Плазменная сварка сосудов обеспечивает более высокие механические характеристики соединений, так как образовывает более мелкозернистую структуру.
Источник
Требования к технологии изготовления сосудов, работающих под давлением
Контроль изготовления, монтажа, эксплуатации, ремонта и реконструкции опасных технических устройств возложен на Федеральную службу по экологическому, технологическому и атомному надзору России (Ростехнадзор). Имеется несколько групп опасных технических устройств: подъемно-транспортное оборудование (ПТО); металлургическое оборудование (МО); газовое оборудование (ГО); оборудование химических, нефтехимических, нефтеперерабатывающих и взрывопожароопасных производств (ОХНВП); нефтегазодобывающее оборудование (НГДО); горнодобывающее оборудование (ГДО); оборудование для транспортировки опасных грузов (ОТОГ).
Сосуды, работающие под давлением, относятся к котельному оборудованию (КО). Требования Ростехнадзора к изготовлению, монтажу и ремонту для этого вида устройств изложены в Правилах устройства и безопасной эксплуатации сосудов, работающих под давлением. С точки зрения производства сварочных работ наиболее полно требования изложены в отраслевом стандарте ОСТ 26291 —94 «Сосуды и аппараты стальные сварные. Общие технические условия».
В соответствии с этими требованиями для сосудов в зависимости от условий эксплуатации (температура, давление, характер среды) регламентированы марки сталей, способы сварки, сварочные материалы. Достаточно подробно сформулированы требования к сборке соединений под сварку, предварительному подогреву и последующей термической обработке. В сосудах при сварке обечаек и труб, приварке днищ разрешено использовать только стыковые соединения с полным проплавлением. Угловые и тавровые соединения (с полным проплавлением) допускается применять при приварке штуцеров, люков и плоских днищ. Таким образом, ремонт сосуда путем наложения заплат недопустим. Нахлесточные соединения можно применять только на опорных элементах и закрепляющих кольцах. Сварные швы следует располагать так, чтобы их можно было проконтролировать визуально и с помощью физических методов неразрушающего контроля (ультразвук, радиография и т. д.).
Все 100 % сварных швов сосудов подлежат визуальному и измерительному контролю. Радиографическому и/или ультразвуковому контролю подлежат от 10 до 100 % швов в зависимости от условий эксплуатации сосуда. С их помощью выявляют внутренние дефекты — поры, трещины, включения, непровары. Недоступные для этих видов контроля швы подвергают цветной и магнитопорошковой дефектоскопии.
Кроме этого, при изготовлении сосудов должны быть выполнены контрольные сварные соединения, воспроизводящие одно из стыковых соединений сосуда, определяющее его прочность. Из этого соединения вырезают образцы для проведения механических испытаний и определения механических свойств. Если сосуд изготавливают из хромомолибденовых сталей (12ХМ, 15Х5М), из аустенитных или аустенитно-ферритных сталей, то надлежит проводить и металлографические исследования. В этих же случаях необходимо провести стилоскопирование шва — определение содержания основных легирующих элементов в сварном шве.
В дополнение к этому на сварных соединениях из хромомолибденовых сталей необходимо провести контроль твердости металла шва и околошовной зоны, а соединения аустенитных и аустенитно-ферритных сталей подвергнуть испытаниям на стойкость против межкристаллитной коррозии и определить содержание ос-фазы.
После изготовления и исправления выявленных дефектов сосуд подвергают гидравлическим испытаниям на прочность и герметичность. Для этого сосуд заполняют контрольной жидкостью (водой, маслом, гидросмесью), предварительно заглушив все отверстия, и выдерживают под давлением, превышающим рабочее, определенное время. В течение заданного времени испытаний в сосуде не должно происходить снижения давления. После испытаний жидкость сливают. Все данные об испытаниях и исправлении дефектов заносят в паспорт сосуда.
Источник