Давление в сосудах 0 07мпа
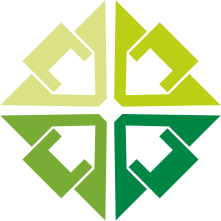
Определение отбраковочных толщин сосудов, работающих под давлением ниже 0,07 МПа и вакуумом
Министерство образования и науки Российской Федерации
Федеральное государственное бюджетное образовательное учреждение
высшего профессионального образования
«УФИМСКИЙ ГОСУДАРСТВЕННЫЙ НЕФТЯНОЙ
Кафедра технологических машин и оборудования
Отбраковка элементов сосудов, работающих под давлением ниже 0,07 МПа и вакуумом, определение скорости коррозии основных конструктивных элементов сосуда, работающего под давлением ниже 0,07 МПа и вакуумом и периодичности технического освидетельствования
к выполнению практической работы по дисциплине
«Техническое освидетельствование технологического оборудования»
Учебно-методическое пособие предназначено для студентов очной и заочной форм обучения направлений подготовки 151000, 15.03.02 «Технологические машины и оборудование» профиля «Оборудование нефтегазопереработки».
Составители: Рубцов А.В., доцент, канд. техн. наук
Закирничная М.М., докт. техн. наук, профессор
Ковшова Ю.С., канд. техн. наук
Рецензенты: Габбасова А.Х., канд. техн. наук, доцент каф. ТМО
Хасбутдинова Е.В., канд. техн. наук, доцент каф. ТМО
© Уфимский государственный нефтяной технический университет, 2015
С | |
Введение | 4 |
Практическая работа. Отбраковка элементов сосудов, работающих под давлением ниже 0,07 МПа и вакуумом, определение скорости коррозии основных конструктивных элементов сосуда, работающего под давлением ниже 0,07 МПа и вакуумом и периодичности технического освидетельствования | 5 |
Пример выполнения задания | 12 |
Контрольные вопросы | 18 |
Перечень вариантов к практической работе | 19 |
Список использованных источников | 19 |
Приложение А. Допускаемые напряжения для материала элемента аппарата при расчетной температуре | 21 |
Приложение Б. Требования к оформлению отчета о практической работе | 23 |
Приложение В. Пример оформления титульного листа отчета о практической работе | 24 |
ВВЕДЕНИЕ
На предприятиях нефтегазопереработки и нефтехимии эксплуатируется большое количество сосудов и аппаратов, работающих под давлением ниже 0,07 МПа и вакуумом, которые участвуют в различных технологических процессах. В процессе эксплуатации сосуды и аппараты подвергаются воздействию эксплуатационных нагрузок и рабочих сред. Это приводит к развитию различных дефектов, которые снижают эксплуатационную безопасность оборудования и могут привести к возникновению аварийных ситуаций.
Основным мероприятием по обеспечению безопасной и надежной эксплуатации сосудов и аппаратов являются периодическое техническое освидетельствование и своевременная отбраковка дефектных элементов.
Целью данного учебно-методического пособия является приобретение навыков студентами по определению отбраковочных толщин основных конструктивных элементов сосудов и аппаратов, работающих под давлением ниже 0,07 МПа и вакуумом, а также определению периодичности их технического освидетельствования по скорости коррозионного износа основных конструктивных элементов.
Практическая работа. Отбраковка элементов сосудов, работающих под давлением ниже 0,07 МПа и вакуумом, определение скорости коррозии основных конструктивных элементов сосуда, работающего под давлением ниже 0,07 МПа и вакуумом и периодичности технического освидетельствования
Цель работы:
1. Определение отбраковочных толщин основных конструктивных элементов сосудов (аппаратов) работающих под давлением ниже 0,07 МПа и вакуумом;
2. Определение периодичности технического освидетельствования сосудов давления, исходя из максимальной скорости коррозии основных элементов сосуда (аппарата).
ОБЩИЕ ПОЛОЖЕНИЯ
Определение отбраковочных толщин сосудов, работающих под давлением ниже 0,07 МПа и вакуумом
Отбраковка элементов сосудов (аппаратов) работающих под давлением ниже 0,07 МПа и вакуумом производится согласно РУА-93 «Руководящие указания по эксплуатации и ремонту сосудов и аппаратов, работающих под давлением ниже 0,07 МПа (0,7 кгс/см 2 ) и вакуумом».
Элементы сосудов и аппаратов (в том числе и литых), определяющие их прочность, должны отбраковываться если при толщинометрии выявится, что под действием коррозии и эрозии уменьшилась толщина металла стенки (обечаек корпуса, днищ, крышек, заглушек, штуцеров и др.) до значений, определенных расчетами по действующим методикам (ГОСТ Р 52857.1¸12-2007. и др.) или по паспорту, с учетом всех действующих нагрузок (внутреннего или наружного давления, весовых, ветровых, сейсмических, температурных и пр.) без учета прибавки на коррозию (отбраковочный размер);
Если расчетная толщина стенки (без учета прибавки на коррозию) оказалась меньше величины, указанной ниже, то за отбраковочный размер принимается величина:
— для обечаек и днищ сосудов и аппаратов при диаметре 2000 мм и ниже — 3 мм, а при диаметре более 2000 мм — 4 мм;
— для патрубков — в соответствии с таблицей 1.
Таблица 1 — Минимальный отбраковочный размер для толщины стенки патрубка
Наружный диаметр, мм | £ 25 | £ 57 | £ 108(114) | £ 219 | ³ 325 |
Наименьшая допустимая толщина стенки, мм | 1,0 | 1,5 | 2,0 | 2,5 | 3,0 |
Расчетные толщины стенок элементов сосудов, работающих под давлением ниже 0,07 МПа и вакуумом, определяются по ГОСТ Р 52857.1-2007 «Сосуды и аппараты. Нормы и методы расчета на прочность. Общие требования.», ГОСТ Р 52857.2-2007 «Сосуды и аппараты. Нормы и методы расчета на прочность. Расчет цилиндрических и конических обечаек, выпуклых и плоских днищ и крышек», ГОСТ Р 52857.3-2007. «Сосуды и аппараты. Нормы и методы расчета на прочность. Укрепление отверстий в обечайках и днищах при внутреннем и внешнем давлениях. Расчет на прочность обечаек и днищ при внешних статических нагрузках на штуцер».
Для цилиндрических обечаек расчетная толщина стенки определяется по формуле (1):
, (1)
где p – расчетное внутреннее избыточное давление, МПа;
D – внутренний диаметр, мм;
[s] – допускаемое напряжение для материала, из которого изготовлен элемент, МПа. Выбирается в зависимости от материала и расчетной температуры из приложения А;
j — коэффициент сварного шва, который выбирается по таблице 2.
Таблица 2 — Коэффициенты прочности сварных швов
Вид сварного шва
Значение коэффициентов прочности
Для эллиптических и полусферических днищ расчетная толщина стенки определяется по формуле (2):
, (2)
где R — радиус кривизны в вершине днища, который равен:
R = D — для эллиптических днищ с Н = 0,25 D;
R = 0,5 D — для полусферических днищ с Н = 0,5 D.
Для плоских днищ расчетная толщина стенки определяется по формуле (3):
, (3)
где К- коэффициент, который в зависимости от конструкции днищ и крышек определяют по таблице 4 ГОСТ Р 52857.2-2007 «Сосуды и аппараты. Нормы и методы расчета на прочность. Расчет цилиндрических и конических обечаек, выпуклых и плоских днищ и крышек» (в данной работе принимаем К=0,53).
К – коэффициент, который равен 1 для днищ (крышек) без отверстий; для днищ и крышек, имеющих одно отверстие коэффициент К определяется по формуле (4):
, (4)
где dp – диаметр отверстия в днище или крышке;
Dр – расчетный диаметр днища (крышки), мм
В рассматриваемых вариантах Dр=D, где D – внутренний диаметр сосуда, мм.
Для штуцеров расчетная толщина стенки определяется по формуле (5):
, (5)
где p – расчетное внутреннее избыточное давление, МПа;
d – внутренний диаметр штуцера, мм;
cs – прибавка на коррозию к расчетной толщине стенки штуцера, мм. Зависит от коррозионности среды. В работе принимаем cs=1;
[s]1 – допускаемое напряжение для материала, из которого изготовлен штуцер, МПа. Выбирается в зависимости от материала и расчетной температуры из приложения А;
j1 — коэффициент сварного шва. Если ось сварного шва обечайки (днища) удалена от наружной поверхности штуцера на расстояние более чем три толщины укрепляемого элемента (3s, рисунок 1б), то коэффициент прочности этого сварного соединения при расчете укрепления отверстий следует принимать j1 = 1. В исключительных случаях, когда сварной шов пересекает отверстие или удален от наружной поверхности штуцера на расстояние менее 3s, принимают j1 £ 1в зависимости от вида и качества сварного шва.
Если плоскость, проходящая через продольный шов вальцованного штуцера и ось этого штуцера, образует угол не менее 60 0 с плоскостью продольного осевого сечения цилиндрической или конической обечайки (рисунок 2), то принимают j1 = 1. В остальных случаях j1 £ 1 в зависимости от вида и качества сварного шва.
Определение периодичности технического освидетельствования работающих под давлением ниже 0,07 МПа и вакуумом, исходя из максимальной скорости коррозии основных элементов сосуда (аппарата)
Для определения периодичности технического освидетельствования сосудов (аппаратов) необходимо знать скорость равномерной коррозии
Скорость равномерной коррозии а определяется по формуле (6):
, (6)
где SИ – исполнительная (проектная) толщина стенки элемента, мм;
SФ – минимальная измеренная толщина стенки элемента, мм;
— плюсовой допуск на толщину стенки, мм;
t1 — время от момента начала эксплуатации до момента обследования, лет.
Проведение периодических технических освидетельствований сосудов (аппаратов), как правило, приурочивается к планово-предупредительным ремонтам отдельных агрегатов и установок. При этом периодичность технических освидетельствований сосудов (аппаратов) не должна выходить за пределы, установленные таблицей 3.
Таблица 3- Периодичность технического освидетельствования сосудов и аппаратов, эксплуатирующихся по РУА-93
Назначение сосудов | Наружный и внутренний осмотр не реже одного раза в | Гидравлическое испытание пробным давлением не реже одного раза в |
Сосуды (аппараты) группы 5а, работающие со средой, вызывающей коррозию металла корпуса со скоростью: | ||
— не более 0,1 мм/год | 6 лет | 12 лет |
— более 0,1 мм/год до 0,3 мм/год | 2 года | 8 лет |
— более 0,3 мм/год | 1 год | 8 лет |
Сосуды (аппараты) группы 5б, работающие со средой, вызывающей коррозию металла корпуса со скоростью: | ||
— не более 0,1 мм/год | 12 лет | 12 лет |
— более 0,1 мм/год до 0,3 мм/год | 4 года | 8 лет |
— более 0,3 мм/год | 2 года | 8 лет |
Пример выполнения задания
Определение отбраковочных толщин сосудов, работающих под давлением ниже 0,07 МПа и вакуумом
Необходимо назначить отбраковочные толщины основных конструктивных элементов емкости. Необходимые исходные данные берутся из акта изучения и анализа технической документации, выдаваемого преподавателем.
Данные, которые необходимы для выполнения задания:
Срок ввода в эксплуатацию 1959 год
Расчетные параметры
Расчетное давление — 0,25 МПа
Расчетная температура — 200 0 С
Внутренний диаметр
Цилиндрическая обечайка – 1000 мм
Эллиптические днища – 1000 мм
Исполнительная толщина стенки:
Цилиндрическая обечайка – 8 мм
Эллиптические днища – 8 мм
Материал, из которого изготовлен элемент:
Цилиндрическая обечайка – Ст3сп по ГОСТ 380
Эллиптические днища – Ст3сп по ГОСТ 380
Сведения о штуцерах.
— ручная электродуговая сварка (обечайка) электродами Э 42 ГОСТ 2523-51.
Объем контроля при изготовлении, эксплуатации и проведении экспертизы промышленной безопасности:
Эскиз емкости приведён на рисунке А.1.
По формуле (1) определим расчетные толщины стенок для цилиндрической обечайки корпуса:
Так как диаметр емкости равен 1000 мм, что меньше 2000 мм и расчетные толщины стенок цилиндрической обечайки и днищ получились меньше 3 мм, то за отбраковочный размер этих конструктивных элементов согласно РУА-93 принимаем толщину равную 3 мм.
Так как расчетные толщины штуцеров получились меньше указанных в таблице 4, то принимаем отбраковочные толщины для:
штуцера Г Ду500 – 3,0 мм.
Определение периодичности технического освидетельствования работающих под давлением ниже 0,07 МПа и вакуумом, исходя из максимальной скорости коррозии основных элементов сосуда (аппарата).
Для емкости рассмотренной выше необходимо определить скорость коррозии для каждого конструктивного элемента и по максимальному значению определить периодичность освидетельствования.
Приводятся результаты толщинометрии основных конструктивных элементов емкости, а также на рисунке А.2 схема обследования с указанием мест точек замеров. Номера точек в таблице с замерами, соответствуют номерам точек на рисунке А.2.
Определение периодичности технического освидетельствования работающих под давлением ниже 0,07 МПа и вакуумом, исходя из максимальной скорости коррозии основных элементов сосуда (аппарата).
Для емкости рассмотренной выше необходимо определить скорость коррозии для каждого конструктивного элемента и по максимальному значению определить периодичность освидетельствования.
Приводятся результаты толщинометрии основных конструктивных элементов емкости, а также на рисунке А.2 схема обследования с указанием мест точек замеров. Номера точек в таблице с замерами, соответствуют номерам точек на рисунке А.2.
Источник
Известно, что под термином «опасный производственный объект» понимается объект, на котором применяется оборудование, работающее под давлением более 0,07 Мпа. Именно такая формулировка встречается в ряде официальных документов.
Данная формулировка означает, что требование касается оборудования, которое работает под давлением более 0,7 кгс/см2. То же самое можно сказать об оборудовании, находящемся под определенным разрежением.
Практическое измерение давления газа или жидкости измеряется относительно абсолютного вакуума или атмосферного давления. В первом случае речь идет об абсолютном давлении Раб., во втором – об атмосферном Ратм..
Давление, которое отличается от атмосферного, но измеряется относительно него, называется избыточным – Ризб. или вакуумметрическим давлением – Рвак.. В итоге, абсолютное давление представляет собой сумму атмосферного давления и избыточного, или же разность атмосферного и вакуумметрического.
Избыточное давление нередко именуют манометрическим, так как оно измеряется соответсвующими приборами для контроля давления.
В технической системе единиц давление имеет размерность кгс/м2 и кгс/см2 («килограмм силы на квадратный метр» и «килограмм силы на квадратный сантиметр»). Единицу измерения кгс/см2 называют также «технической атмосферой». Если измерение производят в технических атмосферах, то абсолютное давление обозначают, как «ата», а избыточное – как «ати».
В европейских странах распространена также единица измерения «пси», которая определяется, как фунт силы на квадратный дюйм. Для измерения избыточного и абсолютного давлений применяют соответственно «psig» и «psia».
В международной системе единиц размерностью силы является «ньютон» Н, а размерностью площади – «метр в квадрате» м2. Единицей давления является «паскаль» Па, при этом 1 Па=1 Н/м2. В практическом применении часто встречаются «килопаскаль» кПа и «мегапаскаль» Мпа.
На территории Российской Федерации принято использовать единицы, обозначения и наименования согласно международной системы единиц, то есть в современных документах в качестве единицы измерения давления следует использовать единицу Па или ее производные.
Значение 0,7 появилось впервые в «Правилах устройства и безопасной эксплуатации сосудов, работающих под давлением», которые вступили в силу в 1957 году. Данный документ имел силу в отношении емкостей с рабочим давлением более 0,7 ати. Выражение «более 0,7 ати» можно понимать, как «давление выше атмосферного более чем на 0,7 кгс/см2. А если переводить в международную систему, то 0,7 кгс/см2=0,07 Мпа. Однако такой перевод необходимо сопровождать пояснением «с избыточным давлением свыше 0,07 Мпа», так как отдельного обозначения не имеется. В другом случае, верной можно считать формулировку «с давлением свыше атмосферного более чем на 0,07 Мпа».
Можно также встретить и другие подходы к моменту пояснения об избыточном давлении.
В системе единиц СГС в качестве размерности силы применяют «дину», а в качестве единицы давления – «бар», то есть 1 бар=1дин/см2. Все тот же ГОСТ 8.417-2002 для расчетов допускает применять бар, при этом 1 бар = 105 Па = 0,1 Мпа.
Можно также встретить такую единицу измерения давления, как «атмосфера» атм, которая численно равна 760 мм рт.ст. («миллиметров ртутного столба»).
Кстати, европейская директива, требования которой затрагивают оборудование, работающее под давлением, предъявляет более серьезные требования. В ней значение давления, которое является рабочим для сосудов, является более 0,5 бар. Причем в этой директиве конкретно указано, что давление принимается относительно атмосферного.
Пояснения об избыточном давлении в российских документах, а также расшифровка термина «давление», подразумевающая разницу между давлением в сосуде и атмосферным давлением, наталкивают на мысль, что выражение «…оборудование, работающее под давлением более 0,07 Мпа…» – это небрежность, а не техническая неточность.
Встречающиеся приборы для измерения давления с нулевой отметкой делают более логичным определение «с избыточным давлением свыше 0,07 Мпа».
В итоге выходит, что официально закрепленное выражение «оборудование, работающее под давлением более 0,07 Мпа» означает, что оборудование работает в условиях разрежения, то есть в вакууме. Для исключения данного казуса, во всех законотворческих документах перед словом «давление» необходимо приписать «избыточное», или же дать развернутое определение «давлению».
Если вы нашли ошибку, пожалуйста, выделите фрагмент текста и нажмите Ctrl+Enter.
Вам понравилась статья? Не хотите пропускать новые? Тогда подпишитесь на RSS или получайте новые статьи мгновенно на электронную почту
Источник
Вопрос:
Для корректного проектирования технической документации, а также в целях формирования единого подхода, используемого различными организациями в сфере проектирования, изготовления, эксплуатации и надзора за оборудованием, работающим под давлением, просим Вас дать пояснения по вопросу перевода единиц измерения давления в соответствии с нижеприведенными доводами.
Традиционно при указании в проектной документации двух единиц измерения давления (МПа и кгс/см2) их значения принимаются с переводным коэффициентом 1:10, т.е. 1 МПа ≈ 10 кгс/см2. К примеру, в технической характеристике сосуда в качестве рабочего давления указывается: 51 кгс/см2 (5,1 МПа). Такое же соотношение между МПа и кгс/см2 принято и при указании давления одновременно в обеих единицах измерения в нормативно-технической документации, регламентирующей проектирование и эксплуатацию сосудов под давлением, в частности ТР ТС 032/2013, ПБ 03-584-03, ФНП «Правила промышленной безопасности опасных производственных объектов на которых используется оборудование, работающее под избыточным давлением» (0,07 МПа (0,7 кгс/см2), 16 МПа (160 кгс/см2) и т.п.).
Согласно «Положению о единицах величин, допускаемых к применению в Российской Федерации» (утверждено постановлением Правительства РФ № 879 от 31.10.2009) и ГОСТ 8.417-2002 1 кгс/см2 = 98066,5 Па, т.е. в случае точного перевода: 1 МПа = 10,197 кгс/см2.
Очевидно, что применение переводного коэффициента 1:10 приводит к ошибке менее 2% которая зачастую нивелируется большей погрешностью используемых на оборудовании приборов (при установке манометров с классом точности 2,5). Однако, согласно п. 307 ФНП «Правила промышленной безопасности опасных производственных объектов на которых используется оборудование, работающее под избыточным давлением» для сосудов с рабочим давлением более 2,5 МПа класс точности применяемых манометров должен быть не ниже 1,5 т.е. погрешность измерения не должна превышать 1,5%. Таким образом, в последнем случае применение переводного коэффициента 1:10 приводит к превышению установленного предела погрешности на 0,47%.
В то же время нормы проектирования сосудов регламентируют не учитывать дополнительные прибавки к основным расчетным величинам (давлению, толщине стенки) в пределах 5% от их номинального значения (см. п. 6.3, 6.5, 12.4 ГОСТ 34233.1-2017). Т.е. фактически погрешность выполнения расчета на прочность любого проектируемого сосуда может составлять, как, минимум 5%.
В связи с различием требований в действующей нормативной документации просим Вас пояснить, каким переводным коэффициентом следует пользоваться при указании в технической документации значений давления одновременно в двух единицах измерения (МПа и кгс/см2), с учетом сложившихся практики проектирования и условий эксплуатации оборудования, работающего под давлением свыше 2,5 МПа.
Ответ: Согласно положениям пунктов 7 и 12 Технического регламента Таможенного союза «О безопасности оборудования, работающего под избыточным давлением» (далее – ТР ТС 032/2013):
- оборудование должно разрабатываться (проектироваться) и изготавливаться (производится) таким образом, чтобы при применении по назначению, эксплуатации и техническом обслуживании обеспечивалось его соответствие требованиям безопасности;
- при изготовлении (производстве) оборудования и устройств безопасности изготовителем обеспечивается их соответствие параметрам и характеристикам, установленным проектной документацией, и требованиям ТР ТС 032/2013.
В соответствии с пунктом 11 ТР ТС 032/2013 безопасность оборудования обеспечивается путем соблюдения при разработке (проектировании), изготовлении (производстве) требований безопасности, изложенных в ТР ТС 032/2013 и приложении № 2 к нему.
В том числе при разработке (проектировании) оборудования для обеспечения его безопасности при эксплуатации:
- с целью определения рисков для оборудования должны учитываться факторы, представляющие собой основные виды опасности, перечисленные в пункте 8 ТР ТС 032/2013;
- для идентифицированных видов опасности должна проводится оценка риска расчетным, экспериментальным, экспертным путем или по данным эксплуатации аналогичных видов оборудования согласно пункту 9 ТР ТС 032/2013;
- рассчитывается прочность оборудования с учетом прогнозируемых нагрузок, которые могут возникнуть в процессе его эксплуатации, транспортировки, перевозки, монтажа и прогнозируемых отклонений от таких нагрузок, а также с учетом факторов, перечисленных в пункте 1 приложения 2 к ТР ТС 032/2013.
Кроме этого, пункт 7 приложения № 2 к ТР ТС 032/2013, устанавливает требования к проекту оборудования, в части применения:
- а) средств контроля и измерений, погрешность которых в рабочих условиях не превышает предельно допустимое отклонение контрольного параметра;
- б) средств измерений в соответствии с условиями эксплуатации оборудования.
Исходя из вышесказанного, обращаем Ваше внимание, что, например, для указанного Вами случая, рабочее давление 51 кгс/см2 (5,1 МПа) при применении манометра классом точности 1,5 со шкалой от 0 до 10 МПа: 1,5% погрешности в пересчете в МПа составит 0,15 МПа, что составит меньше 0,09860 МПа разницы между округленным значением 5,1 МПа и 5,00199 МПа (при точном переводе 51 кгс/см2 в МПа). А при применении манометра со шкалой от 0 до 100 кгс/см2 с классом точности 1,5 – вышеуказанное значение 0,09860 МПа при переводе в кгс/см2 равна 1,00551 кгс/см2, что также ниже 1,5% погрешности прибора, составляющей 1,5 кгс/см2.
Следовательно, при таких параметрах, указание в технической документации технических характеристик в кгс/см2 и МПа с использованием коэффициента точного перевода, создаст неисполнимые условия для эксплуатирующих организаций, а также не обеспечит возможности выполнения требований пункта 7 приложения № 2 к ТР ТС 032/2013.
Источник