Детали и узлы сосудов и аппаратов
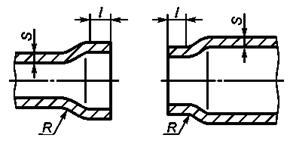
Версия для печати
4.1 Общие требования
4.1.1 Конструкция сосудов должна быть технологичной, надежной в течение установленного в технической документации срока службы, обеспечивать безопасность при изготовлении, монтаже и эксплуатации, предусматривать возможность осмотра (в том числе внутренней поверхности), очистки, промывки, продувки и ремонта, контроля технического состояния сосуда при диагностировании, а также контроля за отсутствием давления и отбора среды перед открытием сосуда.
Если конструкция сосуда не позволяет при техническом освидетельствовании проведение осмотра (наружного или внутреннего), гидравлического испытания, то разработчик сосуда должен в технической документации на сосуд указать методику, периодичность и объем контроля сосуда, выполнение которых обеспечит своевременное выявление и устранение дефектов.
4.1.2 Срок службы сосуда устанавливает разработчик сосуда, и он указывается в технической документации.
4.1.3 При проектировании сосудов следует учитывать требования Правил перевозки грузов железнодорожным, водным и автомобильным транспортом.
Сосуды, которые не могут быть транспортированы в собранном виде, должны проектироваться из частей, соответствующих по габаритам требованиям к перевозке транспортными средствами. Деление сосуда на транспортируемые части следует указывать в технической документации.
4.1.4 Расчет на прочность сосудов и их элементов следует проводить в соответствии с ГОСТ Р 52857.1 – ГОСТ Р 52857.11, ГОСТ Р 51273, ГОСТ Р 51274, ГОСТ 30780.
Допускается использование настоящего стандарта совместно с другими международными и национальными стандартами на расчет на прочность при условии, что их требования не ниже требований российских национальных стандартов.
4.1.5 Сосуды, транспортируемые в собранном виде, а также транспортируемые части должны иметь строповые устройства (захватные приспособления) для проведения погрузочно-разгрузочных работ, подъема и установки сосудов в проектное положение.
Допускается использовать технологические штуцера, горловины, уступы, бурты и другие конструктивные элементы сосудов при подтверждении расчетом на прочность.
Конструкция, места расположения строповых устройств и конструктивных элементов для строповки, их количество, схема строповки сосудов и их транспортируемых частей должны быть указаны в технической документации.
4.1.6 Опрокидываемые сосуды должны иметь приспособления, предотвращающие самоопрокидывание.
4.1.7 В зависимости от расчетного давления, температуры стенки и характера рабочей среды сосуды подразделяют на группы. Группу сосуда определяет разработчик, но не ниже, чем указано в таблице 1.
Таблица 1 – Группы сосудов
Группа | Расчетное давление, МПа | Температура стенки, °С | Характеристика рабочей среды |
---|---|---|---|
1 | Независимо | Независимо | Взрывоопасная, пожароопасная, токсичная 1-го, 2-го, 3-го классов опасности по ГОСТ 12.1.007 |
2 | До 2,5 | Выше 400 | Любая, за исключением указанной для 1-й группы сосудов |
2,5 до 5,0 | Выше 200 | ||
5,0 и более | Независимо | ||
До 5,0 | Ниже минус 40 | ||
3 | До 2,5 | От минус 40 до 400 | |
От 2,5 до 5,0 | От минус 40 до 200 | ||
4 | До 1,6 | От минус 20 до 200 | |
5 | От вакуума до 0,07 | Независимо | Взрывобезопасная, пожаробезопасная или 4-го класса опасности по ГОСТ 12.1.007 |
Группу сосуда с полостями, имеющими различные расчетные параметры и среды, допускается определять для каждой полости отдельно.
4.1.8 Базовые диаметры сосудов рекомендуется принимать по ГОСТ 9617.
4.2 Днища, крышки, переходы
4.2.1 В сосудах применяют днища: эллиптические, полусферические, торосферические, сферические неотбортованные, конические отбортованные, конические неотбортованные, плоские отбортованные, плоские неотбортованные, плоские, присоединяемые на болтах.
4.2.2 Заготовки выпуклых днищ допускается изготовлять сварными из частей с расположением сварных швов согласно указанным на рисунке 1.
Рисунок 1 – Расположение сварных швов заготовок выпуклых днищ
Расстояния l и l1 от оси заготовки эллиптических и торосферических днищ до центра сварного шва должны быть не более 1/5 внутреннего диаметра днища. При этом для вариантов в), д), ж), и), к), л) сумма расстояний l + l1 должна быть не менее 1/5 внутреннего диаметра днища.
При изготовлении заготовок с расположением сварных швов согласно рисунку 1 м) количество лепестков не регламентируется.
4.2.3 Выпуклые днища допускается изготовлять из штампованных лепестков и шарового сегмента. Количество лепестков не регламентируется.
Если по центру днища устанавливают штуцер, то шаровой сегмент допускается не изготовлять.
4.2.4 Круговые швы выпуклых днищ, изготовленных из штампованных лепестков и шарового сегмента или заготовок с расположением сварных швов согласно рисунку 1 м, должны быть расположены от центра днища на расстоянии по проекции не более 1/3 внутреннего диаметра днища. Для полусферических днищ расположение круговых швов не регламентируется.
Наименьшее расстояние между меридиональными швами в месте их примыкания к шаровому сегменту или штуцеру, установленному по центру днища вместо шарового сегмента, а также между меридиональными швами и швом на шаровом сегменте, должно быть более трехкратной толщины днища, но не менее 100 мм по осям швов.
4.2.5 Основные размеры эллиптических днищ должны соответствовать ГОСТ 6533. Допускаются другие базовые диаметры эллиптических днищ при условии, что высота выпуклой части не менее 0,25 внутреннего диаметра днища.
4.2.6 Полусферические составные днища (см. рисунок 2) применяют в сосудах при выполнении следующих условий:
– нейтральные оси полушаровой части днища и переходной части обечайки корпуса должны совпадать; совпадение осей должно быть обеспечено соблюдением размеров, указанных в конструкторской документации;
– смещение t нейтральных осей полушаровой части днища и переходной части обечайки корпуса не должно превышать 0,5(S – S1);
– высота h переходной части обечайки корпуса должна быть не менее 3у.
Рисунок 2 – Узел соединения днища с обечайкой
4.2.7 Сферические неотбортованные днища допускается применять в сосудах 5-й группы, за исключением работающих под вакуумом.
Сферические неотбортованные днища в сосудах 1-й, 2-й, 3-й, 4-й групп и в сосудах, работающих под вакуумом, допускается применять только в качестве элемента фланцевых крышек.
Сферические неотбортованные днища (см. рисунок 3) должны:
– иметь радиус сферы R не менее 0,85D и не более D;
– привариваться сварным швом со сплошным проваром.
Рисунок 3 – Сферическое неотбортованное днище
4.2.8 Торосферические днища должны иметь:
– высоту выпуклой части, измеренную по внутренней поверхности, не менее 0,2 внутреннего диаметра днища;
– внутренний радиус отбортовки не менее 0,095 внутреннего диаметра днища;
– внутренний радиус кривизны центральной части не более внутреннего диаметра днища.
4.2.9 Конические неотбортованные днища или переходы допускается применять:
а) для сосудов 1-й, 2-й, 3-й, 4-й групп, если центральный угол при вершине конуса не более 45°. Допускается использование конических днищ и переходов с углом при вершине более 45° при условии дополнительного подтверждения их прочности расчетом по допускаемым напряжениям в соответствии с ГОСТ Р 52857.1, подраздел 8.10;
б) для сосудов, работающих под наружным давлением или вакуумом, если центральный угол при вершине конуса не более 60°.
Части выпуклых днищ в сочетании с коническими днищами или переходами применяют без ограничения угла при вершине конуса.
4.2.10 Плоские днища (см. рисунок 4), применяемые в сосудах 1-й, 2-й, 3-й, 4-й групп, следует изготовлять из поковок.
При этом следует выполнять следующие условия:
– расстояние от начала закругления до оси сварного шва не менее (D – внутренний диаметр обечайки, S – толщина обечайки);
– радиус закругления r ≥ 2,5S [см. рисунок 4а)];
– радиус кольцевой выточки r1 ≥ 2,5S, но не менее 8 мм [см. рисунок 4б)];
– наименьшая толщина днища [см. рисунок 4б)] в месте кольцевой выточки S2 ≥ 0,8S1, но не менее толщины обечайки S (S1 – толщина днища);
– длина отбортовки днищ h1 ≥ r;
– угол проточки γ должен составлять от 30° до 90°;
– зона А контролируется в направлениях Z согласно требованиям 5.4.2.
Рисунок 4 – Плоские днища
Допускается изготовление плоского днища (см. рисунок 4) из листа, если отбортовка выполняется штамповкой или обкаткой кромки листа с изгибом на 90°.
4.2.11 Основные размеры плоских днищ, предназначенных для сосудов 5-й группы, должны соответствовать ГОСТ 12622 или ГОСТ 12623.
4.2.12 Длина цилиндрического борта l (l – расстояние от начала закругления отбортованного элемента до окончательно обработанной кромки) в зависимости от толщины стенки S (см. рисунок 5) для отбортованных и переходных элементов сосудов, за исключением штуцеров, компенсаторов и выпуклых днищ, должна быть не менее указанной в таблице 2. Радиус отбортовки R ≥ 2,5S.
Рисунок 5 – Отбортованный и переходный элементы
Таблица 2 – Длина цилиндрического борта
Толщина стенки S, мм | Длина цилиндрического борта l, мм, не менее |
---|---|
До 5 включ. | 15 |
Св. 5 до 10 включ. | 2S + 5 |
Св. 10 до 20 включ. | S + 15 |
Св. 20 до 150 включ. | S/2 + 25 |
Св. 150 | 100 |
4.3 Люки, лючки, бобышки и штуцера
4.3.1 Сосуды должны быть снабжены люками или смотровыми лючками, обеспечивающими осмотр, очистку, безопасность работ по защите от коррозии, монтаж и демонтаж разборных внутренних устройств, ремонт и контроль сосудов. Количество люков и лючков определяет разработчик сосуда. Люки и лючки необходимо располагать в доступных для пользования местах.
4.3.2 Сосуды с внутренним диаметром более 800 мм должны иметь люки.
Внутренний диаметр люка круглой формы у сосудов, устанавливаемых на открытом воздухе, должен быть не менее 450 мм, а у сосудов, располагаемых в помещении, – не менее 400 мм. Размер люков овальной формы по наименьшей и наибольшей осям должен быть не менее 325×400 мм.
Внутренний диаметр люка у сосудов, не имеющих корпусных фланцевых разъемов и подлежащих внутренней антикоррозионной защите неметаллическими материалами, должен быть не менее 800 мм.
Допускается проектировать без люков:
– сосуды, предназначенные для работы с веществами 1-го и 2-го классов опасности по ГОСТ 12.1.007, не вызывающими коррозии и накипи, независимо от их диаметра, при этом следует предусмотреть необходимое количество смотровых лючков;
– сосуды с приварными рубашками и кожухотрубчатые теплообменные аппараты независимо от их диаметра;
– сосуды, имеющие съемные днища или крышки, а также обеспечивающие возможность проведения внутреннего осмотра без демонтажа трубопровода горловины или штуцера.
4.3.3 Сосуды с внутренним диаметром не более 800 мм должны иметь круглый или овальный лючок. Размер лючка по наименьшей оси должен быть не менее 80 мм.
4.3.4 Каждый сосуд должен иметь бобышки или штуцера для наполнения водой и слива, удаления воздуха при гидравлическом испытании. Для этой цели допускается использовать технологические бобышки и штуцера.
Штуцера и бобышки на вертикальных сосудах должны быть расположены с учетом возможности проведения гидравлического испытания как в вертикальном, так и в горизонтальном положениях.
4.3.5 Для крышек люков массой более 20 кг должны быть предусмотрены приспособления для облегчения их открывания и закрывания.
4.3.6 Шарнирно-откидные или вставные болты, закладываемые в прорези, хомуты и другие зажимные приспособления люков, крышек и фланцев должны быть предохранены от сдвига или ослабления.
4.4 Расположение отверстий
4.4.1 Расположение отверстий в эллиптических и полусферических днищах не регламентируется.
Расположение отверстий на торосферических днищах допускается в пределах центрального сферического сегмента. При этом расстояние от наружной кромки отверстия до центра днища, измеряемое по хорде, должно быть не более 0,4 наружного диаметра днища.
4.4.2 Отверстия для люков, лючков и штуцеров в сосудах 1-й, 2-й, 3-й, 4-й групп должны быть расположены, как правило, вне сварных швов.
Расположение отверстий допускается:
– на продольных швах цилиндрических и конических обечаек сосудов, если диаметр отверстий не более 150 мм;
– кольцевых швах цилиндрических и конических обечаек сосудов без ограничения диаметра отверстий;
– швах выпуклых днищ без ограничения диаметра отверстий при условии 100-процентной проверки сварных швов днищ радиографическим или ультразвуковым методом;
– швах плоских днищ.
4.4.3 Отверстия не разрешается располагать в местах пересечения сварных швов сосудов 1-й, 2-й, 3-й, 4-й групп.
Данное требование не распространяется на случай, оговоренный в 4.2.3.
4.4.4 Отверстия для люков, лючков, штуцеров в сосудах 5-й группы разрешается устанавливать на сварных швах без ограничения по диаметру.
4.5 Требования к опорам
4.5.1 Опоры из углеродистых сталей допускается применять для сосудов из коррозионно-стойких сталей при условии, что к сосуду приваривается переходная обечайка опоры из коррозионно-стойкой стали высотой, определяемой расчетом, выполненным разработчиком сосуда.
4.5.2 Для горизонтальных сосудов угол охвата седловой опоры, как правило, должен быть не менее 120°.
4.5.3 При наличии температурных расширений в продольном направлении в горизонтальных сосудах следует выполнять неподвижной лишь одну седловую опору, остальные опоры – подвижными. Указание об этом должно содержаться в технической документации.
4.6 Требования к внутренним и наружным устройствам
4.6.1 Внутренние устройства в сосудах (змеевики, тарелки, перегородки и др.), препятствующие осмотру и ремонту, как правило, должны быть съемными.
При использовании приварных устройств следует выполнять требования 4.1.1.
4.6.2 Внутренние и наружные приварные устройства необходимо конструировать так, чтобы были обеспечены удаление воздуха и полное опорожнение аппарата при гидравлическом испытании в горизонтальном и вертикальном положениях.
4.6.3 Рубашки и змеевики, применяемые для наружного обогрева или охлаждения сосудов, могут быть съемными и приварными.
4.6.4 Все глухие части сборочных единиц и элементов внутренних устройств должны иметь дренажные отверстия для обеспечения полного слива (опорожнения) жидкости в случае остановки сосуда.
<< назад / к содержанию ГОСТа Р 52630-2012 / вперед >>
Источник
Типовые элементы корпусов сосудов и аппаратов. Элементы и детали внутренних устройств аппаратов.
Обечайки, крышки и днища
Обечайка. Обечайка является главным составным элементом корпуса, это наиболее материалоемкий и ответственный узел (деталь) любого химического аппарата.
Наибольшее распространение в химическом аппаратостроении получили цилиндрические обечайки. Главным их достоинством является простота изготовления и рациональный расход материала. Поэтому при конструировании аппаратов, если это не идет в разрез с какими-либо особыми требованиями, предъявляемыми к аппарату, рекомендуется применять цилиндрические обечайки.
Плоские стенки (коробчатая обечайка) применяются только в аппаратуре, работающей при небольших перепадах давлений. Плоские стенки невыгодны потому, что они плохо сопротивляются действующему на них давлению и расход металла на единицу полезного объема в таких конструкциях бывает более высок.
Днища. Днища также являются составными элементами корпусов химических аппаратов. Они, как правило, органически связаны с обечайкой аппарата и изготовляются из того же материала.
В сварной и паяной аппаратуре днища обычно привариваются или припаиваются к обечайке; в кованой и литой аппаратуре из пластичных материалов они либо представляют собой одно целое с обечайкой, либо также свариваются с ней; в литой аппаратуре из хрупких материалов днище всегда выполняется заодно с обечайкой.
Наиболее широко используются эллиптические днища, которые имеют следующие преимущества: простота изготовления, рациональное расходование конструкционного материала, хорошая сопротивляемость давлению среды.
Плоские днища применяются в основном в аппаратах, работающих при атмосферном давлении. Они представляют собой круглые пластины (отбортованные или неотбортованные), привариваемые по контуру к обечайке корпуса или присоединяемые другими способами.
Конические днищаприменяются в 3-х случаях: 1) при необходимости удалять из аппаратов сыпучие материалы или жидкости с большим содержанием твердых веществ; 2) для лучшего распределения газа или жидкости по всему сечению аппарата и 3) в качестве конфузоров и диффузоров для постепенного изменения скорости жидкости или газа, что необходимо для уменьшения гидравлического сопротивления аппаратов.
Крышки. В отличие от днищ, неразъемно соединенных с обечайкой корпуса, крышки могут изготавливаться либо совместно с аппаратом, либо в виде съемных частей. Применение отъемных крышек для аппаратов больших диаметров считается нецелесообразным, прежде всего из-за повышенного расхода металла, трудоемкости изготовления фланцев большого диаметра и их уплотнения. Возможность внутреннего осмотра и чистки аппарата, а также сборки и разборки мешалок и внутренних устройств обеспечивается в этих случаях путем установки люков достаточно большого размера. Конструктивно крышки выполняются плоскими, сферическими или эллиптическими.
Устройства для присоединения трубопроводов и гарнитура реакционных аппаратов
Штуцеры изготавливаются из того же материала, что и обечайки и крышки самих аппаратов. Штуцеры стальных и алюминиевых аппаратов привариваются, медных – привариваются или припаиваются к ним. Штуцеры литой аппаратуры отливаются с ней заодно.
Штуцеры могут располагаться: на крышке аппарата, на обечайке и на днище.
Бобышки. Вместо штуцеров с фланцами в некоторых случаях применяются бобышки, которые представляют собой фланцы, приваренные непосредственно к корпусу аппарата (рис. 5).
Достоинство бобышек состоит в том, что они служат укрепляющими кольцами. К их недостаткам относятся необходимость обработки их на цилиндр или сферу и, вследствие этого, большая толщина, чем фланца, и необходимость применения вместо болтов шпилек, ввернутых в тело бобышки.
Бобышки применяют для устройства смотровых стекол, при установке сальников, контрольно-измерительных приборов и для присоединения трубопроводов небольших диаметров, вместо штуцеров малых диаметров, которые легко поломать при перевозке и монтаже. Более широко бобышки применяются в литой чугунной аппаратуре, где они отливаются вместе с царгами аппарата.
Люки и лазы
Люки служат для осмотра аппарата, монтажа и демонтажа внутренних устройств, загрузки сырья и очистки.
Конструкции люков и лазов зависят от условий работы и давлении в аппарате. Если лазом пользуются редко, то крышку делают в виде заглушки, поставленную на бобышке или коротком штуцере с фланцем (рис. 6, а).
При необходимости частого открывания крышку делают на откидных болтах (рис. 6, б), которые отвертываются значительно быстрее, чем обыкновенные,
а люки и лазы, которые необходимо открывать несколько раз в день, делают с поворотной скобой, на конец которой накидывают петлю (рис. 6, в).
Опоры аппаратов
Опоры аппаратов служат для установки аппаратов на фундаменты и несущие конструкции.
При установке вертикальных аппаратов на полу или на фундаментах применяют опорные лапы (стойки), при подвеске их между перекрытиями – боковые.
Для опирания горизонтальных аппаратов используют седловидные опоры, размещаемые снизу аппарата и охватывающие его не менее чем на 120° по окружности. Количество опор может быть 2, 3 и более, в зависимости от длины аппарата.
Рубашки в технологических аппаратах предназначаются для нагревания или охлаждения обрабатываемых или хранящихся в аппарате главным образом жидких продуктов. Они могут устанавливаться на цилиндрических вертикальных и горизонтальных аппаратах. Наибольшее применение имеют рубашки на вертикальных аппаратах.
По конструкции рубашки бывают неразъемные (приварные к корпусу аппарата) и отъемные..
Классическая колонна представляет собой вертикальный цилиндр, внутри которого располагаются контактные устройства — тарелки или насадки. Соответственно различают ректификационные колонны тарельчатые и насадочные. Вспомогательные узлы предназначены для ввода, распределения и аккумулирования (сбора) жидкости и пара.
Тарелка ректификационной колонны представляет собой горизонтальную перегородку в колонне, на тарелке находится слой стекающей по колонне жидкости ( орошение), сквозь которую барботируют поднимающиеся снизу пары. Тарелки бывают разнообразных конструкций и различаются по типу барботаж-ных устройств. Наиболее распространены колпачковые тарелки ( рис. 13), в которых имеются паровые патрубки 2, перекрытые колпачками 3 с зазубренными нижними краями. Чем больше в колонне тарелок и чем интенсивнее ее орошение, тем более четко удается разделить компоненты исходной смеси.
В малых ректификационных колоннах вместо тарелок применяется насадка. Она может быть регулярной (вставной) или хаотической (насыпной). Эти контактные элементы заполняют собой весь внутренний объём ректификационной части колонны.
Тепломассообмен в насадке происходит не на поверхности пузырьков, как в тарельчатых колоннах, а между тонким слоем флегмы, покрывающим материал насадки и паром, движущимся в свободном пространстве (в объёме насадки).
Основные требования, предъявляемые к конструкциям машин и аппаратов, и факторы определяющие конструкцию основных деталей и сборочных единиц.
Конструкция сосуда должна быть технологичной, надежной в течение предусмотренного технической документацией срока службы, предусматривать возможность полного опорожнения от рабочей среды, очистки, промывки, продувки, осмотра внутренних и наружных поверхностей, ремонта и проведения гидравлических испытаний со сливом воды как в проектном, так и в горизонтальном положении
Все глухие полости сосуда и его частей должны иметь отверстия для удаления воздуха. Для теплообменных аппаратов и аппаратов с полостями, имеющими различные характеристики и параметры, необходимо указывать их для каждой полости.
При проектировании сосудов должны учитываться требования «Правил перевозки грузов железнодорожным, водным и автомобильным транспортом».
Сосуды, которые не могут транспортироваться в собранном виде, должны проектироваться из минимального количества частей.
Для крепления на монтажной площадке к корпусу сосуда металлоконструкций (лестниц, кронштейнов, монтажных цапф и т.п.), а также теплоизоляции, должны быть предусмотрены специальные накладки или другие устройства, привариваемые на предприятии-изготовителе к корпусу сосуда до окончательной термообработки. Приварка указанных элементов на месте монтажа непосредственно к корпусу не допускается.
При конструировании сосудов, а также отдельно транспортируемых частей должны быть предусмотрены строповые устройства(цапфы, упоры, хомуты, опоры, захватные приспособления) для проведения погрузочно-разгрузочных работ, подъема и установки в проектное положение с учетом их конструктивных особенностей и монтажа.
Кроме того, для выведения сосудов массой более 100 т в вертикальное положение должны быть предусмотрены, по указанию монтажной организации, шарнирные устройства.
Факторы, определяющие конструкцию:
1) рабочее давление, МПа (кгс/см2 ;);
2) расчетное давление, МПа (кгс/см2 );
3) пробное давление, МПа (кгс/см2 );
4) расчетная температура стенки, °С;
5) минимально-допустимая отрицательная температура стенки, находящейся под давлением, °С;
6) характеристику рабочей среды (класс опасности по ГОСТ12.1.007, воспламеняемость, категория и группа взрывоопасности по ГОСТ 12.1.010,максимальная и минимальная температура, состав);
7) прибавка для компенсации коррозии и эрозии,мм;
8) срок службы, лет;
9) число циклов нагружений сосуда за весь срок службы;
10)объем внутренний (вместимость), м3 ;
11)массу, кг;
12) расположение центра масс;
13) сейсмичность, балл;
14) скоростной напор ветра (в зависимости отклиматического района установки сосуда).
Расчет толщин днищ и крышек, их виды. Типы опор аппаратов, особенности расчета опор аппаратов.
Расчет днищ и крышек, нагруженных внутренним давлением:
Полушаровые (сферические) днища и крышки.
Толщина стенки сферического днища (крышки), нагруженного внутренним давлением определяется по формуле
где р – расчетное давление, МПа;
D – внутренний диаметр, мм;
с – общая прибавка на коррозию, мм;
[σ] – допускаемое напряжение, МПа.
φ – коэффициент прочности сварного шва.
Эллиптические днища (крышки).
Толщина стенки эллиптического днища (крышки), нагруженного внутренним давлением определяется по формуле
где R – радиус кривизны в вершине днища (для стандартных днищ R = D)
Стальные днища диаметром до 1600 мм изготавливают штампованными из цельного листа, для них φ = 1.
Конические днища (крышки).
При α < 70° :
Толщина стенки конической части отбортованного конического днища определяется по формуле
где Dp = D + 2 × [r × (1 – cos α) + 10 × sin α] – диаметр линии перехода между конической и отбортованной частями (для днищ без отбортовки Dp = D).
Толщина отбортованной части днища определяется по формуле
где D – диаметр днища у основания;
yк – коэффициент формы днища [4, с.46, рис.22].
Из двух полученных величин выбирается большее. Это и есть толщина днища.
При α > 70°:
Общая толщина днища определяется по формуле
Плоские днища (крышки).
Толщина плоского днища определяется по формуле
где К – коэффициент конструкции днища, его значение определяется по графикам в зависимости от закрепления крышки
D – диаметр аппарата.
Согласно рисунку имеем: I и II – K = 0,57; III – K = 0,52; IV – K = 0,47; V и VI – K = 0,44; VII – K = 0,40; VIII – K = 0,45.
Расчет днищ и крышек, нагруженных наружным давлением:
Полушаровые (сферические) и эллиптические днища (крышки) рассчитывают на устойчивость под действием наружного давления по формулам
где kэ – коэффициент, определенный по графику [4, с.47, рис.25], в зависимости от отношений H/D и R/(s – c1);
R – радиус кривизны в вершине днища;
Е – модуль упругости;
β1 – коэффициент.
Конические днища рассчитываются на наружное давление так же, как и короткие цилиндрические обечайки, принимая за расчетную длину L высоту конуса, за расчетный диаметр
.
где D1 и D0 – диаметры большего и меньшего оснований конуса.
Типы опор аппаратов, особенности расчета опор аппаратов.
Опоры аппаратов служат для установки аппаратов на фундаменты и несущие конструкции.
При установке вертикальных аппаратов на полу или на фундаментах применяют опорные лапы (стойки), при подвеске их между перекрытиями – боковые.
Для опирания горизонтальных аппаратов используют седловидные опоры, размещаемые снизу аппарата и охватывающие его не менее чем на 120° по окружности. Количество опор может быть 2, 3 и более, в зависимости от длины аппарата.
Выбор типа опоры зависит от ряда условий:
места установки аппарата (в помещении или на открытой площадке)
соотношение высоты к диаметру аппарата
его массы и т.д.
Рисунок 10.2.1 – Основные типовые конструкции опор для вертикальных аппаратов
Расчет
Первоначально выбираем количество и тип опор согласно массе аппарата.
Затем рассчитываем нагрузку на одну опору.
Рассчитаем обечайку на местную прочность и устойчивость в местах, где крепятся лапы:
Ребра привариваем к корпусу сплошным швом с катетом hш. Общая длинна сварного шва, Lш, м:
,
где Н – параметр выбранной опоры (см. таблицу 10.2.1)
s – толщина аппарата, м.
Проверим прочность сварных швов:
где G – нагрузка, воспринимаемая одной опорой, МН
МН/м2
Если условие выполняется, то прочность сварного шва обеспечена.
Определим максимальные напряжения в корпусе аппарата в месте присоединения к нему лап.
Найдем параметры для нахождения коэффициентов Кк и Км
, ,
.
где В,Н – размеры опоры
D – диаметр аппарата, м
s – толщина стенки аппарата, м
Cк – прибавка на коррозию, м
Момент от реакции опоры Ми, МН·м, действующий на лапу при расчетном плече:
,
где – определяем из чертежа опоры, м.
По графику на рисунке 10.3.1 определяем значение коэффициентов Кк и Км.
Далее определяем параметр β для нахождения моментов действующих на корпус:
для определения меридиональных моментов:
,
для определения кольцевых моментов:
.
Рисунок 10.3.1 – Графики для определения коэффициента К
Км ,——— Кк
По графику на рисунке 10.3.2 определяем параметр , используя β1 и .
Рисунок 10.3.2 – Графики для определения, отнесенного к единице длины меридионального момента Мм, действующего на стенку цилиндрического корпуса аппарата в месте присоединения к нему лапы (опоры)
Отсюда определяем меридиональный момент Мм, МН×м/м.
По графику на рисунке 10.3.3 определяем параметр , используя β2 и
Рисунок 10.3.3 – Графики для определения, отнесенного к единице длины меридионального момента Мк, действующего на стенку цилиндрического корпуса аппарата в месте присоединения к нему лапы (опоры)
Отсюда определяем кольцевой момент Мк, МН×м/м.
Далее по графикам на рисунке 10.3.4 определяем коэффициенты К’к и К’м, для определения сил действующих на корпус.
Рисунок 10.3.4 – Графики для определения коэффициентов К’ при определении расчетных сил Рм и Рк, действующих на стенку цилиндрического корпуса
Км ,——— Кк
Определяем параметр β для определения сил действующих на корпус аппарата:
.
По графику на рисунке 10.3.5 определяем параметр , используя β3 и .
Рисунок 10.3.5 – Графики для определения, отнесенного к единице длины меридиональной силы Рм, действующего на стенку цилиндрического корпуса аппарата в месте присоединения к нему лапы (опоры)
Отсюда определяем меридиональную силу Рм, МН/м.
По графику на рисунке 10.3.6 определяем параметр , используя β3 и .
Отсюда определяем кольцевую силу Рк, МН/м.
Суммарное напряжение сжатия σc, МН/м2, в корпусе аппарата при толщине стенки , мм в месте присоединения лапы:
в меридиональном направлении:
,
в кольцевом направлении:
,
Если оба напряжения меньше допускаемого, следовательно, лапа может быть приварена к обечайке без подкладного листа. В противном случае используется подкладной лист. Толщина стенки в этом случае рассчитывается по формуле sп = s + s1 – cк и весь расчет производить заново.
Рисунок 10.3.6 – Графики для определения, отнесенного к единице длины кольцевой силы Рк, действующего на стенку цилиндрического корпуса аппарата в месте присоединения к нему лапы (опоры)
Источник