Какой сосуд считается под давлением
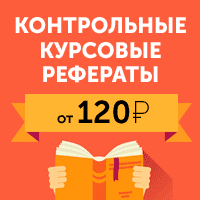
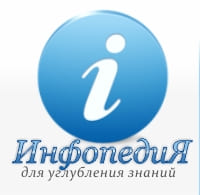
Мы поможем в написании ваших работ!
Мы поможем в написании ваших работ!
Мы поможем в написании ваших работ!
ЗНАЕТЕ ЛИ ВЫ?
Сосудом, работающим под давлением, называют герметически закрытую емкость, предназначенную для ведения химических, тепловых и других технологических процессов, а также для хранения и транспортирования газообразных, жидких и других веществ. Границей сосуда являются входной и выходной штуцера. К числу сосудов, работающих под давлением, относятся котлы, баллоны, цистерны, бочки. Сосуды, работающие под давлением, изготавливают сварными или литыми на предприятиях, имеющих разрешение Госнадзорохрантруда. На заводе на поверхность сосудов наносят паспортные данные. После изготовления все сосуды подлежат испытанию пробным давлением.
При эксплуатации наиболее частыми причинами аварий и взрывов сосудов являются: превышение предельно допустимого давления, нарушение температурного режима, потеря ими механической прочности.
Сосуды, работающие под давлением, из-за возможности взрыва являются оборудованием повышенной опасности, поэтому эксплуатировать их необходимо в соответствии с “Правилами устройства и безопасной эксплуатации сосудов, работающих под давлением”. Эти правила распространяются на: сосуды, работающие под давлением воды с температурой выше 115°С или другой жидкости с температурой, превышающей температуру кипения при давлении 0,07 МПа (без учета гидростатического давления); сосуды, работающие под давлением пара или газа свыше 0,07 МПа; баллоны, предназначенные для транспортирования и хранения сжатых, сжиженных и растворенных газов под давлением свыше 0,07 МПа; цистерны и бочки для транспортирования и хранения сжиженных газов, давление паров которых при температуре до 50°С превышает 0,07 МПа; цистерны и сосуды для транспортирования или хранения сжатых, сжиженных газов, жидкостей и сыпучих тел, в которых давление выше 0,07 МПа создается периодически для их опорожнения; барокамеры.
Указанные правила не распространяются на: сосуды и баллоны вместимостью не более 0,025 м3(25 л), для которых произведение давления (р) в МПа на вместимость (V) в м3 не превышает 0,02; сосуды, работающие под вакуумом; приборы парового и водяного отопления; трубчатые печи; части машин, не представляющие собой самостоятельных сосудов, и некоторые другие.
Сосуды, на которые распространяются “Правила устройства и безопасной эксплуатации сосудов, работающих под давлением”, подлежат регистрации и техническому освидетельствованию – осмотру и испытанию пробным давлением. Предусмотрена регистрация некоторых сосудов в органах Госнадзорохрантруда. Регистрации в этих органах не подлежат: сосуды холодильных установок и холодильных блоков в составе технологических установок; бочки для перевозки сжиженных газов, баллоны вместимостью до 100 л включительно, установленные стационарно, а также предназначенные для транспортировки и (или) хранения сжатых, сжиженных и растворенных газов; сосуды для хранения или транспортировки сжиженных газов, жидкостей и сыпучих тел, находящиеся под давлением периодически при их опорожнении; сосуды со сжатым и сжиженным газами, предназначенные для обеспечения топливом двигателей транспортных средств, на которых они установлены, и некоторые другие.
На предприятиях торговли и общественного питания не используются сосуды, подлежащие регистрации в органах Госнадзор-охрантруда. Однако на этих предприятиях имеются или обращаются сосуды (аппараты), на которые распространяются требования “Правил устройства и безопасной эксплуатации сосудов, работающих под давлением”. К таким сосудам относятся аппараты стационарных холодильных установок, автосатураторы, баллоны с различными газами.
Разрешение на ввод в эксплуатацию сосуда, не подлежащего регистрации в органах Госнадзорохрантруда, выдается лицом, назначенным приказом по предприятию для осуществления надзора за техническим состоянием и эксплуатацией сосудов, на основании документации предприятия-изготовителя после проверки представителем организации обслуживания и, при необходимости, технического освидетельствования. Разрешение на ввод сосуда в эксплуатацию записывается в его паспорт. На поверхности сосуда должны быть следующие данные: регистрационный номер, разрешенное рабочее давление, дата (число, месяц и год) следующих осмотра и испытания.
Cосуд или группа сосудов, входящих в установку, включаются в работу на основании письменного распоряжения администрации предприятия. Сосуды, на которые распространяются требования указанных выше правил, периодически в процессе эксплуатации и, при необходимости, досрочно подвергаются техническому освидетельствованию. Объем, методы и периодичность технических освидетельствований сосудов (за исключением баллонов) определены предприятиями-изготовителями, указаны в паспортах и инструкциях по монтажу и безопасной эксплуатации. Техническое освидетельствование сосудов, цистерн, баллонов и бочек может производиться на специальных ремонтно-испытательных пунктах, на предприятиях-изготовителях, на наполнительных станциях, а также на предприятиях владельцев.
На предприятиях должны быть обеспечены содержание сосудов в исправном состоянии и безопасные условия их работы. Приказом по предприятию или объединению предприятий назначаются из числа инженерно-технических работников лицо, ответственное за исправное состояние и безопасное действие сосудов, и лицо, осуществляющее надзор за их техническим состоянием и эксплуатацией. К обслуживанию сосудов, работающих под давлением, допускаются лица, достигшие 18-летнего возраста, прошедшие специальное обучение (в профессионально-техническом училище, учебно-курсовом комбинате), аттестацию в квалификационной комиссии и инструктаж по безопасному обслуживанию сосудов. Проверка знаний персонала, обслуживающего сосуды, проводится не реже одного раза в год.
Инструкции по режиму работы и безопасной эксплуатации сосудов должны быть вывешены на рабочих местах и выданы под расписку обслуживающему персоналу.
При нарушениях режимов работы и появлении неисправностей эксплуатация сосудов должна быть прекращена.
Для управления работой и обеспечения безопасной эксплуатации сосуды оборудуют приборами для измерения давления и температуры, предохранительными устройствами, запорной арматурой и, при необходимости, указателями уровня жидкости.
На сосудах для измерения давления устанавливают манометры, проверка которых с опломбированием или клеймением производится не реже одного раза в год. Не реже одного раза в 6 месяцев на предприятии проверяют показания рабочих манометров по контрольному; результаты проверки записывают в журнал. Манометр должен иметь красную черту по делению, соответствующему разрешенному рабочему давлению в сосуде.
Предохранительные клапаны бывают пружинного и рычажно-грузового действия. Предохранительные клапаны должны соответствовать требованиям ГОСТ 12.2.085-82.”ССБТ. Сосуды, работающие под давлением. Клапаны предохранительные. Требования безопасности”. Давление настройки предохранительных клапанов должно быть равно рабочему давлению в сосуде или превышать его, но не более чем на 25% . Рабочую среду, выходящую из предохранительного клапана, следует отводить в безопасное место. Предохранительные клапаны проверяют не реже одного раза в 6 месяцев или одного раза в год в зависимости от вида сосуда, на котором они установлены. При проведении периодических проверок предохранительный клапан после испытания и тарировки должен пломбироваться.
Вместо предохранительных клапанов могут быть использованы предохранительные пластины, разрывающиеся при давлении в сосуде, превышающем рабочее не более чем на 25% .
Сосуд, работающий под давлением, меньшим давления питающего его источника, должен быть оборудован автоматическим редуцирующим устройством для понижения давления газа. Камера низкого давления редуктора должна иметь манометр и пружинный предохранительный клапан, отрегулированный на соответствующее разрешенное давление в емкости, в которую перепускается газ. Такие устройства-редукторы имеются, например, в автосатураторах.
Запорную арматуру устанавливают на трубопроводах, по которым к сосуду подводятся или от него отводятся жидкости, пары или газы. Установка запорной арматуры между сосудом и предохранительным клапаном не допускается. Нельзя устанавливать запорные приспособления на трубах, отводящих газ или пар от предохранительных устройств.
Между сосудом с чрезвычайно опасным или высокоопасным веществом, а также с пожаро- или взрывоопасной средой и насосом (компрессором) устанавливают обратный клапан, автоматически закрывающийся под действием давления из сосуда.
При необходимости контроля уровня жидкости в сосудах, имеющих границу раздела сред, применяются указатели уровня. Кроме указателей уровня, на сосудах могут быть установлены звуковые, световые и другие сигнализаторы и блокировки по уровню.
Эксплуатацию паровых и водогрейных котлов регламентируют “Правила устройства и безопасной эксплуатации паровых и водогрейных котлов”.
Паровые котлы с рабочим давлением до 0,07 МПа должны соответствовать требованием ГОСТ 12.2.096-83. “ССБТ. Котлы паровые с рабочим давлением до 0,07 МПа. Требования безопасности”.
§ 2. Дополнительные требования к баллонам,
Источник
Определение категории сосудов под давлением
Вы производите оборудование, работающее под избыточным давлением: сосуды, аппараты, теплообменники, колонны, трубопроводы, котлы и т.п., тогда Вам нужно идти к нам!
А если серьезно, то наша компания одна из первых аккредитовалась на ТР ТС 032/2013
(далее Технический регламент «Оборудование, под давлением…») и, что не маловажно, начала проводить работы по сертификации в соответствии с этим регламентом. Когда многие
не хотели быть первыми и ждали реакции большинства, мы делали все в соответствии
с написанным в регламенте на свой страх и риск. Технический регламент «Оборудование,
под давлением…» достаточно сложный регламент. Он не похож на все предыдущие технические регламенты Таможенного союза, которые вступили силу до него. Редактировался он с участием Федеральной Службы по Экологическому, Технологическому и Атомному надзору (Ростехнадзор) и похож немного на правила промышленной безопасности, которые существовали ранее.
Для того, чтобы определиться требуется проводить подтверждение соответствия ТР ТС 032/2013 нужно не так много: определить для какой среды предназначено ваше оборудование, определить вместимость вашего оборудования или диаметр и максимально допустимое рабочее давление. Это все. Зная эти три параметра, вы четко для себя можете понять каким требованиям должна соответствовать ваша продукция. Если вы знаете для какой среды применяется оборудование, тогда определите к какой группе относится Ваша среда.
Если рабочая среда может быть разная, то нужно выбирать самую опасную. Технический регламент «Оборудование, под давлением…» разделяет среды на две группы первую и вторую.
Группа 1 — включает рабочие среды, состоящие из воспламеняющихся, окисляющихся, горючих, взрывчатых, токсичных и высокотоксичных газов, жидкостей и паров в однофазном состоянии, а также их смесей.
Группа 2 – это все остальные среды, кроме сред относящихся к группе 1. Теперь вы знаете,
к какой группе относится Ваша рабочая среда. Далее нужно открыть приложение 1 к ТР ТС 032/2013. Там есть несколько таблиц. Таблицы делятся по оборудованию и по рабочей среде. Конкретней таблицы делятся на сосуды, котлы и трубопроводы. В свою очередь сосуды делятся на две группы и так же котлы и трубопроводы.
Что это значит? Если Ваша среда относится к группе 1 и вы производите сосуды, тогда Вам нужна таблица 1. И по таблице вы уже смотрите, зная вместимость и максимально допустимое рабочее давление, и выбираете категорию вашего оборудования.
Источник
Таблица N 4. Распределение сосудов по группам опасности
Распределение сосудов по группам опасности
Группа опасности сосуда
Расчетное давление, МПа
Температура стенки, °C
Взрывоопасная и (или) пожароопасная, и (или) вредная среда 1, 2 классов опасности
Любая, за исключением указанной для 1-й группы сосудов
От — 0 до -20, от 200 до 400
108. При изготовлении, монтаже, ремонте и реконструкции (модернизации) сосудов должны быть выполнены требования ПКД и ТД в части контроля:
1) соответствия металла свариваемых деталей и сварочных материалов;
2) соответствия качества подготовки кромок и сборки под сварку;
3) соблюдения технологического процесса сварки и термической обработки.
109. Основными методами контроля металла и сварных соединений являются:
1) визуальный и измерительный контроль;
2) радиографический контроль;
3) ультразвуковая дефектоскопия;
4) атомно-эмиссионный спектральный анализ (стилоскопирование);
5) измерение твердости;
6) гидравлические испытания;
7) пневматические испытания;
8) магнитопорошковая дефектоскопия.
Кроме этого, могут применяться другие методы контроля (акустическая эмиссия, магнитография, капиллярный контроль, определение содержания в металле шва ферритной фазы) в объеме, предусмотренном ПКД.
110. При разрушающем контроле должны проводиться механические испытания, металлографические исследования и испытания на стойкость к межкристаллитной коррозии в объеме, предусмотренном ПКД.
111. Приемочный контроль изделия, сборочных единиц и сварных соединений должен выполняться после окончания всех технологических операций, связанных с термической обработкой, деформированием и наклепом металла.
Последовательность контроля отдельными методами должна соответствовать требованиям ТД. Визуальный и измерительный контроль должен предшествовать контролю другими методами.
112. Контроль сварных соединений должен производиться по методикам организации-изготовителя сосуда, согласованным с головной материаловедческой организацией.
113. Методы и объемы контроля сварных соединений приварных деталей, не работающих под внутренним давлением, должны устанавливаться в ПКД.
114. При операционном контроле проверяется выполнение исполнителями требований ТД.
115. Результаты по каждому виду контроля, в том числе и операционному, должны фиксироваться в отчетной документации (журналах, формулярах, протоколах, маршрутных паспортах).
116. Средства измерения должны проходить метрологическую поверку (калибровку), а испытательное оборудование — аттестацию.
117. Каждая партия материалов для дефектоскопии (пенетранты, порошок, суспензии, радиографическая пленка, химические реактивы) до начала их использования должна быть подвергнута входному контролю.
118. Сварное соединение признается годным, если при контроле в нем не будут обнаружены внутренние и наружные дефекты, выходящие за пределы допустимых норм.
119. Сведения о контроле сварных соединений основных элементов сосудов, работающих под давлением, определенных в ПКД, должны заноситься в паспорт сосуда.
120. Визуальному и измерительному контролю при изготовлении, монтаже, ремонте и реконструкции (модернизации) сосудов подлежат все сварные соединения сосудов и их элементов в целях выявления в них следующих дефектов:
1) трещин всех видов и направлений;
2) свищей и пористости наружной поверхности соединения;
4) наплывов, прожогов, незаваренных кратеров;
5) смещения и совместного увода кромок свариваемых элементов свыше норм, предусмотренных настоящими Правилами;
6) непрямолинейности соединяемых элементов;
7) несоответствия формы и размеров соединений требованиям НД.
121. Перед визуальным и измерительным контролем поверхность сварного соединения и прилегающие к нему участки основного металла шириной не менее 20 мм в обе стороны от соединения должны быть зачищены от шлака и других загрязнений, при электрошлаковой сварке это расстояние должно быть не менее 100 мм.
122. При двустороннем доступе визуальный и измерительный контроль должны производиться с наружной и внутренней стороны по всей протяженности швов. В случае невозможности проведения визуального и измерительного контроля сварного соединения с двух сторон, его контроль должен производиться в порядке, предусмотренном в руководстве (инструкции) по эксплуатации сосуда.
123. Ультразвуковая дефектоскопия и радиографический контроль сварных соединений при изготовлении, монтаже, ремонте и реконструкции (модернизации) сосудов производятся в целях выявления в сварных соединениях внутренних дефектов (в том числе трещин, непроваров, пор, шлаковых включений).
124. Метод контроля (ультразвуковая дефектоскопия, радиографический контроль или оба метода в сочетании) выбирается исходя из возможности обеспечения более полного и точного выявления дефектов с учетом особенностей физических свойств металла, а также освоенности данного метода контроля для конкретного вида сварных соединений.
125. Объем контроля ультразвуковой дефектоскопией или радиографическим методом стыковых, угловых, тавровых и других сварных соединений сосудов (включая соединения люков и штуцеров с корпусом сосуда) должен соответствовать информации, приведенной в таблице N 5 настоящих Правил.
Указанный объем контроля относится к каждому сварному соединению. Места сопряжений (пересечений) сварных соединений подлежат обязательному контролю ультразвуковой дефектоскопией или радиографическим методом.
Ультразвуковая дефектоскопия или радиографический контроль швов приварки внутренних и наружных устройств к корпусу сосуда должны производиться при наличии требования в ПКД.
Источник
Рассмотрим основные виды сосудов и аппаратов, работающих под давлением.
Виды сосудов и аппаратов, работающих под давлением. Классификация. Требования к обозначениям.
При осуществлении различных технологических процессов, проведении ремонтных работ, в быту и т.д. широко используются различные системы повышенного давления: трубопроводы, баллоны и емкости для хранения или перевозки сжатых, сжиженных и растворенных газов, паровые и водяные котлы, газгольдеры и др. Основная характеристика этого оборудования состоит в том, что давление газа или жидкости здесь превышает атмосферное. Указанное оборудование принято называть сосудами, работающими под давлением.
Сосуд — герметически закрытая емкость, предназначенная для ведения химических,тепловых и других технологических процессов, а также для хранения и транспортировки газообразных, жидких и других веществ. Границей сосуда являются входные и выходные штуцера.
Резервуар — стационарный сосуд, предназначенный для хранения газообразных, жидких и других веществ.
Баллон — сосуд, имеющий одну или две горловины для установки вентилей,фланцев или штуцеров, предназначенный для транспортировки, хранения и использован сжатых, сжиженных или растворенных под давлением газов.
Бочка — сосуд цилиндрической или другой формы, который можно перекатывать содного места на другое и ставить на торцы без дополнительных опор, предназначенный для транспортировки и хранения жидких и других веществ.
Барокамера — сосуд, оснащенный приборами и оборудованием и предназначенный для размещения в нем людей.
Цистерна — передвижной сосуд, постоянно установленный на раме железнодорожного вагона, на шасси автомобиля (прицепа) или на других средствах передвижения, предназначенный для транспортировки и хранения газообразных,жидких и других веществ.
Степень опасности сосудов определяется в соответствии с Федеральным законом «О промышленной безопасности опасных производственных объектов» — по Приложению №1 ФЗ, сосуды работающие под давлением отнесены к категории технических устройств на опасных производственных объектах, на которых, — «используется оборудование, работающее под давлением более 0,07 МПа или при температуре нагрева воды более 115 ºС», в том числе это относится и к баллонам, бочкам, цистернам в которых получаются, используются, перерабатываются, образуются, хранятся, транспортируются, уничтожаются опасные вещества»
Рассмотрим основные виды сосудов и аппаратов, работающих под давлением.
Трубопроводы — устройства для транспортировки жидкостей и газов. По ГОСТ все жидкости и газы, транспортируемые по ним, разбиты на десять групп. Для определения вида вещества, транспортируемого по трубопроводам, их окрашивают в соответствующие цвета (опознавательная окраска):
Источник
Источник