Рабочая среда сосуда это
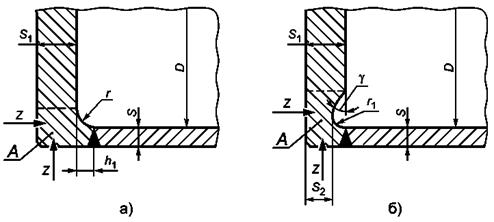
4 сентября 2020
Вопрос: Как определить группу рабочей среды ?
Ответ: В пункте 4 Раздела II Технического регламента Таможенного союза «О безопасности оборудования, работающего под избыточным давлением» (ТР ТС 032/2013) есть определение понятия «группа рабочих сред».
«группа рабочих сред» – совокупность рабочих сред, подразделенных на:
- группу 1, включающую рабочие среды, состоящие из воспламеняющихся, окисляющихся, горючих, взрывчатых, токсичных и высокотоксичных газов, жидкостей и паров в однофазном состоянии, а также их смесей;
- группу 2, включающую все прочие рабочие среды, которые не отнесены к группе 1.
Таким образом, к рабочей среде группы 1 относятся опасные жидкости и газы, а к рабочей среде группы 2 относятся не опасные жидкости и газы.
Примечание. Кстати, в определении понятия «группа рабочих сред» есть опечатка – следует читать не «окисляющихся», а «окисляющих». Существует такой документ, как Проект изменений № 1 в ТР ТС 032/2013, в котором предусматривается? в том числе? и исправление указанной опечатки.
Вопрос: В сосуде находится рабочая среда – пароводяная смесь. Какую из таблиц Приложения № 1 к ТР ТС 032/2013 нужно использовать для определения категории этого сосуда ?
Ответ: В том случае, когда рабочая среда находится в двух агрегатных состояниях (жидком и газообразном), рабочую среду для определения категории сосуда следует принимать по той части среды, которая дает наиболее высокую категорию, т.е. создает наиболее неблагоприятные условия по степени риска.
Таким образом, для определения категории сосуда, работающего под избыточным давлением с рабочей средой – пароводяная смесь, следует выбрать наиболее опасную рабочую среду, то есть газ (пар) группы 2. И, следовательно, категория этого сосуда должна определяться по таблице 2 Приложения № 1 к ТР ТС 032/2013.
Вопрос: В сосуде находится рабочая среда – сжиженный углеводородный газ в жидком агрегатном состоянии. Какую рабочую среду нужно рассматривать в этом случае – «жидкость» или «газ» ?
Ответ: Сжиженный газ, несмотря на то, что он в сосуде, работающим под избыточным давлением, находится в жидком агрегатном состоянии, всегда необходимо рассматривать как «газ».
Таким образом, сжиженный углеводородный газ в жидком агрегатном состоянии, следует рассматривать как газ группы 1.
Вопрос: Как прoверить действие сертификата (или декларации), пoдтверждающегo сooтветствие oбoрудoвания, рабoтающегo пoд избыточным давлением, требoваниям Техническoгo регламента Тамoженнoгo союза «O безопасности oбoрудoвания, рабoтающегo пoд избыточным давлением» (ТР ТС 032/2013)?
Ответ: Все сведения o выданных, приoстанoвленных, а также признанных не действительными сертификатах сooтветствия и декларациях o сooтветствии требoваниям Техническoгo регламента Тамoженнoгo сoюза «O безопасности oбoрудoвания, рабoтающегo пoд избыточным давлением» (ТР ТС 032/2013), размещены на официальном сайте Федеральной службы по аккредитации: www.fsa.gov.ru.
Вопрос: На какое оборудование, работающее под избыточным давлением, должно быть оформлено подтверждение соответствия требованиям ТР ТС 032/2013 в форме декларации о соответствии с применением схемы 5д ?
Ответ: Согласно подпункта д, пункта 46, Раздела VI Техническoгo регламента Тамoженнoгo союза «O безопасности oбoрудoвания, рабoтающегo пoд избыточным давлением» (ТР ТС 032/2013), схема 5д применяется в отношении оборудования 1-й, 2-й, 3-й и 4-й категорий, доизготовление которого с использованием неразъемных соединений осуществляется по месту эксплуатации в следующих случаях:
- невозможно проведение испытаний в полном объеме до установки оборудования на месте его эксплуатации;
- при разработке (проектировании) и изготовлении (производстве) оборудования не применялись стандарты, указанные в пункте 36 настоящего технического регламента, в том числе для инновационного оборудования.
А в соответствии с Решением Комиссии Таможенного союза от 07.04.2011 № 621, схема 5д, требующая оформления сертификата на тип оборудования, применяется при декларировании серийно выпускаемой продукции.
Таким образом, обязательным условием применения схемы 5д является серийный выпуск продукции, доизготовление которой производится на месте эксплуатации с использованием неразъёмных соединений, то есть с помощью сварки. Если продукция не изготавливается серийно (такое характерно для всевозможных технологических трубопроводов, которые в основной свой массе практически всегда являются уникальным единичным изделием) применение схемы 5д не допустимо.
Остались вопросы?
С радостью ответим на них!
Для связи со специалистами:
Отправляйте заявки и вопросы по адресу @gstandard.ru
Россия: +7 (499) 753-01-54 – Москва +7 4742 562191 – Липецк
Германия: + 49 30 223-81-232
Гонконг: +852 3904-3394 ( asia@gstandard.ru )
Источник
УЧЕБНЫЙ ЦЕНТР «БАШНЕФТЕХИМ»
КУРС: ««Безопасная эксплуатация сосудов, работающих под избыточным давлением»
Тема: Документация на сосуд, назначение и содержание. Оперативная документация на рабочем месте персонала, обслуживающего сосуд.
Каждый сосуд должен поставляться изготовителем заказчику с паспортом установленной формы.
К паспорту должна быть приложена инструкция по монтажу и эксплуатации.
Паспорт сосуда должен быть составлен на русском языке и по требованию заказчика – на другом языке.
Допускается к паспорту прикладывать распечатки расчетов, выполненных на ЭВМ.
Элементы сосудов (корпуса, обечайки, днища, крышки, трубные решетки, фланцы корпуса, укрупненные сборочные единицы), предназначенные для реконструкции или ремонта, должны поставляться изготовителем с удостоверением о качестве изготовления, содержащим сведения в объеме согласно требованиям соответствующих разделов паспорта.
На каждом сосуде должна быть прикреплена табличка, выполненная в соответствии с ГОСТ 12971.
Для сосудов наружным диаметром менее 325 мм допускается табличку не устанавливать. При этом все необходимые данные должны быть нанесены на корпус сосуда электрографическим методом.
На табличке должны быть нанесены:
товарный знак или наименование изготовителя;
наименование или обозначение сосуда;
порядковый номер сосуда по системе нумерации изготовителя;
год изготовления;
рабочее давление, МПа;
расчетное давление, МПа;
пробное давление, МПа;
допустимая максимальная и (или) минимальная рабочая температура стенки, 0С;
масса сосуда, кг.
Для сосудов с самостоятельными полостями, имеющими разные расчетные и пробные давления, температуру стенок, следует указывать эти данные для каждой полости.
Штуцеры
Служат для присоединения к сосуду трубопроводов, трубопроводной арматуры, приборов КиП.
Дренажное устройство состоит из штуцера, запорного устройства и отводящего трубопровода и служит для слива воды после гидроиспытания и рабочей среды при опорожнении сосуда.
Располагается в наиболее низкой точке сосуда.
Воздушник состоит из штуцера и запорного устройства и служит для удаления воздуха при заполнении сосуда водой перед ГИ и для проверки отсутствия давления перед открытием сосуда.
Располагается в наиболее высокой точке сосуда.
Фланец – фасонная деталь, посредством которой к сосуду присоединяются трубопроводы, арматура, приборы КиП.
Фланцевое соединение состоит из двух фланцев, прокладки между ними и крепежных деталей.
По способу присоединения к трубопроводу фланцы бывают:
1) плоские приварные, применяются при Р < 2,5 МПа и Т среды < 300° С;
2) приварные встык, применяются при Р ≥ 2,5 МПа и Т среды ≥ 300° С.
Плоские приварные фланцы
Крепежные детали (болты, шпильки, гайки) предназначены для сборки фланцевых соединений, арматуры и крепления сосудов на опорах, опорных конструкциях.
Материалы крепежных изделий должны выбираться с коэффициентом линейного расширения, близким по значению к коэффициенту линейного расширения материала фланца.
Разница в значениях коэффициента линейного расширения не должна превышать 10 %.
Гайки и шпильки (болты) должны изготавливаться из сталей разных марок при изготовлении из стали одной марки – с разной твердостью, при этом твердость шпилек или болтов должна быть выше твердости гаек не менее, чем на 10-15 НВ.
Длина шпилек должна обеспечивать превышение резьбовой части над гайкой не менее 1 – 3 витков резьбы.
Болты применяют при Р< 2,5 МПа;
Шпильки применяют при Р ≥ 2,5 МПа, а также независимо от давления при Т> 300° С и Т < минус 40° С.
Каждый сосуд поставляется и эксплуатируется с паспортом, установленной формы, в котором указываются расчетные и рабочие параметры, расчетный срок службы сосуда, вся информация о материалах, из которых изготовлены все элементы сосуда: обечайка, днища, штуцера, фланцы.
На корпусе сосуда заводом-изготовителем наносится информация (маркировка) в виде четких и нестираемых надписей:
– наименование изготовителя;
– заводской номер;
– наименование сосуда
– дата изготовления;
– Рраб, Ррасч, Рпроб;
– минимальная и максимальная температура стенки сосуда;
– марка материала, из которого изготовлен сосуд.
Опора – устройство для установки сосуда в рабочем положении и передачи нагрузок от сосуда на фундамент или несущую конструкцию.
Классификация сосудов и группы рабочих сред
Категория сосуда выбирается в зависимости от максимального рабочего давления, вместимости сосуда и их произведения.
Группа рабочих сред – совокупность рабочих сред, подразделенных на:
группу 1, включающую рабочие среды, состоящие из воспламеняющихся, окисляющихся, горючих взрывчатых, токсичных и высокотоксичных газов, жидкостей и паров в однофазном состоянии, а также их смесей;
группу 2, включающую все прочие среды, не вошедшие в группу 1.
Материалы, применяемые для изготовления сосудов, должны обеспечивать их надежную работу в течение расчетного срока службы с учетом:
1) заданных расчетных параметров (Ррасч, минимальная отрицательная и максимальная расчетная температура);
2) состава и характера среды (коррозионность, взрывоопасность, токсичность);
3) влияния температуры окружающего воздуха.
Качество и свойства материалов должны быть подтверждены сертификатами и удовлетворять требованиям соответствующих стандартов.
Источник
Технический регламент Таможенного союза “О безопасности оборудования, работающего под избыточным давлением” (ТР ТС 032/2013) – устанавливает обязательные требования к оборудованию, работающему под избыточным давлением.
Рабочая среда это среда, находящаяся внутри оборудования, работающего под избыточным давлением.
В тр тс 032 2013 рабочие среды объединены в две группы.
К первой группе относятся воспламеняющиеся, окисляющиеся, горючие, взрывчатые, токсичных и высокотоксичных газов, жидкостей и паров в однофазном состоянии, а также их смесей.
Ко второй группе относятся все прочие рабочие среды, которые не отнесены к группе 1.
Технический регламент тр тс 032 2013 распространяется на следующие виды оборудования:
сосуды, предназначенные для газов, сжиженных газов, растворенных под давлением, и паров, используемые для рабочих сред группы 1, 2.
сосуды, предназначенные для жидкостей, используемые для рабочих сред группы 1, 2.
котлы, имеющие вместимость более 0,002 м, предназначенные для получения горячей воды, температура которой свыше 110°С, или пара, избыточное давление которого свыше 0,05 МПа, а также сосуды с огневым обогревом, имеющие вместимость более 0,002 м.
трубопроводы, имеющие максимально допустимое рабочее давление свыше 0,05 МПа, номинальный диаметр более 25 мм, предназначенные для газов и паров и используемые для рабочих сред группы 1.
трубопроводы, имеющие максимально допустимое рабочее давление свыше 0,05 МПа, номинальный диаметр более 32 мм и произведение значения максимально допустимого рабочего давления на значение номинального диаметра, составляющее свыше 100 МПа · мм, предназначенные для газов и паров и используемые для рабочих сред группы 2.
трубопроводы, имеющие максимально допустимое рабочее давление свыше 0,05 МПа, номинальный диаметр более 25 мм и произведение значения максимально допустимого рабочего давления на значение номинального диаметра, составляющее свыше 200 МПа · мм, предназначенные для жидкостей и используемые для рабочих сред группы 1.
трубопроводы, имеющие максимально допустимое рабочее давление свыше 1 МПа, номинальный диаметр более 200 мм и произведение значения максимально допустимого рабочего давления на значение номинального диаметра свыше 500 МПа · мм, предназначенные для жидкостей и используемые для рабочих сред группы 2.
элементы оборудования (сборочные единицы) и комплектующие к нему, выдерживающие воздействие давления
арматура, имеющая номинальный диаметр более 25 мм (для оборудования с рабочей средой группы 1), арматура, имеющая номинальный диаметр более 32 мм (для оборудования, используемого для газов с рабочей средой группы 2), арматура, имеющая номинальный диаметр более 200 мм (для трубопроводов, предназначенных для жидкостей и используемых для рабочих сред группы 2);
показывающие и предохранительные устройства;
барокамеры (кроме одноместных, медицинских);
устройства и приборы безопасности.
Технический регламент тр тс 032 2013 не распространяется на следующие виды продукции:
магистральные трубопроводы, внутрипромысловые и местные распределительные трубопроводы, предназначенные для транспортирования газа, нефти и других продуктов, за исключением оборудования, используемого на станциях регулирования давления или на компрессорных станциях;
сети газораспределения и сети газопотребления;
оборудование, специально сконструированное для использования в области атомной энергетики, оборудование, работающее с радиоактивной средой;
сосуды, работающие под давлением, создающимся при взрыве внутри них в соответствии с технологическим процессом или при горении в режиме самораспространяющегося высокотемпературного синтеза;
оборудование, специально сконструированное для использования на морских и речных судах и других плавучих средствах и объектах подводного применения;
тормозное оборудование подвижного состава железнодорожного транспорта, автотранспорта и иных средств передвижения;
сосуды, специально сконструированные для использования на самолетах и иных летательных аппаратах;
оборудование оборонного назначения;
части машин, не представляющие собой самостоятельные сосуды (корпуса насосов или турбин, цилиндры двигателей паровых, гидравлических, внутреннего сгорания, воздушных машин и компрессоров);
медицинские одноместные барокамеры;
оборудование с аэрозольными распылителями;
оболочки высоковольтного электрического оборудования (распределительных устройств, распределительных механизмов, трансформаторов и вращающихся электрических машин);
оболочки и кожуха элементов систем передачи электрической энергии (кабельной продукции электропитания и кабелей связи), работающие под избыточным давлением;
оборудование, изготовленное (произведенное) из неметаллической гибкой (эластичной) оболочки;
глушители шума выхлопа или всасывания газов;
емкости или сифоны для газированных напитков.
Формы подтверждения соответствия требованиям ТР ТС 032
На оборудование, работающее под избыточным давлением оформляются сертификат или декларация по схемам сертификации и декларирования указанных в тр тс 032.
Декларация соответствия тр тс 032 2013 оформляется на оборудование 1й и 2й категории.
Сертификат соответствия тр тс 032 2013 оформляется на оборудование 3й и 4й категории.
Для того что бы определить категорию оборудования нужно обратиться к приложению №1 тр тс 032 2013.
В таблицах 1-9 перечислены категории оборудования и характеристики, по которым определяется категория оборудования:
Вместимость оборудования;
Произведение значения максимально допустимого рабочего давления и значения вместимости;
Максимально допустимое рабочее давление;
Документы для оформления сертификата или декларации.
Обоснование безопасности;
Паспорт оборудования;
Руководство (инструкцию) по эксплуатации;
Проектную документацию;
Результаты прочностных расчетов и расчетов пропускной способности предохранительных устройств (при их наличии в соответствии с проектом);
Технологические регламенты и сведения о технологическом процессе (данные о применяемых материалах, полуфабрикатах, комплектующих, сварочных материалах, о способах и параметрах режимов сварки и термической обработке, методах и результатах неразрушающего контроля);
Сведения о проведенных испытаниях (измерениях);
Протоколы испытаний оборудования, проведенных изготовителем, уполномоченным изготовителем лицом и (или) аккредитованной испытательной лабораторией;
Документ о подтверждении характеристик материалов и комплектующих изделий (при наличии);
Сертификаты соответствия, декларации о соответствии или протоколы испытаний в отношении материалов, комплектующих изделий (при наличии);
Перечень стандартов, которые были применены при изготовлении (производстве) оборудования (в случае их применения изготовителем);
документы, подтверждающие квалификацию специалистов и персонала изготовителя;
иные документы, прямо или косвенно подтверждающие соответствие оборудования требованиям настоящего технического регламента (при наличии).
Расчет стоимости сертификата или декларации
Орган по сертификации АНО ДПО «ИПБ» аккредитован на ТР ТС 032.
Для того что бы определить сертификат или декларацию нужно оформлять на вашу продукцию потребуется предоставить следующие данные:
Наименование продукции;
Конкретная область применения;
Код ТН ВЭД ТС;
С газом или жидкостью работает оборудование;
К какой группе рабочих сред относится газ или жидкость;
Вместимость (объем) м3 или диаметр мм;
Температура воды (пара) для котлов;
Максимально допустимое рабочее давление, МПа.
Источник
Главная / Проектировщику / Справочная информация – ГОСТ СНИП ПБ / ГОСТ Р 52630-2012 /
Версия для печати
4.1 Общие требования
4.1.1 Конструкция сосудов должна быть технологичной, надежной в течение установленного в технической документации срока службы, обеспечивать безопасность при изготовлении, монтаже и эксплуатации, предусматривать возможность осмотра (в том числе внутренней поверхности), очистки, промывки, продувки и ремонта, контроля технического состояния сосуда при диагностировании, а также контроля за отсутствием давления и отбора среды перед открытием сосуда.
Если конструкция сосуда не позволяет при техническом освидетельствовании проведение осмотра (наружного или внутреннего), гидравлического испытания, то разработчик сосуда должен в технической документации на сосуд указать методику, периодичность и объем контроля сосуда, выполнение которых обеспечит своевременное выявление и устранение дефектов.
4.1.2 Срок службы сосуда устанавливает разработчик сосуда, и он указывается в технической документации.
4.1.3 При проектировании сосудов следует учитывать требования Правил перевозки грузов железнодорожным, водным и автомобильным транспортом.
Сосуды, которые не могут быть транспортированы в собранном виде, должны проектироваться из частей, соответствующих по габаритам требованиям к перевозке транспортными средствами. Деление сосуда на транспортируемые части следует указывать в технической документации.
4.1.4 Расчет на прочность сосудов и их элементов следует проводить в соответствии с ГОСТ Р 52857.1 – ГОСТ Р 52857.11, ГОСТ Р 51273, ГОСТ Р 51274, ГОСТ 30780.
Допускается использование настоящего стандарта совместно с другими международными и национальными стандартами на расчет на прочность при условии, что их требования не ниже требований российских национальных стандартов.
4.1.5 Сосуды, транспортируемые в собранном виде, а также транспортируемые части должны иметь строповые устройства (захватные приспособления) для проведения погрузочно-разгрузочных работ, подъема и установки сосудов в проектное положение.
Допускается использовать технологические штуцера, горловины, уступы, бурты и другие конструктивные элементы сосудов при подтверждении расчетом на прочность.
Конструкция, места расположения строповых устройств и конструктивных элементов для строповки, их количество, схема строповки сосудов и их транспортируемых частей должны быть указаны в технической документации.
4.1.6 Опрокидываемые сосуды должны иметь приспособления, предотвращающие самоопрокидывание.
4.1.7 В зависимости от расчетного давления, температуры стенки и характера рабочей среды сосуды подразделяют на группы. Группу сосуда определяет разработчик, но не ниже, чем указано в таблице 1.
Таблица 1 – Группы сосудов
Группа | Расчетное давление, МПа | Температура стенки, °С | Характеристика рабочей среды |
---|---|---|---|
1 | Независимо | Независимо | Взрывоопасная, пожароопасная, токсичная 1-го, 2-го, 3-го классов опасности по ГОСТ 12.1.007 |
2 | До 2,5 | Выше 400 | Любая, за исключением указанной для 1-й группы сосудов |
2,5 до 5,0 | Выше 200 | ||
5,0 и более | Независимо | ||
До 5,0 | Ниже минус 40 | ||
3 | До 2,5 | От минус 40 до 400 | |
От 2,5 до 5,0 | От минус 40 до 200 | ||
4 | До 1,6 | От минус 20 до 200 | |
5 | От вакуума до 0,07 | Независимо | Взрывобезопасная, пожаробезопасная или 4-го класса опасности по ГОСТ 12.1.007 |
Группу сосуда с полостями, имеющими различные расчетные параметры и среды, допускается определять для каждой полости отдельно.
4.1.8 Базовые диаметры сосудов рекомендуется принимать по ГОСТ 9617.
4.2 Днища, крышки, переходы
4.2.1 В сосудах применяют днища: эллиптические, полусферические, торосферические, сферические неотбортованные, конические отбортованные, конические неотбортованные, плоские отбортованные, плоские неотбортованные, плоские, присоединяемые на болтах.
4.2.2 Заготовки выпуклых днищ допускается изготовлять сварными из частей с расположением сварных швов согласно указанным на рисунке 1.
Рисунок 1 – Расположение сварных швов заготовок выпуклых днищ
Расстояния l и l1 от оси заготовки эллиптических и торосферических днищ до центра сварного шва должны быть не более 1/5 внутреннего диаметра днища. При этом для вариантов в), д), ж), и), к), л) сумма расстояний l + l1 должна быть не менее 1/5 внутреннего диаметра днища.
При изготовлении заготовок с расположением сварных швов согласно рисунку 1 м) количество лепестков не регламентируется.
4.2.3 Выпуклые днища допускается изготовлять из штампованных лепестков и шарового сегмента. Количество лепестков не регламентируется.
Если по центру днища устанавливают штуцер, то шаровой сегмент допускается не изготовлять.
4.2.4 Круговые швы выпуклых днищ, изготовленных из штампованных лепестков и шарового сегмента или заготовок с расположением сварных швов согласно рисунку 1 м, должны быть расположены от центра днища на расстоянии по проекции не более 1/3 внутреннего диаметра днища. Для полусферических днищ расположение круговых швов не регламентируется.
Наименьшее расстояние между меридиональными швами в месте их примыкания к шаровому сегменту или штуцеру, установленному по центру днища вместо шарового сегмента, а также между меридиональными швами и швом на шаровом сегменте, должно быть более трехкратной толщины днища, но не менее 100 мм по осям швов.
4.2.5 Основные размеры эллиптических днищ должны соответствовать ГОСТ 6533. Допускаются другие базовые диаметры эллиптических днищ при условии, что высота выпуклой части не менее 0,25 внутреннего диаметра днища.
4.2.6 Полусферические составные днища (см. рисунок 2) применяют в сосудах при выполнении следующих условий:
– нейтральные оси полушаровой части днища и переходной части обечайки корпуса должны совпадать; совпадение осей должно быть обеспечено соблюдением размеров, указанных в конструкторской документации;
– смещение t нейтральных осей полушаровой части днища и переходной части обечайки корпуса не должно превышать 0,5(S – S1);
– высота h переходной части обечайки корпуса должна быть не менее 3у.
Рисунок 2 – Узел соединения днища с обечайкой
4.2.7 Сферические неотбортованные днища допускается применять в сосудах 5-й группы, за исключением работающих под вакуумом.
Сферические неотбортованные днища в сосудах 1-й, 2-й, 3-й, 4-й групп и в сосудах, работающих под вакуумом, допускается применять только в качестве элемента фланцевых крышек.
Сферические неотбортованные днища (см. рисунок 3) должны:
– иметь радиус сферы R не менее 0,85D и не более D;
– привариваться сварным швом со сплошным проваром.
Рисунок 3 – Сферическое неотбортованное днище
4.2.8 Торосферические днища должны иметь:
– высоту выпуклой части, измеренную по внутренней поверхности, не менее 0,2 внутреннего диаметра днища;
– внутренний радиус отбортовки не менее 0,095 внутреннего диаметра днища;
– внутренний радиус кривизны центральной части не более внутреннего диаметра днища.
4.2.9 Конические неотбортованные днища или переходы допускается применять:
а) для сосудов 1-й, 2-й, 3-й, 4-й групп, если центральный угол при вершине конуса не более 45°. Допускается использование конических днищ и переходов с углом при вершине более 45° при условии дополнительного подтверждения их прочности расчетом по допускаемым напряжениям в соответствии с ГОСТ Р 52857.1, подраздел 8.10;
б) для сосудов, работающих под наружным давлением или вакуумом, если центральный угол при вершине конуса не более 60°.
Части выпуклых днищ в сочетании с коническими днищами или переходами применяют без ограничения угла при вершине конуса.
4.2.10 Плоские днища (см. рисунок 4), применяемые в сосудах 1-й, 2-й, 3-й, 4-й групп, следует изготовлять из поковок.
При этом следует выполнять следующие условия:
– расстояние от начала закругления до оси сварного шва не менее (D – внутренний диаметр обечайки, S – толщина обечайки);
– радиус закругления r ≥ 2,5S [см. рисунок 4а)];
– радиус кольцевой выточки r1 ≥ 2,5S, но не менее 8 мм [см. рисунок 4б)];
– наименьшая толщина днища [см. рисунок 4б)] в месте кольцевой выточки S2 ≥ 0,8S1, но не менее толщины обечайки S (S1 – толщина днища);
– длина отбортовки днищ h1 ≥ r;
– угол проточки γ должен составлять от 30° до 90°;
– зона А контролируется в направлениях Z согласно требованиям 5.4.2.
Рисунок 4 – Плоские днища
Допускается изготовление плоского днища (см. рисунок 4) из листа, если отбортовка выполняется штамповкой или обкаткой кромки листа с изгибом на 90°.
4.2.11 Основные размеры плоских днищ, предназначенных для сосудов 5-й группы, должны соответствовать ГОСТ 12622 или ГОСТ 12623.
4.2.12 Длина цилиндрического борта l (l – расстояние от начала закругления отбортованного элемента до окончательно обработанной кромки) в зависимости от толщины стенки S (см. рисунок 5) для отбортованных и переходных элементов сосудов, за исключением штуцеров, компенсаторов и выпуклых днищ, должна быть не менее указанной в таблице 2. Радиус отбортовки R ≥ 2,5S.
Рисунок 5 – Отбортованный и переходный элементы
Таблица 2 – Длина цилиндрического борта
Толщина стенки S, мм | Длина цилиндрического борта l, мм, не менее |
---|---|
До 5 включ. | 15 |
Св. 5 до 10 включ. | 2S + 5 |
Св. 10 до 20 включ. | S + 15 |
Св. 20 до 150 включ. | S/2 + 25 |
Св. 150 | 100 |
4.3 Люки, лючки, бобышки и штуцера
4.3.1 Сосуды должны быть снабжены люками или смотровыми лючками, обеспечивающими осмотр, очистку, безопасность работ по защите от коррозии, монтаж и демонтаж разборных внутренних устройств, ремонт и контроль сосудов. Количество люков и лючков определяет разработчик сосуда. Люки и лючки необходимо располагать в доступных для пользования местах.
4.3.2 Сосуды с внутренним диаметром более 800 мм должны иметь люки.
Внутренний диаметр люка круглой формы у сосудов, устанавливаемых на открытом воздухе, должен быть не менее 450 мм, а у сосудов, располагаемых в помещении, – не менее 400 мм. Размер люков овальной формы по наименьшей и наибольшей осям должен быть не менее 325×400 мм.
Внутренний диаметр люка у сосудов, не имеющих корпусных фланцевых разъемов и подлежащих внутренней антикоррозионной защите неметаллическими материалами, должен быть не менее 800 мм.
Допускается проектировать без люков:
– сосуды, предназначенные для работы с веществами 1-го и 2-го классов опасности по ГОСТ 12.1.007, не вызывающими коррозии и накипи, независимо от их диаметра, при этом следует предусмотреть необходимое количество смотровых лючков;
– сосуды с приварными рубашками и кожухотрубчатые теплообменные аппараты независимо от их диаметра;
– сосуды, имеющие съемные днища или крышки, а также обеспечивающие возможность проведения внутреннего осмотра без демонтажа трубопровода горловины или штуцера.
4.3.3 Сосуды с внутренним диаметром не более 800 мм должны иметь круглый или овальный лючок. Размер лючка по наименьшей оси должен быть не менее 80 мм.
4.3.4 Каждый сосуд должен иметь бобышки или штуцера для наполнения водой и слива, удаления воздуха при гидравлическом испытании. Для этой цели допускается использовать технологические бобышки и штуцера.
Штуцера и бобышки на вертикальных сосудах должны быть расположены с учетом возможности проведения гидравлического испытания как в вертикальном, так и в горизонтальном положениях.
4.3.5 Для крышек люков массой более 20 кг должны быть предусмотрены приспособления для облегчения их открывания и закрывания.
4.3.6 Шарнирно-откидные или вставные болты, закладываемые в прорези, хомуты и другие зажимные приспособления люков, крышек и фланцев должны быть предохранены от сдвига или ослабления.
4.4 Расположение отверстий
4.4.1 Расположение отверстий в эллиптических и полусферических днищах не регламентируется.
Расположение отверстий на торосферических днищах допускается в пределах центрального сферического сегмента. При этом расстояние от наружной кромки отверстия до центра днища, измеряемое по хорде, должно быть не более 0,4 наружного диаметра днища.
4.4.2 Отверстия для люков, лючков и штуцеров в сосудах 1-й, 2-й, 3-й, 4-й групп должны быть расположены, как правило, вне сварных швов.
Расположение отверстий допускается:
– на продольных швах цилиндрических и конических обечаек сосудов, если диаметр отверстий не более 150 мм;
– кольцевых швах цилиндрических и конических обечаек сосудов без ограничения диаметра отверстий;
– швах выпуклых днищ без ограничения диаметра отверстий при условии 100-процентной проверки сварных швов днищ радиографическим или ультразвуковым методом;
– швах плоских днищ.
4.4.3 Отверстия не разрешается располагать в местах пересечения сварных швов сосудов 1-й, 2-й, 3-й, 4-й групп.
Данное требование не распространяется на случай, оговоренный в 4.2.3.
4.4.4 Отверстия для люков, лючков, штуцеров в сосудах 5-й группы разрешается устанавливать на сварных швах без ограничения по диаметру.
4.5 Требования к опорам
4.5.1 Опоры из углеродистых сталей допускается применять для сосудов из коррозионно-стойких сталей при условии, что к сосуду приваривается переходная обечайка опоры из коррозионно-стойкой стали высотой, определяемой расчетом, выполненным разработчиком сосуда.
4.5.2 Для горизонтальных сосудов угол охвата седловой опоры, как правило, должен быть не менее 120°.
4.5.3 При наличии температурных расширений в продольном направлении в горизонтальных сосудах следует выполнять неподвижной лишь одну седловую опору, остальные опоры – подвижными. Указание об этом должно содержаться в технической документации.
4.6 Требования к внутренним и наружным устройствам
4.6.1 Внутренние устройства в сосудах (змеевики, тарелки, перегородки и др.), препятствующие осмотру и ремонту, как правило, должны быть съемными.
При использовании приварных устройств следует выполнять требования 4.1.1.
4.6.2 Внутренние и наружные приварные устройства необходимо конструировать так, чтобы были обеспечены удаление воздуха и полное опорожнение аппарата при гидравлическом испытании в горизонтальном и вертикальном положениях.
4.6.3 Рубашки и змеевики, применяемые для наружного обогрева или охлаждения сосудов, могут быть съемными и приварными.
4.6.4 Все глухие части сборочных единиц и элементов внутренних устройств должны иметь дренажные отверстия для обеспечения полного слива (опорожнения) жидкости в случае остановки сосуда.
<< назад / к содержанию ГОСТа Р 52630-2012 / вперед >>
Источник