Ребра жесткости в сосуде под давлением
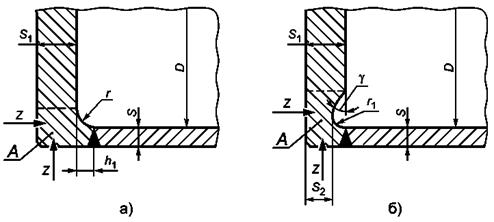
Версия для печати
4.1 Общие требования
4.1.1 Конструкция сосудов должна быть технологичной, надежной в течение установленного в технической документации срока службы, обеспечивать безопасность при изготовлении, монтаже и эксплуатации, предусматривать возможность осмотра (в том числе внутренней поверхности), очистки, промывки, продувки и ремонта, контроля технического состояния сосуда при диагностировании, а также контроля за отсутствием давления и отбора среды перед открытием сосуда.
Если конструкция сосуда не позволяет при техническом освидетельствовании проведение осмотра (наружного или внутреннего), гидравлического испытания, то разработчик сосуда должен в технической документации на сосуд указать методику, периодичность и объем контроля сосуда, выполнение которых обеспечит своевременное выявление и устранение дефектов.
4.1.2 Срок службы сосуда устанавливает разработчик сосуда, и он указывается в технической документации.
4.1.3 При проектировании сосудов следует учитывать требования Правил перевозки грузов железнодорожным, водным и автомобильным транспортом.
Сосуды, которые не могут быть транспортированы в собранном виде, должны проектироваться из частей, соответствующих по габаритам требованиям к перевозке транспортными средствами. Деление сосуда на транспортируемые части следует указывать в технической документации.
4.1.4 Расчет на прочность сосудов и их элементов следует проводить в соответствии с ГОСТ Р 52857.1 – ГОСТ Р 52857.11, ГОСТ Р 51273, ГОСТ Р 51274, ГОСТ 30780.
Допускается использование настоящего стандарта совместно с другими международными и национальными стандартами на расчет на прочность при условии, что их требования не ниже требований российских национальных стандартов.
4.1.5 Сосуды, транспортируемые в собранном виде, а также транспортируемые части должны иметь строповые устройства (захватные приспособления) для проведения погрузочно-разгрузочных работ, подъема и установки сосудов в проектное положение.
Допускается использовать технологические штуцера, горловины, уступы, бурты и другие конструктивные элементы сосудов при подтверждении расчетом на прочность.
Конструкция, места расположения строповых устройств и конструктивных элементов для строповки, их количество, схема строповки сосудов и их транспортируемых частей должны быть указаны в технической документации.
4.1.6 Опрокидываемые сосуды должны иметь приспособления, предотвращающие самоопрокидывание.
4.1.7 В зависимости от расчетного давления, температуры стенки и характера рабочей среды сосуды подразделяют на группы. Группу сосуда определяет разработчик, но не ниже, чем указано в таблице 1.
Таблица 1 – Группы сосудов
Группа | Расчетное давление, МПа | Температура стенки, °С | Характеристика рабочей среды |
---|---|---|---|
1 | Независимо | Независимо | Взрывоопасная, пожароопасная, токсичная 1-го, 2-го, 3-го классов опасности по ГОСТ 12.1.007 |
2 | До 2,5 | Выше 400 | Любая, за исключением указанной для 1-й группы сосудов |
2,5 до 5,0 | Выше 200 | ||
5,0 и более | Независимо | ||
До 5,0 | Ниже минус 40 | ||
3 | До 2,5 | От минус 40 до 400 | |
От 2,5 до 5,0 | От минус 40 до 200 | ||
4 | До 1,6 | От минус 20 до 200 | |
5 | От вакуума до 0,07 | Независимо | Взрывобезопасная, пожаробезопасная или 4-го класса опасности по ГОСТ 12.1.007 |
Группу сосуда с полостями, имеющими различные расчетные параметры и среды, допускается определять для каждой полости отдельно.
4.1.8 Базовые диаметры сосудов рекомендуется принимать по ГОСТ 9617.
4.2 Днища, крышки, переходы
4.2.1 В сосудах применяют днища: эллиптические, полусферические, торосферические, сферические неотбортованные, конические отбортованные, конические неотбортованные, плоские отбортованные, плоские неотбортованные, плоские, присоединяемые на болтах.
4.2.2 Заготовки выпуклых днищ допускается изготовлять сварными из частей с расположением сварных швов согласно указанным на рисунке 1.
Рисунок 1 – Расположение сварных швов заготовок выпуклых днищ
Расстояния l и l1 от оси заготовки эллиптических и торосферических днищ до центра сварного шва должны быть не более 1/5 внутреннего диаметра днища. При этом для вариантов в), д), ж), и), к), л) сумма расстояний l + l1 должна быть не менее 1/5 внутреннего диаметра днища.
При изготовлении заготовок с расположением сварных швов согласно рисунку 1 м) количество лепестков не регламентируется.
4.2.3 Выпуклые днища допускается изготовлять из штампованных лепестков и шарового сегмента. Количество лепестков не регламентируется.
Если по центру днища устанавливают штуцер, то шаровой сегмент допускается не изготовлять.
4.2.4 Круговые швы выпуклых днищ, изготовленных из штампованных лепестков и шарового сегмента или заготовок с расположением сварных швов согласно рисунку 1 м, должны быть расположены от центра днища на расстоянии по проекции не более 1/3 внутреннего диаметра днища. Для полусферических днищ расположение круговых швов не регламентируется.
Наименьшее расстояние между меридиональными швами в месте их примыкания к шаровому сегменту или штуцеру, установленному по центру днища вместо шарового сегмента, а также между меридиональными швами и швом на шаровом сегменте, должно быть более трехкратной толщины днища, но не менее 100 мм по осям швов.
4.2.5 Основные размеры эллиптических днищ должны соответствовать ГОСТ 6533. Допускаются другие базовые диаметры эллиптических днищ при условии, что высота выпуклой части не менее 0,25 внутреннего диаметра днища.
4.2.6 Полусферические составные днища (см. рисунок 2) применяют в сосудах при выполнении следующих условий:
– нейтральные оси полушаровой части днища и переходной части обечайки корпуса должны совпадать; совпадение осей должно быть обеспечено соблюдением размеров, указанных в конструкторской документации;
– смещение t нейтральных осей полушаровой части днища и переходной части обечайки корпуса не должно превышать 0,5(S – S1);
– высота h переходной части обечайки корпуса должна быть не менее 3у.
Рисунок 2 – Узел соединения днища с обечайкой
4.2.7 Сферические неотбортованные днища допускается применять в сосудах 5-й группы, за исключением работающих под вакуумом.
Сферические неотбортованные днища в сосудах 1-й, 2-й, 3-й, 4-й групп и в сосудах, работающих под вакуумом, допускается применять только в качестве элемента фланцевых крышек.
Сферические неотбортованные днища (см. рисунок 3) должны:
– иметь радиус сферы R не менее 0,85D и не более D;
– привариваться сварным швом со сплошным проваром.
Рисунок 3 – Сферическое неотбортованное днище
4.2.8 Торосферические днища должны иметь:
– высоту выпуклой части, измеренную по внутренней поверхности, не менее 0,2 внутреннего диаметра днища;
– внутренний радиус отбортовки не менее 0,095 внутреннего диаметра днища;
– внутренний радиус кривизны центральной части не более внутреннего диаметра днища.
4.2.9 Конические неотбортованные днища или переходы допускается применять:
а) для сосудов 1-й, 2-й, 3-й, 4-й групп, если центральный угол при вершине конуса не более 45°. Допускается использование конических днищ и переходов с углом при вершине более 45° при условии дополнительного подтверждения их прочности расчетом по допускаемым напряжениям в соответствии с ГОСТ Р 52857.1, подраздел 8.10;
б) для сосудов, работающих под наружным давлением или вакуумом, если центральный угол при вершине конуса не более 60°.
Части выпуклых днищ в сочетании с коническими днищами или переходами применяют без ограничения угла при вершине конуса.
4.2.10 Плоские днища (см. рисунок 4), применяемые в сосудах 1-й, 2-й, 3-й, 4-й групп, следует изготовлять из поковок.
При этом следует выполнять следующие условия:
– расстояние от начала закругления до оси сварного шва не менее (D – внутренний диаметр обечайки, S – толщина обечайки);
– радиус закругления r ≥ 2,5S [см. рисунок 4а)];
– радиус кольцевой выточки r1 ≥ 2,5S, но не менее 8 мм [см. рисунок 4б)];
– наименьшая толщина днища [см. рисунок 4б)] в месте кольцевой выточки S2 ≥ 0,8S1, но не менее толщины обечайки S (S1 – толщина днища);
– длина отбортовки днищ h1 ≥ r;
– угол проточки γ должен составлять от 30° до 90°;
– зона А контролируется в направлениях Z согласно требованиям 5.4.2.
Рисунок 4 – Плоские днища
Допускается изготовление плоского днища (см. рисунок 4) из листа, если отбортовка выполняется штамповкой или обкаткой кромки листа с изгибом на 90°.
4.2.11 Основные размеры плоских днищ, предназначенных для сосудов 5-й группы, должны соответствовать ГОСТ 12622 или ГОСТ 12623.
4.2.12 Длина цилиндрического борта l (l – расстояние от начала закругления отбортованного элемента до окончательно обработанной кромки) в зависимости от толщины стенки S (см. рисунок 5) для отбортованных и переходных элементов сосудов, за исключением штуцеров, компенсаторов и выпуклых днищ, должна быть не менее указанной в таблице 2. Радиус отбортовки R ≥ 2,5S.
Рисунок 5 – Отбортованный и переходный элементы
Таблица 2 – Длина цилиндрического борта
Толщина стенки S, мм | Длина цилиндрического борта l, мм, не менее |
---|---|
До 5 включ. | 15 |
Св. 5 до 10 включ. | 2S + 5 |
Св. 10 до 20 включ. | S + 15 |
Св. 20 до 150 включ. | S/2 + 25 |
Св. 150 | 100 |
4.3 Люки, лючки, бобышки и штуцера
4.3.1 Сосуды должны быть снабжены люками или смотровыми лючками, обеспечивающими осмотр, очистку, безопасность работ по защите от коррозии, монтаж и демонтаж разборных внутренних устройств, ремонт и контроль сосудов. Количество люков и лючков определяет разработчик сосуда. Люки и лючки необходимо располагать в доступных для пользования местах.
4.3.2 Сосуды с внутренним диаметром более 800 мм должны иметь люки.
Внутренний диаметр люка круглой формы у сосудов, устанавливаемых на открытом воздухе, должен быть не менее 450 мм, а у сосудов, располагаемых в помещении, – не менее 400 мм. Размер люков овальной формы по наименьшей и наибольшей осям должен быть не менее 325×400 мм.
Внутренний диаметр люка у сосудов, не имеющих корпусных фланцевых разъемов и подлежащих внутренней антикоррозионной защите неметаллическими материалами, должен быть не менее 800 мм.
Допускается проектировать без люков:
– сосуды, предназначенные для работы с веществами 1-го и 2-го классов опасности по ГОСТ 12.1.007, не вызывающими коррозии и накипи, независимо от их диаметра, при этом следует предусмотреть необходимое количество смотровых лючков;
– сосуды с приварными рубашками и кожухотрубчатые теплообменные аппараты независимо от их диаметра;
– сосуды, имеющие съемные днища или крышки, а также обеспечивающие возможность проведения внутреннего осмотра без демонтажа трубопровода горловины или штуцера.
4.3.3 Сосуды с внутренним диаметром не более 800 мм должны иметь круглый или овальный лючок. Размер лючка по наименьшей оси должен быть не менее 80 мм.
4.3.4 Каждый сосуд должен иметь бобышки или штуцера для наполнения водой и слива, удаления воздуха при гидравлическом испытании. Для этой цели допускается использовать технологические бобышки и штуцера.
Штуцера и бобышки на вертикальных сосудах должны быть расположены с учетом возможности проведения гидравлического испытания как в вертикальном, так и в горизонтальном положениях.
4.3.5 Для крышек люков массой более 20 кг должны быть предусмотрены приспособления для облегчения их открывания и закрывания.
4.3.6 Шарнирно-откидные или вставные болты, закладываемые в прорези, хомуты и другие зажимные приспособления люков, крышек и фланцев должны быть предохранены от сдвига или ослабления.
4.4 Расположение отверстий
4.4.1 Расположение отверстий в эллиптических и полусферических днищах не регламентируется.
Расположение отверстий на торосферических днищах допускается в пределах центрального сферического сегмента. При этом расстояние от наружной кромки отверстия до центра днища, измеряемое по хорде, должно быть не более 0,4 наружного диаметра днища.
4.4.2 Отверстия для люков, лючков и штуцеров в сосудах 1-й, 2-й, 3-й, 4-й групп должны быть расположены, как правило, вне сварных швов.
Расположение отверстий допускается:
– на продольных швах цилиндрических и конических обечаек сосудов, если диаметр отверстий не более 150 мм;
– кольцевых швах цилиндрических и конических обечаек сосудов без ограничения диаметра отверстий;
– швах выпуклых днищ без ограничения диаметра отверстий при условии 100-процентной проверки сварных швов днищ радиографическим или ультразвуковым методом;
– швах плоских днищ.
4.4.3 Отверстия не разрешается располагать в местах пересечения сварных швов сосудов 1-й, 2-й, 3-й, 4-й групп.
Данное требование не распространяется на случай, оговоренный в 4.2.3.
4.4.4 Отверстия для люков, лючков, штуцеров в сосудах 5-й группы разрешается устанавливать на сварных швах без ограничения по диаметру.
4.5 Требования к опорам
4.5.1 Опоры из углеродистых сталей допускается применять для сосудов из коррозионно-стойких сталей при условии, что к сосуду приваривается переходная обечайка опоры из коррозионно-стойкой стали высотой, определяемой расчетом, выполненным разработчиком сосуда.
4.5.2 Для горизонтальных сосудов угол охвата седловой опоры, как правило, должен быть не менее 120°.
4.5.3 При наличии температурных расширений в продольном направлении в горизонтальных сосудах следует выполнять неподвижной лишь одну седловую опору, остальные опоры – подвижными. Указание об этом должно содержаться в технической документации.
4.6 Требования к внутренним и наружным устройствам
4.6.1 Внутренние устройства в сосудах (змеевики, тарелки, перегородки и др.), препятствующие осмотру и ремонту, как правило, должны быть съемными.
При использовании приварных устройств следует выполнять требования 4.1.1.
4.6.2 Внутренние и наружные приварные устройства необходимо конструировать так, чтобы были обеспечены удаление воздуха и полное опорожнение аппарата при гидравлическом испытании в горизонтальном и вертикальном положениях.
4.6.3 Рубашки и змеевики, применяемые для наружного обогрева или охлаждения сосудов, могут быть съемными и приварными.
4.6.4 Все глухие части сборочных единиц и элементов внутренних устройств должны иметь дренажные отверстия для обеспечения полного слива (опорожнения) жидкости в случае остановки сосуда.
<< назад / к содержанию ГОСТа Р 52630-2012 / вперед >>
Источник
1 Область применения
Настоящий стандарт устанавливает нормы и методы расчета на прочность цилиндрических обечаек, конических элементов, выпуклых днищ и плоских крышек сосудов и аппаратов, применяемых в химической, нефтехимической, нефтеперерабатывающей и смежных отраслях промышленности, работающих в условиях однократных 1) статических нагрузок под внутренним избыточным давлением, вакуумом или наружным давлением, под действием осевых и поперечных усилий и изгибающих моментов. Нормы и методы расчета на прочность применимы, если отклонение от геометрической формы и неточности изготовления рассчитываемых элементов сосудов не превышают допусков, установленных нормативными документами.
Настоящий стандарт применим совместно с ГОСТ Р 52857.1.
1) Нормы и методы расчета применяются также при многократных нагрузках при условии, что количество циклов и размах нагрузок не превышают значений, при которых по ГОСТ Р 52857.6 необходимо проводить расчет на малоцикловую прочность.
2 Нормативные ссылки
В настоящем стандарте использованы нормативные ссылки на следующие стандарты:
ГОСТ Р 52857.1-2007 Сосуды и аппараты. Нормы и методы расчета на прочность. Общие требования
ГОСТ Р 52857.3-2007 Сосуды и аппараты. Нормы и методы расчета на прочность. Укрепление отверстий в обечайках и днищах при внутреннем и внешнем давлениях. Расчет на прочность обечаек и днищ при внешних статических нагрузках на штуцер
ГОСТ Р 52857.6-2007 Сосуды и аппараты. Нормы и методы расчета на прочность. Расчет на прочность при малоцикловых нагрузках
ГОСТ Р 52857.8-2007 Сосуды и аппараты. Нормы и методы расчета на прочность. Сосуды и аппараты с рубашками
Примечание — При пользовании настоящим стандартом целесообразно проверить действие ссылочных стандартов в информационной системе общего пользования — на официальном сайте Федерального агентства по техническому регулированию и метрологии в сети Интернет или по ежегодно издаваемому информационному указателю «Национальные стандарты», который опубликован по состоянию на 1 января текущего года, и по соответствующим ежемесячно издаваемым информационным указателям, опубликованным в текущем году. Если ссылочный стандарт заменен (изменен), то при пользовании настоящим стандартом следует руководствоваться заменяющим (измененным) стандартом. Если ссылочный стандарт отменен без замены, то положение, в котором дана ссылка на него, применяется в части, не затрагивающей эту ссылку.
3 Обозначения
В настоящем стандарте применены следующие обозначения:
А к — площадь поперечного сечения кольца жесткости, мм 2 ;
А р — площадь поперечного сечения ребра жесткости, мм 2 ;
а — ширина кольца жесткости у сферического днища или крышки, мм;
а 1р , а2р — расчетные длины переходных частей обечаек, мм;
а 1 , а2 — фактические длины переходных частей обечаек, мм;
b — расстояние между двумя смежными кольцами жесткости, мм;
bi ( i = 1, 2, 3, . n ) — длины хорд отверстий в днищах, мм;
с — сумма прибавок к расчетным толщинам стенок, мм;
с 1 — прибавка для компенсации коррозии и эрозии, мм;
с 2 — прибавка для компенсации минусового допуска, мм;
с 3 — технологическая прибавка, мм;
D — внутренний диаметр сосуда или аппарата, мм;
D с.п — средний диаметр прокладки, мм (см);
DE — эффективный диаметр конической обечайки при внешнем давлении, мм;
DF — эффективный диаметр конической обечайки при осевом сжатии и изгибе, мм;
D к — расчетный диаметр гладкой конической обечайки, мм;
D p — расчетный диаметр днища (крышки) и конической обечайки, мм;
D 1 — наружный диаметр сосуда или аппарата, а также диаметр меньшего основания конической обечайки, мм;
D 2 — наименьший диаметр наружной утоненной части крышки, мм;
D 3 — диаметр болтовой окружности, мм;
d — диаметр отверстия в днище или крышке, мм;
d б — диаметр отверстия под болт (шпильку), мм;
d о — наружный диаметр центральной втулки, мм;
di ( i = 1, 2, 3, . n ) — диаметр отверстий в днищах, мм;
Е — модуль продольной упругости при расчетной температуре, МПа;
е — расстояние между центром тяжести поперечного сечения кольца жесткости и срединной поверхностью обечайки, мм;
е o — расстояние от центра тяжести поперечного сечения ребра жесткости до его основания, мм;
е 1 — расстояние от точки пересечения средней линии стенки сферического сегмента с кольцом до горизонтальной оси, проходящей через центр тяжести кольца, мм;
е 2 — расстояние от окружности расположения болтов до внутреннего диаметра кольца, мм;
е 3 — расстояние от окружности расположения болтов до линии действия реакции прокладки, мм;
е 4 — расстояние от срединной поверхности пластины крышки с ребрами до нейтральной поверхности, мм;
F — расчетное осевое растягивающее или сжимающее усилие (без учета нагрузки, возникающей от внутреннего избыточного или наружного давления), Н;
[ F ] — допускаемое растягивающее или сжимающее усилие, Н;
[ F ] E — допускаемое осевое сжимающее усилие из условия устойчивости в пределах упругости, Н;
[ F ]п — допускаемое осевое сжимающее усилие из условия прочности при φ = 1, Н;
[ F ] E 1 — допускаемое осевое сжимающее усилие, определяемое из условия местной устойчивости в пределах упругости, Н;
[ F ] E 2 — допускаемое осевое сжимающее усилие, определяемое из условия общей устойчивости в пределах упругости, Н;
Н — высота выпуклой части днища без учета цилиндрической части, мм;
h 3 — расстояние от нижней поверхности крышки (днища) до нижнего торца втулки, мм;
h — высота кольца, мм;
h 1 — длина цилиндрической части отбортовки днищ, мм;
h 2 — высота сечения кольца жесткости, измеряемая от срединной поверхности обечайки, мм;
h 3 — расстояние от нижней поверхности крышки (днища) до нижнего торца втулки, мм;
I — эффективный момент инерции расчетного поперечного сечения кольца жесткости, мм 4 ;
I к — момент инерции поперечного сечения кольца жесткости относительно оси, проходящей через центр тяжести поперечного сечения кольца (относительно оси X — X ), мм 4 ;
I р — расчетный эффективный момент инерции расчетного поперечного сечения кольца жесткости, мм 4 ;
К — коэффициент конструкции плоских днищ и крышек;
k — коэффициент жесткости обечайки, подкрепленной кольцами жесткости;
К o — коэффициент ослабления плоских днищ (крышек) отверстием;
К р — поправочный коэффициент;
Кэ — коэффициент приведения радиуса кривизны эллиптического днища;
К с — коэффициент тонкостенности сферических днищ;
L — расчетная длина цилиндрической обечайки, укрепленной кольцами жесткости, мм;
l — расчетная длина гладкой обечайки, мм;
l Е — эффективная длина конической обечайки, мм;
l е — эффективная длина стенки обечайки, учитываемая при определении эффективного момента инерции, мм;
l пр — приведенная длина, мм;
l 1 — расстояние между двумя кольцами жесткости по осям, проходящим через центр тяжести поперечного сечения колец жесткости, мм;
l 2 — расстояние между крайними кольцами жесткости и следующими эффективными элементами жесткости, мм;
l 3 — длина примыкающего элемента, учитываемая при определении расчетной длины / или L , мм;
М — расчетный изгибающий момент, Н·мм;
[М] — допускаемый изгибающий момент, Н·мм;
п — число радиальных ребер;
[М]Е — допускаемый изгибающий момент из условия устойчивости в пределах упругости, Н·мм;
[М]п — допускаемый изгибающий момент из условия прочности при φ = 1, Н·мм;
п у — коэффициент запаса устойчивости;
р — расчетное внутреннее избыточное или наружное давление, МПа;
Р F — эквивалентное давление при нагружении осевым усилием, МПа;
р м — эквивалентное давление при нагружении изгибающим моментом, МПа;
[р] — допускаемое внутреннее избыточное или наружное давление, МПа;
[р] E — допускаемое наружное давление из условия устойчивости в пределах упругости, МПа;
[р]п — допускаемое наружное давление из условия прочности при φ = 1, МПа;
[ p ]1 — допускаемое внутреннее избыточное давление или наружное, определяемое из условия прочности или устойчивости всей обечайки (с кольцами жесткости), МПа;
[р]1E — допускаемое наружное давление из условия устойчивости всей обечайки (с кольцами жесткости) в пределах упругости, МПа;
[р]1п — допускаемое наружное давление из условия прочности всей обечайки при φ = 1, МПа;
[р]2 — допускаемое внутреннее избыточное давление или наружное, определяемое из условия прочности или устойчивости обечайки между двумя соседними кольцами жесткости, МПа;
[ Q ] E — допускаемое поперечное усилие из условия устойчивости в пределах упругости, Н;
[ Q ]п — допускаемое поперечное усилие из условия прочности при φ = 1, Н;
Q — расчетное поперечное усилие, Н;
Q — дополнительное усилие, действующее на центральную часть крышки с ребрами, Н;
[ Q ] — допускаемое поперечное усилие, Н;
R — радиус кривизны в вершине днища по внутренней поверхности, мм;
R c — радиус кривизны сферического сегмента по внутренней поверхности, мм;
r — внутренний радиус отбортовки конической обечайки (днища), мм;
R б — болтовая нагрузка, Н;
R п — реакция прокладки, Н;
r 1 — наружный радиус отбортовки торосферического днища, мм;
s — исполнительная толщина стенки обечайки, мм;
s к — исполнительная толщина стенки конической обечайки, мм;
s п — толщина крышки в месте уплотнения, мм;
s p — расчетная толщина стенки обечайки или днища, мм;
s к.p — расчетная толщина стенки конической обечайки, мм;
s 1p — расчетная толщина стенки днища (крышки) или переходной части конической обечайки, мм;
s 2p — расчетная толщина стенки переходной части обечайки, мм;
s т — исполнительная толщина стенки тороидального перехода конической обечайки, мм;
s ‘ — исполнительная толщина стенки пологого конического днища, мм;
s т.p — расчетная толщина стенки переходной части с тороидальным переходом, мм;
s 1э ; s 2э — эффективные толщины стенок переходной части обечаек, мм;
s 1 — исполнительная толщина стенки днища (крышки) или переходной части конической обечайки, мм;
s 2 — исполнительная толщина стенки переходной части обечайки, мм;
s 3 — толщина крышки вне уплотнения, мм;
s 4 — толщина утоненной части днища в месте кольцевой выточки, мм;
s 5 — исполнительная толщина выступающей выше днища части обечайки, мм;
t — ширина поперечного сечения кольца жесткости в месте его приварки к обечайке, мм;
tj — несущая ширина кольцевого сварного шва, мм;
α; α1; α2 — половина угла раствора при вершине конической обечайки, град;
χ — отношение допускаемых напряжений
λ — гибкость элемента;
ψ — угол между касательной к сферическому сегменту в краевой зоне и вертикальной осью, град;
[σ] — допускаемое напряжение при расчетной температуре, МПа;
[σ]20 — допускаемое напряжение при температуре 20 °С, МПа;
[σ]к — допускаемое напряжение для ребра жесткости при расчетной температуре, МПа;
[σ]1, [σ]2, [σ]5 — допускаемое напряжение для частей сосуда (цилиндрических, конических, сферических) при расчетной температуре, МПа;
[σ]р — допускаемое напряжение для ребра жесткости, МПа;
[σ]в — допускаемое напряжение для втулки, МПа;
Σd 1 — максимальная сумма длин хорд отверстий в наиболее ослабленном диаметральном сечении днища или крышки, мм;
φ — коэффициенты прочности сварных швов;
φк — коэффициент прочности сварных швов кольца жесткости;
φр — коэффициент прочности продольного сварного шва;
φт — коэффициент прочности кольцевого сварного шва;
φ1 — коэффициент снижения допускаемых напряжений при расчете на устойчивость из условия местной устойчивости при осевом сжатии;
φ2 — коэффициент снижения допускаемых напряжений при расчете на устойчивость из условия общей устойчивости при осевом сжатии;
φ3 — коэффициент снижения допускаемых напряжений при расчете на устойчивость из условия местной устойчивости при изгибе.
4 Общие положения
4.1 Приведенный в настоящем стандарте расчет применим при выполнении требований ГОСТ Р 52857.1 .
4.2 В основу расчетных формул, приведенных в настоящем стандарте, при оценке прочности положен метод предельных нагрузок. При расчете на устойчивость от внешнего давления, при вакууме, а также от других нагрузок, вызывающих сжимающее напряжение, в качестве предельного состояния принято достижение нижних критических напряжений.
4.3 При одновременном действии нескольких нагрузок (давления, осевого сжатия и т.п.) условие прочности (устойчивости) проверяют на основе линейного суммирования повреждений, за исключением случаев, когда имеются более точные решения.
4.4 В настоящем стандарте приведены формулы для определения исполнительных размеров элементов сосудов и аппаратов при проектировочном расчете и определении допускаемых нагрузок при поверочном расчете.
5 Расчет цилиндрических обечаек
5.1 Расчетные схемы
5.1.1 Расчетные схемы цилиндрических обечаек приведены на рисунках 1-4.
а — обечайка с фланцем или с плоским днищем; б — обечайка с жесткими перегородками
Рисунок 1 — Гладкие цилиндрические обечайки
а — обечайка с отбортованными днищами; б — обечайка с неотбортованными днищами
Рисунок 2 — Гладкие обечайки с выпуклыми или коническими днищами
Рисунок 3 — Гладкие обечайки с рубашкой
Рисунок 4 — Цилиндрическая обечайка, подкрепленная кольцами жесткости
Примечание — Рисунки 1-4 не определяют конструкцию и приведены только для указания расчетных размеров.
5.2 Условия применения расчетных формул
5.2.1 Расчетные формулы применимы при отношении толщины стенки к диаметру:
для обечаек и труб при D ≥ 200 мм;
для труб при D
5.2.2 Формулы, приведенные в 5.3.2; 5.3.4-5.3.7 и 5.4.2, следует применять при условии, что расчетные температуры не превышают значений, при которых учитывается ползучесть материалов, т. е. при таких температурах, когда допускаемое напряжение определяют только по пределу текучести или временному сопротивлению (пределу прочности). Если нет точных данных, то формулы допускается применять при условии, что расчетная температура стенки обечайки из углеродистой стали не превышает 380 °С, из низколегированной 420 °С, а из аустенитной 525 °С.
5.2.3 Для обечаек, подкрепленных кольцами жесткости, дополнительно к требованиям 5.2.1 и 5.2.2 следует выполнять следующие ограничения:
— отношение высоты сечения кольца жесткости к диаметру
— расчетные формулы следует применять при условии равномерного расположения колец жесткости;
— в тех случаях, когда кольца жесткости установлены неравномерно, значения b и l 1 необходимо подставлять для того участка, на котором расстояние между двумя соседними кольцами жесткости максимальное;
— если l 2 > l 1 то в качестве расчетной длины принимают l 2 .
5.2.4 Расчетные формулы для обечаек, работающих под действием осевого сжимающего усилия, приведенные в 5.3.4, 5.4.3, применимы при следующем условии:
Для обечаек, у которых
при отсутствии более точных расчетов, допускается пользоваться формулами (15) и (17).
5.3 Гладкие цилиндрические обечайки
5.3.1 Обечайки, нагруженные внутренним избыточным давлением
5.3.1.1 Толщину стенки вычисляют по формуле
где расчетную толщину стенки вычисляют по формуле
5.3.1.2 Допускаемое внутреннее избыточное давление вычисляют по формуле
5.3.1.3 При изготовлении обечайки из листов разной толщины, соединенных продольными швами, расчет толщины обечайки проводят для каждого листа с учетом имеющихся в них ослаблений.
5.3.2 Обечайки, нагруженные наружным давлением
5.3.2.1 Толщина стенки
Толщину стенки предварительно вычисляют по формулам (4) и (5) с обязательной последующей проверкой по формуле (7)
где расчетную толщину стёнки вычисляют по формуле
Коэффициент В вычисляют по формуле (6)
5.3.2.2 Допускаемое наружное давление вычисляют по формуле
где допускаемое давление из условия прочности вычисляют по формуле
а допускаемое давление из условия устойчивости в пределах упругости вычисляют по формуле
При определении расчетной длины обечайки l или L длину примыкающего элемента l 3 следует вычислять по формулам
— для выпуклых днищ;
— для конических обечаек (днищ) без отбортовки, но не более длины конического элемента;
— для конических обечаек (днищ) с отбортовкой, но не более длины конического элемента.
5.3.3 Обечайки, нагруженные осевым растягивающим усилием
5.3.3.1 Толщину стенки вычисляют по формуле
где расчетную толщину стенки вычисляют по формуле
5.3.3.2 Допускаемое осевое растягивающее усилие вычисляют по формуле
5.3.4 Обечайки, нагруженные осевым сжимающим усилием
5.3.4.1 Допускаемое осевое сжимающее усилие вычисляют по формуле
где допускаемое осевое сжимающее усилие из условия прочности вычисляют по формуле
а допускаемое осевое сжимающее усилие в пределах упругости из условия устойчивости вычисляют по формуле
Примечание — В случае если
формула (16) принимает вид [ F ] E = [ F ] E 1 .
В формуле (16) допускаемое осевое сжимающее усилие вычисляют из условия местной устойчивости в пределах упругости по формуле
а допускаемое осевое сжимающее усилие вычисляют из условия общей устойчивости в пределах упругости по формуле
Гибкость λ вычисляют по формуле
Приведенную расчетную длину l пр принимают по таблице 1. Для схем, не приведенных в таблице 1, l пр определяют с помощью специальных методов расчета.
Таблица 1 — Приведенная расчетная длина l пр
Источник
Источник