Сферический сосуд на получение
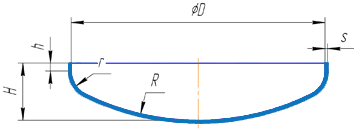
Рассмотрим технологию изготовления сферического сосуда давления, предназначенного для хранения газообразного азота и газообразного кислорода в системе жизнеобеспечения орбитальной станции. Газ хранится в 12 сферических баллонах вместимостью 27 л каждый под давлением 30 МПа.
На рис. 6.41 представлена конструктивная схема сосуда давления. В качестве герметизирующей оболочки использованы жесткие полимерные полиэтилентефталатные пленки (лавсановые) и ПМФ-352 (полиимидные). Силовую оболочку изготавливают из углепластика методом намотки (УКН-5000 + + ЭДТ-10П).
Намотка герметизирующего лейнера и силовой оболочки осуществляется на песчано-поли-мерную оправку, изготовленную в специальной форме согласно технологии, описанной в гл. 2.
Маршрут изготовления сосуда давления состоит из следующих операций.
Рис. 6.41. Типовая конструкция сферического сосуда давления:
1 — герметизирующая оболочка;
2 — штуцер; 3 — гайка; 4 — шайба;
5 — углепластиковая оболочка
1. Сборка и установка на намоточном станке СН-6 технологической оправки с металлическими штуцерами.
2. Обезжиривание поверхности штуцеров, контактирующих с наматываемым пленочным лей-
нером. Поверхность штуцеров предварительно пескоструят.
3. Установка кассеты с пленочным материалом на раскладчике намоточного станка, регулировка и настройка механизма технологического натяжения.
4. Программная многослойная намотка пленочного материала до получения расчетной толщины лейнера.
5. Нанесение верхнего разделительного слоя фторопластовой пленки и обмотка с увеличенным натяжением термоуса-живающейся лентой.
6. Термическая обработка многослойного лейнера при температуре спекания (в данном случае при 573 К) и охлаждение его вместе с печью.
7. Извлечение из нагревательной печи, снятие слоев термо-усаживающейся ленты и разделительного слоя.
8. Снятие кассеты с пленкой и установка кассеты с угле-пластиковым препрегом.
9. Закрепление конца намоточной ленты на наружной поверхности лейнера, установка расчетного технологического натяжения и зональная намотка силовой оболочки.
488
31-2-243
489
6.6. Изготовление трубопроводов
10. Намотка антиадгезионного разделительного слоя фторопластовой пленки.
11. Намотка технологического слоя термоусаживающейся ленты на разделительный слой и закрепление конца ленты на оправке.
12. Установка оправки с намотанной оболочкой в термопечь и термообработка в соответствии с технологическими режимами.
13. Извлечение оправки с изделием из термопечи, размотка слоев термоусаживающейся ленты, снятие разделительного слоя.
14. Осмотр и контроль поверхности силовой оболочки и штуцеров, удаление отвердевших натеков связующего.
15. Удаление технологической оправки вымыванием водой, нагретой до температуры 70…80 °С.
16. Сушка внутренней поверхности сосуда давления, установка технологических заглушек и опрессовка изделия давлением 0,3…0,5 рабочего давления.
Представленная здесь технология изготовления является типовой для сосудов давления и может незначительно меняться в зависимости от применяемых материалов и типа оправки.
6.6. Изготовление трубопроводов
В настоящее время во всем мире производится более 200 тыс. т труб из ПКМ, в основном из стеклопластика. Трубопроводы из композитов широко применяют в коммунальном хозяйстве, в нефтедобывающей и газовой промышленности, в химических производствах. Особое место занимают трубопроводы в ракетной и аэродинамической технике, где к ним предъявляют высокие требования по удельной прочности, герметичности, хемостойкости и где они должны надежно функционировать в широком диапазоне температур и давлений. Эти требования накладывают отпечаток как на конструкцию, так и на технологию изготовления трубопроводов.
Рассмотрим конструкторско-технологические решения топливопроводов применительно к криогенным топливным системам, работающим на жидком кислороде, водороде или сжиженном природном газе.
В силу функционального признака в криогенном топливном комплексе выделяют четыре основных типа трубопроводов, расположенных как вне бака, так и внутри его: 1 -заправочно-сливные; 2 — подачи топлива к двигателям; 3 -циркуляции и наддува; 4 – дренажные.
6. ПРОЦЕССЫ ИЗГОТОВЛЕНИЯ КОНСТРУКЦИЙ ИЗ КОМПОЗИТОВ
Конструкции внебаковых трубопроводов более сложные, чем внутрибаковых, так как они помимо герметизирующего лейнера, силовой оболочки и законцовок включают в себя теплоизоляцию и наружную защитную оболочку. Теплоизоляция криогенных трубопроводов предназначена для уменьшения теплопритока к компоненту, сохранение его температуры и кондиционного состояния при нахождении летательного аппарата в заправленном состоянии и для обеспечения минимальных потерь компонента на испарение.
Наружная защитная оболочка защищает теплоизоляцию от криоподсоса воздуха и предохраняет ее от разрушения.
На рис. 6.42 показана конструкция отвода внебакового криогенного топливопровода самолета. Отвод — наиболее сложная в технологическом отношении конструкция.
Рис. 6.42.Отвод внебакового криогенного топливопровода самолета: 1 — законцовка; 2— герметизирующий лейнер (12Х18Н10Т); 3 – силовая углепластиковая оболочка; 4— теплоизолирующая оболочка; 5— наружная защитная оболочка
490
491
6.6. Изготовление трубопроводов
Источник
Список убитых принеожиданном разрыве орудийного ствола, начатый шотландским королем ЯковомII, был бы длинен и впечатляющ. Тем не менее, когда в начале XIX в. в Лондонестало вводиться газовое освещение, трубы заказали бирмингемским оружейныммастерам, так что первые газовые трубы на самом деле были цепочками соединенныхмежду собой мушкетных стволов.
Можно найти множество книг, где говорится об истории развития паровогодвигателя, но почти ничего нельзя прочесть об истории совершенствованиятруб и котлов, которые в значительной мере определяли это развитие. Первыедвигатели были тяжелыми и громоздкими и потребляли огромные количестватоплива главным образом потому, что они работали при очень низких давленияхпара. Однако для несовершенных котлов того времени эти давления следуетпризнать значительными.
Производство более легких, компактных и экономичных двигателей целикомзависело от возможности перехода на более высокие рабочие давления. Пароходы20-х годов прошлого века при давлении пара 0,5-1,0 атм, обеспечиваемогоквадратным котлом типа «стога сена», потребляли около 7 кг угля на лошадинуюсилу в час (кг/л.с.-ч).
В 50-е годы прошлого века инженеры все еще имели дело с давлениями около1,5 атм и расход угля был примерно 4 кг/л.с.-ч. К 1900 г. давление параперевалило за 15 атм, а расход угля упал до 0,6-0,7 кг/л.с.-ч — десятикратноеуменьшение за 80 лет. Это были уже не те первые пароходы, которые вытеснялис морских путей парусные суда, а пароходы с двигателями тройного расширения,»шотландскими» котлами и низкой стоимостью топлива, способные покрыватьбольшие расстояния.
История котлов высокого давления тоже изобилует несчастными случаями. Втечение всего XIX в. взрывы котлов были сравнительно частыми, и, конечно,нередко ужасными были их последствия. В развернувшемся процессе повышениярабочих давлений лидерство принадлежало американским речным пароходам. Всередине прошлого века на Миссисипи речные пароходы регулярно пускались втысячекилометровые драматичные рейсы. Проектировщики почти все приносили вжертву скорости и легкости судна, довольно легкомысленно и оптимистическиоценивая возможности паровых котлов. Только за 1859 и 1860 гг. 27 из этихпароходов затонули в результате взрыва котлов.
Хотя причиной некоторых из этих несчастных случаев была преступная практикаэксплуатации (например, перекрытие предохранительных клапанов), в большинствесвоем они были вызваны отсутствием надлежащих расчетов при проектировании. Этодостойно сожаления, поскольку рассчитать напряжения, возникающие в сосудевысокого давления, очень просто. Настолько просто, что, насколько мне удалосьустановить, никто не претендовал когда-либо на честь первооткрывателя этихрасчетов,здесь достаточно самой элементарной алгебры.
Сферические сосуды высокого давления
Рассмотрение сосудов высокого давления любого рода (различные баллоны,пузыри, трубки, желудочки, котлы, артерии) связано с анализом растягивающихнапряжений, которые одновременно действуют более чем в одном направлении.На первый взгляд это может показаться сложным, но на самом деле здесь нетповодов для беспокойства. Стенки любого сосуда высокого давления несутдве функции. Они должны удерживать жидкость и быть водо- или газонепроницаемымии в то же время выдерживать напряжения, возникающие за счет внутреннегодавления. Растягивающие напряжения в этих стенках почти всегда действуютв плоскости этих стенок в обоих направлениях, то есть как бы параллельноих поверхности. Напряжение в третьем направлении, перпендикулярном к поверхности,обычно пренебрежимо мало, и им можно пренебречь. Рассмотрим в первую очередьсосуд высокого давления сферической формы. Предположим, что стенки, илиоболочка, сосуда, изображенного на рис. 26, являются достаточно тонкимии их толщина составляет, скажем, менее 1/10 от его диаметра. Радиус оболочки,взятый до половины толщины стенок, обозначим через r, толщинастенок оболочки — t и давление жидкости или газа на оболочкуизнутри — p (эти величины могут быть взяты в любых единицахизмерения). Мысленно разрежем камеру, подобно грейпфруту, пополам; из рассмотрениярис. 26, 27 и 28 достаточно ясно следует, что напряжение оболочки во всехнаправлениях, параллельных ее поверхности, будет выражаться формулойs = rp/2t
Это стандартная инженерная формула.
Рис. 26. Сосуд высокого давления сферической формы. Внутреннее давлениеp, средний радиус сосуда r и толщина стенки t.
Рис. 27. Схематический разрез сосуда высокогодавления. Представим себе, что сосуд разрезан пополам. Равнодействующаясил давления, действующего внутри каждой из половинок оболочки, должнауравновешиваться напряжениями, действующими на поверхности разреза. Площадьэтой поверхности равна 2πrt.
Рис. 28. Равнодействующая сил давления, действующего на поверхностьполусферы, равна силе давления, действующей на плоский диск того же диаметра,которая имеет величину πrp. Следовательно, напряжение s =(нагрузка / площадь) = (πrp) / (2πrt) = rp/2t
Источник
Торосферические днища – элемент, применяемый в сосудах под давлением, конструкцию которого определяют две геометрические фигуры – сфера и тор. Сферическая часть формируется штамповкой на гидравлическом прессе и обеспечивается определенным радиусом штампа. Торовая часть формируется методом холодного фланжирования (Фланжирование — метод обкатки, пластической деформации, при котором нужный профиль формируется без удаления металла.) на обкатном станке различными радиусами роликов.
Торосферические днища изготавливаются с учетом индивидуальных особенностей емкостей, условий эксплуатации, величины давления, выбранного материала и др.
Конструктивные особенности
Сосуды под давлением являются оборудованием повышенной опасности, их проектирование – серьезная и ответственная работа. Задачей конструктора является оптимальный выбор всех элементов аппарата. Важной задачей, требующей определенных знаний, является выбор правильной формы днища. Лучшая форма, распределяющая давление по всей поверхности, это полусфера (Гемисферические днища). Несмотря на то, что данная форма оптимально распределяет внутренние напряжения по всей своей поверхности, позволяя, в свою очередь, конструктору закладывать более тонкую стенку, данный вид не получил широкого распространения. В основном, в таких аппаратах используют торосферические и эллиптические днища.
Выпускаемые ОАО «Цвет» днища торосферического типа имеют диаметр от 320 мм до 5000 мм, изготовлены из углеродистой или нержавеющей стали толщиной от 3 до 30 мм. Все изделия в точности соответствуют нормам ГОСТ Р 34347-2017 и имеют как стандартные, так и выходящие за рамки установленных стандартами типоразмеров. Продукция изготавливается только из сертифицированных материалов и снабжается паспортами качества.
Преимущества торосферических днищ:
Каждый вид имеет свои плюсы и минусы. Преимущества эллиптической формы описаны на соответствующей странице нашего сайта. К плюсам же торосферы можно отнести следующее:
- Широкий диапазон размеров. Холодное фланжирование позволяет получать продукцию любого диаметра (в отличии от штамповки, где диаметр обусловлен размерами штампа)
- Удельный расход материала. Технология производства допускает изготовление элемента толщиной от 3мм. Наше предприятие тесно сотрудничает с машиностроительными предприятиями, изготавливающими автоцистерны для перевозки нефтепродуктов, где используются тонкостенные днища больших диаметров.
- Варьирование формы в соответствии с конструктивными особенностями аппаратов. ГОСТ 34347 определяет основные типы днищ:
Технические характеристики:
- R≈ D;
- r ≥ 0,095 D;
- h ≥ 3,5 s;
- hmin = 20 мм.
Технические характеристики:
- R≈ 0,9D;
- r ≥ 0,170 D;
- h ≥ 3,5 s;
- hmin = 20 мм.
Технические характеристики:
- R ≈ 0,8D;
- r ≥ 0,150 D;
- h ≥ 3,5 s;
- hmin = 20 мм.
Пример условного обозначения: Торосферические днища ГОСТ 52630 ДТ-1000-800-150-35-10; Внутренний диаметр (D) 1000мм; Радиус сферической части (R) 800мм; Радиус закатки (r) 150мм; Высота прямого участка (h) 35мм; Толщина листа (s) 10мм.
Сферы использования
Данный вид нашел широкое применение в пищевой промышленности: в конструкции сироповарочных котлов, танков для приготовления и хранения сахарного сиропа, в напорных, сортировочных и купажных емкостях. В химической и нефтехимической промышленности: в конструкции ресиверов, вакуумприемников и воздухосборников, адсорберов, дисольверов и конверторов. Помимо основных направлений использования — применение в сфере ЖКХ в качестве заглушек трубопроводов.
Вы можете заказать торосферические днища в нужном количестве, по стандартным размерам или индивидуально, с уточнением требуемых характеристик изделия. А мы обеспечим быстрое выполнение заказа и поставку продукции точно в назначенные сроки.
По желанию заказчика наше предприятие может предложить дополнительные услуги:
- Термообработка;
- Радиографический контроль сварного соединения;
- Подрезка торца, снятие фаски под сварку;
- Стеклоструйная или пескоструйная обработка;
- Полировка внутренней и внешней поверхности до Ra=0,4мкм
Днища в наличии
Тип днища | Размер днища | Марка стали | Количество | Цена, руб., с НДС |
---|---|---|---|---|
Днище торосферическое | 1100×6 | 12Х18Н10Т | 2 | 64 428 руб. |
География работы
На протяжении порядка сорока лет мы поставляем на российский рынок высококачественное и надежное емкостное технологическое оборудование, а также предлагаем своим клиентам весь спектр услуг, связанных с изготовлением днищ различного типа (в том числе и торосферические днища).
Продукция ОАО “Цвет”, успешно используется промышленными предприятиями во многих регионах РФ в частности: Москва и Московская область, Нижегородская область (Дзержинск), Урал (Екатеринбург, Челябинск, Магнитогорск), Юг России и другие города, а также в странах СНГ (Белоруссия, Казахстан). В начале 2016 г. мы заключили крупные контракты с предприятиями криогенной отрасли из городов Екатеринбург и Челябинск.
Доставка в регионы:
Москва и Московская область, Нижний Новгород, Екатеринбург, Челябинск, Магнитогорск, Белоруссия, Казахстан
Источник
Версия для печати
02 Сентября 2015 г.
Наши Заказчики часто задают вопрос, по какому принципу мы на Заводе выбираем ту или иную форму днищ в различных горизонтальных резервуарах и емкостях или, например, на основе каких государственных стандартов проектируются днища. В данной статье мне бы хотелось представить обзор тематики, касающейся типов днищ, зависимость конструкции днища от условий эксплуатации и т.п.
Наш Завод изготавливает различные резервуары и емкости горизонтальной конструкции и различного назначения: для хранения жидкостей и газообразных сред, дренажные емкости и сосуды, работающие под давлением и без, что зависит от свойств эксплуатируемой рабочей среды.
Так, ассортимент предлагаемых нами горизонтальных емкостей включает в себя:
- горизонтальные резервуары РГС, РГСН, РГСП, РГСД
- емкости ЕП (ЕПП)
- аппараты ГЭЭ, ГКК, ГПП
- сосуды для сжиженных газов
Все вышеперечисленные емкости представляют собой горизонтальный цилиндрический корпус с двумя днищами. В зависимости от характеристик рабочей среды (жидкость или газообразные составы, плотность, температурный режим) и условий эксплуатации (хранение под давлением или без) днища могут иметь различную конструкцию. Так, различают следующие виды днищ:
- плоские днища
- конические днища
- сферические днища
- торосферические днища
- эллиптические днища
Выбор той или иной формы днищ зависит от многих параметров. Ниже мы подготовили краткую, но полную информацию по характеристикам днищ, выпускаемых Заводом САРРЗ в партнерстве с производителем днищ ООО “СП Бомбе”.
Процесс изготовления днищ для горизонтальных емкостей
Для изготовления качественной продукции, например, днищ, партнеры располагают всем необходимым оборудованием: оборудованием для плазменной резки металла, аппаратом для автоматической сварки, множеством токарно-фрезерных станков для обработки краев, фланжировочным станком, гидравлическими прессами и др.
Процесс производства днищ резервуаров условно можно разделить на этапы. Это:
- проектирование днищ в соответствии с государственными стандартами
- резка, формирование днищ из заготовок, обработка кромок и отбортовка
- сварка днищ и обечаек горизонтальных емкостей
В отделе проектирования наши инженеры-проектировщики оперируют и полагаются на требования нормативных документов. Их огромное множество, но мы определили наиболее значимые:
- ГОСТ 17032-2010 “Резервуары стальные горизонтальные для нефтепродуктов. Технические условия”
- ГОСТ Р 52630-2012 “Сосуды и аппараты стальные сварные. Общие технические условия (с Изменением № 1)”
- ПБ 03-584-03 “Правила проектирования, изготовления и приемки сосудов и аппаратов стальных сварных”
- ГОСТ 12619-78 “Днища конические отбортованные с углами при вершине 60 и 90°. Основные размеры”
- ГОСТ 12621-78 “Днища конические неотбортованные с углом при вершине 140 градусов. Основные размеры”
- ГОСТ 12620-78 “Днища конические неотбортованные с углами при вершине 60, 90 и 120 градусов. Основные размеры”
- ГОСТ 12622-78 “Днища плоские отбортованные. Основные размеры”
- ГОСТ 12623-78 “Днища плоские неотбортованные. Основные размеры”
- ГОСТ 6533-78 “Днища эллиптические отбортованные стальные для сосудов, аппаратов и котлов. Основные размеры”
- ГОСТ 25221-82 “Сосуды и аппараты. Днища и крышки сферические неотбортованные. Нормы и методы расчета на прочность”
К описанию конструкций днищ я вернусь немного позже. Для начала мне бы хотелось рассказать Вам как изготавливаются сами днища.
После получения металлопроката и карт раскройки днищ от инженеров-проектировщиков начинается процесс производства днищ, который зависит от их (днищ) конструкций (конические, эллиптические, плоские, сферические) и марки стали.
Сначала наши специалисты осуществляют раскрой заготовки на станке плазменной или механической резки. Заготовки для эллиптических, сферических или плоских днищ отправляются на гидравлический пресс для штамповки или фланжировочную машину для холодной обкатки.
На гидравлическом прессе заготовке придается необходимая форма при ее нагреве под давлением. Далее уже сформированное днище проходит процесс отбортовки методом холодной накатки – пластической загибке бортов (кромок) днищ. Гибку кромок выполняют формовочные ролики, которые двигаются в горизонтальном и вертикальном направлении. Также для обработки бортов может использоваться метод вальцевания. Для получения ровных кромок их обрабатывают на шлифовочной машине или установке плазменной резки. На фланжировочном же станке происходит последовательно – придание формы днища и отбортовка кромок роликами. Для защиты днищ впоследствии во время эксплуатации, поверхность шлифуют, проводят электрохимическое травление, окрашивают, подвергают пескоструйной обработке или наносят специальное антикоррозионное покрытие. Выбор того или иного способа защиты зависит от требований Заказчика.
После получения готового элемента он проходит контроль качества в имеющейся на Заводе лаборатории визуально-измерительным методом, ультразвуковым или методом проникающего контроля.
Далее скажу несколько слов о различных конструкциях днищ.
Плоские днища
Плоские днища, в основном, применяются на резервуарах с малыми перепадами давления, рабочее давление в которых не превышает 0,07 МПа. Толщину металла, а также необходимость установки ребер жесткости наши специалисты рассчитывают исходя из давления внутри сосуда. Плоские днища бывают отбортованными или неотбортованными. Отбортованные днища имеют обработанные края и более удобны для получения качественного сварного шва со стенкой. Такие днища изготавливаются методом холодной накатки на фланжировочных машинах, на которых происходит отбортовка кромок. Предварительно заготовку могут подвергнуть термической обработке для повышения увеличения прочности.
Конические днища
Геометрия конических днищ характеризуется диаметрами широкой (место сварки с самим аппаратом) и узкой части, углом наклона от центра к краям (60°, 90°, 120°, 140°) и расстоянием от широкой до узкой частей. Конические отбортованные днища изготавливаются из нескольких элементов, которые сначала свариваются, а затем подаются на фланжировочную машину для отбортовки краев. Конические неотбортованные днища производятся на гидравлических прессах с последующей обработкой кромок и поверхности.
Эллиптические и торосферические днища
Наиболее распространенным видом днищ являются эллиптические, так как их применяют в сосудах, работающих под высоким давлением. Подобные днища изготавливаются двумя способами в зависимости от диаметра: днища диаметром до 2 м производят на гидравлических прессах, более крупные днища – на фланжировочных станках с последующей сваркой элементов. Края днищ проходят отбортовку кромок. Размеры эллиптических днищ типизированы. Но мы также предлагаем производство днищ по индивидуальным размерам. Единственное, что следует отметить: высота выпуклой части должна быть не менее 0,25 внутреннего диаметра днища.
Торосферические днища являются разновидностью эллиптических днищ. При этом они должны иметь высоту выпуклой части не менее 0,2 от внутреннего диаметра днища, радиус отбортовки не менее 0,095 внутреннего диаметра днища и внутренний радиус кривизны центральной части не более внутреннего диаметра днища.
Сферические днища
Сферические днища могут производиться как холодной, так и горячей штамповкой. Также если диаметр сферы слишком велик, такие днища состоят из нескольких свариваемых между собой отдельных”лепестков”. Для изготовления точного сферического днища важны такие параметры как внутренний диаметр и радиус сферы. При этом радиус сферы должен быть не менее 0,85 диаметра и не более диаметра.
Ниже для Вашего удобства привожу сводную справочную таблицу по соответствию типов емкостей и их днищ в зависимости от условий эксплуатации и соответствующие государственные стандарты.
Сводная таблица по конструктивным типам днищ горизонтальных емкостей
Типы горизонтальных емкостей | Тип днища | Рабочая среда | Рабочее давление | Температурный режим эксплуатации | Нормативная база |
---|---|---|---|---|---|
Горизонтальные резервуары РГС (РГСН, РГСП, РГСД) | плоские отбортованные | неагрессивные жидкие продукты, техническая вода плотностью до 1300 кг/м3 | до 0,04 МПа | от -65ºС до +90ºС |
|
плоские неотбортованные | |||||
конические отбортованные | до 0,07 МПа | ||||
конические неотбортованные | |||||
Дренажные емкости ЕП и ЕПП | конические | нефтепродукты, масла, кислоты, щелочи с плотностью до 1000 кг/м3 и вязкостью не более 30х10-6 м2/с | до 0,07 МПа | от -15ºС до +80ºС |
|
Аппараты ГЭЭ | эллиптические | жидкие и газообразные невзрывоопасные и нетоксичные среды плотностью до 1600 кг/м3 | до 1,6 МПа | от -60ºС до +50ºС |
|
Аппараты ГКК | конические | жидкие и газообразные невзрывоопасные и нетоксичные среды плотностью до 1600 кг/м3 | до 1,6 МПа | от -60ºС до +50ºС |
|
Аппараты ГПП | плоские | жидкие и газообразные невзрывоопасные и нетоксичные среды плотностью до 1600 кг/м3 | до 1,6 МПа | от -60ºС до +50ºС |
|
Цилиндрические аппараты тип 1 | эллиптические | неагрессивные газовые и жидкие рабочие среды с плотностью до 1000 кг/м3 | до 2,5 МПа | от -60ºС до +300ºС |
|
Отстойники | эллиптические | сточная вода, нефть, попутный газ | до 2,5 МПа | от -60ºС до +100ºС |
|
Если у Вас остались вопросы, звоните на Завод по телефону 8-800-555-9480 или пишите на электронную почту .
С уважением,
Директор Саратовского резервуарного завода Гамаюнов Михаил Михайлович
Источник