Сосуд под давлением реактор
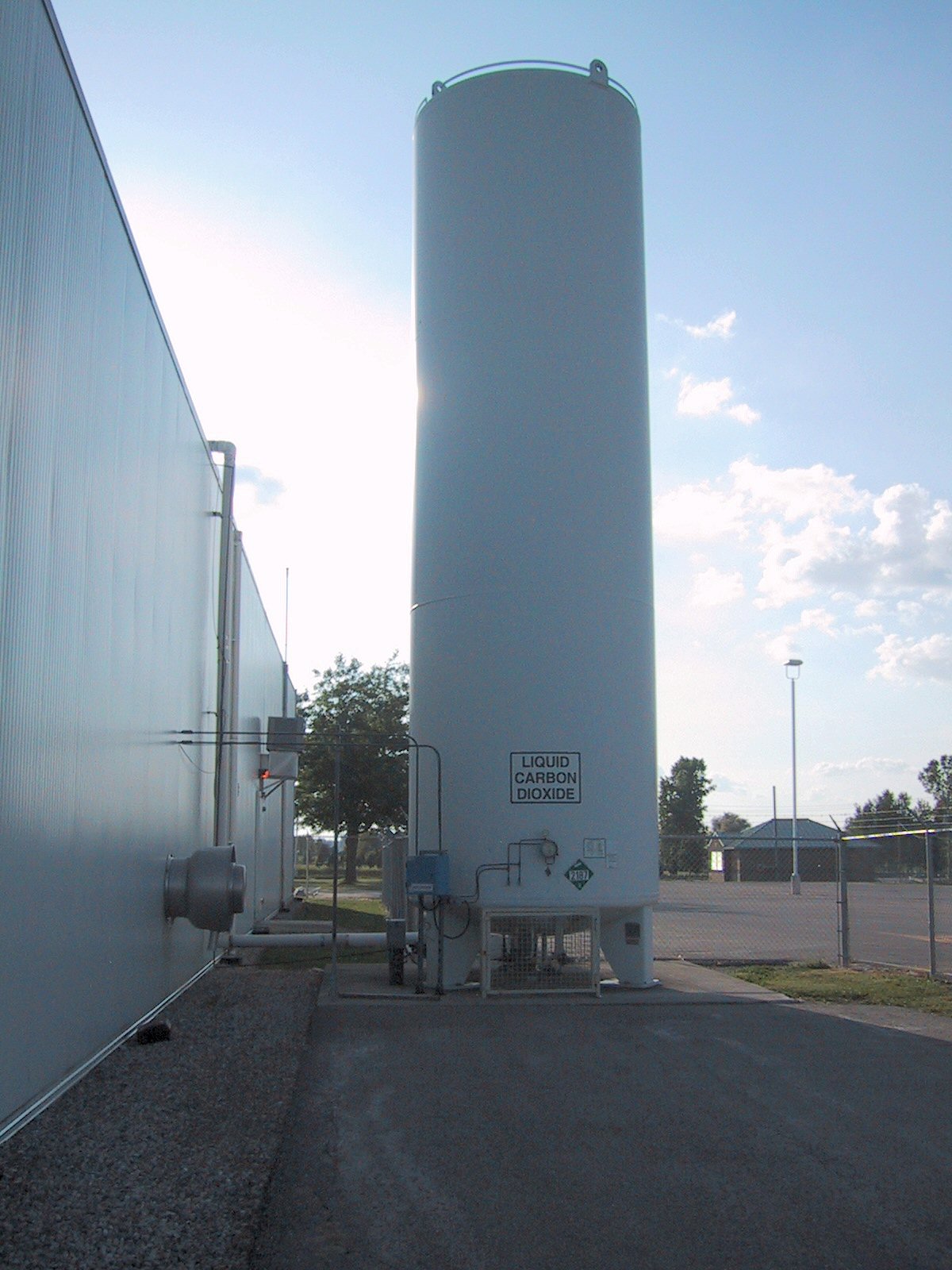
Текущая версия страницы пока не проверялась опытными участниками и может значительно отличаться от версии, проверенной 4 сентября 2018; проверки требует 1 правка.
У этого термина существуют и другие значения, см. Сосуд.
Сосуд под давлением – закрытая ёмкость (стационарно установленная или передвижная), предназначенная для ведения химических, тепловых и других технологических процессов, а также для хранения и транспортировки газообразных, жидких и других веществ[1]. Границей сосуда являются входные и выходные штуцеры.
Использование[править | править код]
Сосуды под давлением широко используются как в промышленности, так и в быту, спорте и пр. Разнообразие размеров, технических характеристик и способов применения их чрезвычайно велико, начиная от ядерных реакторов и заканчивая домашними отопительными котлами и баллонами для дайвинга. Другими примерами использования сосудов под давлением являются паровые котлы, барокамеры, автоклавы, ресиверы, цистерны, газовые баллоны и бочки, предназначенные для транспортировки или хранения сжатых, сжиженных газов, жидкостей и сыпучих тел.
Требования к сосудам под давлением в РФ[править | править код]
Крышка реактора PWR – сосуда с очень высокими параметрами среды
В едином перечне продукции, в отношении которой устанавливаются обязательные требования в рамках Таможенного союза, присутствуют пункты: «оборудование, работающее под избыточным давлением» и «сосуды, работающие под давлением».[2] Соответствующие требования установлены ТР ТС 032/2013 «О безопасности оборудования, работающего под избыточным давлением».[3]
Сосуды под давлением являются техническими устройствами, эксплуатация которых делают производственный объект опасным. С авариями сосудов под давлением связано большое количество несчастных случаев, поэтому на их проектирование, устройство, изготовление, реконструкцию, наладку, монтаж, ремонт, техническое диагностирование и эксплуатацию в большинстве стран мира накладывается ряд ограничений.
В России обязательны Федеральные нормы и правила в области промышленной безопасности «Правила промышленной безопасности опасных производственных объектов, на которых используется оборудование, работающее под избыточным давлением», а также ряд других отраслевых документов, действие которых ограничено своей специфической областью (например «Правила устройства и безопасной эксплуатации оборудования и трубопроводов атомных энергетических установок», «Правила устройства и безопасной эксплуатации сосудов, работающих под давлением, для объектов использования атомной энергии» и др.). Эти и другие[4] государственные документы устанавливают границы параметров содержащихся в сосуде веществ, превышение которых причисляет сосуд к опасным, в общем случае, как:
- вода с температурой выше 115 °С или другие нетоксичные, невзрывопожароопасные жидкости при температуре, превышающей температуру кипения при давлении 0,07 МПа;
- пар, газ или токсичные взрывопожароопасные жидкости с давлением свыше 0,07 МПа;
- сжатых, сжиженных и растворенных газов под давлением свыше 0,07 МПа.
Требования к оснащению[править | править код]
Для управления работой и обеспечения безопасных условий эксплуатации сосуды в зависимости от назначения должны быть оснащены:
- запорной или запорно-регулирующей арматурой;
- приборами для измерения давления;
- приборами для измерения температуры;
- предохранительными устройствами;
- указателями уровня жидкости.
Контроль сварных соединений[править | править код]
Организация-изготовитель (доизготовитель), монтажная или ремонтная организация обязаны применять такие виды и объёмы контроля своей продукции, которые гарантировали бы выявление недопустимых дефектов, её высокое качество и надежность в эксплуатации. Контроль качества сварки и сварных соединений должен включать:
- проверку аттестации персонала;
- проверку сборочно-сварочного, термического и контрольного оборудования, аппаратуры, приборов и инструментов;
- контроль качества основных материалов;
- контроль качества сварочных материалов и материалов для дефектоскопии;
- операционный контроль технологии сварки;
- неразрушающий контроль качества сварных соединений;
- разрушающий контроль качества сварных соединений;
- контроль исправления дефектов.
Государственный надзор[править | править код]
Сосуды, на которые распространяются российские государственные правила, до пуска их в работу должны быть зарегистрированы в органах Ростехнадзора России[5], кроме специально оговоренных случаев, на основании письменного заявления владельца сосуда; при перестановке сосуда на новое место или передаче сосуда другому владельцу, а также при внесении изменений в схему его включения сосуд до пуска в работу должен быть перерегистрирован в органах Ростехнадзора России.
Кроме того сосуды, на которые распространяется действие государственных правил, должны подвергаться техническому освидетельствованию после монтажа, до пуска в работу, периодически в процессе эксплуатации и в необходимых случаях – внеочередному освидетельствованию с участием специалиста организации, имеющей лицензию Ростехнадзора России (если сосуд зарегистрирован). Объём, методы и периодичность технических освидетельствований сосудов (за исключением баллонов) должны быть определены изготовителем и указаны в руководстве по эксплуатации. В случае отсутствия таких указаний техническое освидетельствование должно проводиться в соответствии с требованиями государственных правил.
См. также[править | править код]
- Паровой котёл
- Ресивер (сосуд)
- Барокамера
Примечания[править | править код]
Эта статья или раздел описывает ситуацию применительно лишь к одному региону, возможно, нарушая при этом правило о взвешенности изложения. Вы можете помочь Википедии, добавив информацию для других стран и регионов. |
Источник
A реактор давления , иногда называют трубкой высокого давлени, или герметизированной трубкой, представляет собой химический реактор который может проводить реакцию под давлением. Реактор высокого давления – это особая сфера применения сосуда высокого давления . Давление может быть вызвано самой реакцией или внешним источником, например водородом при каталитическом переносе гидрирование .
Преимущества
Реактор высокого давления может иметь несколько преимуществ перед обычная колба с круглым дном . Во-первых, он может проводить реакцию выше точки кипения растворителя . Во-вторых, давление может уменьшить реакционный объем, включая жидкую фазу, и, в свою очередь, увеличить концентрацию и частоту столкновений , и ускорить реакцию.
Повышение температуры может ускорить желаемую реакцию, но также ускорить разложение реагентов и исходных материалов . Однако давление может ускорить желаемую реакцию и влияет на разложение только тогда, когда оно включает в себя выделение газа или реакцию с газом в сосуде. Когда желаемая реакция ускоряется, конкурирующие реакции сводятся к минимуму. Давление обычно способствует более быстрой реакции с более чистыми профилями реакции.
Вышеупомянутые преимущества реактора под давлением были показаны в микроволновой химии . Например, если Suzuki Coupling требуется 8 часов при 80 ° C, то в микроволновом синтезаторе требуется всего 8 минут при 140 ° C. Микроволновый эффект – дискуссионная тема. Более поздние эксперименты показывают, что некоторые из этих ранних отчетов являются артефактами, а увеличение скорости происходит строго из-за тепловых эффектов.
Если реактор высокого давления спроектирован правильно, он может соответствовать 4 из 12 зеленой химии принципы
- 1, меньшее количество растворителя и более чистый профиль реакции приводят к меньшему количеству отходов
- 5, требуется меньше растворителя
- 6, короткое время реакции может сэкономить до 92 процентов электроэнергии и 200 галлонов охлаждающая вода для реакции кипячения с обратным холодильником
- 12, закрытый сосуд может предотвратить выброс токсичного газа и взрывы.
Типы реакторов под давлением
Стандартный стеклянный реактор под давлением
Стандартный стеклянный реактор под давлением
Стеклянные реакторы под давлением обычно используются, когда оператору необходимо наблюдать за протеканием реакции. Хотя номинальное давление в этих системах ниже, чем у большинства металлических реакторов под давлением, они по-прежнему являются эффективной установкой для достижения ответственных пределов давления. Оценки на стеклянных сосудах напрямую связаны с диаметром сосуда. Чем больше диаметр, тем ниже допустимое давление. Встроенные донные клапаны также могут влиять на номинальное давление. Нижний клапан на стеклянном сосуде обычно связан с более низким допустимым рабочим давлением. Все это переменные, определяемые процессом и параметрами каждой отдельной реакции. Стеклянные сосуды под давлением также могут использоваться в инертных приложениях. Эти сосуды используются в реакциях, включая гидрирование, полимеризацию, синтез, каталитическую, нефтехимическую, кристаллизацию и т. Д., Но не ограничиваются ими.
Одним из недостатков стандартного стеклянного реактора под давлением является возможность взрыва из-за трудно прогнозируемого чрезмерного внутреннего давления и отсутствия механизма сброса. Однако при надлежащем обеспечении безопасности, обеспечиваемом производителем, оператор может безопасно выполнять большинство реакций.
Трубка Фишера-Портера
A Трубка Фишера-Портера или сосуд Фишера-Портера представляет собой стеклянный реактор под давлением, используемый в химической лаборатории. Производится компанией Andrews Glass Co. из Вайнленда, штат Нью-Джерси.
Реактор высокого давления
Металлический реактор под давлением
Металлические реакторы под давлением обычно используются для реакций высокого давления. У них гораздо более высокое номинальное давление, чем у стеклянных реакторов. Хотя у них более высокое номинальное давление, у них все же есть свои явные недостатки. Один из них – металлические сосуды более подвержены коррозии. Материал конструкции (МОС) особенно важен на этапе проектирования металлического реактора под давлением. Правильный MOC может уменьшить или даже устранить коррозию, наблюдаемую в резервуаре, но, в зависимости от выбранного материала, может увеличить стоимость системы. Металлические сосуды также намного тяжелее, и с ними следует обращаться осторожно при проведении технического обслуживания.
Металлические реакторы высокого давления используются в реакциях, включая, но не ограничиваясь, гидрирование, полимеризацию, синтез, каталитический, нефтехимический и так далее. Они также используются для выполнения таких исследований, как разведка, биомасса, биополимер, цеолит и т. Д.
Недостатками металлического реактора высокого давления (бомбы) являются установка, обслуживание и коррозионная активность.
СВЧ-синтезатор
Недостатками СВЧ-синтезатора является ограничение растворителя
См. Также
Приготовление под давлением
Емкость под давлением
Ссылки
Источник
Сосуд высокого давления реактора (ДПЛА) в атомной электростанции является сосуд под давлением , содержащий реакторный хладагент ядерного , основной кожух , и активную зону реактора .
Классификация ядерных энергетических реакторов
В российских реакторах РБМК советских времен каждая тепловыделяющая сборка заключена в отдельную трубу диаметром 8 см, а не в сосуд высокого давления. Хотя у большинства энергетических реакторов есть сосуд высокого давления, они обычно классифицируются по типу теплоносителя, а не по конфигурации сосуда, используемого для хранения теплоносителя. Классификации следующие:
- Легководный реактор – включает реактор с водой под давлением и реактор с кипящей водой . Большинство ядерных энергетических реакторов относятся к этому типу.
- Реактор с графитовым замедлителем – включает Чернобыльский реактор ( РБМК ), который имеет весьма необычную конфигурацию реактора по сравнению с подавляющим большинством атомных электростанций в России и во всем мире.
- Термический реактор с газовым охлаждением – включает усовершенствованный реактор с газовым охлаждением, реактор на быстрых нейтронах с газовым охлаждением и высокотемпературный реактор с газовым охлаждением . Примером реактора с газовым охлаждением является British Magnox .
- Реактор с тяжелой водой под давлением – использует тяжелую воду или воду с более высокой, чем обычно, пропорцией изотопа водорода дейтерия. Однако D 2 O (тяжелая вода) дороже и может использоваться в качестве основного компонента, но не обязательно в качестве охлаждающей жидкости в этом случае. Примером тяжеловодного реактора является канадский реактор CANDU .
- Жидкий металл охлаждают реактор – использует жидкий металл, например, натрий или свинец – висмут сплава для охлаждения активной зоны реактора.
- Реактор с расплавом солей – в качестве хладагента используются соли, обычно фториды щелочных и щелочноземельных металлов. Работа аналогична реакторам с металлическим охлаждением, с высокими температурами и низким давлением, что снижает давление, оказываемое на корпус реактора, по сравнению с конструкциями с водяным или паровым охлаждением.
Из основных классов реакторов с корпусом высокого давления реактор с водой под давлением уникален тем, что корпус высокого давления подвергается значительному нейтронному облучению (называемому флюенсом ) во время работы и в результате со временем может стать хрупким. В частности, более крупный сосуд высокого давления реактора с кипящей водой лучше защищен от нейтронного потока, поэтому, хотя он и дороже в производстве в первую очередь из-за этого дополнительного размера, он имеет преимущество в том, что не требует отжига для продления срока его службы.
Отжиг корпусов реакторов с водой под давлением для продления срока их службы – сложная и дорогостоящая технология, активно развиваемая как поставщиками ядерных услуг ( AREVA ), так и операторами реакторов с водой под давлением.
Компоненты корпуса высокого давления реактора с водой под давлением
Все сосуды высокого давления реакторов с водой под давлением имеют некоторые общие черты, независимо от конкретной конструкции.
Корпус корпуса реактора
Корпус реактора является самым большим компонентом и предназначен для размещения тепловыделяющей сборки, теплоносителя и фитингов для поддержки потока теплоносителя и опорных конструкций. Обычно он имеет цилиндрическую форму и открыт сверху для загрузки топлива.
Головка корпуса реактора
Эта конструкция прикреплена к верхней части корпуса реактора. Он содержит отверстия, позволяющие приводному механизму управляющих стержней прикрепляться к управляющим стержням в топливной сборке. Зонд для измерения уровня теплоносителя также входит в емкость через верхнюю часть корпуса реактора.
Топливная сборка
Топливная сборка ядерного топлива, обычно состоящая из урана или уран-плутониевых смесей. Обычно это прямоугольный блок твэлов с сеткой.
Отражатель или поглотитель нейтронов
Защищает внутреннюю часть корпуса от быстрых нейтронов, выходящих из тепловыделяющей сборки, представляет собой цилиндрический экран, обернутый вокруг тепловыделяющей сборки. Отражатели отправляют нейтроны обратно в тепловыделяющую сборку, чтобы лучше использовать топливо. Однако основная цель – защитить сосуд от повреждений, вызванных быстрыми нейтронами, которые могут сделать сосуд хрупким и сократить срок его службы.
Материалы
Корпус реактора играет важную роль в безопасности реактора PWR, и используемые материалы должны быть способны удерживать активную зону реактора при повышенных температурах и давлениях. Материалы, используемые в цилиндрической оболочке резервуаров, со временем эволюционировали, но в целом они состоят из низколегированных ферритных сталей, плакированных 3-10 мм аустенитной нержавеющей сталью . Облицовка из нержавеющей стали в основном используется в местах, контактирующих с охлаждающей жидкостью, чтобы минимизировать коррозию. До середины 1960 г. в корпусе судна использовалась пластинчатая молибден-магниевая сталь марки B SA-302. Поскольку для изменения конструкции требовались сосуды высокого давления большего размера, для увеличения предела текучести потребовалось добавление никеля в этот сплав в количестве примерно 0,4-0,7 мас.%. Другие распространенные стальные сплавы включают SA-533 класса B класса 1 и SA-508 класса 2. Оба материала содержат основные легирующие элементы никель, марганец, молибден и кремний, но последний также включает 0,25-0,45 мас.% Хрома. Все сплавы, перечисленные в ссылке, также содержат> 0,04 мас.% Серы. Низколегированные ферритные стали NiMoMn привлекательны для этой цели из-за их высокой теплопроводности и низкого теплового расширения, свойств, которые делают их устойчивыми к тепловым ударам. Однако при рассмотрении свойств этих сталей необходимо учитывать реакцию, которую они должны будут иметь на радиационное повреждение. Из-за суровых условий материал оболочки цилиндра корпуса реактора часто является компонентом, ограничивающим срок службы ядерного реактора. Понимание воздействия излучения на микроструктуру в дополнение к физическим и механическим свойствам позволит ученым создавать сплавы, более устойчивые к радиационным повреждениям.
В 2018 году Росатом объявил о разработке технологии термического отжига для корпусов реакторов, которая снижает радиационные повреждения и продлевает срок службы от 15 до 30 лет. Это было продемонстрировано на энергоблоке №1 Балаковской АЭС .
Радиационные повреждения металлов и сплавов
Из-за характера производства ядерной энергии материалы, используемые в корпусе реактора, постоянно подвергаются бомбардировке частицами высокой энергии. Эти частицы могут быть нейтронами или фрагментами атома, образованными в результате деления. Когда одна из этих частиц сталкивается с атомом в материале, она передает часть своей кинетической энергии и выбивает атом из его положения в решетке. Когда это происходит, этот первичный «ударный» атом (PKA), который был смещен, и энергичная частица может отскочить и столкнуться с другими атомами в решетке. Это создает цепную реакцию, которая может привести к смещению многих атомов из их исходных положений. Это атомное движение приводит к созданию многих типов дефектов. Накопление различных дефектов может вызвать изменения микроструктуры, которые могут привести к ухудшению макроскопических свойств. Как упоминалось ранее, цепная реакция, вызванная PKA, часто оставляет на краю след вакансий и скоплений дефектов. Это называется каскадом смещения . Богатое вакансиями ядро каскада смещений также может коллапсировать в дислокационные петли. Из-за облучения в материалах обычно образуется более высокая концентрация дефектов, чем в обычных сталях, а высокие рабочие температуры вызывают миграцию дефектов. Это может вызвать такие вещи, как рекомбинация междоузлий и вакансий и скопление подобных дефектов, которые могут либо создавать, либо растворять преципитаты или пустоты. Примерами стоков или термодинамически благоприятных мест для миграции дефектов являются границы зерен, пустоты, некогерентные выделения и дислокации.
Радиационно-индуцированная сегрегация
Взаимодействие между дефектами и легирующими элементами может вызвать перераспределение атомов на стоках, таких как границы зерен. Физический эффект, который может произойти, заключается в том, что определенные элементы будут обогащены или истощены в этих областях, что часто приводит к охрупчиванию границ зерен или другим пагубным изменениям свойств. Это связано с тем, что существует поток вакансий в сторону стока и поток атомов в сторону или в сторону стока, которые могут иметь различные коэффициенты диффузии. Неравномерная скорость диффузии вызывает концентрацию атомов, которая не обязательно будет иметь правильные пропорции сплава. Сообщалось, что никель, медь и кремний имеют тенденцию к обогащению в поглотителях, тогда как хром имеет тенденцию к обеднению. Результирующий физический эффект заключается в изменении химического состава на границах зерен или вокруг пустот / некогерентных выделений, которые также служат стоками.
Образование пустот и пузырей
Пустоты образуются из-за скопления вакансий и обычно легче образуются при более высоких температурах. Пузыри – это просто пустоты, заполненные газом; они будут происходить, если присутствуют реакции трансмутации, то есть газ образуется из-за разрушения атома, вызванного бомбардировкой нейтронами. Самая большая проблема с пустотами и пузырями – нестабильность размеров. Примером того, где это было бы очень проблематично, являются участки с жесткими допусками по размерам, такие как резьба на застежке.
Радиационное упрочнение
Создание дефектов, таких как пустоты или пузыри, выделения, петли или линии дислокаций, а также скопления дефектов может упрочнить материал, поскольку они блокируют движение дислокаций. Движение дислокаций – вот что приводит к пластической деформации. Хотя это приводит к затвердеванию материала, обратная сторона заключается в потере пластичности. Потеря пластичности или увеличение хрупкости опасны для корпусов реакторов корпуса, поскольку они могут без предупреждения привести к катастрофическому отказу. При разрушении пластичных материалов перед разрушением происходит существенная деформация, которую можно контролировать. Хрупкие материалы будут трескаться и взрываться под давлением без особой предварительной деформации, поэтому инженеры мало что могут сделать, чтобы определить, когда материал вот-вот развалится. Медь является особенно опасным элементом сталей, который может привести к закалке или охрупчиванию. Осадки, богатые медью, очень маленькие (1-3 нм), поэтому они эффективны для закрепления дислокаций. Было установлено, что медь является основным вредным элементом в сталях, используемых для корпусов реакторов, особенно если уровень примесей превышает 0,1 мас.%. Таким образом, разработка «чистых» сталей или сталей с очень низким уровнем примесей важна для снижения радиационного упрочнения.
Слизняк
Ползучесть возникает, когда материал находится под давлением ниже предела текучести, что со временем вызывает пластическую деформацию. Это особенно распространено, когда материал подвергается высоким напряжениям при повышенных температурах, потому что диффузия и движение дислокаций происходят быстрее. Облучение может вызвать ползучесть из-за взаимодействия между напряжением и развитием микроструктуры. В этом случае увеличение коэффициента диффузии из-за высоких температур не является очень сильным фактором, вызывающим ползучесть. Размеры материала могут увеличиваться в направлении приложенного напряжения из-за создания дислокационных петель вокруг дефектов, образовавшихся в результате радиационного повреждения. Кроме того, приложенное напряжение может позволить интерстициальным элементам более легко поглощаться дислокацией, что способствует подъему дислокации. Когда вывихи могут подниматься, остаются лишние вакансии, что также может привести к вздутию.
Коррозионное растрескивание под напряжением под воздействием облучения
Из-за охрупчивания границ зерен или других дефектов, которые могут служить инициаторами трещин, добавление радиационного воздействия на трещины может вызвать межкристаллитное коррозионное растрескивание под напряжением. Основным фактором стресса окружающей среды, который образуется из-за излучения, является водородное охрупчивание вершин трещин. Ионы водорода образуются, когда радиация расщепляет молекулы воды, которые присутствуют, потому что вода является хладагентом в PWR, на OH – и H + . Есть несколько подозреваемых механизмов, объясняющие водородное охрупчивание, три из которых являются механизм отслаивания, в теории давления, и метод атаки водорода . В механизме декогезии считается, что накопление ионов водорода снижает прочность связи металл-металл, что облегчает расщепление атомов. Теория давления – это идея, что водород может выделяться в виде газа на внутренних дефектах и создавать пузырьки внутри материала. Напряжение, вызванное расширяющимся пузырем в дополнение к приложенному напряжению, снижает общее напряжение, необходимое для разрушения материала. Метод водородной атаки аналогичен теории давления, но в этом случае предполагается, что водород реагирует с углеродом в стали с образованием метана, который затем образует пузыри и пузыри на поверхности. В этом случае добавленное напряжение пузырьков усиливается обезуглероживанием стали, что ослабляет металл. Помимо водородного охрупчивания, ползучесть, вызванная излучением, может вызвать скольжение границ зерен друг относительно друга. Это еще больше дестабилизирует границы зерен, облегчая распространение трещины по ее длине.
Разработка радиационно стойких материалов для корпусов реакторов.
В очень агрессивных средах требуются новые подходы к материалам для борьбы со снижением механических свойств с течением времени. Один из методов, который пытались использовать исследователи, – это введение функций для стабилизации смещенных атомов. Это может быть сделано путем добавления границ зерен, растворенных веществ большого размера или небольших оксидных диспергаторов, чтобы минимизировать перемещение дефектов. Таким образом, будет меньше радиационно-индуцированной сегрегации элементов, что, в свою очередь, приведет к более пластичным границам зерен и меньшему межкристаллитному коррозионному растрескиванию под напряжением. Блокирование дислокации и движения дефекта также поможет повысить сопротивление ползучести при помощи излучения. Сообщалось о попытках введения оксидов иттрия для блокирования движения дислокаций, но было обнаружено, что технологическая реализация представляет большую проблему, чем ожидалось. Необходимы дальнейшие исследования для повышения стойкости к радиационным повреждениям конструкционных материалов, используемых на атомных электростанциях.
Производители
Из-за экстремальных требований, необходимых для создания крупных современных корпусов реакторов под давлением, и ограниченного рынка, по состоянию на январь 2020 года в мире насчитывается всего несколько производителей, в том числе:
- China’s First Heavy Industries , Erzhong Group, Harbin Electric и Shanghai Electric .
- Французский Framatome (бывший Areva )
- L&T Special Steels and Heavy Forgings Limited , дочерняя компания индийского конгломерата Larsen & Toubro, в партнерстве с Bhabha Atomic Re Center и NPCIL
- Японский металлургический завод Japan Steel Works и IHI Corporation (в совместном предприятии с Toshiba , ранее)
- Объединенный машиностроительный завод России (ОМЗ-Ижора), ЗиО-Подольск и АЭМ-Атоммаш Волгодонск .
- В Южной Корее Doosan Group .
Смотрите также
- Ядерная физика
- Ядерного реактора
- Физика ядерного реактора
- Корпуса ядерных реакторов
- Радиационный ущерб
Рекомендации
Источник