Сосуд высокого давления кислород
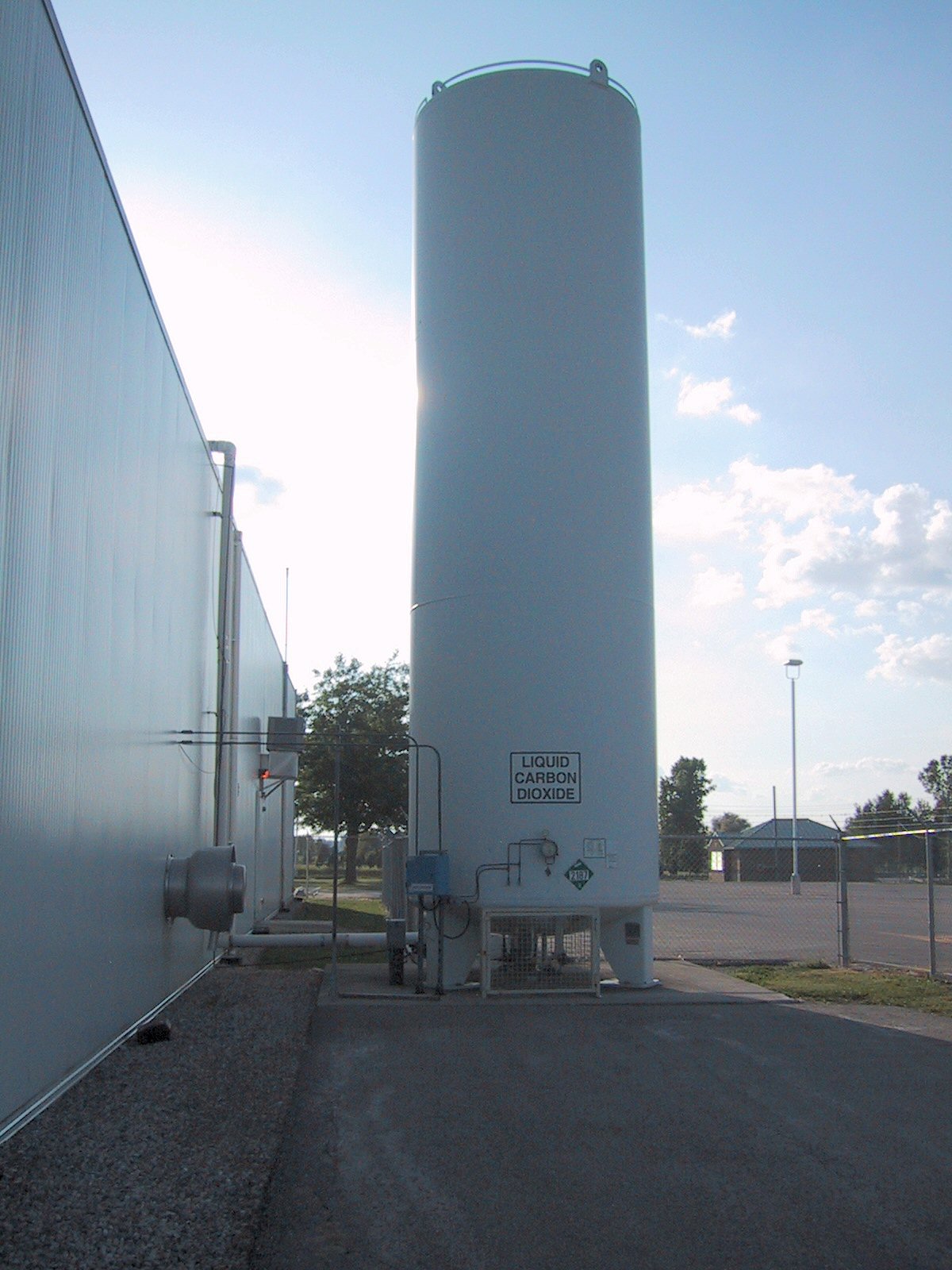
Губайдуллин Д.З.
ООО “Инженерный центр “Промбезопасность”
Начальник экспертно-диагностического отдела
e-mail: ikc_pb@list.ru
Бальжинова Л.Д.
ООО «Прогресс»
Ведущий инженер
e-mail: luninvp@mail.ru
Горохов И.А.
ООО «Прогресс»
Ведущий инженер-конструктор
e-mail: luninvp@mail.ru
Овчаренко И.И.
ООО «Прогресс»
Инженер-эксперт
e-mail: luninvp@mail.ru
Муравин А.Н.
Эксперт
ООО «ИТК ТЕХНОЛОГИЯ»
e-mail:etctech@gktb.ru
Понятие сосудов высокого давления: ёмкость, закрытая герметично. СВД (сокращение от: сосуды высокого давления) используются в двух направлениях: 1. Для протекания различных производственных процессов, например химических или тепловых. 2. Транспортировка (особенно на длительные расстояния) жидкостей, газообразных и прочих веществ.
Сфера применения сосудов высокого давления необычайно широка. В первую очередь, это конечно промышленность. В химической и нефтехимической отрасли, а также нефтяной, нефтегазоперерабатывающей сосуды высокого давления применяются повсеместно. Связано это, в первую очередь, со спецификой веществ, которая в них производится.
Во-вторых, сложно представить себе без них и нашу повседневную жизнь. Котёл отопления, газовый баллончик или даже баллон с кислородом для занятия дайвингом – всё это примеры сосудов высокого давления.
К сосудам высокого давления (в промышленном значении) относятся:
• сосуды, работающие под давлением воды с температурой выше 115 °С или других нетоксичных, не взрывопожароопасных жидкостей при температуре, превышающей температуру кипения при давлении 0,07 МПа (0,7 кгс/см2);
• сосуды, работающие под давлением пара, газа или токсичных взрывопожароопасных жидкостей свыше 0,07 МПа (0,7кгс/см2);
• баллоны, предназначенные для транспортировки и хранения сжатых, сжиженных и растворенных газов под давлением свыше 0,07 МПа (0,7 кгс/см2);
• цистерны и бочки для транспортировки и хранения сжатых и сжиженных газов, давление паров которых при температуре до 50 °С превышает давление 0,07 МПа (0,7 кгс/см2);
• цистерны и сосуды для транспортировки или хранения сжатых, сжиженных газов, жидкостей и сыпучих тел, в которых давление выше 0,07 МПа (0,7 кгс/см2) создается периодически для их опорожнения;
• барокамеры.
И не относятся к ним:
• сосуды атомных энергетических установок, а также сосуды, работающие с радиоактивной средой;
• сосуды вместимостью не более 0,025 м3 (25 л) независимо от давления, используемые для научно-экспериментальных целей. При определении вместимости из общей емкости сосуда исключается объем, занимаемый футеровкой, трубами и другими внутренними устройствами. Группа сосудов, а также сосуды, состоящие из отдельных корпусов и соединенные между собой трубами с внутренним диаметром более 100 мм, рассматриваются как один сосуд;
• сосуды и баллоны вместимостью не более 0,025 м3 (25 л), у которых произведение давления в МПа (кгс/см2)на вместимость в м3 (литрах) не превышает 0,02(200);
• сосуды, работающие под давлением, создающимся при взрыве внутри них в соответствии с технологическим процессом или горении в режиме само распространяющегося высокотемпературного синтеза;
• сосуды, работающие под вакуумом;
• сосуды, устанавливаемые на морских, речных судах и других плавучих средствах (кроме драг);
• сосуды, устанавливаемые на самолетах и других летательных аппаратах;
• воздушные резервуары тормозного оборудования подвижного состава железнодорожного транспорта, автомобилей и других средств передвижения;
• сосуды специального назначения военного ведомства;
• приборы парового и водяного отопления;
• трубчатые печи;
• сосуды, состоящие из труб с внутренним диаметром не более 150мм без коллекторов, а также с коллекторами, выполненными из труб с внутренним диаметром не более 150 мм;
• части машин, не представляющие собой самостоятельных сосудов (корпуса насосов или турбин, цилиндры двигателей паровых, гидравлических, воздушных машин и компрессоров).
Для управления работой и обеспечения безопасных условий эксплуатации сосуды в зависимости от назначения должны быть оснащены: запорной или запорно-регулирующей арматурой; приборами для измерения давления; приборами для измерения температуры; предохранительными устройствами; указателями уровня жидкости.
Сосуды, снабженные быстросъемными крышками, должны иметь предохранительные устройства, исключающие возможность включения сосуда под давление при неполном закрытии крышки и открывании ее при наличии в сосуде давления. Такие сосуды также должны быть оснащены замками с ключом-маркой.
Используемая литература:
1. “Правила промышленной безопасности опасных производственных объектов, на которых используется оборудование, работающее под избыточным давлением” Приказ от 25 марта 2014 года N 116.
2. «ГОСТ 12.2.085-2002. Сосуды, работающие под давлением. Клапаны предохранительные требования безопасности.
3. ПНАЭ Г-7-008-89 «Правила устройства и безопасной эксплуатации оборудования и трубопроводов атомных энергетических установок».
4. Постановление от 19 июня 2003 года N 2/99 «Правила устройства и безопасной эксплуатации сосудов, работающих под давлением, для объектов использования атомной энергии».
Источник
Текущая версия страницы пока не проверялась опытными участниками и может значительно отличаться от версии, проверенной 4 сентября 2018; проверки требует 1 правка.
У этого термина существуют и другие значения, см. Сосуд.
Сосуд под давлением — закрытая ёмкость (стационарно установленная или передвижная), предназначенная для ведения химических, тепловых и других технологических процессов, а также для хранения и транспортировки газообразных, жидких и других веществ[1]. Границей сосуда являются входные и выходные штуцеры.
Использование[править | править код]
Сосуды под давлением широко используются как в промышленности, так и в быту, спорте и пр. Разнообразие размеров, технических характеристик и способов применения их чрезвычайно велико, начиная от ядерных реакторов и заканчивая домашними отопительными котлами и баллонами для дайвинга. Другими примерами использования сосудов под давлением являются паровые котлы, барокамеры, автоклавы, ресиверы, цистерны, газовые баллоны и бочки, предназначенные для транспортировки или хранения сжатых, сжиженных газов, жидкостей и сыпучих тел.
Требования к сосудам под давлением в РФ[править | править код]
Крышка реактора PWR — сосуда с очень высокими параметрами среды
В едином перечне продукции, в отношении которой устанавливаются обязательные требования в рамках Таможенного союза, присутствуют пункты: «оборудование, работающее под избыточным давлением» и «сосуды, работающие под давлением».[2] Соответствующие требования установлены ТР ТС 032/2013 «О безопасности оборудования, работающего под избыточным давлением».[3]
Сосуды под давлением являются техническими устройствами, эксплуатация которых делают производственный объект опасным. С авариями сосудов под давлением связано большое количество несчастных случаев, поэтому на их проектирование, устройство, изготовление, реконструкцию, наладку, монтаж, ремонт, техническое диагностирование и эксплуатацию в большинстве стран мира накладывается ряд ограничений.
В России обязательны Федеральные нормы и правила в области промышленной безопасности «Правила промышленной безопасности опасных производственных объектов, на которых используется оборудование, работающее под избыточным давлением», а также ряд других отраслевых документов, действие которых ограничено своей специфической областью (например «Правила устройства и безопасной эксплуатации оборудования и трубопроводов атомных энергетических установок», «Правила устройства и безопасной эксплуатации сосудов, работающих под давлением, для объектов использования атомной энергии» и др.). Эти и другие[4] государственные документы устанавливают границы параметров содержащихся в сосуде веществ, превышение которых причисляет сосуд к опасным, в общем случае, как:
- вода с температурой выше 115 °С или другие нетоксичные, невзрывопожароопасные жидкости при температуре, превышающей температуру кипения при давлении 0,07 МПа;
- пар, газ или токсичные взрывопожароопасные жидкости с давлением свыше 0,07 МПа;
- сжатых, сжиженных и растворенных газов под давлением свыше 0,07 МПа.
Требования к оснащению[править | править код]
Для управления работой и обеспечения безопасных условий эксплуатации сосуды в зависимости от назначения должны быть оснащены:
- запорной или запорно-регулирующей арматурой;
- приборами для измерения давления;
- приборами для измерения температуры;
- предохранительными устройствами;
- указателями уровня жидкости.
Контроль сварных соединений[править | править код]
Организация-изготовитель (доизготовитель), монтажная или ремонтная организация обязаны применять такие виды и объёмы контроля своей продукции, которые гарантировали бы выявление недопустимых дефектов, её высокое качество и надежность в эксплуатации.
Контроль качества сварки и сварных соединений должен включать:
- проверку аттестации персонала;
- проверку сборочно-сварочного, термического и контрольного оборудования, аппаратуры, приборов и инструментов;
- контроль качества основных материалов;
- контроль качества сварочных материалов и материалов для дефектоскопии;
- операционный контроль технологии сварки;
- неразрушающий контроль качества сварных соединений;
- разрушающий контроль качества сварных соединений;
- контроль исправления дефектов.
Государственный надзор[править | править код]
Сосуды, на которые распространяются российские государственные правила, до пуска их в работу должны быть зарегистрированы в органах Ростехнадзора России[5], кроме специально оговоренных случаев, на основании письменного заявления владельца сосуда; при перестановке сосуда на новое место или передаче сосуда другому владельцу, а также при внесении изменений в схему его включения сосуд до пуска в работу должен быть перерегистрирован в органах Ростехнадзора России.
Кроме того сосуды, на которые распространяется действие государственных правил, должны подвергаться техническому освидетельствованию после монтажа, до пуска в работу, периодически в процессе эксплуатации и в необходимых случаях — внеочередному освидетельствованию с участием специалиста организации, имеющей лицензию Ростехнадзора России (если сосуд зарегистрирован). Объём, методы и периодичность технических освидетельствований сосудов (за исключением баллонов) должны быть определены изготовителем и указаны в руководстве по эксплуатации. В случае отсутствия таких указаний техническое освидетельствование должно проводиться в соответствии с требованиями государственных правил.
См. также[править | править код]
- Паровой котёл
- Ресивер (сосуд)
- Барокамера
Примечания[править | править код]
Эта статья или раздел описывает ситуацию применительно лишь к одному региону, возможно, нарушая при этом правило о взвешенности изложения. Вы можете помочь Википедии, добавив информацию для других стран и регионов. |
Источник
2.1. Назначение и требования, предъявляемые к кислородному оборудованию самолетов
С подъемом на высоту уменьшается парциальное давление кислорода, что приводит к кислородному голоданию. Во избежание этого на самолетах устанавливают кислородное оборудование, которое предназначено для увеличения парциального давления кислорода, как за счет повышения концентрации, так и увеличения его абсолютного давления во вдыхаемой смеси.
Кислородное оборудование устанавливается на самолетах с высотой полета более 3 км и применяется как средство подачи дыхательной смеси:
1) для повышения парциального давления кислорода в альвеолярном воздухе;
2) в случае разгерметизации кабины и принудительного покидании самолета экипажем;
3) для обеспечения работоспособности экипажа при появлении в кабине дыма и токсичных газов;
4) для использования кислорода в профилактических целях при появлении утомляемости экипажа в длительных полетах и в терапевтических целях для пассажиров.
Требования, предъявляемые к кислородному оборудованию:
1. Полная автоматизация всех процессов подачи кислорода. Это вызвано тем, что в нормальных условиях кислород является газом без цвета, запаха и вкуса, поэтому без специальных приборов нельзя проконтролировать количество кислорода во вдыхаемом воздухе.
2. В связи с большой окислительной способностью все ответственные детали кислородных приборов, должны изготавливаться из некорродирующих материалов: коррозионно-стойкой стали, латуни, пластмасс и прорезиненной ткани.
3. Кислородная система и ее агрегаты должны быть работоспособны при воздействии вибрации, механических ударов, изменении давления воздуха, температуры, влажности и т.д.
4. Стационарные источники кислорода должны иметь устройства для аварийного сброса кислорода за борт в случае опасного повышения давления в них.
5. Кислородная система и входящие в нее агрегаты должны иметь минимально возможные габаритные размеры и массу.
Кислород при некоторых условиях становится пожаро- и взрывоопасным:
а) различные жиры и масла при соприкосновении со сжатым до давления 0,6 МПа и более кислородом способны самовоспламеняться;
б) горючие газы (водород, метан, ацетилен и др.) образуют с кислородом взрывчатые смеси;
в) клетчатка (вата, пакля, древесные опилки и др.) под действием сжатого или жидкого кислорода взрываются при ударе;
г) пористые горючие вещества (мох, торф, уголь, угольная пыль), пропитанные жидким кислородом, при воспламенении в замкнутом ограниченном пространстве дают взрыв большой разрушительной силы.
Кислородное оборудование должно иметь хороший доступ к агрегатам для осмотра, обслуживания и контроля наличия и правильной подачей кислорода потребителям. Недопустимо размещение кислородных приборов в непосредственной близости от масло- и бензопроводов. Дымозащитное снаряжение членов экипажа должно размещаться в непосредственной близости от их рабочих мест.
В пассажирских салонах контейнеры с кислородными масками должны располагаться в багажных полках над каждым блоком пассажирских кресел (или в спинках впереди стоящих кресел), вблизи рабочих мест бортпроводников, в кухне и туалетах.
Источники кислорода
Тип источника кислорода на борту самолета определяется, в основном, общей массой кислорода, необходимого для обеспечения одного полета с учетом возможной разгерметизации кабины.
В качестве источников кислорода в авиационных системах кислородного питания (СКП) можно выделить следующие: баллоны высокого и низкого давления; газификаторы; химические генераторы и бортовые газоразделительные аппараты.
Баллонные источники
Наиболее распространенным в настоящее время является баллонные источники (предпочтительный ряд объемов баллонов составляет в литрах: 2, 4, 6 и 8).
Рис. 2.1. Формы кислородных баллонов: 1 – цилиндрический (высокого давления); 2 – цилиндрический сварной (низкого давления); 3 – сферический; 4 – цилиндрический с наружной оплеткой |
Основное преимущество баллонной системы состоит в многоразовости использования баллонов и возможности находиться под давлением неограниченно долгое время.
Баллонные системы имеет существенный недостаток – относительно большой массовый коэффициент (масса пустого баллона, приходящаяся на единицу массы помещенного в него кислорода). Для баллонов из легированной стали большой емкости (более 25 л) при запасе прочности, равном 3…4, давлении зарядки 21 МПа массовый коэффициент составляет (2,2…2,5) кг/л. Форма баллонов показана на рис. 2.1.
Цилиндрические баллоны высокого давления обычно изготавливаются из отрезков толстостенных бесшовных труб, концы которых при горячей ковке превращаются в днище и горловину, толщины которых значительно увеличиваются.
Сферические баллоны свариваются из двух штампованных половин.
Для изготовления кислородных баллонов непригоден титан, так как он нестоек к действию кислорода и интенсивно окисляется под высоким давлением. Для облегчения баллонов иногда применяется армирование их внешней поверхности стекловолокном или металлической проволокой.
Жидкостные газификаторы
Кислород в сжиженном состоянии хранится на борту самолетов в специальных теплоизолированных сосудах-газификаторах под небольшим избыточным давлением. Массовый коэффициент (кг/л) газификаторов большой емкости (более 15 кг) составляет 1… 1,5, малой (менее 15 кг) – 1,6…2.
Применение жидкостных газификаторов целесообразно на самолетах с большим количеством экипажа и значительной продолжительностью полета. Однако при хранении кислорода газификатор имеет существенные потери вследствие испарения кислорода и поэтому малопригоден для длительного хранения.
Жидкий кислород имеет удельную массу 1,14 кг/л при температуре минус 182,98°С (точка замерзания составляет -222,6°С). Для превращения 1 кг жидкого кислорода в газообразное состояние с подогревом от -183 до +20°С необходимо подвести 0,4 кДж тепла. Небольшая теплота испарения представляет основную трудность при хранении жидкого кислорода.
Газификатор состоит из сосуда Дьюара, предназначенного для хранения жидкого кислорода, системы газификации жидкого кислорода с автоматическим регулированием давления и системы контроля запаса жидкого кислорода.
Принципиальная схема газификатора показана на рис. 2.2.
Рис. 2.2. Схема самолетного газификатора жидкого кислорода: 1 – теплоизоляционный сосуд; 2 – электромагнитный кран; 3 – испаритель; 4 – кран; 5 – ограничитель давления; 6 – обратный клапан линии заправки; 7 – предохранительный клапан; 8 – кран линии дренажа, открываемый при заправке |
Заправка газификатора жидким кислородом осуществляется от транспортного резервуара жидкого кислорода (ТРЖК). Сосуд 1 заправляется жидким кислородом через штуцер с обратным клапаном 6, который под действием избыточного давления жидкого кислорода (до 200 кПа), создаваемого в ТРЖК, открывается и дает доступ жидкому кислороду в сосуд. При заправке СКГ вентиль 8 должен быть открыт (для выхода газа из сосуда). Чтобы жидкий кислород при заправке не поступал в испаритель 3 (это увеличивает время заправки и потери кислорода), электромагнитный клапан 2 должен находиться в закрытом положении. Вентиль 4 – «кислород потребителю» расходной магистрали должен быть закрыт. Во время заправки ограничитель давления 5 и предохранительный клапан 7 не работают.
В первый момент подачи от ТРЖК в СКГ жидкий кислород расходуется на охлаждение заправочной магистрали и сосуда, испаряется и в виде газа выходит за борт через штуцер 8 «кислород в атмосферу при заливке». В испаритель 3 кислород не поступает, так как в нем при заливке устанавливается давление, равное давлению заправки. При полностью заправленном сосуде указатель запаса кислорода показывает 100%, а из штуцера 8 пойдет устойчивая струя жидкого кислорода. После окончания заправки шланг ТРЖК отсоединяется от бортового штуцера «залив кислорода». При этом обратный клапан 6 закрывается и препятствует выбросу жидкого кислорода в атмосферу.
При хранении кислорода в СКГ под давлением электромагнитный клапан 2, вентили 4 и 8 должны быть закрыты. Под действием притока теплоты из окружающей атмосферы кислород в сосуде будет частично испаряться, в связи, с чем давление в сосуде 1 будет повышаться. При повышении давления в сосуде до 1,02 ±0,02 МПа открывается предохранительный клапан 7 и стравливает избыток кислорода в атмосферу.
Для пользования кислородом открывается кран 4 в положение «газификация» и включается электромагнитный клапан – СКГ пускается в работу. Жидкий кислород под действием статического столба жидкости поступает из сосуда 1 в испаритель 3, где преобразуется в газовую фазу. Испаритель на части своей длины имеет двойной канал. По одному из них кислород поступает к потребителю, а по второму – к ограничителю давления 5. Кислород из испарителя 3 через открытый клапан 5 поступает по центральной трубке в газовую полость сосуда. При испарении жидкого кислорода давление во всей системе и сосуде повышается и, как только оно достигнет величины (0,85 ± 0,05) МПа, срабатывает ограничитель давления 5 и закрывает доступ газа в сосуд из испарителя. Рост давления в сосуде прекратится. Жидкий кислород в испарителе 3, испаряясь после закрытия ограничителя давления 5, выдавливает остатки жидкого кислорода в сосуд. Отбор кислорода потребителем через кислородные приборы происходит из испарителя 3 при открытии вентиля 4 – «кислород потребителю».
Рис. 2.3. Схема устройства хлоратного химического генератора кислорода: 1 – пусковое (запальное) устройство; 2 – хлоратная «свеча»; 3 – теплоизолятор; 4 – фильтр вредных примесей |
При расходе кислорода потребителем давление в системе и сосуде начинает падать и при достижении величины ниже (0,85+0,05)МПа открывается ограничитель давления 5. Жидкий кислород из сосуда вновь поступает в испаритель 3, где газифицируется. Давление в системе и в сосуде вновь повышается до (0,85 ± 0,05) МПа. Ограничитель давления 5 закрывает проходное сечение. Таким образом, ограничитель давления 5 прикрывает проходное сечение при возрастании давления в сосуде и испарителе и, наоборот, увеличивает проходное сечение при уменьшении давления в сосуде и испарителе, т.е. обеспечивает регулирование и поддержание рабочего давления в газификаторе при его работе.
Когда газообразный кислород не расходуется, жидкий кислород удерживается в сосуде с помощью гидравлического затвора в сливной трубке, которая выполнена в виде сифона.
Давление в сосуде может расти и выше 0,9 МПа, если испаряемость кислорода превышает его расход потребителем. При избыточном давлении (1,02 ± 0,02) МПа предохранительный клапан 7 приоткрывается и стравливает избыток давления в атмосферу, а при давлении в 1,15 МПа клапан открывается полностью.
В газификаторах испарившийся в испарителе кислород перед подачей его потребителю подогревается в змеевике, смонтированном в кожухе газификатора. Здесь горячий воздух обдувает испаритель, и дополнительный подогрев газообразного кислорода перед кислородными приборами не требуется.
Химические источники
Химические генераторы кислорода представляют собой аппараты, в которых кислород выделяется из химических веществ путем их термического разложения, электролиза или иного вида реакции.
Рис. 2.4. Схема устройства хлоратного химического генератора кислорода: 1 – электрозапальное устройство; 2 – химические генераторы кислорода; 3 – обратный клапан; 4 – фильтр примесей; 5 – баллон-ресивер; 6 – редуктор; 7 – световое табло, «сигнализирующего о наличии кислорода; 8 – сигнализатор давления; 9 – блок электроавтоматики поочередного запуска генераторов |
Применяемые на некоторых самолетах химические генераторы кислорода используют реакцию разложения алкалоидов металлов (хлоратов, перхлоратов). При их разложении может выделяться до 40…50% кислорода от общей массы. Необходимость использования устройств для охлаждения выделяемого кислорода и для очистки его от вредных примесей повышает относительную массу аппарата, приближая ее к относительной массе баллонов. Большим преимуществом хлоратных генераторов кислорода является возможность их длительного хранения практически без эксплуатационных затрат. Это особенно важно для запаса кислорода аварийного назначения, который должен находиться в постоянной готовности к работе. Схемы устройства генератора и системы с его использованием даны соответственно на рис. 2.3 и 2.4.
Бортовые разделители кислорода. Другим перспективным направлением развития самолетных источников кислорода следует считать создание бортовых аппаратов для получения кислорода из атмосферного воздуха непосредственно в полете.
Схема одного из возможных вариантов такого аппарата представлена на рис. 2.5. Отделение кислорода в этом аппарате производится при помощи так называемых хелатных соединений. При низкой температуре и высоком давлении эти вещества сорбируют кислород из воздуха, а при последующем нагреве и вакуумировании поглотительного патрона происходит десорбция кислорода. Реализация подобной системы в приемлемом для самолетных условий варианте с учетом лимитов массы, габаритных размеров, а также требований по ресурсам и эксплуатационной технологичности позволит иметь автономный постоянный источник кислорода, не зависящий от продолжительности полета и не требующий заправки на земле.
Особенности эксплуатации кислородного оборудования
Специфической особенностью эксплуатации кислородного оборудования является повышенная опасность возникновения пожара и взрыва в результате взаимодействия материалов с кислородом или с обогащенным кислородом воздухом. Поэтому выбор конструкционных материалов и технических решений при проектировании кислородного оборудования обусловлен выполнением, необходимых требований безопасного применения.
Рис. 2.5. Схема установки для получения кислорода из воздуха, действующей на базе хелатных соединений: 1 – подача сжатого воздуха от системы наддува кабины (от компрессора двигателя); 2 – кран; 3 – патрон с хелатным соединением в стадии сорбции кислорода; 4 – кран; 5 – выброс воздуха в кабину; 6 – патрон с хелатным соединением в стадии десорбции кислорода; 7 – нагревательный элемент; 8 – к компрессору; 9 – компрессор; 10 – ресивер; 11 – на потребление |
Прежде всего, должно быть исключено применение легко воспламеняемых и интенсивно горящих или образующих взрывчатые смеси веществ.
При эксплуатации кислородного оборудования могут возникать непредвиденные утечки кислорода из системы и повреждения, при которых создается повышенная концентрация кислорода в зонах ограниченного объема: отсеках, контейнерах и т.п. Опасность в этом случае усугубляется тем, что кислород вступает в контакт с материалами, не предназначенными для работы в такой атмосфере.
С учетом этого обстоятельства при компоновке кислородного оборудования на борту самолета необходимо обеспечивать размещение агрегатов и трубопроводов в хорошо вентилируемых местах в максимально возможном удалении от легковоспламеняющихся материалов и от вероятных источников воспламенения (искробразующих электроприборов и т.п.).
Применение надлежащим образом обезжиренных и очищенных трубопроводов из меди, никеля и сплавов на основе меди практически полностью исключает вероятность загорания при контакте с кислородом, находящимся под давлением до 40 МПа и более. Однако, в целях снижения массы и стоимости трубопроводов целесообразно, где возможно, применять трубопроводы из алюминиевых сплавов или нержавеющей стали.
Источник