Сварка сосудов и аппаратов под давлением
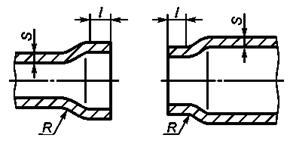
содержание ..
90
91
92
93
94
95
96
97
98
99 ..
4-4.
Сварка СОСУДОВ РАБОТАЮЩИХ ПОД ДАВЛЕНИЕМ
4-4-1. Сварка сосудов и их элементов должна производиться в соответствии
с требованиями технических условий на изготовление сосудов и
утвержденных в установленном порядке производственных инструкций;
последнее должны быть разработаны с учетом специфики изготовляемых
изделий.
Использование новых методов сварки разрешается главным инженером”
предприятия после подтверждения ее технологичности на изделиях, проверки
всего комплекса требуемых свойств сварных соединений и положительного
заключения головной научно-исследовательской организации.
* 4-4-2. К сварке сосудов и их элементов допускаются сварщики, имеющие
удостоверения установленного образца на право производства сварочных
работ, выданные квалификационной комиссией в соответствии с Правилами
аттестации сварщиков, утвержденными Госгортехнадзором СССР. При этом
сварщики могут быть допущены только к тем видам работ, которые указаны в
удостоверениях.
4-4-3. Перед допуском сварщика к выполнению сварочных работ, связанных с
изготовлением сложных или специфичных сварных конструкций, предприятие
обязано провести специальную подготовку и испытание сварщика, сделав об
этом отметку в его удостоверении.
4-4-4. Перед началом сварки должно быть проверено качество сборки
соединяемых элементов, а также состояние стыкуемых кромок и прилегающих
к ним поверхностей. При сборке не допускается подгонка кромок,
вызывающая дополнительные напряжения в металле.
4-4-5. Прихватки должны выполняться с применением присадочных
материалов, предусмотренных техническими условиями для данного сосуда.
4-4-6. Недопустимые дефекты сварки, обнаруженные в процессе изготовления
сварных сосудов и их элементов, должны быть устранены сваркой и
подвергнуты повторному контролю .
4-4-7. Не допускается ведение сварочных работ по изготовлению сосудов и
их элементов при температуре окружающего воздуха ниже 0° С.
При монтаже и ремонте сосудов допускается сварка при отрицательной
температуре окружающего воздуха, если соблюдены требования,
предусмотренные в нормалях, или технических условиях, или инструкциях по
монтажу и ремонту сосудов.
4-4-8. При дожде, ветре и снегопаде сварочные работы по монтажу сосуда
могут выполняться лишь при условии надлежащей защиты сварщика и места
сварки.
* 4-4-9. Технология сварки сосудов должна быть детально разработана и
предусматривать такой порядок выполнения работ, при котором внутренние
напряжения в сварных соединениях будут минимальными.
4-5. Термическая обработка СОСУДОВ РАБОТАЮЩИХ
ПОД ДАВЛЕНИЕМ
4-5-1. Термической обработке подлежат сосуды, в стенках которых в
процессе изготовления (при вальцовке, штамповке, сварке и т. п.)
возможно появление недопустимых напряжений а также сосуды, прочность
которых достигается термообработкой.
Необходимость и режимы термообработки устанавливаются техническими
условиями на изготовление изделия.
4-5-2. Допускается термическая обработка сосуда по частям с последующей
местной термообработкой замыкающего шва (швов). При местной
термообработке должны быть обеспечены равномерный нагрев и охлаждение по
всей длине шва и примыкающей к нему зоны основного металла на ширину, в
2—3 раза превышающую ширину шва.
содержание ..
90
91
92
93
94
95
96
97
98
99 ..
Источник
СВАРКА И РЕЗКА МЕТАЛЛОВ
Резервуары и сосуды, работающие без давления. К этой группе относятся резервуары и сосуды для хранения жидкостей, газгольдеры для газа низкого давления (менее 0,7 ати). Близкими к этим конструкциям по технологическим приемам сварки являются газопроводы большого диаметра, кожухи различного рода химической аппаратуры, корпуса судов, их переборки, палубы, обшивка и пр. Изделия данного типа собирают из листов толщиной до
10— 12 мм, свариваемых друг с другом в стык или в нахлестку При монтаже таких конструкций швы приходится сваривать в разнообразных положениях: нижнем, вертикальном, горизонтальном и потолочном. От швов в этих конструкциях требуется не только прочность, но и плотность.
Типичными для данной группы конструкций являются резервуары для нефтепродуктов, состоящие из плоского днища, цилиндрической части и крыши. Такие резервуары строятся обычно емкостью до 10 000 мъ. Цилиндрическая часть резервуара изготовляется из поясов, высота которых определяется шириной листов и равна 1400—1500 мм. Вертикальные швы свариваются в стык, горизонтальные — в стык или в нахлестку. Ширина нахлестки должна равняться четырехкратной толщине листа, но не менее 20 мм Листы крыши укладываются на решетчатые фермы и балки, располагаемые по радиусам и скрепляемые поперечными прогонами.
В настоящее время при изготовлении резервуаров широко используются наиболее передовые способы сварки — автоматическая и полуавтоматическая под слоем флюса и в среде углекислого газа. Ручная сварка применяется при сборочно-монтажных работах Используются также новые методы организации работ по строительству резервуаров. Так, например, получил распространение новый рулонный метод изготовления крупных резервуаров, разработанный сотрудниками Института электросварки им. Е. О. Патона. По этому способу стенка, днище и кровля резервуара изготовляются заблаговременно на заводе из отдельных листов с применением автоматической сварки Готовые полотнища свертываются в рулон и в таком виде транспортируются на место установки резервуара Корпус резервуара емкостью 5000 мА, диаметром 23 м и высотой 12 м сворачивается в восьмислойный рулон диаметром 2,8 м, весом 40 т.
С помощью кранов рулоны устанавливают на днище (рис. 68), с помощью лебедок и тракторов их развертывают, после чего резер-
Рис. 68. Развертывание рулона корпуса и монтаж ферм кровли при изготовлении нефтерезервуара
вуар окончательно сваривают Фермы кровли монтируются в процессе развертывания рулона Новый способ значительно сокращает стоимость и сроки сборки и сварки резервуаров и позволяет механизировать основные операции по их сооружению, а также улучшает качество резервуаров
Сосуды, работающие под давлением. К этой категории относятся сосуды, в которых рабочее давление превышает атмосферное более чем на 0,7 ати, например резервуары для сжатых газов, химическая аппаратура, паровые котлы, цистерны для сжиженных газов и др Качество сварных швсв в таких сосудах должно быть высоким и регламентируется правилами Госгортехнадзора СССР. К сварке этих сосудов допускаются лица сдавшие специальные испытания в соответствии с правилами Госгортехнадзора и полу-
чившие удостоверениз (диплом) на право сварки сосудов, работающих под давлением.
Сосуды емкостью не свыше 25 л, у которых произведение емкости в литрах на рабочег давление в атмосферах составляет не более 200,, не подлежат действию указанных выше правил независимо от величины рабочего давления в них.
Наплавленный мзталл швов в сосудах для работы под высоким давлением должен обладать механическими свойствами, указанными в табл. 22.
Таблица 22
Механические свойства наплавленного металла швов сосудов, работающих под давлением
Механические свойства наплавленного металла | Низколегированные стали | Углеродистые стали | ||
дуговая сварка | газовая сварка | |||
дуговая сварка | газовая сварка | |||
Предел прочности, кгс/мм2 . . Относительное удлинение, % (не менее) ……………………………………………… Ударная вязкость, кг с – м j см2 (не менее) ……………………………………………………….. | Не йости ОС или ТУ стали 16 5 | ниже ниж :новиого л ДЛЯ СООТВ 12 4 | НЄГО ПрЄд€ металла. п етствующ[9] 18 8 | ла проч – о ГОСТ їй марки 16 4 |
Применяемые при сварке таких резервуаров электроды и металл должны иметь сертификаты*, удостоверяющие их качество. Сосуды, изготовленные из углеродистых сталей, подлежат обязательной термообработке в следующих случаях:
а) если толщина стенки цилиндрической части или днища сосуда в месте сварного стыка более 35 мм
б) если толщина стенки цилиндрической части сосуда, изготовленной из листовой стали вальцовксй, превышает величину, вы-
п численную по формуле ^2р127, > где DB — внутренний диаметр сосуда, см;
в) при изготовлении днищ сосуда (независимо от толщины их стенки) холодной или горячей штамповкой при температуре окончания штамповки ниже 700°. Днища могут подвергаться термообработке до приварки их к обечайке, и в этом случае термообработка, сосуда может не производиться, если она не требуется согласно пп. а и б.
Допускается термообработка сосуда по частям с последующей окончательной местной термообработкой соединительного шва в кольцєеой печи или специальными нагревательными устройствами.
Проверка механических свойств сварных соединений сосудов, работающих под давлением, производится путем испытания образцов, вырезанных из пробных пластин, сваренных одновременно с основным изделием. Механические свойства сварных соединений должны удовлетворять приведенным выше требованиям правил Госгортехнадзора СССР.
После сварки все изделия подвергаются испытанию на прочность и плотность гидравлическим давлением. Для сосудов, у которых рабочее давление менее 5 ати, величина пробного гидравлического давления берется на 50% больше величины рабочего давления, но не ниже 2 ати. При рабочем давлении свыше 5 ати пробное гидравлическое давление должно на 25% (но не менее чем на 3 ати) превышать рабочее давление. Элементы сосудов, работающие при температуре стенки свыше 450° и независимо от температуры стенки — при давлении свыше 50 ати, а также сосуды, изготовленные из легированной стали, воспринимающей закалку на воздухе или склонной к образованию межкристаллитных трещин, подвергаются еще металлографическим исследованиям сварных образцов, вырезанных из контрольных пластин или стыков, если эти испытания предусмотрены ТУ на изготовление.
Кроме вышеуказанных испытаний, стыковые сварные швы исследуются путем проев :чивания рентгеновскими или гамма-лучами[10]. В сосудах, работающих при давлении свыше 50 ати и температуре стенки свыше +430 и ниже —70°, просвечивается 25% общей длины стыковых швов; в сосудах, испытывающих давление до 50 ати и работающих при температуре стенки от +200 до +400 и от —49 до —70°, —15% длины стыковых швов; в сосудах с давлением до 16 ати и температурой стенки от +200 до —40°—10% длины стыковых швов.
Все выполненные швы сварщик обязан клеймить присвоенным ему номером или шифром.
Готовые сосуды снабжаются паспортом, в котором указываются: наименование и заводской номер сосуда, наименование и адрес завода-изготовителя, дата выпуска, рабочее давление и температура стенки, емкость, характер рабочей среды, результаты испытаний и другие сведения, требуемые правилами.
В сосудах, работающих под давлением, следует применять стыковые швы по возможности с двухсторонней сваркой или с подваркой обратной стороны. Сварка должна вестись преимущественно в нижнем положении. Сборочные отверстия в свариваемых листах не допускаются.
Днища сосудос, работающих под давлением, делают обычно выпуклыми и приваривают к обечайке стыковым швом. Продольные и поперечные швы обечаек должны быть только стыковыми Допускаются соединения в тавр для приварки плоских днищ, грубных решеток, фланцев, штуцеров и других подобных элементов, а также двухсторонняя приварка выпуклых днищ в нахлестку к цилиндрической обечайке при толщине отбортованной части днища не свыше 16 мм.
В настоящее время большинство сосудов, работающих под давлением, выполняют с помощью автоматической сварки под флюсом, а толстостенные сосуды — автоматической электрошлаковой сварки. Эти современные способы сварки обеспечивают большую производительность и высокое качество сварных швов. Ручной дуговой сваркой выполняются только короткие швы в местах прихваток, приварки патрубков, опор, люков и др., а также иногда производится предварительная подварка корня швов, свариваемых автоматической сваркой, если эта подварка предусмотрена по технологии.
Есть несколько факторов, анализировать которые при выборе сварочного аппарата нужно обязательно в магазине сварочного оборудования. Следует учесть рабочий диапазон температур, а также мощность. Рекомендуется учесть возможность смены полярности, и показатель …
С каждым днем лазерная резки металла становиться все более востребованной. Давайте разберемся в этом почему же так?
В наши дни, работа сварочным оборудованием используется во многих сферах жизни: начиная от строительства высокоэтажных домов и заканчивая созданием предметов интерьера. Но что же скрывается за этим, малопонятным непосвященному, словом? …
Источник
Версия для печати
4.1 Общие требования
4.1.1 Конструкция сосудов должна быть технологичной, надежной в течение установленного в технической документации срока службы, обеспечивать безопасность при изготовлении, монтаже и эксплуатации, предусматривать возможность осмотра (в том числе внутренней поверхности), очистки, промывки, продувки и ремонта, контроля технического состояния сосуда при диагностировании, а также контроля за отсутствием давления и отбора среды перед открытием сосуда.
Если конструкция сосуда не позволяет при техническом освидетельствовании проведение осмотра (наружного или внутреннего), гидравлического испытания, то разработчик сосуда должен в технической документации на сосуд указать методику, периодичность и объем контроля сосуда, выполнение которых обеспечит своевременное выявление и устранение дефектов.
4.1.2 Срок службы сосуда устанавливает разработчик сосуда, и он указывается в технической документации.
4.1.3 При проектировании сосудов следует учитывать требования Правил перевозки грузов железнодорожным, водным и автомобильным транспортом.
Сосуды, которые не могут быть транспортированы в собранном виде, должны проектироваться из частей, соответствующих по габаритам требованиям к перевозке транспортными средствами. Деление сосуда на транспортируемые части следует указывать в технической документации.
4.1.4 Расчет на прочность сосудов и их элементов следует проводить в соответствии с ГОСТ Р 52857.1 – ГОСТ Р 52857.11, ГОСТ Р 51273, ГОСТ Р 51274, ГОСТ 30780.
Допускается использование настоящего стандарта совместно с другими международными и национальными стандартами на расчет на прочность при условии, что их требования не ниже требований российских национальных стандартов.
4.1.5 Сосуды, транспортируемые в собранном виде, а также транспортируемые части должны иметь строповые устройства (захватные приспособления) для проведения погрузочно-разгрузочных работ, подъема и установки сосудов в проектное положение.
Допускается использовать технологические штуцера, горловины, уступы, бурты и другие конструктивные элементы сосудов при подтверждении расчетом на прочность.
Конструкция, места расположения строповых устройств и конструктивных элементов для строповки, их количество, схема строповки сосудов и их транспортируемых частей должны быть указаны в технической документации.
4.1.6 Опрокидываемые сосуды должны иметь приспособления, предотвращающие самоопрокидывание.
4.1.7 В зависимости от расчетного давления, температуры стенки и характера рабочей среды сосуды подразделяют на группы. Группу сосуда определяет разработчик, но не ниже, чем указано в таблице 1.
Таблица 1 – Группы сосудов
Группа | Расчетное давление, МПа | Температура стенки, °С | Характеристика рабочей среды |
---|---|---|---|
1 | Независимо | Независимо | Взрывоопасная, пожароопасная, токсичная 1-го, 2-го, 3-го классов опасности по ГОСТ 12.1.007 |
2 | До 2,5 | Выше 400 | Любая, за исключением указанной для 1-й группы сосудов |
2,5 до 5,0 | Выше 200 | ||
5,0 и более | Независимо | ||
До 5,0 | Ниже минус 40 | ||
3 | До 2,5 | От минус 40 до 400 | |
От 2,5 до 5,0 | От минус 40 до 200 | ||
4 | До 1,6 | От минус 20 до 200 | |
5 | От вакуума до 0,07 | Независимо | Взрывобезопасная, пожаробезопасная или 4-го класса опасности по ГОСТ 12.1.007 |
Группу сосуда с полостями, имеющими различные расчетные параметры и среды, допускается определять для каждой полости отдельно.
4.1.8 Базовые диаметры сосудов рекомендуется принимать по ГОСТ 9617.
4.2 Днища, крышки, переходы
4.2.1 В сосудах применяют днища: эллиптические, полусферические, торосферические, сферические неотбортованные, конические отбортованные, конические неотбортованные, плоские отбортованные, плоские неотбортованные, плоские, присоединяемые на болтах.
4.2.2 Заготовки выпуклых днищ допускается изготовлять сварными из частей с расположением сварных швов согласно указанным на рисунке 1.
Рисунок 1 – Расположение сварных швов заготовок выпуклых днищ
Расстояния l и l1 от оси заготовки эллиптических и торосферических днищ до центра сварного шва должны быть не более 1/5 внутреннего диаметра днища. При этом для вариантов в), д), ж), и), к), л) сумма расстояний l + l1 должна быть не менее 1/5 внутреннего диаметра днища.
При изготовлении заготовок с расположением сварных швов согласно рисунку 1 м) количество лепестков не регламентируется.
4.2.3 Выпуклые днища допускается изготовлять из штампованных лепестков и шарового сегмента. Количество лепестков не регламентируется.
Если по центру днища устанавливают штуцер, то шаровой сегмент допускается не изготовлять.
4.2.4 Круговые швы выпуклых днищ, изготовленных из штампованных лепестков и шарового сегмента или заготовок с расположением сварных швов согласно рисунку 1 м, должны быть расположены от центра днища на расстоянии по проекции не более 1/3 внутреннего диаметра днища. Для полусферических днищ расположение круговых швов не регламентируется.
Наименьшее расстояние между меридиональными швами в месте их примыкания к шаровому сегменту или штуцеру, установленному по центру днища вместо шарового сегмента, а также между меридиональными швами и швом на шаровом сегменте, должно быть более трехкратной толщины днища, но не менее 100 мм по осям швов.
4.2.5 Основные размеры эллиптических днищ должны соответствовать ГОСТ 6533. Допускаются другие базовые диаметры эллиптических днищ при условии, что высота выпуклой части не менее 0,25 внутреннего диаметра днища.
4.2.6 Полусферические составные днища (см. рисунок 2) применяют в сосудах при выполнении следующих условий:
– нейтральные оси полушаровой части днища и переходной части обечайки корпуса должны совпадать; совпадение осей должно быть обеспечено соблюдением размеров, указанных в конструкторской документации;
– смещение t нейтральных осей полушаровой части днища и переходной части обечайки корпуса не должно превышать 0,5(S – S1);
– высота h переходной части обечайки корпуса должна быть не менее 3у.
Рисунок 2 – Узел соединения днища с обечайкой
4.2.7 Сферические неотбортованные днища допускается применять в сосудах 5-й группы, за исключением работающих под вакуумом.
Сферические неотбортованные днища в сосудах 1-й, 2-й, 3-й, 4-й групп и в сосудах, работающих под вакуумом, допускается применять только в качестве элемента фланцевых крышек.
Сферические неотбортованные днища (см. рисунок 3) должны:
– иметь радиус сферы R не менее 0,85D и не более D;
– привариваться сварным швом со сплошным проваром.
Рисунок 3 – Сферическое неотбортованное днище
4.2.8 Торосферические днища должны иметь:
– высоту выпуклой части, измеренную по внутренней поверхности, не менее 0,2 внутреннего диаметра днища;
– внутренний радиус отбортовки не менее 0,095 внутреннего диаметра днища;
– внутренний радиус кривизны центральной части не более внутреннего диаметра днища.
4.2.9 Конические неотбортованные днища или переходы допускается применять:
а) для сосудов 1-й, 2-й, 3-й, 4-й групп, если центральный угол при вершине конуса не более 45°. Допускается использование конических днищ и переходов с углом при вершине более 45° при условии дополнительного подтверждения их прочности расчетом по допускаемым напряжениям в соответствии с ГОСТ Р 52857.1, подраздел 8.10;
б) для сосудов, работающих под наружным давлением или вакуумом, если центральный угол при вершине конуса не более 60°.
Части выпуклых днищ в сочетании с коническими днищами или переходами применяют без ограничения угла при вершине конуса.
4.2.10 Плоские днища (см. рисунок 4), применяемые в сосудах 1-й, 2-й, 3-й, 4-й групп, следует изготовлять из поковок.
При этом следует выполнять следующие условия:
– расстояние от начала закругления до оси сварного шва не менее (D – внутренний диаметр обечайки, S – толщина обечайки);
– радиус закругления r ≥ 2,5S [см. рисунок 4а)];
– радиус кольцевой выточки r1 ≥ 2,5S, но не менее 8 мм [см. рисунок 4б)];
– наименьшая толщина днища [см. рисунок 4б)] в месте кольцевой выточки S2 ≥ 0,8S1, но не менее толщины обечайки S (S1 – толщина днища);
– длина отбортовки днищ h1 ≥ r;
– угол проточки γ должен составлять от 30° до 90°;
– зона А контролируется в направлениях Z согласно требованиям 5.4.2.
Рисунок 4 – Плоские днища
Допускается изготовление плоского днища (см. рисунок 4) из листа, если отбортовка выполняется штамповкой или обкаткой кромки листа с изгибом на 90°.
4.2.11 Основные размеры плоских днищ, предназначенных для сосудов 5-й группы, должны соответствовать ГОСТ 12622 или ГОСТ 12623.
4.2.12 Длина цилиндрического борта l (l – расстояние от начала закругления отбортованного элемента до окончательно обработанной кромки) в зависимости от толщины стенки S (см. рисунок 5) для отбортованных и переходных элементов сосудов, за исключением штуцеров, компенсаторов и выпуклых днищ, должна быть не менее указанной в таблице 2. Радиус отбортовки R ≥ 2,5S.
Рисунок 5 – Отбортованный и переходный элементы
Таблица 2 – Длина цилиндрического борта
Толщина стенки S, мм | Длина цилиндрического борта l, мм, не менее |
---|---|
До 5 включ. | 15 |
Св. 5 до 10 включ. | 2S + 5 |
Св. 10 до 20 включ. | S + 15 |
Св. 20 до 150 включ. | S/2 + 25 |
Св. 150 | 100 |
4.3 Люки, лючки, бобышки и штуцера
4.3.1 Сосуды должны быть снабжены люками или смотровыми лючками, обеспечивающими осмотр, очистку, безопасность работ по защите от коррозии, монтаж и демонтаж разборных внутренних устройств, ремонт и контроль сосудов. Количество люков и лючков определяет разработчик сосуда. Люки и лючки необходимо располагать в доступных для пользования местах.
4.3.2 Сосуды с внутренним диаметром более 800 мм должны иметь люки.
Внутренний диаметр люка круглой формы у сосудов, устанавливаемых на открытом воздухе, должен быть не менее 450 мм, а у сосудов, располагаемых в помещении, – не менее 400 мм. Размер люков овальной формы по наименьшей и наибольшей осям должен быть не менее 325×400 мм.
Внутренний диаметр люка у сосудов, не имеющих корпусных фланцевых разъемов и подлежащих внутренней антикоррозионной защите неметаллическими материалами, должен быть не менее 800 мм.
Допускается проектировать без люков:
– сосуды, предназначенные для работы с веществами 1-го и 2-го классов опасности по ГОСТ 12.1.007, не вызывающими коррозии и накипи, независимо от их диаметра, при этом следует предусмотреть необходимое количество смотровых лючков;
– сосуды с приварными рубашками и кожухотрубчатые теплообменные аппараты независимо от их диаметра;
– сосуды, имеющие съемные днища или крышки, а также обеспечивающие возможность проведения внутреннего осмотра без демонтажа трубопровода горловины или штуцера.
4.3.3 Сосуды с внутренним диаметром не более 800 мм должны иметь круглый или овальный лючок. Размер лючка по наименьшей оси должен быть не менее 80 мм.
4.3.4 Каждый сосуд должен иметь бобышки или штуцера для наполнения водой и слива, удаления воздуха при гидравлическом испытании. Для этой цели допускается использовать технологические бобышки и штуцера.
Штуцера и бобышки на вертикальных сосудах должны быть расположены с учетом возможности проведения гидравлического испытания как в вертикальном, так и в горизонтальном положениях.
4.3.5 Для крышек люков массой более 20 кг должны быть предусмотрены приспособления для облегчения их открывания и закрывания.
4.3.6 Шарнирно-откидные или вставные болты, закладываемые в прорези, хомуты и другие зажимные приспособления люков, крышек и фланцев должны быть предохранены от сдвига или ослабления.
4.4 Расположение отверстий
4.4.1 Расположение отверстий в эллиптических и полусферических днищах не регламентируется.
Расположение отверстий на торосферических днищах допускается в пределах центрального сферического сегмента. При этом расстояние от наружной кромки отверстия до центра днища, измеряемое по хорде, должно быть не более 0,4 наружного диаметра днища.
4.4.2 Отверстия для люков, лючков и штуцеров в сосудах 1-й, 2-й, 3-й, 4-й групп должны быть расположены, как правило, вне сварных швов.
Расположение отверстий допускается:
– на продольных швах цилиндрических и конических обечаек сосудов, если диаметр отверстий не более 150 мм;
– кольцевых швах цилиндрических и конических обечаек сосудов без ограничения диаметра отверстий;
– швах выпуклых днищ без ограничения диаметра отверстий при условии 100-процентной проверки сварных швов днищ радиографическим или ультразвуковым методом;
– швах плоских днищ.
4.4.3 Отверстия не разрешается располагать в местах пересечения сварных швов сосудов 1-й, 2-й, 3-й, 4-й групп.
Данное требование не распространяется на случай, оговоренный в 4.2.3.
4.4.4 Отверстия для люков, лючков, штуцеров в сосудах 5-й группы разрешается устанавливать на сварных швах без ограничения по диаметру.
4.5 Требования к опорам
4.5.1 Опоры из углеродистых сталей допускается применять для сосудов из коррозионно-стойких сталей при условии, что к сосуду приваривается переходная обечайка опоры из коррозионно-стойкой стали высотой, определяемой расчетом, выполненным разработчиком сосуда.
4.5.2 Для горизонтальных сосудов угол охвата седловой опоры, как правило, должен быть не менее 120°.
4.5.3 При наличии температурных расширений в продольном направлении в горизонтальных сосудах следует выполнять неподвижной лишь одну седловую опору, остальные опоры – подвижными. Указание об этом должно содержаться в технической документации.
4.6 Требования к внутренним и наружным устройствам
4.6.1 Внутренние устройства в сосудах (змеевики, тарелки, перегородки и др.), препятствующие осмотру и ремонту, как правило, должны быть съемными.
При использовании приварных устройств следует выполнять требования 4.1.1.
4.6.2 Внутренние и наружные приварные устройства необходимо конструировать так, чтобы были обеспечены удаление воздуха и полное опорожнение аппарата при гидравлическом испытании в горизонтальном и вертикальном положениях.
4.6.3 Рубашки и змеевики, применяемые для наружного обогрева или охлаждения сосудов, могут быть съемными и приварными.
4.6.4 Все глухие части сборочных единиц и элементов внутренних устройств должны иметь дренажные отверстия для обеспечения полного слива (опорожнения) жидкости в случае остановки сосуда.
<< назад / к содержанию ГОСТа Р 52630-2012 / вперед >>
Источник