Сварка сосудов находящихся под давлением
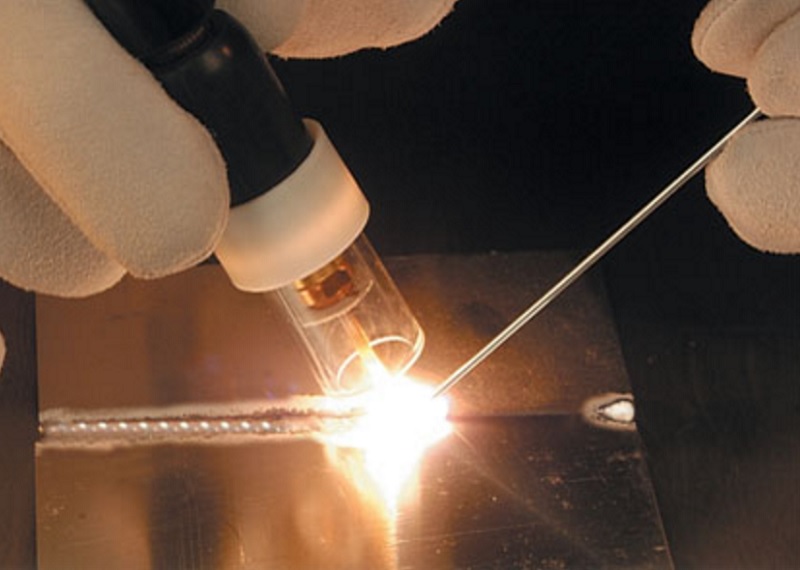
содержание .. 90 91 92 93 94 95 96 97 98 99 ..
4-4.
Сварка СОСУДОВ РАБОТАЮЩИХ ПОД ДАВЛЕНИЕМ
4-4-1. Сварка сосудов и их элементов должна производиться в соответствии с требованиями технических условий на изготовление сосудов и утвержденных в установленном порядке производственных инструкций; последнее должны быть разработаны с учетом специфики изготовляемых изделий.
Использование новых методов сварки разрешается главным инженером” предприятия после подтверждения ее технологичности на изделиях, проверки всего комплекса требуемых свойств сварных соединений и положительного заключения головной научно-исследовательской организации.
* 4-4-2. К сварке сосудов и их элементов допускаются сварщики, имеющие удостоверения установленного образца на право производства сварочных работ, выданные квалификационной комиссией в соответствии с Правилами аттестации сварщиков, утвержденными Госгортехнадзором СССР. При этом сварщики могут быть допущены только к тем видам работ, которые указаны в удостоверениях.
4-4-3. Перед допуском сварщика к выполнению сварочных работ, связанных с изготовлением сложных или специфичных сварных конструкций, предприятие обязано провести специальную подготовку и испытание сварщика, сделав об этом отметку в его удостоверении.
4-4-4. Перед началом сварки должно быть проверено качество сборки соединяемых элементов, а также состояние стыкуемых кромок и прилегающих к ним поверхностей. При сборке не допускается подгонка кромок, вызывающая дополнительные напряжения в металле.
4-4-5. Прихватки должны выполняться с применением присадочных материалов, предусмотренных техническими условиями для данного сосуда.
4-4-6. Недопустимые дефекты сварки, обнаруженные в процессе изготовления сварных сосудов и их элементов, должны быть устранены сваркой и подвергнуты повторному контролю .
4-4-7. Не допускается ведение сварочных работ по изготовлению сосудов и их элементов при температуре окружающего воздуха ниже 0° С.
При монтаже и ремонте сосудов допускается сварка при отрицательной температуре окружающего воздуха, если соблюдены требования, предусмотренные в нормалях, или технических условиях, или инструкциях по монтажу и ремонту сосудов.
4-4-8. При дожде, ветре и снегопаде сварочные работы по монтажу сосуда могут выполняться лишь при условии надлежащей защиты сварщика и места сварки.
* 4-4-9. Технология сварки сосудов должна быть детально разработана и предусматривать такой порядок выполнения работ, при котором внутренние напряжения в сварных соединениях будут минимальными.
4-5. Термическая обработка СОСУДОВ РАБОТАЮЩИХ ПОД ДАВЛЕНИЕМ
4-5-1. Термической обработке подлежат сосуды, в стенках которых в процессе изготовления (при вальцовке, штамповке, сварке и т. п.) возможно появление недопустимых напряжений а также сосуды, прочность которых достигается термообработкой.
Необходимость и режимы термообработки устанавливаются техническими условиями на изготовление изделия.
4-5-2. Допускается термическая обработка сосуда по частям с последующей местной термообработкой замыкающего шва (швов). При местной термообработке должны быть обеспечены равномерный нагрев и охлаждение по всей длине шва и примыкающей к нему зоны основного металла на ширину, в 2-3 раза превышающую ширину шва.
содержание .. 90 91 92 93 94 95 96 97 98 99 ..
Источник
В этой статье мы разберемся что такое плазменная сварка сосудов и проведем ее сравнение с популярной TIG-сваркой. Для начала обратимся к истокам. Львиную долю продукции предприятий химического машиностроения и производителей оборудования для пищевой промышленности в том или ином виде составляют сосуды, работающие под давлением. К материалам, используемых для производства данных конструкций, часто предъявляются повышенные требования к коррозионной стойкости, часто при наличии агрессивных сред. В то же время вещества, что находятся в подобных сосудах, могут иметь рабочий диапазон температур от 200 до 600 °С.
Подбор подходящей стали
Исходя из таких требований, наиболее оптимальным является применение в качестве основного материала сосуда коррозионостойких хромоникелевых сталей аустенитного класса. На постсоветском пространстве наиболее распространенной маркой стали является 12Х18Н10Т, которая в западных странах более известна как AISI 304.
Сварка сталей аустенитного класса, как известно, может быть связана с определенными трудностями: при использовании неподходящей схемы нагрева способа сварки, возможно образование холодных (кристаллизационных) трещин. Также большой проблемой может быть выгорание легирующих элементов (хрома и никеля), что приводит к снижению коррозионной стойкости. Если срок эксплуатации конструкции более 20 лет, то выгорание легирующих элементов может привести к межкристаллитной коррозии через десятилетия после отгрузки с завода.
Требования к сварному шву
Исходя из всех вышеизложенных особенностей, способ сварки должен обеспечивать: высокие механические характеристики (как следствие, мелкозернистую структуру металла), отсутствие выгорания легирующих элементов. Также при изготовлении оборудования для пищевой отрасли есть специфические требования к геометрическим размерам сварного шва – обратный валик должен быть минимальным или отсутствовать. Это связано с тем, что процесс сварки обычно производится с внешней стороны сосуда, и как следствие, обратный валик находится внутри сосуда. В случае, если валик имеет большую высоту, пищевые продукты в небольших количествах могут сосредотачиваться и задерживаться возле него. В последствии, при промывке этой емкости, пищевые продукты в данном месте почти не удаляются, и по окончании своего срока годности, могут испортить уже новые загружаемые продукты.
Именно для обеспечения этих требований используют TIG Cold Wire – способ сварки (сварка неплавящимся способом с подачей присадочной проволоки – ИНп). Сварка этим способом позволяет обеспечить сварному шву оптимальный обратный валик, способствует минимизации выгорания легирующих элементов. Также с присадочной проволокой возможно введение дополнительных элементов-аустенизаторов структуры стали. Но у способа есть и недостатки: скорость сварки в таком случае достаточно низкая: 150-300 мм/мин, а из-за «мягкости» режима (соотношения вложенной энергии в объем металла и времени ее воздействия на него) размер зерен становиться большим (т. н. «крупнозернистая» структура), что несколько снижает механические характеристики сварного шва.
Плазменная сварка сосудов
В последнее время большое распространение плазменная сварка – способ, в котором источником тепла для процесса является плазменная дуга. Она позволяет нивелировать вышеизложенные недостатки ИНп способа сварки.
Основной технологической особенностью плазменной сварки является феномен, названный впоследствии процессом сварки «в замочную скважину» (англ. Key hole welding). Весь феномен состоит в том, что во время сварки поток плазменной дуги изначально образует в свариваемой заготовке сквозное отверстие, вокруг которого находится расплавленный металл. При последующем перемещении плазменной дуги расплавленный метал, который находится позади нее, под действием различных сил смыкается и образовывает единую сварочную ванну.
Сильные стороны
Аппараты для плазменной сварки имеют ряд полезных свойств и особенностей:
1. Обеспечение полного проплавления заготовок до 8 мм без разделки кромок, за один проход:
а) Плазменная сварка стали 12Х18Н10Т толщиной 8 мм, один проход без разделки
б) TIG- сварка стали 12Х18Н10Т толщиной 8 мм, четыре прохода с разделкой:
- угол раскрытия кромок 60°, притупление 3 мм.
2. Наличие значительно меньших остаточных деформаций вследствие меньшего тепловложения в заготовку
3. Большая производительность сварки
4. Плазменная сварка сосудов обеспечивает более высокие механические характеристики соединений, так как образовывает более мелкозернистую структуру.
Источник
2.4.1. При сварке обечаек и труб, приварке днищ к обечайкам должны применяться стыковые швы с полным проплавлением.
Допускаются сварные соединения в тавр и угловые с полным проплавлением для приварки плоских днищ, плоских фланцев, трубных решеток, штуцеров, люков, рубашек.
Применение нахлесточных сварных швов допускается для приварки к корпусу укрепляющих колец, опорных элементов, подкладных листов, пластин под площадки, лестницы, кронштейны и т.п.
2.4.2. Конструктивный зазор в угловых и тавровых сварных соединениях допускается в случаях, предусмотренных НД, согласованной в установленном порядке.
2.4.3. Сварные швы должны быть доступны для контроля при изготовлении, монтаже и эксплуатации сосудов, предусмотренного требованиями Правил, соответствующих стандартов и технических условий.
2.4.4. Продольные швы смежных обечаек и швы днищ сосудов должны быть смещены относительно друг друга на величину трехкратной толщины наиболее толстого элемента, но не менее чем на 100 мм между осями швов.
Указанные швы допускается не смещать относительно друг друга в сосудах, предназначенных для работы под давлением не более 1,6 МПа (16 кгс/см2) и температуре стенки не выше 400 град. С, с номинальной толщиной стенки не более 30 мм при условии, что эти швы выполняются автоматической или электрошлаковой сваркой и места пересечения швов контролируются методом радиографии или ультразвуковой дефектоскопии в объеме 100%.
2.4.5. При приварке к корпусу сосуда внутренних и внешних устройств (опорных элементов, тарелок, рубашек, перегородок и др.) допускается пересечение этих сварных швов со стыковыми швами корпуса при условии предварительной проверки перекрываемого участка шва корпуса радиографическим контролем или ультразвуковой дефектоскопией.
2.4.6. В случае приварки опор или иных элементов к корпусу сосуда расстояние между краем сварного шва сосуда и краем шва приварки элемента должно быть не менее толщины стенки корпуса сосуда, но не менее 20 мм.
Для сосудов из углеродистых и низколегированных марганцовистых и марганцово-кремнистых сталей (приложение 3), подвергаемых после сварки термообработке, независимо от толщины стенки корпуса расстояние между краем сварного шва сосуда и краем шва приварки элемента должно быть не менее 20 мм.
2.4.7. В горизонтальных сосудах допускается местное перекрытие седловыми опорами кольцевых (поперечных) сварных швов на общей длине не более 0,35 пиD, а при наличии подкладного листа – не более 0,5 пиD, где D – наружный диаметр сосуда. При этом перекрываемые участки сварных швов по всей длине должны быть проверены методом радиографии или ультразвуковой дефектоскопии. Перекрытие мест пересечения швов не допускается.
2.4.8. В стыковых сварных соединениях элементов сосудов с разной толщиной стенок должен быть обеспечен плавный переход от одного элемента к другому путем постепенного утонения кромки более толстого элемента. Угол наклона поверхностей перехода не должен превышать 20 град.
Если разница в толщине соединяемых элементов составляет не более 30% толщины тонкого элемента и не превышает 5 мм, то допускается применение сварных швов без предварительного утонения толстого элемента. Форма швов должна обеспечивать плавный переход от толстого элемента к тонкому.
При стыковке литой детали с деталями из труб, проката или поковок необходимо учитывать, что номинальная расчетная толщина литой детали на 25 – 40% больше аналогичной расчетной толщины стенки элемента из труб, проката или поковок, поэтому переход от толстого элемента к тонкому должен быть выполнен таким образом, чтобы толщина конца литой детали была не менее расчетной величины.
Источник