Термообработка сосудов и аппаратов
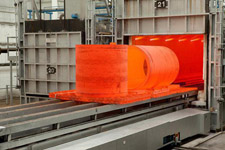
Версия для печати
09 Ноября 2017 г.
Наши заказчики часто спрашивают нас, какие есть способы продления срока службы резервуаров различного назначения, используемых как с нейтральными рабочими средами, так и с агрессивными на химических и нефтяных предприятиях.
Все производимые на Заводе изделия имеют стандартные сроки службы от 10 до 20 лет в зависимости от стали, из которой изготовлена емкость, и условий эксплуатации (температурный режим, давление, свойства рабочей среды и т.д.).
Увеличить срок эксплуатации оборудования позволяет соблюдение правил эксплуатации, проведение регулярных технических обслуживаний и осмотров.
С нашей стороны мы предлагаем термообработку емкостей и сосудов различного назначения. Например, типовые подземные резервуары имеют пятилетний срок службы. Но если их подвергнуть термообработке, срок службы увеличивается до 20-30 лет.
Что же это такое – термическая обработка резервуаров? Для чего она нужна?
Термообработка – это нагрев и охлаждение металла и сплавов для увеличения прочности, жесткости, твердости и износостойкости изделий в тяжелых эксплуатационных условиях. Применяемые для производства резервуаров марки стали зачастую не обладают необходимыми характеристиками, например, для хранения агрессивных жидкостей, щелочей и кислот. Изменить химический состав уже поставленного на Завод листового металлопроката невозможно. Зато можно улучшить качественные показатели, скорректировать и добиться нужных механических и физических характеристик при помощи термической обработки. За счет этого убирается внутреннее напряжение металлов и различных сплавов.
Применение различных режимов термообработки позволяет получать на выходе металлоконструкции, обладающие различными механическими свойствами в зависимости от условий их дальнейшей эксплуатации. Благодаря различной температуре нагрева, его продолжительности и последующего охлаждения достигаются такие параметры, которые необходимы Заказчику.
Термообработке подвергается как непосредственно весь корпус целиком, стенки и днища, так и сварные соединения (локально), так как именно в сварных швах происходит максимальное изменение структуры металла.
Режимы термообработки сталей и сплавов
С разными металлами и сплавами и для придания им необходимых свойств в промышленности используются различные режимы: отжиг, закалка, отпуск и нормализация.
В процессе отжига осуществляется нагрев изделия при температуре до +900°С в течение до 2-х часов и последовательное его медленное охлаждение на разных скоростях в промышленных печах.
Процесс закалки заключается в нагреве выше критической температуры того металла, из которого сделано изделие. Максимальная температура закалки – +1300°С. Металлоконструкции выдерживаются при критической температуре, а затем резко охлаждаются в печи.
В результате закалки структура закаленной стали получается неравновесной, поэтому по окончании закалки проводится отпуск, характеризующийся нагревом до +650°С и последующим его медленным охлаждением. Отпуск приводит к снижению остаточных напряжений, повышению вязкости стали, уменьшению ее твердости и хрупкости.
Процесс охлаждения стали на воздухе после отжига называется нормализацией.
Виды термообработки резервуаров: печная и внепечная термическая обработка
Оба вида позволяют достичь одинаковые цели и отличаются лишь способом проведения.
Так, печная термическая обработка осуществляется в заводских условиях, где имеются промышленные печи (вакуумные, шахтные, дуговые, камерные, с выкатным поддоном и др.) и теплогенераторные агрегаты большого объема, внутрь которых помещается готовое изделие. Способ нагрева может быть разным в зависимости от источника тепла. Так, наиболее распространенными являются газовые и электрические печи. Газовые печи позволяют обрабатывать металлоконструкции размерами до 4000х4000х14 000 мм. В электропечах проводится термообработка деталей размерами до 4000х850х4000 мм.
Внепечная термообработка – это так называемая “выездная” услуга и проводится на месте эксплуатации оборудования. В процессе такого способа осуществляется нагрев внутреннего объема сосуда за счет подачи внутрь емкости продуктов сгорания топлива, сжигаемого в специальных теплогенерирующих устройствах. Также существуют электрические теплогенерирующие устройства, в которых тепловая энергия образуется из электрической.
Для уменьшения теплопотерь через корпус термообрабатываемого изделия, оно теплоизолируется с внутренней стороны (печная термообработка) или с внешней (внепечная термообработка). Теплоизоляция выполняется из специальных материалов, выдерживающих температуру до +1300°С.
Криогенная обработка металлоконструкций
Данный вид воздействия на металл является перспективным направлением в металлургии и машиностроении.
Получение необходимых показателей сталей и сплавов при криогенной обработке достигается за счет низкотемпературного воздействия путем охлаждения изделий до температуры жидкого азота (-196°С) и их выдержкой в течение 24-36 часов.
В результате криообработки емкостей повышается их коррозионная, эрозионная и абразивная износостойкость, а также улучшаются механические свойства материала.
Результаты термической обработки резервуаров и емкостей
Таким образом, термообработка изготавливаемых на нашем Заводе резервуаров и емкостей:
- улучшает эксплуатационные и механические показатели поставляемых металлоконструкций
- снижает вероятность хрупкого разрушения сосудов в результате остаточной деформации металла и изменения структуры металла в местах выполнения сварных монтажных швов
- увеличивает межремонтный цикл резервуаров и емкостей
- уменьшает массу готовых изделий
- повышает надежность и долговечность эксплуатации оборудования
- повышает сопротивляемость металлоконструкций химическому и механическому воздействию
Для получения подробной информации о способах печной и внепечной термообработки, а также преимуществах термически обработанных резервуаров и емкостей, звоните на Завод по телефонам:
- 8-800-555-9480
- 8(8452)250-288 (для Саратова и области).
Источник
Версия для печати
5.1 Общие требования
5.1.1 Требования к основным материалам, их пределы применения, назначение, условия применения, виды испытаний должны удовлетворять требованиям приложений А – Л.
Допускается применение импортных материалов, если их применение предусмотрено международными стандартами на сосуды, работающие под давлением (ASME, EN 13445).
5.1.2 Качество и характеристики материалов должны быть подтверждены предприятием-поставщиком в соответствующих сертификатах.
Сертификаты на материалы должны храниться на предприятии – изготовителе сосудов.
5.1.3 При отсутствии сопроводительных сертификатов на материалы или данных об отдельных видах испытаний должны быть проведены испытания на предприятии – изготовителе сосуда в соответствии с требованиями настоящего стандарта, стандартов или технических условий на эти материалы.
5.1.4 При выборе материалов для изготовления сосудов (сборочных единиц, деталей) следует учитывать расчетное давление, температуру стенки (максимальную и минимальную), химический состав и характер среды, технологические свойства и коррозионную стойкость материалов.
Для сосудов, устанавливаемых на открытой площадке или в неотапливаемом помещении, минимальную температуру стенки сосуда принимают равной:
– абсолютной минимальной температуре окружающего воздуха данного района (СНиП 23-01 [1]), если температура стенки сосуда, находящегося под расчетным (рабочим) давлением, может принять температуру наружного воздуха;
– температуре t2, указанной в таблице М.2 приложения М, если температура стенки сосуда, находящегося под расчетным (рабочим) давлением, не может принять температуру наружного воздуха. При этом пуск, остановка и испытания на герметичность выполняются в соответствии с «Регламентом проведения в зимнее время пуска (остановки) или испытания на герметичность сосудов» (см. приложение М), если нет других указаний в технической документации.
Материал опорных элементов принимают по средней температуре наиболее холодной пятидневке данного района с обеспеченностью 0,92 (СНиП 23-01 [1]).
5.1.5 Элементы, привариваемые непосредственно к корпусу сосуда изнутри или снаружи (лапы, цилиндрические опоры, подкладки под фирменные пластинки, опорные кольца под тарелки и др.), следует изготовлять из материалов того же структурного класса, что и корпус, если в технической документации на сосуд нет соответствующего обоснования применения материалов разных структурных классов.
5.1.6 Углеродистую кипящую сталь не применяют в сосудах, предназначенных для работы со взрыво- и пожароопасными веществами, вредными веществами 1-го и 2-го классов опасности по ГОСТ 12.1.005, ГОСТ 12.1.007 и средами, вызывающими коррозионное растрескивание (растворы едкого калия и натрия, азотнокислого калия, натрия, аммония и кальция, этаноламина, азотной кислоты, жидкий аммиак при содержании влаги менее 0,2 % и др.) или сероводородное растрескивание и расслоение.
5.1.7 Коррозионно-стойкие стали (лист, трубы, сварочные материалы, поковки, отливки и штампованные детали) при наличии требований должны быть проверены на стойкость против межкристаллитной коррозии по ГОСТ 6032.
5.1.8 Допускается снижение нижнего температурного предела применения листового и сортового проката, труб и поковок не более чем на 20 °С (но не ниже минус 70 °С), если:
– при расчете на прочность допускаемые напряжения уменьшены не менее чем в 1,35 раза и проводится термообработка сосуда;
– при расчете на прочность допускаемые напряжения уменьшены не менее чем в 2,85 раза без проведения термообработки сосуда.
5.2 Листовая сталь
5.2.1 Содержание серы и фосфора в углеродистых и низколегированных сталях по ГОСТ 5520 и ГОСТ 19281 должно быть не более 0,035 % каждого элемента.
5.2.2 Для проката по ГОСТ 5520, ГОСТ 14637, ГОСТ 19281 допускается переводить сталь из одной категории в другую при условии проведения необходимых дополнительных испытаний в соответствии с требованиями указанных стандартов.
5.2.3 Коррозионно-стойкая, жаростойкая и жаропрочная толстолистовая сталь по ГОСТ 7350 должна быть термически обработанной, травленой, с качеством поверхности по группе М2б. По указанию разработчика сосуда должны быть оговорены требования по содержанию α-фазы.
5.2.4 Листовая сталь, за исключением сталей аустенитного класса, толщиной листа более 30 мм, предназначенная для сосудов, работающих под давлением, должна быть полистно проконтролирована на сплошность ультразвуковым или другим равноценным методом. Методы контроля должны соответствовать ГОСТ 22727, нормы контроля – 1-му классу по ГОСТ 22727.
5.2.5 Листы из двухслойных сталей, предназначенные для сосудов, работающих под давлением, следует контролировать ультразвуковым методом на сплошность сцепления слоев полистно. Нормы контроля – по 1-му классу сплошности по ГОСТ 10885.
5.3 Трубы
5.3.1 При заказе труб по ГОСТ 9940 необходимо оговаривать требования по очистке от окалины и термообработке труб.
5.3.2 Трубы, закрепляемые в сосудах методом развальцовки, следует испытывать на раздачу, в остальных случаях – на загиб или сплющивание в соответствии со стандартами на трубы.
5.3.3 Допускается применять бесшовные трубы без проведения гидравлического испытания на предприятии – изготовителе труб в случае, если труба подвергается по всей поверхности контролю физическими методами (ультразвуковым или равноценным).
5.4 Поковки
5.4.1 Каждая поковка из углеродистой, низколегированной и легированной сталей, предназначенная для работы под номинальным давлением более 6,3 МПа и имеющая один из габаритных размеров (диаметр) более 200 мм и/или толщину более 50 мм, должна быть проконтролирована ультразвуковым или другим равноценным методом. Поковки из аустенитных и аустенитно-ферритных высоколегированных сталей, работающие под давлением более указанного условного давления, следует подвергать неразрушающему контролю при наличии этого требования.
Контролю ультразвуковым или другим равноценным методом следует подвергать не менее 50 % объема поковки.
Методика контроля и оценка качества должны соответствовать требованиям нормативных документов (НД).
5.4.2 Каждая поковка для плоских днищ, кроме поковок из высоколегированных сталей, должна быть проконтролирована ультразвуковым методом в зоне А в направлении Z (см. рисунок 4) по всей площади.
5.5 Стальные отливки
5.5.1 Стальные отливки следует применять в термообработанном состоянии с проверкой механических свойств после термической обработки.
5.5.2 Отливки из легированных и коррозионно-стойких сталей подвергают контролю макро- и микроструктуры и испытанию на межкристаллитную коррозию при наличии требований в технических условиях.
5.5.3 Каждую полую отливку, работающую при давлении свыше 0,07 МПа, подвергают гидравлическому испытанию пробным давлением, указанным в технических условиях и ГОСТ 356.
Испытание отливок, прошедших на предприятии-изготовителе 100-процентный контроль неразрушающими методами, допускается совмещать с испытанием собранного узла или сосуда пробным давлением, установленным для узла или сосуда.
5.6 Крепежные детали
5.6.1 Требования к материалам, виды их испытаний, пределы применения, назначение и условия применения должны удовлетворять требованиям приложения Ж.
5.6.2 Материалы шпилек и болтов следует выбирать с коэффициентом линейного расширения, близким по значению коэффициенту линейного расширения материала фланца. При этом разница в значениях коэффициентов линейного расширения не должна превышать 10 %. Возможность применения материалов шпилек (болтов) и фланцев с коэффициентами линейного расширения, значения которых отличаются между собой более чем на 10 %, должна быть подтверждена расчетом на прочность.
5.6.3 Для шпилек (болтов) из аустенитных сталей допускается применять гайки из сталей других структурных классов.
5.6.4 Твердость гаек должна быть ниже твердости шпилек (болтов) не менее чем на 15 НВ.
5.6.5 Допускается применять крепежные детали из сталей марок 30Х, 35Х, 38ХА, 40Х, 30ХМА, 35ХМ, 25Х1МФ, 25Х2М1Ф, 20Х1М1ФТР, 20Х1М1Ф1БР, 18X12ВМБФР, 37X12Н8Г8МФБ для соединений при температуре минус 60 °С при условии проведения испытаний на ударную вязкость на образцах типа 11 по ГОСТ 9454. Значение ударной вязкости при температуре минус 60 °С должно быть не ниже 30 Дж/см2.
5.7 Сварочные и наплавочные материалы
Для сварки и наплавки следует применять сварочные и наплавочные материалы в соответствии с НТД, утвержденной в установленном порядке.
<< назад / к содержанию ГОСТа Р 52630-2012 / вперед >>
Источник