В каких сосудах не применяется кипящая углеродистая сталь
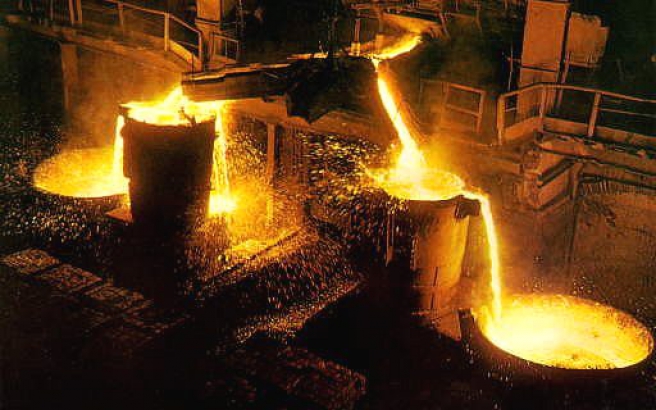
Кипящей называют малораскисленную сталь, интенсивно выделяющую газы в изложнице во время застывания. Образующиеся газы: до 90% CO, углекислый газ, азот, водород, метан. Сильные раскислители типа алюминия и титана в производстве такого металла не применяются.
Структура слитка малораскисленного металла
Основной признак слитка кипящей стали – отсутствие сосредоточенной усадочной раковины. Структура слитка зависит от интенсивности и периода кипения расплава. В затвердевшем состоянии он имеет 5 зон:
- наружная плотная корка;
- скопление сотовых пузырей, имеющих вытянутую форму;
- промежуточная зона между сотовыми и вторичными пузырями;
- скопление глубинных (вторичных) воздушных пузырей;
- сердцевина слитка – зона глубинных пузырей.
В качественных слитках наружная корка настолько плотная и толстая, что при нагреве и прокатке скопление сотовых пузырей не вскрывается.
«Закупоренная» – разновидность кипящей стали
По степени подавления выделения газов при затвердевании расплава материал находится между кипящей и полуспокойной сталями. Отличие этой технологии – закрывание слитка сверху после разливки механическим или химическим способом.
- При механическом закупоривании слиток закрывается тяжелой чугунной крышкой.
- Химическое закупоривание реализуется с помощью добавления сверху изложницы присадок алюминия или ферросилиция. Это приводит к ускоренному твердению верхней части слитка, которая отрезается и отправляется в отходы.
Такая методика позволяет уменьшить время выделения газов и снизить количество воздушных пузырей внутри слитка.
Основные характеристики
Кипящие стали отличаются неоднородностью структуры и химического состава, что приводит к снижению некоторых эксплуатационных характеристик. Прочность металла снижается из-за завариваемых при прокатке воздушных пузырей, которые при вальцовке или штамповке могут привести к расслоению материала.
Свойства кипящей стали
- Проблемная свариваемость из-за резко выраженной неравномерности по толщине изделия расположения фосфора и серы, негативно влияющих на свойства металла. Зоны с повышенным содержанием серы становятся причиной появления кристаллизационных трещин в шве и около него.
- Металл склонен к старению в зоне около сварного шва, что приводит к его охрупчиванию при отрицательных температурах.
- Более высокая подверженность коррозии, по сравнению со спокойными и полуспокойными сталями.
Области применения кипящей стали
Эта металлопродукция имеет определенные ограничения по сферам использования. Она не допускается для изготовления:
- крепежных элементов котлов, работающих под давлением;
- конструкций и оборудования, запланированных для эксплуатации при температурах ниже -20°C
- аппаратов, эксплуатируемых при динамических, знакопеременных, пульсирующих нагрузках;
- оборудования и конструкций, контактирующих с агрессивными, взрыво- и пожароопасными средами, сжатыми и сжиженными газами.
Из слитков кипящей стали производят полосы, листы, тонкие плиты, проволоку, прутки, штрипсы, трубы, предназначенные для изготовления продукции рядового назначения.
Какие марки углеродистых сталей могут относится к кипящим?
Для изготовления сплава этого вида используются:
- углеродистые стали обыкновенного качества – кипящие сплавы изготавливаются по ГОСТу380-2005, обозначение – «кп»;
- качественные и высококачественные стали – регламентируются ГОСТом 1050-88, буквенное обозначение – «кп».
В производстве обычно применяются стали с содержанием углерода более 0,15%.
Источник
Ранее мы рассматривали структуру стали (система железо-углерод), деформацию и разрушение металлов, влияние на ее свойства различных примесей и т.д.
В данной публикации будем рассматривать виды стали по степени раскисления.
Итак, сталь это сплав Fe + C, ( С – не более 2%)+ другие элементы. Сталь подразделяют на углеродистую и легированную учитывая хим.состав, и исходя из применения на-конструкционные и инструментальные. Изготавливают и специальные стали со специфическими характеристиками для использования в агрессивных средах, к таким сталям относят жаро-, коррозионно-, кислото-стойкую стали.
Качество стали определяется по способу производства и количеству плохих примесей и подразделяются на рядовые, качественные, повышенного и высокого качества.
Химический состав сталей обыкновенного качества
Существует типизация по характеру застывания в изложнице и геометрической форме слитка (форма изложницы). Выделяют спокойную, полуспокойную и кипящую.
Углеродистая сталь
Углеродистая сталь выплавляется без добавления каких-либо легирующих элементов и бывает обычной и качественной.
Стали обычного качества принято делить на следующие группы:
- группа А – обеспечивается по механическим свойствам. Изделия из сталей этой группы применяются для последующей сварки, ковки и т.д. Причем, заявляемые мех. свойства могут изменяться. (Ст3, Ст5кп.).
- группа Б – сталь обеспечивается по хим. составу. Применяется для изготовления деталей, при обработке которых, могут изменяться механические характеристики определяемые составом.
Сталь из группы Б подразделяется на 2 категории:
- 1я- установлено содержание С, Si, Mn; ограничено содержание: S, P, N, As,
- 2я – дополнительно ограничено количесво Cr, Ni, Cu.
- группа В – обеспечивается по механическим характеристикам и содержанию химических элементов. Применяется при производстве свариваемых деталей.
Подразделяется на шесть категорий.
Обозначается группа В следующим образом: марка стали, степень раскисления, номер категории. Имеют одинаковый состав со сталью 2 категории группы Б.
Маркировка стали
Рассматривая, на примере, маркировку стали Ст5пс (конструкционная углеродистая сталь обычного качества).
Определяем, что:
- эта сталь относится к группе А, (поскольку категория указывается перед буквами Ст (ВСт1, ВСт2), а не указывается только группа А).
- цифра 5 – определяет условный номер марки исходя из хим. состава и мех.свойств.
- пс- степень раскисления.
Если после цифры определяющей марку стали стоит буква Г- значит сталь содержит повешенное количество марганца.(Ст25Г2С)
Степени раскисления стали
Существует 3 степени раскисления стали.
Процесс раскисления позволяет восстановить окись железа и связать растворенный кислород, уменьшив, таким образом, его вредное влияние.
Кипящая сталь
Кипящая сталь является не полностью раскисленой. Во время разливки в изложницы она кипит из-за обильного выделения газа, поэтому она является наиболее загрязнена газами и неоднородной. Т.е механические свойства по слитку могут отличаться, поскольку распределение химических элементов по слитку не равномерно. В головной части слитка находится наибольшее количество углерода и различных плохих примесей (таких , как сера или фосфор), из-за чего требуется удаление части слитка ( 5% от общей массы).
Скопление серы в определенных участках может послужить причиной появления кристаллизационной трещины по шву. На этих участках сталь менее устойчива к старению и является наиболее хрупкой в минусовые температуры. Содержание кремния в кипящей стали не превышает 0,07%.
Итак, о кипящей стали можно сказать, что она довольно хрупкая, имеет плохие показатели свариваемости и наиболее подвержена коррозии. Поэтому, с целью повышения характеристик стали её раскисляют кремнием (0,12-0,3%), алюминием (до 0,1%) или марганцем, (возможно раскисление и прочими химическими элементами динамично вступающими в реакцию с кислородом). Кипящая сталь – довольно хрупкая, имеет плохие показатели свариваемости и наиболее подвержена коррозии.
Процесс раскисления позволяет восстановить окись железа и связать растворенный кислород, уменьшить его вредное влияние, поддерживая при этом долгое время высокую температуру стали, что способствует максимальному газо и шлакоудалению, а так же, получению микрозернистой структуры, благодаря образованию участков кристаллизации. За счет образование этих очагов происходит улучшение качества стали.
Ликвацией называется образование неоднородной химической структуры стали, возникающая в момент кристаллизации. Различаю две разновидности ликвации: внутрикристаллическую и дендритную. Впервые данное явление обнаружено русскими металлургами Н. В. Калакуцким и А. С. Лавровым в 1866 году.
Спокойная сталь
Полученная в результате раскисления сталь называется спокойной. Содержание кремния в спокойной стали не менее 0,12%, а наличие неметаллических включений и шлаков минимально.
Слитки спокойных сталей имеют плотную однородную структуру, а соответственно и улучшенные показатели по механическим свойствам.
Спокойная сталь отлично подходит для сваривания, а также обладает лучшей сопротивляемостью к ударным нагрузкам. Является более однородной.
Она подходит для возведении опорных металлоконструкции (благодаря ее стойкости к хрупкому разрушению), которые подвергаются сильным нагрузкам.
Спокойная сталь отлично подходит для сваривания, а также имеет лучшее сопротивление ударным нагрузкам и более однородна.
Полуспокойная сталь
Промежуточной по качественным показателям – является полуспокойная сталь.
Она является полураскисленной и кристаллизуется без кипения, выделяя при этом достаточное количество газа и имеет меньшее количество пузырьков, чем кипящая сталь. Поэтому, полуспокойная сталь имеет средние показатели качества (максимально приближенные к спокойной), и иногда заменяет спокойную.
Стоимость полуспокойной стали немного ниже спокойной, а выход качественного проката из таких слитков на 8 – 10% лучше.
Показатели качества полуспокойной стали ближе к спокойной.
Полуспокойная сталь затвердевает без кипения, но с выделением большого количества газа. В таком слитке содержание пузырей меньше, чем кипящей, но больше, чем в спокойной.
Поскольку производство кипящей стали обходится дешевле, чем спокойной и полуспокойной она достаточно широко используется для изготовления наименее ответственных изделий металлопроката, таких , как катанка, полоса, уголок, метизы.
Источник
Таблица 3
Категории
сталей для сосудов в зависимости
от средней температуры воздуха наиболее
холодной пятидневки
Средняя температура воздуха наиболее холодной пятидневки, °С | Марка стали |
Не ниже минус 30 | Ст3пс3, Ст3сп3, Ст3Гпс3 |
15К-3, 16К-3, 18К-3, 20К-3 | |
От минус 31 до минус 40 | Ст3пс4, Ст3сп4, Ст3Гпс4 |
15К-5, 16К-5, 18К-5, 20К-5 | |
16ГС-3, 09Г2С-3, 10Г2С1-3 | |
От минус 41 до минус 60 | 09Г2С-8, 10Г2С1-8 |
3.1.4. Если при проверке категории стали на соответствие требованию табл. 3 окажется, что могут применяться различные категории стали, то следует применять сталь более высокой категории.
3.1.5. Пределы применения двухслойной стали определяются по основному слою.
3.1.6. Допускается применение сталей марок 09Г2С, 10Г2С1 с испытанием на ударный изгиб при средней температуре воздуха наиболее холодной пятидневки для заданного района установки сосуда.
3.1.7. Элементы, привариваемые непосредственно к корпусу сосуда изнутри или снаружи (лапы, цилиндрические опоры, подкладки под фирменные таблички, опорные кольца под тарелки и др.), следует изготавливать из материалов того же класса, что и корпус.
Допускается приварка к поверхности корпуса сосуда элементов из сталей других классов. Возможность применения таких элементов, их размеры (протяженность и толщина) обосновывается проектом.
Для приварных и неприварных внутренних элементов толщиной не более 10 мм для сосудов, работающих при температуре от минус 40 до 475 град. С допускается применять листовую сталь и сортовой прокат марок Ст3кп2 и Ст3пс2.
3.1.8. Для материалов опорных частей сосудов, кронштейнов для крепления навесного оборудования и других деталей наружных приварных элементов выполняются требования таблицы 3.
3.1.9. Углеродистая сталь кипящая не применяется:
в сосудах, предназначенных для сжиженных газов;
в сосудах, предназначенных для работы со взрыво- и пожароопасными веществами, вредными веществами 1-го и 2-го классов опасности и средами, вызывающими коррозионное растрескивание (растворы едкого калия и натрия, азотнокислого калия, натрия, аммония и кальция, этаноламина, азотной кислоты, аммиачная вода, жидкий аммиак при содержании влаги менее 0,2% и др.) или сероводородное растрескивание и расслоение.
3.1.10. Внутренние устройства толщиной не более 10 мм, соприкасающиеся со взрыво- и пожароопасными средами, допускается выполнять из кипящей стали.
3.1.11. Сталь марки Ст3пс категорий 3, 4, 5 толщиной более 12 мм до 25 мм допускается применять для сосудов объемом не более 50 м3, а толщиной 12 мм и менее – наравне со сталью Ст3сп соответствующей категории.
3.1.12. Коррозионно-стойкие стали (лист, трубы, сварочные материалы, поковки и штампованные детали) при наличии требований в проекте следует проверять на стойкость против межкристаллитной коррозии.
3.1.13. Применение материалов для изготовления сосудов, работающих с параметрами, выходящими за установленные пределы, а также применение нерегламентированных материалов допускается в установленном порядке и обосновывается в проекте.
3.1.14. При отсутствии сопроводительных документов на материалы или данных об отдельных видах испытаний необходимо провести испытания на предприятии – изготовителе сосуда в соответствии с требованиями стандартов или технических условий на эти материалы и требованиями настоящих Правил.
Результаты испытаний необходимо хранить в установленном порядке.
3.1.15. Допускается по согласованию в установленном порядке применение материалов по разным нормативно-техническим документам, если качество и свойства материалов по ним удовлетворяют установленным требованиям.
3.1.16. Дополнительные требования к материалам, не предусмотренные стандартами или техническими условиями, следует указывать в технической документации.
Источник
Все конструктивные элементы резервуаров и емкостей разделяются на 3 группы:
- А и Б – основные конструкции:
- Группа А: стенка, привариваемые к стенке листы днища или кольцевые окрайки, обечайки, фланцы и крышки (заглушки) люков и патрубков в стенке, привариваемые к стенке усиливающие или распределительные накладки, кольца жесткости, опорные кольца стационарных крыш.
- Группа Б1 – каркас стационарных крыш (включая фасонки), бескаркасные крыши;
- Группа Б2 – центральная часть днища, анкерные крепления, настил стационарных крыш, плавающие крыши и понтоны, обечайки, фланцы и крышки (заглушки) люков и патрубков в крыше.
- В – вспомогательные конструкции:
- Группа В: лестницы, площадки, ограждения, переходы (за исключением распределительных накладок, привариваемых к стенке).
В государственных стандартах, регламентирующих проектирование и изготовление вертикальных и горизонтальных емкостей, указывается возможность применения тех или иных марок сталей для основных и вспомогательных конструкций.
Для подбора конкретной марки стали для изготовления резервуаров, инженеры-проектировщики проводят необходимые расчеты и анализ условий эксплуатации. Так, основными параметрами для выбора определенной марки стали являются:
- расчетное давление;
- минимальная расчетная температура;
- максимальная расчетная температура;
- коррозионная активность рабочей среды.
Для сталей наиболее релевантными характеристиками являются:
- минимальный предел текучести – этим показателем называют напряжение, при котором начинает развиваться пластическая деформация. Предел текучести относится к характеристикам прочности и устанавливает границу между упругой и упруго-пластической зонами деформирования. Предел текучести металла измеряется в кг/мм2 или H/м2. На значение предела текучести металла влияют самые разные факторов, например: толщина образца, режим термообработки, наличие тех или иных примесей и легирующих элементов, микроструктура, тип и дефекты кристаллической решётки и др.
- расчетная температура металла – этот показатель принимают как наиболее минимальное значение из двух следующих значений:
- минимальная температура складируемого продукта;
- температура наиболее холодных суток для данной местности (минимальная среднесуточная температура), повышенная на 5 °С.
- ударная вязкость – способность металла в процессе деформации поглощать механическую энергию, величина которой ведёт к разрушениям. Испытание проводится до момента разрушения или разрыва опытного образца и выражается в кДж/м2 или в Дж/см2. Обозначают ударную вязкость металлов буквами КС. В конце есть ещё третий символ, который указывает на вид надреза: V – является острым, U – имеет радиус закругления, Т – трещина.
- коррозионная стойкость материала – способность материалов сопротивляться коррозионному воздействию внешней среды (особенно это важно в резервуарах);
- пластичность и др.
Для конструктивных элементов различных групп применяют различные стали:
- Группа А – основные конструкции – применяется только спокойная (полностью раскисленная) сталь. Полученная в результате раскисления сталь называется спокойной. Содержание кремния в спокойной стали не менее 0,12%, а наличие неметаллических включений и шлаков минимально. Слитки спокойных сталей имеют плотную однородную структуру, а соответственно и улучшенные показатели по механическим свойствам. Спокойная сталь отлично подходит для сваривания, а также обладает лучшей сопротивляемостью к ударным нагрузкам. Является более однородной. Она подходит для возведении опорных металлоконструкции (благодаря ее стойкости к хрупкому разрушению), которые подвергаются сильным нагрузкам.
- Группа Б – применяется спокойная или полуспокойная сталь. Промежуточной по качественным показателям – является полуспокойная сталь. Она является полураскисленной и кристаллизуется без кипения, выделяя при этом достаточное количество газа и имеет меньшее количество пузырьков, чем кипящая сталь. Поэтому, полуспокойная сталь имеет средние показатели качества (максимально приближенные к спокойной), и иногда заменяет спокойную. Стоимость полуспокойной стали немного ниже спокойной, а выход качественного проката из таких слитков на 8 – 10% лучше. Показатели качества полуспокойной стали ближе к спокойной.
- Группа В – наряду с вышеперечисленными сталями с учетом температурных условий эксплуатации допускается применение кипящей стали. Кипящая сталь является не полностью раскисленой. Во время разливки в изложницы она кипит из-за обильного выделения газа, поэтому она является наиболее загрязнена газами и неоднородной. Т.е механические свойства по слитку могут отличаться, поскольку распределение химических элементов по слитку не равномерно. Она довольно хрупкая, имеет плохие показатели свариваемости и наиболее подвержена коррозии.
Исходя из нормативной базы по производству резервуаров и емкостей, можно привести следующие итоги:
- горизонтальные резервуары (по ГОСТ 17032-2010) должны изготавливаться из углеродистой полностью раскисленной стали (основные металлоконструкции) и углеродистой полуспокойной или кипящей стали (вспомогательные конструкции)
- вертикальные резервуары (по ГОСТ 31385-2008 и СТО 0048-2005) должны изготавливаться из спокойных низкоуглеродистых и низколегированных сталей, для вспомогательных конструкций возможно применение полуспокойных и кипящих сталей
- сосуды и аппараты (по ГОСТ 52630-2012) могут изготавливаться из углеродистых сталей, коррозионно-стойких и низколегированные, жаростойких и жаропрочных толстолистовой стали
Таблица показывает какие марки стали наиболее часто используются при производстве резервуаров и емкостей
МАРКИРОВКА | РАСШИФРОВКА |
---|---|
Ст3сп | конструкционная углеродистая обыкновенного качества сталь |
09Г2С | конструкционная низколегированная сталь |
08Х13 | сталь коррозионностойкая и жаростойкая ферритного класса. |
10Х17Н13М2Т | сталь коррозионностойкая аустенитного класса |
12Х18Н9 | сталь коррозионностойкая и жаростойкая аустенитного класса |
08Х18Н10 | сталь коррозионностойкая, жаропрочная, аустенитного класса |
12Х18Н9Т | сталь коррозионностойкая аустенитная класса |
08Х18Н10Т | сталь коррозионностойкая и жаростойкая аустенитного класса |
12Х18Н12Т | сталь коррозионностойкая, жаростойкая и жаропрочная аустенитного класса |
08Х18Г8Н2Т | сталь коррозионностойкая аустенитно-ферритного класса |
08Х22Н6Т | сталь коррозионностойкая аустенитно-ферритного класса |
ВСт3сп | сталь конструкционная |
10Х14Г14Н4Т | сталь конструкционная криогенная аустенитного класса |
Для производства резервуаров и емкостей заводы по изготовлению резервуаров используют металлопрокат, отвечающий требованиям государственных стандартов в зависимости от марки стали:
- ГОСТ 380-2005 «Сталь углеродистая обыкновенного качества. Марки»
- ГОСТ 1050-2013 «Металлопродукция из нелегированных конструкционных качественных и специальных сталей. Общие технические условия»
- ГОСТ 4543-71 «Прокат из легированной конструкционной стали. Технические условия»
- ГОСТ 27772-88 «Прокат для строительных стальных конструкций. Общие технические условия»
- ГОСТ 5520-79 «Прокат листовой из углеродистой, низколегированной и легированной стали для котлов и сосудов, работающих под давлением. Технические условия»
- ГОСТ 19281-2014 «Прокат повышенной прочности. Общие технические условия»
- ГОСТ 14637-89 «Прокат толстолистовой из углеродистой стали обыкновенного качества. Технические условия»
- ГОСТ 7350-77 «Сталь толстолистовая коррозионно-стойкая, жаростойкая и жаропрочная. Технические условия»
- ГОСТ 535-2005 «Прокат сортовой и фасонный из стали углеродистой обыкновенного качества. Общие технические условия»
- ГОСТ 10885-85 «Сталь листовая горячекатаная двухслойная коррозионно-стойкая. Технические условия»
Помимо марок стали для резервуаров стоит уделить внимание и листовому прокату, который используется для производства
- Листовой прокат, применяемый для изготовления конструкций резервуаров, должен соответствовать по форме, размерам и предельным отклонениям ГОСТ 19903, если иное не указано в проекте КМ.
- Листовой прокат поставляется толщиной от 4 мм до 60 мм, шириной от 1500 мм до 3000 мм, длиной от 6000 мм до 12000 мм с обрезными кромками.
- Толщина листового проката для изготовления стенок резервуаров не должна превышать 40 мм.
- По точности изготовления листовой прокат должен соответствовать:
- по толщине (предельный минусовой допуск на прокат) – в соответствии с таблицей 7.2 или с постоянным предельным нижнем отклонением равным 0,3 мм;
- по плоскостности – особо высокой или высокой.
- Серповидность листов должна быть пониженной и на базе 1 м не должна превышать 2 мм.
- Листовой прокат для изготовления конструкций группы А резервуаров 1 и 2 классов опасности должен иметь класс сплошности соответственно 0 и 1 по ГОСТ 22727. Неконтролируемые зоны не должны превышать: у продольной кромки – 5 мм, у поперечной – 10 мм.
Источник