Виды контроля сварных соединений сосуда
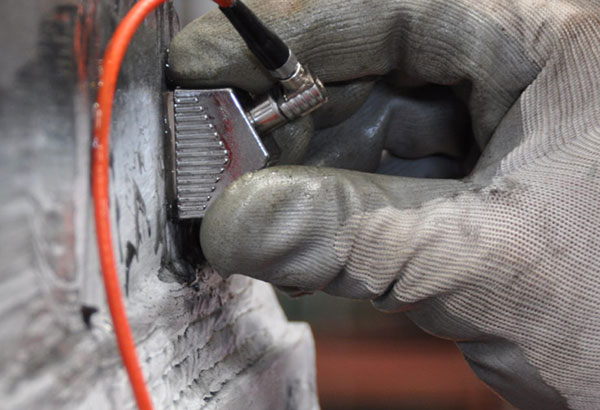
Среди обязательных этапов любых сварочных работ находится проверка качества швов. Благодаря такому подходу, специалист может выявить недоработки, которые негативно сказываются на прочности соединения. Своевременное устранение производственных дефектов позволяет продлить срок службы конструкции. Как проверить качество сварного шва? Конечно, это можно оценить визуально. Но это далеко не точный и не единственно доступный метод контроля.
Ни один специалист, даже самый опытный, визуально не сможет определить наличие пустот и трещин внутреннего характера. Здесь необходим совершенно иной подход. На больших предприятиях качество мониторится контроллером сварочных работ. А во всех остальных случаях ответственность ложится на плечи самого исполнителя. Далее мы рассмотрим разные существующие варианты проверки швов, помимо визуального контроля.
Методы контроля качества сварных швов
На практике применяются разные средства технического контроля, которые отличаются нюансами в работе; обладают разными достоинствами и недостатками. Тем не менее, весь их функционал ориентирован на то, чтобы определить прочность и долговечность сварочного шва. Качество соединения двух металлических заготовок можно предсказать. Ведь в большей части оно зависит от мастерства исполнителя и качества используемых расходников. Обладая этими данными, несложно предусмотреть итог контроля. Однако, лучше выполнить несложные процедуры контроля, чтобы объективно убедиться в надежности соединения.
Самым распространенным способом определения качества сварного шва остается визуальный. Наряду с ним используются магнитный, капиллярный и радиационный виды контроля. Конечно, существуют и другие варианты, но перечисленный выше являются максимально простыми и наиболее часто востребованными. Желательно практиковать пооперационный контроль качества. Сначала сварочный шов осматривается, после этого выполняется капиллярное исследование образца и т.д.
Визуальный контроль
Наиболее доступный способ определить качество сварных соединений. Для внешнего осмотра не нужны никакие дополнительные приборы или материалы. Достаточно иметь хорошее зрение и обладать внимательностью к деталям. Сварное соединение необходимо рассматривать как можно тщательнее. Говорить о хорошем качестве можно только тогда, если нет видимых дефектов, сколов, трещин; а шов характеризуется одинаковой шириной (высотой) по всей длине. Очень важно, чтобы не было грубых дефектов сварки: складок, наплывов, непроваренных участков.
Чтобы максимально эффективно контролировать качество сварного шва, стоит в перечень используемых инструментов включить хорошую лампу, лупу, штангенциркуль и рулетку. Эти инструменты понадобятся, чтобы найти дефект, определить его размеры и наметить пути устранения проблемы. Простейшие приспособления, конечно, не позволяют полноценно контролировать качество сварки, но станут первым шагом на пути к этому.
Капиллярный контроль
Проверенный временем способ дает возможность проверить сварной шов на прочность. Суть его сводится к тому, что для проверки применяются специальные жидкости с высокой текучестью. Они проникают в самые тонкие пустоты, которые принято называть капиллярами.
Данный метод дает возможность проверить качество сварного соединения с любого состава. Он отлично подходит в ситуациях, когда есть потребность в проверке скрытых дефектов сварного соединения при ограниченном бюджете на проверку. Здесь нет потребности в дорогостоящем оборудовании, а исполнить манипуляции сможет даже новичок.
Жидкости, которые применяются в капиллярной методе оценки, называются пенетрантами. Это походное слово от английского «penetrant», что переводится как «проникающая жидкость». Для них характерно малое поверхностное натяжение. Благодаря такому свойству, субстанция легко проникает в капилляры, которые могут образоваться во время сварки. Говоря проще, пенетранты проникают в пустоты, окрашивают их, делая видимыми для человеческого глаза.
На практике используются разные растворы, каждый из которых можно приготовить самостоятельно. Они отличаются не только химическим составом, но и свойствами. На практике чаще всего применяются пенетранты, изготовленные на основе воды либо другой органической жидкости – бензола, скипидара и т.д. Именно они наиболее чувствительны к самым незначительным дефектам.
Проверка сварных швов на герметичность
На капиллярно методе испытания сварочного шва не заканчиваются. Важно определить степень герметичности стыка. Метод, который применяется в данных целях, называется по-разному: пузырьковый, гидроиспытание, течеискание и много иных вариаций. Их объединяет общая суть – обнаружение дефектов герметичности.
Герметичность стыка проверяется при помощи газа или жидкости. Суть метода идентична капиллярному. Разница заключается только в том, что кислород, азот или вода подаются под высоким давлением. Субстанции распределяются по пустотам и в случае негерметичности стыка, выходят наружу. Классификация методологий зависит от вида применяемого материала. Он бывает гидравлическим или пневматическим. Последний делится на подвиды: вакуумный или нагнетательный.
Пневматический метод контроля базируется на использовании воздуха или газовоздушной смеси, которые подаются к тестируемой области под давлением. Предварительно место стыка обильно смазывается раствором из воды и мыла. Подвидом пневматического метода является контроль с использованием вакуума. Сварочный шов промазывается мыльным раствором. После этого конструкция или деталь помещается в безвоздушную среду, созданную специальным оборудованием. Если существуют сквозные дефекты, то будут образовываться мыльные пузыри.
Для приготовления мыльного раствора необходимо использовать один кусок мыла на литр воды. В случаях, когда предполагается использовать раствор при отрицательной температуре, необходимо половину воды заменить техническим спиртом. Не лишним будет подключение манометра к емкости, где создается вакуум или нагнетается давление. Изменения в показаниях прибора будут свидетельствовать о наличии дефектов сварочного шва.
Есть очень простой и надежный способ контроля качества шва, который заключается в погружении испытуемой детали в воду. Не требуется ни мыльный раствор, ни герметичные резервуары или нагнетательное оборудование. В случаях, когда присутствуют дефекты, то из детали, погруженной в воду, будут подыматься мелкие пузырьки воздуха. Данный метод называют полевом. Несмотря на свою простоту, он достаточно эффективный.
Еще одна разновидность пневматического контроля основывается на проверке соединений при помощи аммиака. Он подается на соединение вместо воды или газа. Предварительно стыки покрываются бумажной лентой. Аммиак проникает во все доступные полости и, если шов имеет пустоты, то на поверхности бумажной ленты образуются красные пятна.
При гидравлическом методе контроля давление создается при помощи масла или воды. В зависимости от вида металла деталь выдерживается в жидкости от 5 до 15 минут. В это время зона по периметру сварочного шва обстукивается молоточком. Даже при слабых ударах жидкость станет вытекать в случаях, когда шов имеет сквозные дефекты.
Читайте также: Виды сварочных швов
Магнитное поле
В основу метода легла технология использования электромагнетизма в промышленности. С помощью специального приспособления вокруг сварочного шва создается магнитное поле, имеющее свой рисунок электромагнитных линий. Если они ровные, то можно смело сказать, что работа выполнена качественно. В случаях наличия дефектов, линия будут иметь явное искажение.
Для визуализации магнитных линий достаточно на поверхность проверяемых деталей насыпать ферримагнитный порошок. В случае искажения магнитного поля он скапливается в том месте, где присутствует дефект. В силу объективных обстоятельств данный метод приемлем только при работе с ферримагнитными металлами. Качество сварки меди, алюминия, стали с большой долей никеля или хрома проверить не получится. Помимо этого, технология является достаточно затратной. Они востребована только в случаях, когда есть необходимость точной проверки соединения особо важных узлов.
Ультразвук
Для контроля над качеством сварного шва используются также уникальные свойства ультразвука. Звуковые волны по-разному отражаются от монолитной и деформированной поверхности. Сколы и трещины имеют свои акустические особенности, которые фиксируются специальной аппаратурой. Проще говоря, на сварочный шов подается ультразвук. Если он сталкивается с пустотой, сколом или иным дефектом, то отображается от металла под другим углом. Более того, разные виды дефектов отражают ультразвук неодинаково, что позволяет диагностировать их.
Благодаря тому, что ультразвуковой метод диагностики является сравнительно недорогим и стабильно эффективным, он используется повсеместно. Распространению способствует и простота использования. К примеру, не нужно учитывать физико-химические особенности металлических сплавов, как в случаях с магнитным или радиационным контролем. Да и приобретение дорогостоящей оснастки тоже не требуется. Недостатком является необходимость наличия специальных знаний и навыков. То есть для контроля привлекается специалист со стороны. Сварщик выполнить процедуру самостоятельно не сможет.
Радиография
Радиационный контроль является миниатюрной версией всем знакомого медицинского рентгена. Гамма-лучи прошивают металл и оставляют свой след на специальной пленке. Соответственно, отображаются и скрытые от глаз внутренние дефекты сварочного стыка. Данный метод является самым передовым и позволяет точно обрисовать картину внутреннего состояния соединения.
Наряду с этим, метод имеет и недостатки. Прежде всего, это необходимость приобретения дорогостоящего оборудования. Другой нюанс – требуется предварительная подготовка специалиста. Плюс ко всему, нельзя работать с оборудованием длительной время, поскольку это негативно сказывается на состоянии здоровья.
С недавних пор есть возможность приобрести цифровой радиограф, работающий с компьютерной программой. Вместо пленки в этом случае применяются многоразовые пластины, которые реагируют с любыми лучами. Ключевое отличие от классического рентген-аппарата заключается в том, что изображение сразу отображается на мониторе компьютера. Его можно масштабировать и редактировать. Перспективой технологии является полная автоматизация процесса.
Заключение
Специалист, выполняющий контролирующие функции, должен максимально ответственно относиться к своим обязанностям. От его внимательности зависит функциональность и срок службы конструкции. Нужно фиксировать все отклонения от нормы, которые поддаются диагностированию. Чтобы получить максимально детальную картинку, желательно комбинировать несколько методов контроля. Строго воспрещается прибегать к методам, которые могут нанести вред сварному соединению.
Источник
содержание ..
90
91
92
93
94
95
96
97
98
99 ..
4-6.
Контроль сварных соединений СОСУДОВ РАБОТАЮЩИХ
ПОД ДАВЛЕНИЕМ
4-6-1. Завод-изготовитель, а также монтажные и ремонтные организации,
производящие сварку сосудов и их элементов, обязаны осуществлять
контроль сварных соединений, обеспечивающий их высокое качество и
эксплуатационную надежность. При этом объем контроля должен быть не
менее предусмотренного настоящими Правилами.
4-6-2. Все сварные соединения с толщиной стенки 6 мм и более подлежат
обязательному клеймению или иному условному обозначению, позволяющему
установить фамилию сварщика, выполнявшего сварку.
4-6-3. Система клеймения (обозначения) устанавливается производственной
инструкцией по сварке и контролю сварных соединений, она должна
предусматривать одинаковое клеймение сварных соединений изделия и
относящихся к ним контрольных сварных соединений (пластин, стыков и
др.).
4-6-4. Контроль качества сварных соединений сосудов и их элементов
должен производиться:
а) внешним осмотром и измерением;
б) ультразвуковой дефектоскопией, просвечиванием рентгеновскими или
гамма-лучами или этими методами в сочетании;
в) механическим испытанием;
г) металлографическим исследованием;
д) гидравлическим испытанием;
е) другими методами (стилоскопированием, замерами твердости, травлением,
цветной дефектоскопией и т. д.), если они предумострены техническими
условиями на изготовление данного изделия.
* 4-6-5. При сварке сосудов и их элементов из сталей аустенитного класса
должно производиться испытание сварных соединений на межкристаллитную
коррозию в соответствии с ГОСТ 6038—58*. Необходимость проведения такого
испытания определяется проектом или техническими условиями на
изготовление.
4-6-6. Контроль качества сварных соединений должен производиться после
термической обработки изделия, если последняя является обязательной.
4-6-7. Результаты контроля сварных соединений должны быть зафиксированы
в соответствующих документах (журналах, картах, формулярах и др.).
Внешний осмотр и измерения
4-6*8. Внешнему осмотру и измерениям подлежат все сварные соединения с
целью выявления в них:
а) трещин всех видов и направлений;
б) наплывов, подрезов, прожогов, незаваренных кратеров, непроваров,
пористости и других технологических дефектов;
в) излома осей соединяемых элементов;
г) смещения кромок соединяемых элементов;
д) отступлений от геометрии швов, предусмотренной чертежами (по высоте,
катету и ширине шва, по равномерности усиления и т. д.).
4-6-9. Перед внешним осмотром поверхность сварного шва и прилегающих к
нему участков основного металла шириной не менее 20 мм в обе стороны от
шва должна быть зачищена от шлака и других загрязнений.
4-6-10. Осмотр и измерения сварных соединений должны производиться с
двух сторон по всей протяженности швов в соответствии с требованиями
ГОСТ 3242—69 и ведомственных инструкций по сварке и контролю сварных
соединений. В случае невозможности осмотра внутренней поверхности
сварного соединения его осмотр следует производить только с наружной
стороны.
Ультразвуковая дефектоскопия и просвечивание
сварных соединений
4-6-11. Ультразвуковая дефектоскопия и просвечивание рентгеновскими или
гамма-лучами производятся с целью выявления в сварных соединениях
внутренних дефектов (трещин, непроваров, пор, шлаковых включений и др.).
4-6-12. Ультразвуковой контроль сварных соединений должен производиться
в соответствии с ГОСТ 14782—69 и инструкций по ультразвуковому контроля
сварных соединений, утвержденной министерством.
4-6-13. Контроль сварных соединений просвечиванием должен производиться
в соответствии с требованиями ГОСТ 7512—68 и производственных инструкций
по рентгено-гаммаграфированию.
4-6-14. Метод контроля (ультразвуковая дефектоскопия, просвечивание, оба
метода в сочетании) выбирается исходя из возможности обеспечения более
полного и точного выявления недопустимых дефектов с учетом особенностей
физических свойств металла, а также освоенности данного метода контроля
для конкретного вида сварных соединений.
*4-6-15. Объем контроля ультразвуковой дефектоскопией или просвечиванием
сварных соединений сосудов и их элементов должен быть не менее
указанного в табл. 4-6-15.
Места сопряжений (пересечений) сварных соединений подлежат обязательному
контролю просвечиванием или ультразвуковой дефектоскопией. При вварке
штуцеров и труб внутренним диаметром менее 100 мм проведение контроля
угловых и тавровых сварных соединений ультразвуком или просвечиванием не
обязательно.
4-6-16. Места ультразвукового контроля и просвечивания устанавливаются
ОТК завода-изготовителя.
4-6-17. Перед просвечиванием соответствующего участка сварные соединения
должны быть так замаркированы, чтобы их можно
было легко обнаружить на картах контроля и рентгено-
или гамма снимках.
4-6-18. Предусмотренный настоящими Правилами объем ультразвуковой
дефектоскойии и просвечивании сварных соединений может быть уменьшен по
согласованию с местными органами госгортехнадзора в случае массового
изготовления предприятием однотипных изделий при неизменном
технологическом процессе, специализации сварщиков на отдельных видах
работ и высоком качестве сварных соединений, подтвержденном результатами
контроля за период не менее одного года.
При монтаже и ремонте указанный объем контроля может быть уменьшен в
следующих случаях:
а) при невозможности осуществления контроля в полном объеме вследствие
недоступности отдельных сварных соединений (из числа подлежащих
100%-ному контролю);
б) при недоступности выполнения контроля просвечиванием по условиям
техники безопасности.
4-6-19. При выявлении недопустимых дефектов в сварных соединениях,
подвергаемых ультразвуковой дефектоскопии или просвечиванию в объеме
менее 100%, обязательному контролю тем же методом подлежат все
однотипные стыковые швы1 этого изделия, выполненные данным сварщиком, по
всей длине соединения (за исключением недоступных участков на отдельных
стыках).
Таблица 4-6-15
Примечание. При отсутствии сочетания параметров,
при определении длины прозвучиваемых и просвечиваемых швов необходимо
принимать наибольший параметр.
4-6-20. Ультразвуковая дефектоскопия и
просвечивание стыковых сварных соединений по согласованию с
Госгортехнадзором СССР могут быть заменены другим эффективным методом
неразрушающего контроля.
Механическое испытание и металлографическое
исследование
4-6-21. Механическим испытанием должны подвергаться стыковые сварные
соединения с целью проверки соответствия их прочности и пластических
характеристик требованиям настоящих Правил и технических условий на
изготовление изделия.
Обязательные виды механических испытаний:
а) на статическое растяжение;
б) на статический изгиб или сплющивание;
в) на ударную вязкость.
Испытание на статическое растяжение не является обязательным для
кольцевых сварных соединений сосудов цилиндрической формы и для труб при
условии 100%-нога контроля этих соединений ультразвуковой дефектоскопией
или просвечиванием.
Испытание на ударную вязкость сварных соединений должно производиться
при сварке сосудов и их элементов с толщиной стенки 12 мм и более в
случаях, если:
а) сосуды предназначены для работы под давлением выше 50 кгс/см2;
б) рабочая температура стенки превышает +450° С.
в) рабочая температура стенки ниже указанной минусовой температуры в
Приложении 3.
Испытание на ударную- вязкость по пунктам’«а» и «б» должно производиться
в соответствии с ГОСТ 6996—66 или техническими условиями, а по п. «в» —
на таких же образцах при рабочих температурах.
4-6-22. Металлографическому исследованию должны подвергаться стыковые,
тавровые и угловые сварные соединения сосудов и их элементов, работающих
при температуре стенки свыше 4-450° С, и независимо от температуры
стенки при давлении свыше 50 кгс/см2, а также сосудов, изготовляемых из
легированной стали, воспринимающей закалку на воздухе или склонной к
образованию межкристаллитных трещин. Этот вид исследования обязателен,
если он предусмотрен техническими условиями.
4-6-23. Проверку механических свойств и металлографическое исследование
сварных соединений производить на образцах, изготовленных из контрольных
сварных соединений (пластин, стыков И др.).
Контрольные сварные соединения должны быть идентичны контролируемым
производственным сварным соединениям по марке стали, толщине листа или
размерам труб, форме разделки кромок, методу сварки, сварочным
материалам, положению, режимам и температуре подогрева при сварке,
выполненной в один и тот же период времени.
4-6-24. Из каждого контрольного стыкового сварного соединения должны
быть вырезаны:
а) два образца для испытания на статическое растяжение;
б) два образца для испытания на статический изгиб или сплющивание;
в) три образца для испытания на ударную вязкость;
г) образцы (шлифы) для металлографического исследования в количестве не
менее одного, а при контроле сварочных соединений элементов из
высоколегированной стали — не менее двух.
в количестве не менее одного, а при контроле сварных соединений образцы
(шлифы) вырезаются только для металлографического исследования.
4-6-26. Механические испытания на статический изгиб контрольных стыков
трубчатых элементов сосудов с условным проходом труб менее 100 мм и
толщиной стенки менее 12 мм могут быть заменены испытанием на
сплющивание.
4-6-27. При сварке контрольных пластин, предназначенных для проверки
механических свойств, а также для металлографического исследования
пластины следует прихватывать к свариваемым элементам так, чтобы шов
контрольной пластины являлся продолжением шва свариваемого изделия.
Сварка контрольных пластин для проверки соединений элементов сосудов, к
которым прихватка пластин невозможна, может производиться отдельно от
изделия, но с обязательным соблюдением всех условий сварки
контролируемых стыковых соединений.
4-6-28. При автоматической сварке сосудов на каждое изделие должна
свариваться одна контрольная пластина. При ручной сварке сосудов
несколькими сварщиками каждым из них должна быть сварена одна
контрольная пластина на каждое изделие.
В случае, когда в течение рабочей смены на автоматической сварочной
машине сваривается несколько однотипных сосудов, разрешается на каждый
вид сварки варить по одной контрольной пластине в начале и конце смены
на всю партию сосудов, сваренных в данной смене.
4-6-29. При серийном изготовлении однотипных сосудов из листового
материала в случае 100%-ного контроля стыковых сварных соединений
ультразвуковой дефектоскопией или просвечиванием допускается на каждый
вид сварки варить по одной контрольной пластине на всю партию сосудов.
При этом в одну партию могут быть объединены сосуды одного вида из
листового материала одной марки, имеющие одинаковую форму разделки
кромок, выполненные по единому технологическому процессу и подлежащие
термообработке по одному режиму, если цикл изготовления всех изделий по
сборочно-сварочным работам, термообработке и контрольным операциям не
превышает 3 месяцев.
4-6-30. Для контроля качества сварных соединений в трубчатых элементах
со Стыковыми швами одновременно со сваркой последних должны
изготовляться в тех же производственных условиях контрольные стыки для
проведения испытаний механических свойств соединений.
Число контрольных стыков должно составлять 1% от общего числа сваренных
каждым сварщиком однотипных стыков, но не менее одного стыка на каждого
сварщика.
4-6-31. Сварка контрольных соединений во всех случаях должна
осуществляться сварщиками, выполнявшими контролируемые сварные
соединения на изделиях.
4-6-32. Контрольные сварные соединения (пластины, стыки, тавровые и
угловые соединения) должны подвергаться внешнему осмотру,
ультразвуковому контролю или просвечиванию по всей длине.
Если в контрольном сварном соединении будут обнаружены
недопустимые дефекты, все производственные сварные
соединения, контролируемые данным соединением и не подвергнутые
дефектоскопии ультразвуком или просвечиванию, подлежат проверке тем же
методом неразрушающего контроля по всей длине, за исключением мест,
недоступных для контроля.
4-6-33. Размеры контрольных пластин должны быть достаточными для вырезки
из них необходимого числа образцов для всех предусмотренных видов
механических испытаний и металлографического исследования, а также для
повторных испытаний.
4-6-34. Механические испытания сварных соединений должны выполняться в
соответствии с требованиями ГОСТ 6996—66 или производственных инструкций
по сварке и контролю сварных соединений, действующих в данной отрасли
промышленности.
4-6-35. При испытании контрольных сварных соединений на статическое
растяжение временное сопротивление разрыву должно быть не менее
минимально допустимого предела для основного металла по ГОСТ или
техническим условиям на соответствующие полуфабрикаты.
4-6-36. При испытании стальных сварных соединений на статический изгиб
полученные показатели должны быть не ниже приведенных в табл. 4-6-36.
Таблица 4-6-36
Минимально | |||
Тип стали | электродуговая, | газовая сварка при | |
не более 20 | более 20 | ||
Углеродистая Низколегированная | 100 | 100 | 70 |
80 | 60 | 50 | |
Низколегированная | 50 | 40 | 30 |
Высоколегированная | 50 | 40 | |
Высоколегированная | 100 | 100 | — |
При изготовлении сосудов из других материалов
показатели угла устанавливаются техническими условиями.
4-6-37. Испытание сварных соединений на ударную вязкость производится на
образцах с надрезом по оси шва со стороны его раскрытия, если место
надреза специально не оговорено техническими условиями на изготовление
изделия или инструкцией по сварке контролю сварных соединений.
4-6-38. При испытании сварных соединений труб на
сплющивание показатели испытаний должны быть не ниже соответствующих
минимально допустимых показателей, установленных ГОСТ или техническими
условиями для труб того же сортамента и из того же материала.
При испытании на сплющивание образцов из труб с продольным сварным швом
последний должен находиться в плоскости, перпендикулярной к направлению
сближения стенок.
4-6-39. Показатели механических свойств сварных соединений должны
определяться как среднеарифметическое значение результатов испытания
отдельных образцов. Общий результат испытаний считается
неудовлетворительным, если хотя бы один из образцов по любому виду
испытаний показал результат, отличающийся от установленных норм
временного сопротивления и угла статического изгиба в сторону снижения
более чем на 10%.
4-6-40. При получении неудовлетворительных результатов по какому-либо
виду механических испытаний допускается повторное испытание на удвоенном
числе образцов, вырезаемых из тех же пластин или стыков. В случае
невозможности вырезки образцов из указанных стыков повторные
механические испытания должны быть проведены на выполненных тем же
сварщиком производственных стыках, вырезанных из контролируемого
изделия.
Если при повторном испытании хотя бы на одном из образцов были получены
показатели, не удовлетворяющие установленным нормам, общий результат
испытаний считается неудовлетворительным.
4-6-41. Образцы (шлифы) для металлографического исследования сварных
соединений должны вырезаться поперек шва и изготовляться в соответствии
с требованиями ГОСТ.
Образцы для металлографических исследований сварных соединений должны
включать все сечение шва, обе зоны термического влияния сварки,
прилегающие к ним участки основного металла, а также подкладное кольцо,
если таковое применялось при сварке и не подлежит удалению.
Образцы для микроисследования сварных соединений элементов с толщиной
стенки 25 мм и более могут включать лишь часть сечения соединения. При
этом расстояние от линии сплавления до краев образца должно быть не
менее 12 мм, а площадь контролируемого сечения 25X25 мм.
При изготовлении образцов для металлографического
исследования тавровых и угловых сварных соединений трубных элементов
контрольные соединения должны разрезаться вдоль оси трубы (штуцера).
4-6-46. Помимо основных механических испытаний,
стыковые, тавровые и угловые соединения могут быть подвергнуты
дополнительным механическим испытаниям (замерам твердости металла и
др.), если они предусмотрены техническими условиями на изготовление
изделия.
содержание ..
90
91
92
93
94
95
96
97
98
99 ..
Источник