Защита от коррозии сосудов работающих под давлением
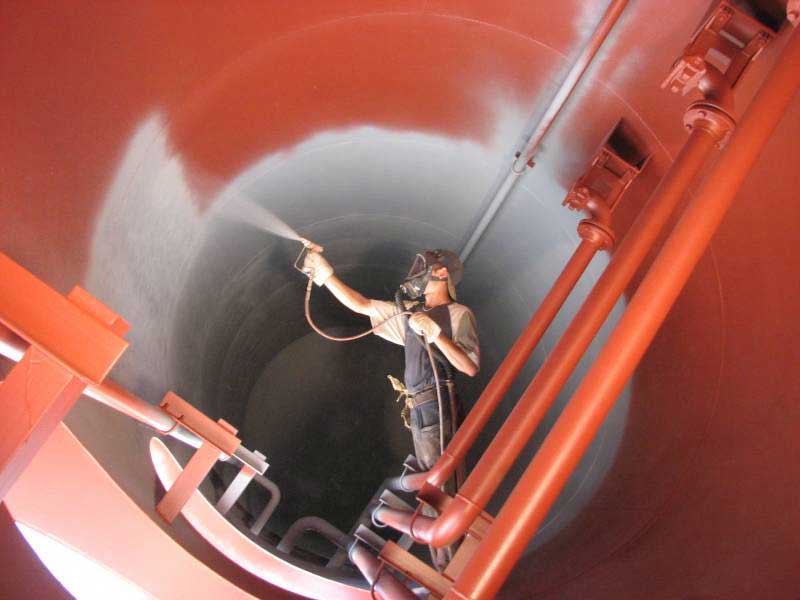
Ни одно производство не обходится без использования систем повышенного давления (трубопроводов, баллонов и емкостей для хранения или перевозки сжатых, сжиженных и растворенных газов, газгольдеров и т.д.). Любые системы повышенного давления всегда представляют потенциальную опасность.
Взрывозащита систем повышенного давления достигается организационно-техническими мероприятиями; разработкой инструктивных материалов, регламентов, норм и правил ведения технологических процессов; организацией обучения и инструктажа обслуживающего персонала; осуществлением контроля и надзора за соблюдением норм технологического режима, правил и норм техники безопасности, пожарной безопасности и т.п. Кроме того, оборудование повышенного давления должно быть оснащено системами взрывозащиты, которые предполагают:
· применение гидрозатворов, огнепреградителей, инертных газов или паровых завес;
· защиту аппаратов от разрушения при взрыве с помощью устройств аварийного сброса давления (предохранительных мембран и клапанов, быстродействующих задвижек, обратных клапанов и т.д.).
Для обеспечения безопасной и безаварийной эксплуатации сосуды и аппараты, работающие под давлением, должны подвергаться техническому освидетельствованию после монтажа и пуска в эксплуатацию, периодически в процессе эксплуатации, а в необходимых случаях и внеочередному освидетельствованию.
Объемы, методы и периодичность технического освидетельствования оговариваются изготовителем и указываются в инструкциях по монтажу и эксплуатации. В случае отсутствия таких указаний техническое освидетельствование проводится по указанию правил ПБ10 – 115 – 96. Так, для сосудов, не подлежащих регистрации в органах Госгортехнадзора России, установлена следующая периодичность:
· гидравлические испытания пробным давлением один раз в восемь лет;
· наружный и внутренний осмотр один раз в два года при работе со средой, вызывающей разрушение и физико-химическое превращение материала (коррозия и т.п.). Давление в испытываемом сосуде контролируется двумя манометрами одного типа, одинаковых пределов измерения, классов точности, цены деления. Время выдержки пробного давления устанавливается разработчиком в зависимости от толщины стенки сосуда. Так, при толщине стенки до 50 мм оно составляет 10 мин, при 50 – 100 мм – 20 мин, свыше 100 мм – 30 мин. Для литых неметаллических и многослойных сосудов независимо от толщины стенки время выдержки составляет 60 мин.
После выдержки под пробным давлением давление снижается до расчетного, при котором производят осмотр наружной поверхности сосуда, всех его разъемных и сварных соединений. Сосуд считается выдержавшим гидравлическое испытание, если не обнаружено:
· течи, трещин, слезок, потения в сварных соединениях и на основном металле;
· течи в разъемных соединениях;
· видимых остаточных деформаций, падения давления по манометру.
Сжиженные газы хранят и перевозят в стационарных и транспортных сосудах – цистернах (сосудах для сжиженных газов), которые в случае хранения криогенных жидкостей снабжены высокоэффективной тепловой изоляцией.
Для управления работой и обеспечения безопасных условий эксплуатации сосуды в зависимости от назначения должны быть оснащены:
· запорной или запорно-регулирующей арматурой;
· приборами для измерения давления;
· приборами для измерения температуры;
· предохранительными устройствами;
· указателями уровня жидкости.
Арматура должна иметь следующую маркировку:
· наименование или товарный знак изготовителя;
· условный проход;
· условное давление, МПа (допускается указывать рабочее давление и допустимую температуру);
· направление потока среды;
· марку материала корпуса.
Распространенным средством защиты технологического оборудования от разрушений при взрывах являются предохранительные мембраны (разрывные, ломающиеся, срезные, хлопающие, специальные) и взрывные клапаны.
Эксплуатационные факторы, влияющие на оборудование, работающее под давлением.
К эксплуатационным причинам относятся: нарушение режимов эксплуатации (превышение допустимых значений давлений, температур), в том числе вследствие ошибочных действий персонала или из-за отсутствия контрольных приборов; побочные процессы в устройствах и установках (коррозия, образование накипи); расширение жидкостей в замкнутых объемах вследствие нагрева;
изменение прочностных свойств конструкционных материалов в условиях низких температур; образование смеси «горючее – окислитель».
Взрыв баллонов сжатых и сжиженных газов может произойти при заполнении их рабочим телом, для которого они не предназначены.
Методы борьбы с коррозией
– Изменение коррозионной среды в сторону уменьшения ее агрессивности. Химические методы основаны на избирательном взаимодействии удаляемого газа с дозируемыми реагентами.
– Применение коррозионно-стойких материалов.
– Электрохимическая защита металла от коррозии. Уменьшается скорость коррозии.
– Замедлители коррозии(ингибиторы)
– Изоляция металлических поверхностей путем нанесения соответствующих покрытий
Методы борьбы с накипью
· – Применение в виде рабочего тела смазочно-охлаждающих эмульсий
· – Химическая подготовка воды
· – Магнитные преобразователи воды
· – Очистка воды многоступенчатыми мембранными фильтрами
· – Электрогидроимпульсная очистка сосудов от накипи
· – Ультразвуковые противонакипные устройства
Источник
Резервуары для нефтяных продуктов и газа должны сохраняться в герметичном состоянии – это одна из основных задач, стоящих перед специализированными предприятиями. Чтобы эксплуатируемое оборудование меньше подвергалось поломкам и авариям, каждую емкость требуется защитить. Делается это с помощью разнообразных средств антикоррозийной защиты.
Причины возникновения коррозии резервуаров
Чтобы понять, как защитить резервуар для нефти от коррозии, нужно знать, из-за чего она возникает. Это естественное явление, причины ее образования могут быть самыми разными:
- влажность в сочетании с перепадами температуры,
- агрессивность продуктов, которые хранятся в емкостях,
- покрасочная технология, которая для них применена.
Коррозия, которая проявляется на резервуарах для нефтепродуктов, при длительной эксплуатации может поражать как внутреннюю его часть, так и внешнюю. Основная причина, по которой коррозия резервуара проявляется на внешней части – это воздействие влажности и других неблагоприятных атмосферных явлений, а внутри емкость разъедается самим продуктом.
Необходимость защиты резервуара от коррозии
Чтобы противокоррозийная защита подземных резервуаров была действительно эффективной, для нее используются специальные защитные средства плюс труд квалифицированных специалистов.
Контролировать состояние защитного слоя необходимо постоянно, выявляя его недостатки и изъяны. Проверка должна проводиться как на внутреннем, так и на внешнем слое, она должна соответствовать всем тем стандартам, на основе которых проводятся специализированные работы. Основная задача защиты от коррозии – это препятствование возникновению коррозийных повреждений в любой части емкости. Обычно такие мероприятия начинаются еще на этапе проектирования, что позволяет значительно увеличить срок эксплуатации хранилища, так что для него изначально используются более толстые металлические листы и антикоррозийная обработка.
Способы защиты резервуаров от коррозии
Чтобы защитить подземную емкость, проводятся мероприятия двух типов. Такому резервуару нужен антикоррозийный слой от двух типов повреждений – почвенной (она же электрохимическая) коррозии и блуждающими токами. Для этого используют три типа защиты:
- протекторную;
- дренажную;
- почвенную.
Наружные поверхности защищаются нанесением на них антикоррозионных покрытий.Это очень эффективный метод, который требует предварительной обработки поверхности емкости. Как покрытие против коррозии используются полимерные ленты, битумно-полимерные или битумно-резиновые мастики.
Чтобы защитить днище резервуара от почвенной коррозии, перед монтажом его защищают с помощью специального гидроизоляционного слоя, а также с этой целью используется протекторная защита от коррозии. В чем она заключается? К днищу резервуара прикрепляется алюминиево-магниевые протекторы, которые находятся на расстоянии полутора метров от него. Эффективной также считается катодная защита.
Как проводится защита от коррозии
Чтобы защитить наружную и внутреннюю часть резервуаров от коррозийных повреждений, в качестве специальный антикоррозийных средств используют лакокрасочные покрытия. Мы обеспечиваем эффективную защиту поверхности стальных емкостей благодаря тому, что используем различные сочетания антикоррозийных составов. Результатом становится общая схема, которая максимально изолирует поверхность. Результат – она эффективно защищена от негативного влияния как окружающей среды, так и эксплуатационных факторов.
Выбор лакокрасочного покрытия напрямую зависит от того, насколько агрессивной является среда и как долго должна эксплуатироваться емкость. В работе по антикоррозионному предохранению наружных поверхностей резервуаров руководствуются требованиями РД 112-РСФСР-015-89 и ИСО 12944.
Протекторная защита емкости от коррозии предполагает использование гальванического метода. Применение такого способа индивидуально, он подходит не под каждый случай.
Протекторная защита резервуара от коррозии
Основывается она на том, что вся емкостная поверхность превращается в один неразрушаемый слой. К поверхности хранилища подключаются электроды металла с отрицательным зарядом, которые и выступают положительными анодами. Они же – протекторы. Чтобы создавался защитный ток, используют гальваническую пару протектор – металл резервуара. Но тут есть и отрицательный момент, который заключается в том, что по прошествии определенного промежутка времени протектор утрачивает свой отрицательный потенциал, то есть по мере его изнашивания эффективность защитного слоя утрачивается.
Наиболее эффективно такая защита работает для предотвращения коррозии локального типа. Ее можно применять как для уже используемых, так и для монтируемых резервуаров, ведь она не только предотвращает, что и замедляет те процессы, которые уже происходят.
Наиболее удачно использовать протекторную защиту в сочетании с пассивной, поскольку она увеличивает срок службы резервуара благодаря более ровному распределению тока по поверхности емкости. Даже если при монтаже и эксплуатации образовались дефекты покрытия, они компенсируются.
Подготовка резервуара к антикоррозийной защите
Перед нанесением антикоррозийной защиты необходимо осуществить подготовку поверхности. Заключается она в следующем:
- слой очищается от сварочных брызг, а также шлака;
- ее избавляют от последствий монтажа, транспортировки;
- с нее убирают следы, оставшиеся после газовой резки, разных острых кромок;
- а также очищают от разных отложений.
Особые требования применяются к местам стыковки металла и сварочным швам. Никаких наплывов и подрезов в этих местах быть не должно, все максимально плавно. Конструктивные элементы должны быть проварены.
Перед тем, как проводить противокоррозийную обработку, все поверхности обязательно обезжириваются. Для внутренних работ можно использовать лакокрасочные и металлизированные материала, а для наружных – только лакокрасочные. Но в обоих случаях срок службы должен составлять не менее 10 лет.
Источник
Версия для печати
6.3.1 Проект антикоррозионной защиты резервуаров для нефти и нефтепродуктов разрабатывают с учетом требований действующих нормативных документов*, а также особенностей конструкции резервуаров. условий их эксплуатации и требуемого срока службы резервуара.
6.3.2 При выборе защитных покрытий и назначении припусков на коррозию следует учитывать степень агрессивного воздействия среды на элементы металлоконструкций внутри резервуара и его наружные поверхности, находящиеся на открытом воздухе. Степень агрессивного воздействия среды на элементы металлоконструкций внутри резервуара приведена в таблице 15.
6.3.3 Степень агрессивного воздействия среды на элементы металлоконструкций резервуара, находящиеся на открытом воздухе, определяют температурно-влажностными характеристиками окружающего воздуха и концентрацией содержащихся в атмосфере воздуха коррозионно-активных газов, аэрозолей, солей и пыли в соответствии с действующими нормативными документами*.
6.3.4 Защиту металлоконструкций резервуара от коррозии необходимо осуществлять с использованием лакокрасочных покрытий, а также методами ЭХЗ. Возможно применение иных типов антикоррозионных покрытий.
6.3.5 Для обеспечения требуемой долговечности резервуара наряду с конструктивными, расчетными и технологическими мероприятиями используют увеличение толщины основных элементов конструкций (стенка, днище, крыши стационарные и плавающие, понтоны) за счет припуска на коррозию.
Значение припуска на коррозию зависит от степени агрессивности хранимого продукта, характеризующейся скоростью коррозионного повреждения металлоконструкций:
– слабоагрессивная среда — не более 0,05 мм в год;
– среднеагрессивная среда — от 0,05 до 0,5 мм в год;
– сильноагрессивная среда — более 0,5 мм в год.
6.3.6 Продолжительность срока службы защитных покрытий — не менее 10 лет.
6.3.7 ЭХЗ конструкций резервуара следует осуществлять с применением установок протекторной или катодной защиты. Выбор метода защиты должен быть обоснован технико-экономическими показателями.
Таблица 15 – Воздействие среды на элементы резервуара
Элемент конструкций резервуаров | Степень агрессивного воздействия продуктов хранения на стальные конструкции внутри резервуара | |||||
---|---|---|---|---|---|---|
Сырая нефть1 | Мазут, гудрон, битум | Дизельное топливо, керосин | Бензин2 | Пластовая вода3 | Производственные стоки без очистки4 | |
1 Внутренняя поверхность днища и нижний пояс на высоте 1 м от днища | Среднеагрессивная | Слабоагрессивная | Сильноагрессивная | 3≤pH<11, суммарная концентрация сульфатов и хлоридов до 5 г/дм3, среднеагрессивная | ||
2 Средние пояса и нижние части понтонов и плавающих крыш | Слабоагрессивная | Сильноагрессивная | ||||
3 Кровля и верхний пояс, бортовые поверхности понтона и плавающих крыш | Среднеагрессивная | Сильноагрессивная | ||||
Примечания 1 При содержании в сырой нефти сероводорода в концентрации свыше 10 мг/дм3 или сероводорода и углекислого газа в любых соотношениях степень агрессивного воздействия (см. показатели 1 и 3) повышается на одну ступень. 2 Для бензина прямогонного (см показатель 2) – повышается на одну ступень. 3 При содержании в пластовой воде сероводорода в концентрации ниже 10 г/дм3 или сероводорода и углекислого газа в любых соотношениях степень агрессивного воздействия снижается на одну ступень. 4 При периодическом смачивании поверхности конструкций или при повышении температуры стоков с 50 до 100°С в закрытых резервуарах без деаэрации следует принимать сильноагрессивную степень воздействия среды. |
* На территории Российской Федерации действует СП 28.13330.2012 «СНиП 2.03.11-85 Защита строительных конструкций от коррозии».
<< назад / к содержанию ГОСТа 31385-2016 / вперед >>
Источник
МИНИСТЕРСТВО
НЕФТЕПЕРЕРАБАТЫВАЮЩЕЙ И НЕФТЕХИМИЧЕСКОЙ ПРОМЫШЛЕННОСТИ СССР
СОГЛАСОВАНО Заместитель В.П. Бибилуров 3/X 1978 г. | УТВЕРЖДАЮ Л.А. Бычков 12/X 1978 г. |
ИНСТРУКЦИЯ
по выбору сосудов и аппаратов, работающих
под давлением до 100 кгс/см2 и защите их
от превышения давления
Москва
– 1978 г.
Настоящая
Инструкция является единым нормативным документом по выбору сосудов и
аппаратов, работающих под давлением до 100 кгс/см2 и защите их от
превышения давления на предприятиях нефтеперерабатывающей и нефтехимической
промышленности.
При подготовке
Инструкции учтен накопленный опыт по выбору, эксплуатации и защите
оборудования, а также меры безопасности, обеспечивающие безаварийную работу
оборудования.
Содержание
1.1.
Инструкция по выбору сосудов и аппаратов работающих под давлением до 100 кгс/см2
и защите их от превышения давления содержит указания, направленные на повышение
безопасности эксплуатации предприятий нефтеперерабатывающей и нефтехимической
промышленности и на дальнейшее уменьшение загрязнения воздушного бассейна
выбросами от предохранительных клапанов.
1.2.
Выполнение инструкции обязательно для вновь проектируемых объектов
нефтеперерабатывающей и нефтехимической промышленности.
1.3. С
введением в действие настоящей инструкции утрачивают силу “Рекомендации по
установке предохранительных клапанов” (РПК-66).
2.1. Каждый
сосуд, аппарат или группа сосудов и аппаратов должны быть защищены от
превышения давления.
2.2. Защита
сосудов и аппаратов от превышения давления осуществляется:
– путем установки
предохранительных клапанов или мембран;
– исключением
из системы источников, которые могут создать давление в сосуде и аппарате выше
их расчетного давления.
2.3.
Предохранительные клапаны устанавливаются непосредственно на сосуде и аппарате
в наиболее высокой их части с таким расчетом, чтобы в случае открытия клапана и
аппарата, в первую очередь, удалялись скапливающиеся пары и газы.
На
горизонтальных цилиндрических сосудах и аппаратах предохранительные клапаны
следует устанавливать по длине верхнего положения образующей; на вертикальных
сосудах и аппаратах, как правило, на верхних днищах или в местах наибольшего
скопления паров и газов.
Если клапаны
по конструктивным соображениям нельзя разместить на верхнем днище сосуда и
аппарата, в виде исключения, их можно ставить на отводящем трубопроводе или
специальном отводе.
2.4.
Предохранительные клапаны должны быть защищены от примерзания, прикипания или
засорения рабочей средой.
2.5. Установка
запорной арматуры между сосудом и аппаратом и предохранительным клапаном не
допускается за исключением решений, согласованных с Госгортехнадзором СССР.
2.6. Проходное
сечение подводящего патрубка, на котором устанавливается предохранительный
клапан, должно быть не менее проходного сечения фланца со стороны входа продукта
в предохранительный клапан. При необходимости установки двух клапанов и более
(по расчету) на одном патрубке, площадь поперечного сечения патрубка должна
быть не менее 1,25 суммарной площади проходного сечения клапанов.
2.7.
Внутренний диаметр выхлопной трубы предохранительного клапана должен быть не
менее внутреннего диаметра выходного штуцера клапана. В случае объединения
выхлопных труб от нескольких предохранительных клапанов, установленных на одном
сосуде или аппарате, сечение коллектора должно быть не менее суммы сечений
выхлопных труб от этих клапанов.
2.8. При
проектировании сброса от предохранительных клапанов технологических установок в
факельные системы следует руководствоваться “Временными нормами и
Правилами по проектированию факельных систем” ВН и ПФ 01-74.
2.9.
Количество рабочих клапанов, их пропускная способность должны быть выбраны так,
чтобы в сосуде или в аппарате при полном открытии клапана не могло образоваться
давление, превышающее расчетное более, чем на 0,5 кгс/см2 для
сосудов и аппаратов с давлением до 3 кгс/см2 включительно и на 10%
для сосудов и аппаратов с давлением свыше 3 кгс/см2.
Примечание. При выборе
предохранительного клапана следует учитывать, что клапаны конструкции
ВНИИНефтемаша типа ППК4, СППК4 открываются на полный проход при превышении
давления над давлением начала открытия на 10%.
2.10.
Регулировка предохранительных клапанов перед установкой должна осуществляться
на давление начала открытия.
2.11. На
сосудах и аппаратах, содержащих ядовитые, горючие или взрывоопасные среды, на
которых подрыв предохранительных клапанов в процессе нормальной работы приводит
к потере герметичности клапана, нарушению технологического режима, загазованию
территории, должны устанавливаться предохранительные клапаны без приспособления
для принудительного открывания их (рычага для принудительной продувки).
2.12. В
случаях, когда продукты в сосудах и аппаратах по своим свойствам не гарантируют
нормальную работу предохранительных клапанов (повышенная коррозия,
полимеризация, коксообразование, отложения и т.д.) перед клапанами должны
устанавливаться предохранительные мембраны.
2.13. Ревизия
предохранительных клапанов всех типов должна производиться в сроки,
предусмотренные “Руководящими указаниями по эксплуатации, ревизии и
ремонту пружинных предохранительных клапанов”, согласованными
Госгортехнадзором СССР 2 декабря 1977 г.
2.14. На
аппаратах непрерывно действующих процессов, оборудованных предохранительными
клапанами, продолжительность межремонтного пробега которых меньше межремонтного
пробега установки или цеха, допускается установка резервного клапана к
рабочему.
Рабочий и
резервный клапаны должны устанавливаться на отдельных штуцерах, иметь
одинаковую пропускную способность и обеспечивать в отдельности полную защиту
сосуда или аппарата от превышения давления. Допускается установка на сосуде или
аппарате рабочего и резервного клапанов с использованием переключающего
устройства в соответствии с указаниями статьи 5-2-3 “Правил устройства и
безопасной эксплуатации сосудов работающих под давлением”.
2.15.
Выхлопные трубы от каждого предохранительного клапана до коллектора, к которому
они подключаются, при необходимости теплоизолируются и обогреваются, чтобы
избежать конденсации, кристаллизации, застывания и забивания проходного сечения
в зависимости от химического состава, физических свойств и температуры
сбрасываемого продукта.
Стояки,
отводящие сбросы от предохранительных клапанов непосредственно в атмосферу,
также, при необходимости, теплоизолируются и обогреваются.
Теплоизоляция
должна быть из несгораемых материалов.
2.16.
Конструкция стояка для отвода газа от предохранительного клапана в атмосферу
должна исключать возможность попадания в него атмосферных осадков и в нижней
точке, т.е. около клапана, иметь дренажное отверстие диаметром 20-50 мм для
спуска жидкости.
2.17. В случае
возможности уноса жидкости через предохранительный клапан вместе с газами или
парами должен быть предусмотрен сепаратор (отбойник). В этом случае выхлопная
труба от предохранительных клапанов должна прокладываться с уклоном не менее
0,002 в сторону сепаратора (отбойника).
2.18.
Крепления предохранительных клапанов должны быть рассчитаны на нагрузки от веса
клапанов и реактивных усилий, возникающих при срабатывании клапана.
2.19.
Допускается защищать сосуд или аппарат от превышения давления установкой
предохранительного клапана на насосе или компрессоре, если они являются
единственными источниками давления. Сбросы от предохранительного клапана в этом
случае разрешается осуществлять на прием машин.
3.1. Выбор
сосудов и аппаратов следует осуществлять с учетом рабочей среды, давления и
температуры стенок.
3.2. Расчетное
давление сосудов и аппаратов, оборудованных предохранительными клапанами (без учета
гидростатического давления) должно превышать рабочее давление:
– для сосудов
и аппаратов содержащих нейтральные продукты (вещества) на 10%, но не менее, чем
на 1 кгс/см2;
– для сосудов
и аппаратов со взрывоопасными, взрывопожароопасными и высокотоксичными
продуктами (веществами) с рабочим давлением до 40 кгс/см2 на 20%, но
не менее, чем на 3 кгс/см2;
– для сосудов
и аппаратов со взрывоопасными, взрывопожароопасными и высокотоксичными
продуктами (веществами) с рабочим давлением свыше 40 кгс/см2 на 15%.
3.3. При
выборе емкостей для хранения сжиженных нефтяных газов и легковоспламеняющихся
жидкостей с температурой кипения до +45°С расчетное давление
должно соответствовать или превышать упругость паров продуктов при температуре
+50°С.
4.1. Сброс
ядовитых, взрывоопасных и взрывопожароопасных паров и газов от
предохранительных клапанов и мембран должен осуществляться в закрытую систему
на улавливание, сжигание на факеле или в атмосферу – в безопасное место.
4.2. Сбросы
газов и паров в атмосферу от предохранительных клапанов, установленных на
сосудах и аппаратах, содержащих ядовитые среды, производятся после
обезвреживания в специальном поглощающем устройстве.
4.3. При
сбросе в атмосферу ядовитых газов и паров без обезвреживания, а также сбросе в
атмосферу взрывоопасных и взрывопожароопасных газов и паров на сосудах и
аппаратах следует устанавливать две системы клапанов: рабочие – со сбросом в
атмосферу в безопасное место и контрольные – со сбросом в закрытую систему на
улавливание или сжигание на факеле.
4.4. Сбросы
газов и паров от предохранительных клапанов, установленных на сосудах и
аппаратах с невзрывоопасными и неядовитыми средами, направляются в атмосферу.
4.5. Сбросы
жидких продуктов от предохранительных клапанов и мембран должны осуществляться
в специальные емкости или на приемы насосов.
4.6. В
отдельных случаях сбросы от предохранительных клапанов допускается направлять в
другие сосуды и аппараты, расположенные на установке, если это не вызывает
опасных последствий или нарушений технологического режима.
4.7. Давление
начала открытия рабочих предохранительных клапанов следует принимать равным
расчетному давлению сосудов и аппаратов.
4.8. Давление
начала открытия контрольных клапанов, устанавливаемых на сосудах и аппаратах с
расчетным давлением до 60 кгс/см2 следует принимать на 10 процентов,
но не менее чем на 1,5 кгс/см2 ниже их расчетного давления, а для
сосудов и аппаратов с расчетным давлением выше 60 кгс/см2 – на 11% ниже
их расчетного давления.
При наличии
противодавления системы сброса от контрольного клапана давление начала открытия
увеличивается на величину этого противодавления.
4.9.
Пропускная способность контрольных клапанов должна быть равной пропускной
способности рабочих клапанов. Рабочие и контрольные клапаны в отдельности
должны обеспечивать полную защиту сосуда и аппарата от превышения давления. Для
отключения контрольных клапанов на ремонт и ревизию допускается установка
запорной арматуры до и после этих клапанов.
Запорная
арматура на контрольных клапанах должна устанавливаться в положении,
исключающем ее самопроизвольное закрытие и пломбироваться в открытом состоянии.
4.10.
Допускается взамен контрольных клапанов, в случае технической целесообразности
предусматривать блокировку источника давления, которая должна автоматически его
исключать при превышении давления в сосуде и аппарате на 10 процентов, но не
менее чем на 1,5 кгс/см2 выше рабочего.
Примечание. под автоматической
блокировкой понимается такая блокировка при срабатывании которой повышение
давления в сосуде и аппарате исключается от любой причины.
Например:
когда источником давления является нагрев-отключение источника нагрева; когда
источником давления является насос или компрессор-отключение насоса или
компрессора от сосуда и т.п. В случае, когда источником давления является
химическая реакция, автоматическая блокировка не может заменять установку
предохранительного контрольного клапана.
4.11. Емкости,
предназначенные для хранения сжиженных газов, а также легковоспламеняющихся
жидкостей с температурой начала кипения до 45°С, во всех случаях должны
быть оборудованы рабочими и контрольными клапанами независимо от принятой
системы сброса паров и газов.
4.12.
Максимальная температура паров и газов, сбрасываемых от предохранительных
клапанов в общезаводскую факельную систему, не должна превышать 200°С, а
температура газов на входе в газгольдер должна быть не более 60°С.
4.13. Для
предотвращения попадания сбрасываемого газа в газгольдер с температурой выше 60°С
допускается установка блокировки по сбросу газа на факел, минуя газгольдер.
№№ пп | Продукты сброса | Температура сброса | Направление сброса от | Направление сброса от контрольного |
1 | 2 | 3 | 4 | 5 |
1 | Вода | – | В | Не |
2 | Вода, | В | ||
3 | Воздух, | – | В | |
4 | Водородосодержащий | В | ||
5 | Легкие | В | В | |
6 | Пары | В | В | |
7 | Жидкие | до 80°С | В | Не |
8 | Жидкие | выше 80°С | В | Не |
9 | Нефтяные | Через | В | |
10 | Сероводород | В | На | |
11 | Аммиак | – | Через | |
12 | Нефтепродукты | до 100°С | В | |
13 | Нефтепродукты | выше 100°С | В |
Примечание:
1. При содержании в газах и
парах сероводорода в количестве больше 8%, эти газы и пары должны подаваться на
сжигание по специальным трубопроводам.
2. Сброс аммиака в атмосферу
производить только при соответствующих обоснованиях. В остальных случаях
предусматривать систему его поглощения.
Рабочее
давление в сосуде – максимальное избыточное давление, возникающее при
нормальном протекании рабочего процесса, без учета допустимого кратковременного
превышения давления во время действия предохранительного клапана или других
предохранительных устройств.
Расчетное
давление сосуда – наименьшее из расчетных давлений отдельных элементов
сосуда, работающего под давлением.
Сосуд,
работающий под давлением – это герметический закрытый аппарат или емкость,
предназначенный для ведения тепловых, химических и других технологических
процессов, для хранения и перевозки сжатых, сжиженных и растворенных газов и
жидкости под давлением.
Рабочие
предохранительные клапаны – предохранительные клапаны, предназначенные для
защиты сосудов, аппаратов и трубопроводов от разрыва.
Контрольные
предохранительные клапаны – предохранительные клапаны, предназначенные для
уменьшения случаев срабатывания рабочих предохранительных клапанов в атмосферу.
Источник