Защита сосудов от коррозии
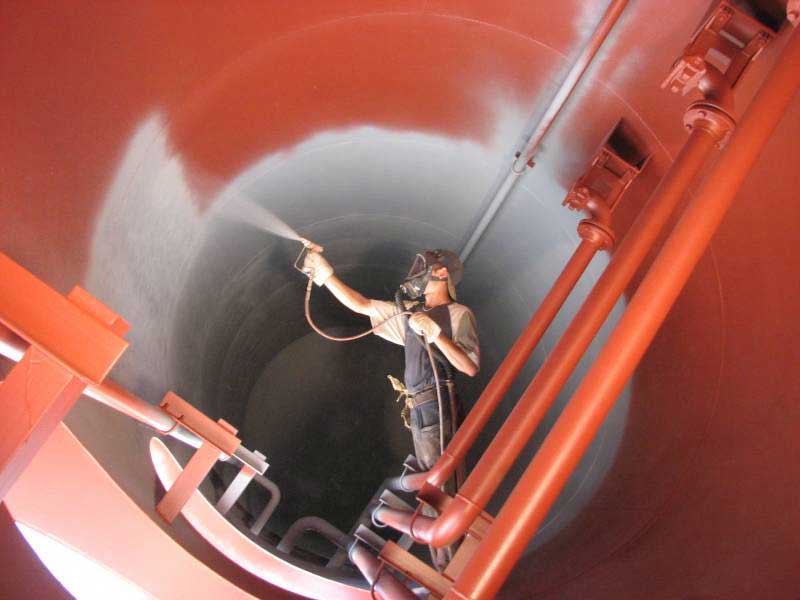
Резервуары для нефтяных продуктов и газа должны сохраняться в герметичном состоянии – это одна из основных задач, стоящих перед специализированными предприятиями. Чтобы эксплуатируемое оборудование меньше подвергалось поломкам и авариям, каждую емкость требуется защитить. Делается это с помощью разнообразных средств антикоррозийной защиты.
Причины возникновения коррозии резервуаров
Чтобы понять, как защитить резервуар для нефти от коррозии, нужно знать, из-за чего она возникает. Это естественное явление, причины ее образования могут быть самыми разными:
- влажность в сочетании с перепадами температуры,
- агрессивность продуктов, которые хранятся в емкостях,
- покрасочная технология, которая для них применена.
Коррозия, которая проявляется на резервуарах для нефтепродуктов, при длительной эксплуатации может поражать как внутреннюю его часть, так и внешнюю. Основная причина, по которой коррозия резервуара проявляется на внешней части – это воздействие влажности и других неблагоприятных атмосферных явлений, а внутри емкость разъедается самим продуктом.
Необходимость защиты резервуара от коррозии
Чтобы противокоррозийная защита подземных резервуаров была действительно эффективной, для нее используются специальные защитные средства плюс труд квалифицированных специалистов.
Контролировать состояние защитного слоя необходимо постоянно, выявляя его недостатки и изъяны. Проверка должна проводиться как на внутреннем, так и на внешнем слое, она должна соответствовать всем тем стандартам, на основе которых проводятся специализированные работы. Основная задача защиты от коррозии – это препятствование возникновению коррозийных повреждений в любой части емкости. Обычно такие мероприятия начинаются еще на этапе проектирования, что позволяет значительно увеличить срок эксплуатации хранилища, так что для него изначально используются более толстые металлические листы и антикоррозийная обработка.
Способы защиты резервуаров от коррозии
Чтобы защитить подземную емкость, проводятся мероприятия двух типов. Такому резервуару нужен антикоррозийный слой от двух типов повреждений – почвенной (она же электрохимическая) коррозии и блуждающими токами. Для этого используют три типа защиты:
- протекторную;
- дренажную;
- почвенную.
Наружные поверхности защищаются нанесением на них антикоррозионных покрытий.Это очень эффективный метод, который требует предварительной обработки поверхности емкости. Как покрытие против коррозии используются полимерные ленты, битумно-полимерные или битумно-резиновые мастики.
Чтобы защитить днище резервуара от почвенной коррозии, перед монтажом его защищают с помощью специального гидроизоляционного слоя, а также с этой целью используется протекторная защита от коррозии. В чем она заключается? К днищу резервуара прикрепляется алюминиево-магниевые протекторы, которые находятся на расстоянии полутора метров от него. Эффективной также считается катодная защита.
Как проводится защита от коррозии
Чтобы защитить наружную и внутреннюю часть резервуаров от коррозийных повреждений, в качестве специальный антикоррозийных средств используют лакокрасочные покрытия. Мы обеспечиваем эффективную защиту поверхности стальных емкостей благодаря тому, что используем различные сочетания антикоррозийных составов. Результатом становится общая схема, которая максимально изолирует поверхность. Результат – она эффективно защищена от негативного влияния как окружающей среды, так и эксплуатационных факторов.
Выбор лакокрасочного покрытия напрямую зависит от того, насколько агрессивной является среда и как долго должна эксплуатироваться емкость. В работе по антикоррозионному предохранению наружных поверхностей резервуаров руководствуются требованиями РД 112-РСФСР-015-89 и ИСО 12944.
Протекторная защита емкости от коррозии предполагает использование гальванического метода. Применение такого способа индивидуально, он подходит не под каждый случай.
Протекторная защита резервуара от коррозии
Основывается она на том, что вся емкостная поверхность превращается в один неразрушаемый слой. К поверхности хранилища подключаются электроды металла с отрицательным зарядом, которые и выступают положительными анодами. Они же – протекторы. Чтобы создавался защитный ток, используют гальваническую пару протектор – металл резервуара. Но тут есть и отрицательный момент, который заключается в том, что по прошествии определенного промежутка времени протектор утрачивает свой отрицательный потенциал, то есть по мере его изнашивания эффективность защитного слоя утрачивается.
Наиболее эффективно такая защита работает для предотвращения коррозии локального типа. Ее можно применять как для уже используемых, так и для монтируемых резервуаров, ведь она не только предотвращает, что и замедляет те процессы, которые уже происходят.
Наиболее удачно использовать протекторную защиту в сочетании с пассивной, поскольку она увеличивает срок службы резервуара благодаря более ровному распределению тока по поверхности емкости. Даже если при монтаже и эксплуатации образовались дефекты покрытия, они компенсируются.
Подготовка резервуара к антикоррозийной защите
Перед нанесением антикоррозийной защиты необходимо осуществить подготовку поверхности. Заключается она в следующем:
- слой очищается от сварочных брызг, а также шлака;
- ее избавляют от последствий монтажа, транспортировки;
- с нее убирают следы, оставшиеся после газовой резки, разных острых кромок;
- а также очищают от разных отложений.
Особые требования применяются к местам стыковки металла и сварочным швам. Никаких наплывов и подрезов в этих местах быть не должно, все максимально плавно. Конструктивные элементы должны быть проварены.
Перед тем, как проводить противокоррозийную обработку, все поверхности обязательно обезжириваются. Для внутренних работ можно использовать лакокрасочные и металлизированные материала, а для наружных – только лакокрасочные. Но в обоих случаях срок службы должен составлять не менее 10 лет.
Источник
Коррозия – это ужасная гадость, от которой страдает множество машин и механизмов. Бытует мнение, что если коррозия поползла по детали или изделию, то это уже бесповоротно. Именно поэтому на практике используется множество способов борьбы с коррозией.
Рассмотрим самые популярные из них в формате научно-популярного материала. Сразу хочу отметить, что если вы уже знаете этот вопрос довольно глубоко, то материал может показаться вам не особенно полным. Мы на исчерпывающий учебник не претендуем, а ставим собой целью просветить тех, кто только столкнулся с задачей борьбы с коррозией. Ну а в конце статьи приведем полезные советы для тех, кто пытается бороться с коррозией своими силами 🙂
Вспоминаем, что такое коррозия
Прежде, чем обсуждать способы защиты от коррозии, давайте вспомним, что такое коррозия. Вопрос этот мы подробно разобрали на канале в этом материале. Тут вспомним самое главное.
Коррозия – это разрушение материала (причем, не обязательно металла) при воздействии кислорода (будь -то из воздуха или из воды). И всё! Значит в космосе без кислорода коррозия невозможна, но это не значит, что невозможны другие вариант деградации свойств материалов.
При взаимодействии с кислородом деталь протухает. Было у нас железо, стал оксид железа. У одного свойства как у меча викинга, у другого свойства как у оранжевого песка 🙂
Соответственно, все методы коррозии преимущественно построены на том, что нужно исключить доступ кислорода к поверхности защищаемой детали. Правда есть методики, которые пытаются уменьшить восприимчивость детали к кислороду, но их мало. Большинство методов крутится вокруг защитных пленок разного типа и природы. Какие же промышленные методы защиты от коррозии можно выделить?
Пассивация
Слово пассивация означает, что металл делается невосприимчивым к кислороду. Становится пассивным. Мы уже обсуждали, как работает нержавеющая сталь. В этой статье вопрос рассматривается подробно. По сути дела – это создание нержавейки.
Схема найдена на Яндекс.Картинках
Результат достигается благодаря добавлению к железному сплаву при выплавке элементов, типа хрома или никеля. Эти элементы образуют такие соединения, которые в ответ на воздействие кислорода не превращаются в оранжевую пыль и ржавчину, а формируют плотную пленку на поверхности металла, которая будет невосприимчива к кислороду.
Защитное покрытие
Вы наверняка встречали хромированные детали или слышали слово оцинковка. И то, и другое есть способ защиты от коррозии. Берем железную деталь и на поверхность наносим материал ,который не коррозирует. Например, слой цинка или никеля.
Этот слой не будет воспринимать агрессивное воздействие кислорода и защитит основной металл. Правда рано или поздно покрытие начинает отслаиваться. Под ним начинает расти ржавчина, а остатки покрытия усугубляют процесс. Хороший пример тут – это какой-нибудь старый бампер.
Но, несмотря на подобного рода недостатки, способ активно используется и гораздо более экономичен, чем выплавка нержавейки.
Электрозащита от коррозии
Как мы помним, любая химическая реакция, коей и является коррозия, связана с передаче электронов. Окисление – отдача, а восстановление прием. Если запретить этот процесс или препятствовать ему, то возможно фактически затормозить коррозионный процесс. Именно так работает методика электрозащиты от коррозии.
Есть защита активная, а есть пассивная.
Активная (катодная) заключается в пропускании через деталь токов, которые не дают электронам свободно блуждать по детали и генерировать блуждающие токи, а значит и с кислородом оно будет меньше взаимодействовать. Электронов не хватит 🙂
Пассивная защита (протекторная) заключается в том, что мы используем в паре с основным металлом, некоторый более активный металл. Например, в морских судах часто используют заклепки из цинковки, которые оттягивают на себя эти лишние электроны и забирают себе коррозию.
Ингибиторы коррозии
Ингибиторы – это вещества, которые замедляют коррозию. Их существует огромное количество. Происходит это преимущественно благодаря воздействию на окружающую среду.
Например, если коррозия протекает у нас в кислой среде, то логично было бы выравнивать эту среду для достижения ею нейтрального pH.
Термическая обработка
Термическая обработка любого металла заключается в том, что при воздействии некоторых температур происходят фазовые превращения. Одна фаза в металле превращается в другую.
Все фазы по разному воспринимают воздействие внешних факторов. В частности – кислорода. Значит, если произошло фазовое превращение, то и деталь становится менее восприимчива к окружающим агрессивным факторам.
На этом построена логика улучшения антикоррозионных свойств посредством термической обработки. Само собой, процесс явно не для домашнего использования.
Лакокрасочное покрытие
Это самый простой и экономичный способ защитить деталь от коррозии. В простонародье звучит просто как “покрасить”. Если сказать более умно, то создается специальное защитное полимерное покрытие на поверхности детали, которое препятствует попаданию на металла кислорода в той или иной его форме. Вариантов ЛКП и их реализаций существует бесчисленное множество. Перечислять их бессмысленно.
Разве что, отметим. Все ЛКП рано или поздно разрушаются от агрессивных факторов, а металл под ними начинает цвести. Именно из-за этого на всех машинах появляются зоны цветения.
Как бороться с коррозией в домашних условиях
Вот и добрались мы до самого важного.
Все перечисленные выше методики применимы для промышленного использования. Что же делать в домашних условиях?
Ну если деталь очень важная, то при некоторых условиях и при наличии производства под боком, можно нанести покрытие. Например, сделать оцинковку. Но это опять не совсем дома.
Разве что, только ЛКП и можно реализовать дома. Вот именно такой вариант обычно и используется простыми обывателями для защиты от ржавчины.
На что важно обращать внимание, при попытке создать ЛКП или защититься от коррозии различными шайтан-методами, типа растворенного в ацетоне линолеума или проварки деталей в масле.
- Самое важное – помнить определение коррозии. Она начинается тогда, когда на детали попадает кислород. Значит, если автомобилист утверждает, что под лкп протекает бескислородная коррозия, он совсем не прав! Ну а нам нужно добиться максимального исключения взаимодействия голой детали с внешней средой.
- ЛКП всегда нужно наносить строго по установленной производителем технологии. Она обычно приводится на банке с краской. И написана та мне случайно 🙂 Некоторые умники наносят лкп, например, в мороз. Так оно не поможет.
- Поверхность всегда должна быть правильно подготовлена. Нужно полностью исключить следы старой ржавчины, например путем механической зачистки детали и последующей обработкой преобразователем ржавчины. Малейшая частичка ржавчины или пораженная зона даже под краской начнет цвести. Не забывайте, что нет ничего абсолютного. Вот так и лкп или полимерное покрытие пропускают кислород в том или ином количестве. Кислород будет проникать и диффундировать через краску, даже в минимальных масштабах.
4. Нужно использовать грунтовку. Ведь для нас важна адгезия полимерного слоя краски к чистому металлу. Если адгезии нет, но есть полимерная пленка, то она отслаивается, как пакет от хлеба. А в полости начинает скапливаться влага и появляются благоприятные условия для коррозии. Сродство у металла и краски не хорошее. А значит, промежуточный слой точно не станет лишним!
5. Нужно следить за чистотой детали и использовать ингибиторы. Любая грязь способствует изменению показателя ph среды, что в свою очередь, сказывается и на защитных свойствах. Нам нужно стремиться к нейтральной среде.
Вот как-то так! Всем спасибо
Если статья помогла или интересна, то обязательно поддержите нас лайком и подпиской ;)!!!
Источник
Версия для печати
11.1. Защита резервуаров от коррозии должна проводиться на основании анализа условий эксплуатации, климатических факторов, атмосферных и иных воздействий на наружные поверхности резервуаров, а также вида и степени агрессивного воздействия хранимого продукта и его паров на внутренние поверхности. По результатам анализа должен быть разработан отдельный проект или раздел в составе проекта КМ антикоррозионной защиты (АКЗ) резервуара с указанием систем АКЗ, срока их службы при выполнении принятых в проекте технических решений.
Производитель лакокрасочных материалов (ЛКМ) разрабатывает регламент (инструкцию) по нанесению ЛКМ, в котором подробно описывается система АКЗ, применяемые материалы и технология их нанесения.
На выполнение работ по антикоррозионной защите резервуара Производитель работ разрабатывает проект производства работ, в котором отражаются технология подготовки поверхностей резервуара, нанесение грунтовочных и покрывных слоев покрытия, методы по контролю качества, применяемое оборудование с учетом требований Регламента производителя ЛКМ, меры безопасности, противопожарные мероприятия.
11.2. Защиту от коррозии рекомендуется осуществлять применением систем лакокрасочных или металлизационно-лакокрасочных антикоррозионных покрытий, а также применением электрохимических способов.
Для защиты резервуаров от коррозии могут применяться следующие типы ЛКМ со сроком службы не менее 10 лет для внутренней поверхности и 15 лет для наружной поверхности:
– эпоксидные покрытия;
– двухкомпонентные полиуретановые покрытия;
– однокомпонентные полиуретановые влагоотверждаемые покрытия.
В том случае, если нормативный срок службы резервуара превышает расчетный срок службы антикоррозионных покрытий, в техническом задании на проектирование резервуара (Приложение П.2) должны быть установлены припуски на коррозию основных конструктивных элементов – стенки, днища, крыши, понтона, плавающей крыши.
11.3. При выборе типа ЛКМ необходимо отдавать предпочтение материалам с высокой степенью ремонтопригодности и технологичности их применения, а также учитывать погодно-климатические условия во время нанесения антикоррозионных покрытий:
– для эпоксидных и двухкомпонентных полиуретановых покрытий – температура поверхности не ниже +5°С и относительная влажность воздуха не выше 80 %;
– для однокомпонентных полиуретановых влагоотверждаемых покрытий – температура поверхности не ниже 0°С и относительная влажность воздуха до 98 %.
11.4. Системы АКЗ, тип покрытия и материалы для защиты внутренних поверхностей резервуаров определяются с учетом эксплуатационных условий и свойств хранимых жидкостей, а также степени их агрессивного воздействия на конструкции резервуаров в соответствии с таблицей 11.1.
Таблица 11.1
Элементы конструкций резервуаров | Степень агрессивного воздействия среды на стальные конструкции внутри резервуаров | ||
---|---|---|---|
сырой нефти | мазута, дизельного топлива, керосина | бензина | |
Внутренняя поверхность днища и нижний пояс на высоту 1 м от днища | средне-агрессивная | средне- | слабо-агрессивная |
Средние пояса, нижние части понтонов и плавающих крыш | слабо-агрессивная | слабо- | слабо-агрессивная |
Верхний пояс (зона периодического смачивания) | средне-агрессивная | слабо- | средне-агрессивная |
Кровля резервуара, верх и бортовые поверхности понтонов и плавающих крыш | средне-агрессивная | средне- | слабо-агрессивная |
Примечания: 1. Степень агрессивного воздействия мазута принимается для температуры до 90°С. 2. Для нефти и нефтепродуктов с высоким содержанием серы (более 1,8 %) степень агрессивного воздействия на внутреннюю поверхность днища, нижний пояс стенки, кровлю, верх и бортовые поверхности понтонов и плавающих крыш повышается на одну ступень. |
11.5. Антикоррозионные покрытия внутренних поверхностей резервуаров должны удовлетворять следующим условиям:
– быть устойчивыми к воздействию нефти, нефтепродуктов, подтоварной воды;
– обладать хорошей адгезией к грунтовочному слою или основному металлу (в зависимости от технологии нанесения);
– не вступать в реакцию с хранимыми продуктами и не оказывать влияние на их кондицию;
– быть стойкими к растрескиванию;
– обеспечивать совместимость деформаций с корпусом резервуара (с учетом различных толщин стенки по высоте) при заполнении и опорожнении;
– обладать износостойкостью на истирание (в резервуарах с плавающими крышами и понтонами) и долговечностью;
– сохранять адгезионные свойства, механическую прочность и химическую стойкость в расчетном диапазоне температур;
– сохранять защитные свойства при совместной работе с электрохимической, катодной и протекторной защитой;
– быть технологичными при нанесении и соответствовать температуре и относительной влажности воздуха во время выполнения работ;
– удовлетворять требованиям электростатической искробезопасности.
11.6. Наружные поверхности резервуаров, находящиеся на открытом воздухе, должны быть защищены антикоррозионными покрытиями на основе ЛКМ светлого тона с высокой светоотражательной способностью – не менее 98 % по ГОСТ 896-69. Степень агрессивного воздействия среды на наружные поверхности резервуаров определяется температурно-влажностными характеристиками окружающего воздуха и концентрацией в нем коррозионно-активных газов в соответствии со СНиП 2.03.11-85.
11.7. При защите от коррозии наружной поверхности днищ резервуаров следует руководствоваться следующими требованиями:
– устройство фундаментов и основания под резервуар должно обеспечивать отвод грунтовых вод и атмосферных осадков от днища;
– при выполнении гидрофобного слоя из битумно-песчаной смеси по п. 10.3.2 не требуется нанесения защитных покрытий на наружную поверхность днища. Применяемые песок и битум не должны содержать коррозионно-активных агентов.
11.8. В целях активной защиты резервуара от почвенной коррозии и коррозии блуждающими токами рекомендуется применение электрохимической защиты.
Электрохимическая защита наружной поверхности днища, а также внутренних поверхностей днища и нижнего пояса стенки в зоне контакта с донным осадком и слоем подтоварной воды осуществляется установками протекторной защиты (УПЗ) или установками катодной защиты (УКЗ).
Выбор метода защиты осуществляется на основании сравнения технико-экономических показателей.
11.9. При подготовке резервуара для нанесения антикоррозионных покрытий следует руководствоваться требованиями ГОСТ 9.402-2004 «ЕСЗКС. Покрытия лакокрасочные. Подготовка металлических поверхностей перед окрашиванием».
На поверхностях металлоконструкций, подготовленных к выполнению антикоррозионных работ, должны отсутствовать:
– возникшие при сварке остатки шлака, сварочные брызги, наплывы, неровности сварных швов;
– следы обрезки и газовой резки, расслоения и растрескивания;
– острые кромки до радиуса менее 3,0 мм на внутренней и 1,5 мм на наружной поверхностях резервуара;
– вспомогательные элементы, использованные при сборке, монтаже, транспортировании, подъемных работах и следы оставшиеся от приварки этих элементов;
– химические загрязнения (остатки флюса, составов использовавшихся при дефектоскопии сварных швов), которые находятся на поверхности сварных швов и рядом с ними;
– жировые, механические и другие загрязнения.
Сварные швы должны иметь плавный переход к основному металлу без подрезов и наплывов. Все элементы металлоконструкций внутри резервуара, привариваемые к стенке, днищу или крыше, должны быть обварены по контуру для исключения образования зазоров и щелей. Кроме того, все элементы металлоконструкций, находящихся на открытом воздухе, при средне-агрессивном воздействии окружающей среды, также должны быть обварены по контуру для исключения образования зазоров и щелей.
Перед нанесением защитных покрытий все поверхности должны быть очищены от окислов до степени 2 по ГОСТ 9.402-2004 или до степени не ниже Sa 2,5 по ИСО 8501-1, обеспылены и обезжирены. Степень обезжиривания – 1 по ГОСТ 9.402-2004. Степень обеспылевания должна быть не ниже 2 класса по ИСО 8502-3.
11.10. При выполнении антикоррозионных работ должны быть учтены требования к охране окружающей среды и требований действующих правил техники безопасности в строительстве: СНиП 2.03.11, СНиП 1.03-05, ГОСТ 12.3.005, ГОСТ 12.3.016, ГОСТ 12.4.011, СН-245.
11.11. После проведения антикоррозионных работ по результатам пооперационного контроля составляется заключение о качестве нанесенных защитных материалов, разрешающее выполнение следующего этапа работ. После завершения всего комплекса работ по антикоррозионной защите оформляется Акт освидетельствования комплексного защитного покрытия.
<< назад / к содержанию СТО-СА-03-002-2009 / вперед >>
Источник