Класс опасности сосудов работающих под давлением
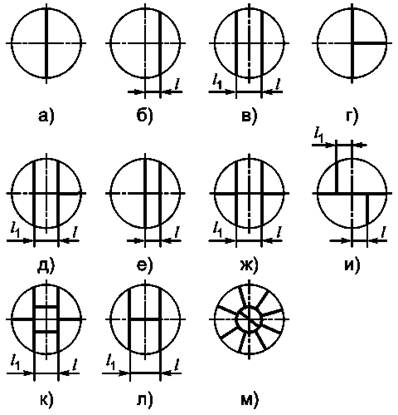
Таблица N 4
Распределение сосудов по группам опасности
Группа опасности сосуда | Расчетное давление, МПа | Температура стенки, °C | Рабочая среда |
1 | Свыше 0,07 | Независимо | Взрывоопасная и (или) пожароопасная, и (или) вредная среда 1, 2 классов опасности |
2 | До 2,5 | Ниже -70, выше 400 | Любая, за исключением указанной для 1-й группы сосудов |
Свыше 2,5 до 4 | Ниже – 70, выше 200 | ||
Свыше 4 до 5 | Ниже -40, выше 200 | ||
Свыше 5 | Независимо | ||
До 1,6 | От – 0 до -20, от 200 до 400 | ||
3 | Свыше 1,6 до 2,5 | От -70 до 400 | |
Свыше 2,5 до 4 | От -70 до 200 | ||
Свыше 4 до 5 | От -40 до 200 | ||
4 | До 1,6 | От -20 до 200 |
108. При изготовлении, монтаже, ремонте и реконструкции (модернизации) сосудов должны быть выполнены требования ПКД и ТД в части контроля:
1) соответствия металла свариваемых деталей и сварочных материалов;
2) соответствия качества подготовки кромок и сборки под сварку;
3) соблюдения технологического процесса сварки и термической обработки.
109. Основными методами контроля металла и сварных соединений являются:
1) визуальный и измерительный контроль;
2) радиографический контроль;
3) ультразвуковая дефектоскопия;
4) атомно-эмиссионный спектральный анализ (стилоскопирование);
5) измерение твердости;
6) гидравлические испытания;
7) пневматические испытания;
8) магнитопорошковая дефектоскопия.
Кроме этого, могут применяться другие методы контроля (акустическая эмиссия, магнитография, капиллярный контроль, определение содержания в металле шва ферритной фазы) в объеме, предусмотренном ПКД.
110. При разрушающем контроле должны проводиться механические испытания, металлографические исследования и испытания на стойкость к межкристаллитной коррозии в объеме, предусмотренном ПКД.
111. Приемочный контроль изделия, сборочных единиц и сварных соединений должен выполняться после окончания всех технологических операций, связанных с термической обработкой, деформированием и наклепом металла.
Последовательность контроля отдельными методами должна соответствовать требованиям ТД. Визуальный и измерительный контроль должен предшествовать контролю другими методами.
112. Контроль сварных соединений должен производиться по методикам организации-изготовителя сосуда, согласованным с головной материаловедческой организацией.
113. Методы и объемы контроля сварных соединений приварных деталей, не работающих под внутренним давлением, должны устанавливаться в ПКД.
114. При операционном контроле проверяется выполнение исполнителями требований ТД.
115. Результаты по каждому виду контроля, в том числе и операционному, должны фиксироваться в отчетной документации (журналах, формулярах, протоколах, маршрутных паспортах).
116. Средства измерения должны проходить метрологическую поверку (калибровку), а испытательное оборудование – аттестацию.
117. Каждая партия материалов для дефектоскопии (пенетранты, порошок, суспензии, радиографическая пленка, химические реактивы) до начала их использования должна быть подвергнута входному контролю.
118. Сварное соединение признается годным, если при контроле в нем не будут обнаружены внутренние и наружные дефекты, выходящие за пределы допустимых норм.
119. Сведения о контроле сварных соединений основных элементов сосудов, работающих под давлением, определенных в ПКД, должны заноситься в паспорт сосуда.
120. Визуальному и измерительному контролю при изготовлении, монтаже, ремонте и реконструкции (модернизации) сосудов подлежат все сварные соединения сосудов и их элементов в целях выявления в них следующих дефектов:
1) трещин всех видов и направлений;
2) свищей и пористости наружной поверхности соединения;
3) подрезов;
4) наплывов, прожогов, незаваренных кратеров;
5) смещения и совместного увода кромок свариваемых элементов свыше норм, предусмотренных настоящими Правилами;
6) непрямолинейности соединяемых элементов;
7) несоответствия формы и размеров соединений требованиям НД.
121. Перед визуальным и измерительным контролем поверхность сварного соединения и прилегающие к нему участки основного металла шириной не менее 20 мм в обе стороны от соединения должны быть зачищены от шлака и других загрязнений, при электрошлаковой сварке это расстояние должно быть не менее 100 мм.
122. При двустороннем доступе визуальный и измерительный контроль должны производиться с наружной и внутренней стороны по всей протяженности швов. В случае невозможности проведения визуального и измерительного контроля сварного соединения с двух сторон, его контроль должен производиться в порядке, предусмотренном в руководстве (инструкции) по эксплуатации сосуда.
123. Ультразвуковая дефектоскопия и радиографический контроль сварных соединений при изготовлении, монтаже, ремонте и реконструкции (модернизации) сосудов производятся в целях выявления в сварных соединениях внутренних дефектов (в том числе трещин, непроваров, пор, шлаковых включений).
124. Метод контроля (ультразвуковая дефектоскопия, радиографический контроль или оба метода в сочетании) выбирается исходя из возможности обеспечения более полного и точного выявления дефектов с учетом особенностей физических свойств металла, а также освоенности данного метода контроля для конкретного вида сварных соединений.
125. Объем контроля ультразвуковой дефектоскопией или радиографическим методом стыковых, угловых, тавровых и других сварных соединений сосудов (включая соединения люков и штуцеров с корпусом сосуда) должен соответствовать информации, приведенной в таблице N 5 настоящих Правил.
Указанный объем контроля относится к каждому сварному соединению. Места сопряжений (пересечений) сварных соединений подлежат обязательному контролю ультразвуковой дефектоскопией или радиографическим методом.
Ультразвуковая дефектоскопия или радиографический контроль швов приварки внутренних и наружных устройств к корпусу сосуда должны производиться при наличии требования в ПКД.
Источник
НовостиВсе новости Нам доверяют | Классфикация ОПО появилась в 2013 году. «Виновник» – федеральный закон № 22-ФЗ от 04.03.2013 г. Ростехнадзор разделил опасные объекты на четыре класса по степени опасности (п. 3 статьи 2 ФЗ №116):
В статье расскажем, как определить класс опасности опасного производственного объекта. Как определить класс опасности ОПОКласс опасности ОПО определяют согласно Приложению 2 к Федеральному закону от 21 июля 1997 г. № 116 «О промышленной безопасности ОПО». Он зависит от технических параметров объекта, характеристик машин и механизмов, которые входят в его состав (сосуды под давлением, грузоподъемные механизмы, газо- и паропроводы и т.д.). Пример 1 Для газифицированных котельных (ОПО «Сеть газопотребления», есть на многих предприятиях), которые транспортируют «природный газ под давлением свыше 0,005 мегапаскаля до 1,2 мегапаскаля включительно или сжиженный углеводородный газ под давлением свыше 0,005 мегапаскаля до 1,6 мегапаскаля включительно», предусмотрен 3 класс опасности (см. п.п. 2 п. 4 Приложения 2 к ФЗ №116). Если ваш объект газопотребления предназначен «для транспортировки природного газа под давлением свыше 1,2 мегапаскаля или сжиженного углеводородного газа под давлением свыше 1,6 мегапаскаля», то он при регистрации получит 2 класс опасности (см. п.п. 1 п. 4 Приложения 2 к ФЗ №116). Пример 2 Возьмем объект, на котором есть воздухосборник модели В-4 (сосуд, работающий под избыточным давлением). Согласно эксплуатационной документации, устройство имеет следующие технические характеристики: рабочее давление 6 кг/см2 (порядка 0,6 МПа), температура рабочей среды (сжатый воздух) около 200 градусов по Цельсию. Согласно п.п. 2 п. 5 Приложения 2 к ФЗ №116, такой ОПО принадлежит к 4 классу опасности. Обоснование: п. 5 Приложения 2 к ФЗ №116 гласит: «Для опасных производственных объектов, указанных в пункте 2 приложения 1 (ОПО, где используется оборудование, работающее под избыточным давлением более 0,07 мегапаскаля) к настоящему Федеральному закону (ФЗ №116), устанавливаются следующие классы опасности: 1) III класс опасности – для ОПО, осуществляющих теплоснабжение населения и социально значимых категорий потребителей, а также иных опасных производственных объектов, на которых применяется оборудование, работающее под избыточным давлением 1,6 мегапаскаля и более или при температуре рабочей среды 250 градусов Цельсия и более; 2) IV класс опасности – для опасных производственных объектов, не указанных в подпункте 1 настоящего пункта». Наш воздухосборник работает под давлением 0,6 МПа и при температуре рабочей среды 200 С. Соответственно, он будет принадлежать к 4 классу опасности. Пример 3 На вашем ОПО (цех, производственная площадка, ангар) установлен сосуд, работающий под давлением, иностранного производства «Autoclave Ø 1300 x L 3600 a 10 bar e 300 °C». Согласно паспорту изделия, рабочее давление на корпус составляет 1 МПа, а температура рабочей среды (сжатый воздух или сжиженный газ) – 300 С. Объект регистрируется впервые, поэтому надо определить его категорию опасности. Обратимся к п. 5 Приложения 2 к ФЗ №116. Нас интересует п.п. 1: … устанавливаются следующие классы опасности: 1) III класс опасности – для ОПО, осуществляющих теплоснабжение населения и социально значимых категорий потребителей, а также иных опасных производственных объектов, на которых применяется оборудование, работающее под избыточным давлением 1,6 мегапаскаля и более или при температуре рабочей среды 250 градусов Цельсия и более». Давление в сосуде ниже 1,6 МПа, но температура рабочей среды более 250 С. Обращаем внимание на заключительную фразу «…или при температуре рабочей среды 250 градусов Цельсия и более» и определяем, что по термическим показателям наш автоклав даст ОПО 3 класс опасности. Пример 4 Опасные производственные объекты, на которых используют стационарно установленные грузоподъемные механизмы (ОПО с ПС) принадлежат к 4 классу опасности (п. 6 Приложения 2 к ФЗ №116). Другими словами, если на вашем объекте применяется грузоподъемный кран (мостовой, башенный, козловой и т.д.), автокран или подъемник (к примеру, в гараже, производственном цехе), то ему будет присвоен 4 класс опасности. Полезная статья по теме:
Зачем ОПО нужен класс опасностиНеобходимость присвоить каждому ОПО класс опасности регламентирована законодательно – об этом говорит Федеральный закон от 21 июля 1997 г.№ 116 «О промышленной безопасности ОПО». Кроме того, некоторые владельцы ОПО (в частности, 3 и 4 классов опасности) получают преимущества по проверкам Ростехнадзора, а также с точки зрения разрешительных документов. Напомним, что с документальной и эксплуатационной точки зрения ОПО характеризуются следующим образом: ОПО 1 и 2 класса опасности:
ОПО 3 класса опасности:
ОПО 4 класса опасности:
Будет полезно изучить:
Остались вопросы?Получите консультацию эксперта по телефону +7 (926) 333-48-13 или электронной почте expert@mtk-exp.ru |
Источник
Данная публикация посвящена проблеме, с которой сталкиваются многие владельцы автогазозаправочных станций, заправляющих автотранспорт сжиженными углеводородными газами (СУГ), на которых применяются сосуды под давлением менее 1,6 МПа.
Такие АГЗС обладают признаками опасных производственных объектов (ОПО) и подлежат регистрации в Государственном реестре опасных производственных объектов.
При регистрации заявитель должен определить и указать в заявлении класс опасности объекта, один из четырех возможных вариантов, указанных в п. 3 ст. 2 Закона о промышленной безопасности:
I класс опасности – объекты чрезвычайно высокой опасности;
II класс опасности – объекты высокой опасности;
III класс опасности – объекты средней опасности;
IV класс опасности – объекты низкой опасности.
Как правило, отнесение АГЗС к числу опасных производственных объектов (ОПО) обусловлено применением оборудования, работающего под избыточным давлением более 0,07 МПа[1].
Исходя из положений подпунктов 1 и 2 пункта 5 Приложения 2 к Закону о промышленной безопасности, объекты, на которых применяется оборудование, работающее под давлением 1,6 МПа и более, относятся к III классу опасности.
Объекты, на которых применяется оборудование с давлением менее 1,6 МПа, относятся к объектам IV класса опасности.
Ряд производителей АГЗС имеет в линейке своей продукции заправочные станции, оборудование которых настроено на работу с давлением менее 1,6 МПа.
Однако при регистрации данных АГЗС в качестве ОПО возникают сложности, органы Ростехнадзора отказываются регистрировать АГЗС, на которых используются сосуды с давлением менее 1,6 МПа в качестве ОПО IV класса опасности.
Ранее мы писали о том, как удалось оспорить в суде отказ Ростехнадзора в регистрации АГЗС, на которой используются сосуды, работающие под давлением 1,57 МПа (подробнее: /nashi-raboty/2018-god/dobilis-priznanija-nezakonnym-otkaza-rostekhnadzora-v-registracii-agzs-v-kachestve-opasnogo-proizvodstvennogo-obekta-iv-klassa-opasnosti/)
Ростехнадзор отказал в регистрации, указав на неправильно проведенную заявителем идентификацию ОПО. По мнению уполномоченного на регистрацию органа, АГЗС предпринимателя является объектом III класса опасности.
Суд первой инстанции согласился с позицией предпринимателя, основанной на том, что представленными в материалы дела документами, в том числе паспортом завода-изготовителя и сертификатом соответствия подтверждается факт того, что давление применяемого на АГЗС оборудования составляет 1,57 МПа, т.е. менее 1,6 МПа:
«Из материалов дела следует, что согласно проектной документации на спорной ОПО предпринимателем установлены сосуды, работающие под давлением – резервуары надземные одностенные для сжиженных углеводородных газов РНГО – 10 – 04, 2 шт, рег. № А-22667, А-22668, заводские № 352, 353 с максимальным рабочим давлением СУГ в технологической системе Рраб = 1,57 Мпа (лист 1.2, шифр: ЧПГ-949-839-00).
В соответствии с паспортами на названные сосуды, которые составлены заводом-изготовителем (…..), рабочее давление СУГ составляет 1,57 МПа…
… Таким образом, поскольку максимальное рабочее давление оборудования, применяемого на спорном ОПО, составляет менее 1,6 Мпа, следовательно, вопреки доводам управления, оно не подлежит отнесению к III классу опасности».
Суд признал незаконным решение Управления Ростехнадзора об отказе в регистрации опасного производственного объекта в Государственном реестре опасных производственных объектов и обязал Управление Ростехнадзора устранить допущенное нарушение.
Суд апелляционной инстанции признал решение суда первой инстанции законным и не подлежащим отмене.
Однако суд кассационной инстанции отменил решения нижестоящих судов и пришел к выводу о необоснованности идентификации АГЗС в качестве ОПО IV класса опасности.
Он исходил из того, что согласно ГОСТ Р 52087-2003давление насыщенных паров СУГ может составлять 1,6 МПа при достижении температуры + 45°С, и фактически АГЗС будет эксплуатироваться при давлении 1,6 МПа.
По мнению суда, указание в паспорте сосуда рабочего давления 1,8 МПа также свидетельствует о потенциальной возможности работы АГЗС при давлении в сосуде 1,6 МПа и более:
«…. Фактически данный сосуд может эксплуатироваться и при давлении 1,8 МПа, а с учетом технической характеристики максимальной рабочей температуры рабочей среды +45°С давление насыщенных паров СУГ при такой температуре может достигать 1,6 МПа. Данный факт указывает на то, что опасный производственный объект должен быть отнесен к III классу опасности, а не к IV, поскольку потенциально сосуд рассчитан на эксплуатацию с давлением до 1,8 МПа включительно….
…. При совокупности изложенного, указание в паспорте рабочего давления 1,57 МПа однозначно не свидетельствует, что фактически не будет допускать давление до 1,6 МПа (включительно) и более….».
Верховный суд отказал в удовлетворении жалобы об отмене постановления суда кассационной инстанции (с судебными актами по делу и текстом общения в Верховный суд можно ознакомиться ЗДЕСЬ).
Таким образом, правоприменительная практика свидетельствует о том, что при идентификации ОПО помимо критериев, указанных в Законе о промышленной безопасности (Приложение 2) учитываются и иные факторы.
Об этом свидетельствует практика по следующим судебным делам: № А33-22652/2017; № А60-46018/2018; № А74-914/2018.
В настоящее время по данной ситуации готовится обращение в Конституционный суд России.
[1] В данной статье не рассматривается такой критерий как количество опасного вещества, находящегося на ОПО.
Данная статья является объектом интеллектуальной собственности.
Копирование и размещение материалов разрешено только с указанием источника ©.
Источник
Версия для печати
4.1 Общие требования
4.1.1 Конструкция сосудов должна быть технологичной, надежной в течение установленного в технической документации срока службы, обеспечивать безопасность при изготовлении, монтаже и эксплуатации, предусматривать возможность осмотра (в том числе внутренней поверхности), очистки, промывки, продувки и ремонта, контроля технического состояния сосуда при диагностировании, а также контроля за отсутствием давления и отбора среды перед открытием сосуда.
Если конструкция сосуда не позволяет при техническом освидетельствовании проведение осмотра (наружного или внутреннего), гидравлического испытания, то разработчик сосуда должен в технической документации на сосуд указать методику, периодичность и объем контроля сосуда, выполнение которых обеспечит своевременное выявление и устранение дефектов.
4.1.2 Срок службы сосуда устанавливает разработчик сосуда, и он указывается в технической документации.
4.1.3 При проектировании сосудов следует учитывать требования Правил перевозки грузов железнодорожным, водным и автомобильным транспортом.
Сосуды, которые не могут быть транспортированы в собранном виде, должны проектироваться из частей, соответствующих по габаритам требованиям к перевозке транспортными средствами. Деление сосуда на транспортируемые части следует указывать в технической документации.
4.1.4 Расчет на прочность сосудов и их элементов следует проводить в соответствии с ГОСТ Р 52857.1 – ГОСТ Р 52857.11, ГОСТ Р 51273, ГОСТ Р 51274, ГОСТ 30780.
Допускается использование настоящего стандарта совместно с другими международными и национальными стандартами на расчет на прочность при условии, что их требования не ниже требований российских национальных стандартов.
4.1.5 Сосуды, транспортируемые в собранном виде, а также транспортируемые части должны иметь строповые устройства (захватные приспособления) для проведения погрузочно-разгрузочных работ, подъема и установки сосудов в проектное положение.
Допускается использовать технологические штуцера, горловины, уступы, бурты и другие конструктивные элементы сосудов при подтверждении расчетом на прочность.
Конструкция, места расположения строповых устройств и конструктивных элементов для строповки, их количество, схема строповки сосудов и их транспортируемых частей должны быть указаны в технической документации.
4.1.6 Опрокидываемые сосуды должны иметь приспособления, предотвращающие самоопрокидывание.
4.1.7 В зависимости от расчетного давления, температуры стенки и характера рабочей среды сосуды подразделяют на группы. Группу сосуда определяет разработчик, но не ниже, чем указано в таблице 1.
Таблица 1 – Группы сосудов
Группа | Расчетное давление, МПа | Температура стенки, °С | Характеристика рабочей среды |
---|---|---|---|
1 | Независимо | Независимо | Взрывоопасная, пожароопасная, токсичная 1-го, 2-го, 3-го классов опасности по ГОСТ 12.1.007 |
2 | До 2,5 | Выше 400 | Любая, за исключением указанной для 1-й группы сосудов |
2,5 до 5,0 | Выше 200 | ||
5,0 и более | Независимо | ||
До 5,0 | Ниже минус 40 | ||
3 | До 2,5 | От минус 40 до 400 | |
От 2,5 до 5,0 | От минус 40 до 200 | ||
4 | До 1,6 | От минус 20 до 200 | |
5 | От вакуума до 0,07 | Независимо | Взрывобезопасная, пожаробезопасная или 4-го класса опасности по ГОСТ 12.1.007 |
Группу сосуда с полостями, имеющими различные расчетные параметры и среды, допускается определять для каждой полости отдельно.
4.1.8 Базовые диаметры сосудов рекомендуется принимать по ГОСТ 9617.
4.2 Днища, крышки, переходы
4.2.1 В сосудах применяют днища: эллиптические, полусферические, торосферические, сферические неотбортованные, конические отбортованные, конические неотбортованные, плоские отбортованные, плоские неотбортованные, плоские, присоединяемые на болтах.
4.2.2 Заготовки выпуклых днищ допускается изготовлять сварными из частей с расположением сварных швов согласно указанным на рисунке 1.
Рисунок 1 – Расположение сварных швов заготовок выпуклых днищ
Расстояния l и l1 от оси заготовки эллиптических и торосферических днищ до центра сварного шва должны быть не более 1/5 внутреннего диаметра днища. При этом для вариантов в), д), ж), и), к), л) сумма расстояний l + l1 должна быть не менее 1/5 внутреннего диаметра днища.
При изготовлении заготовок с расположением сварных швов согласно рисунку 1 м) количество лепестков не регламентируется.
4.2.3 Выпуклые днища допускается изготовлять из штампованных лепестков и шарового сегмента. Количество лепестков не регламентируется.
Если по центру днища устанавливают штуцер, то шаровой сегмент допускается не изготовлять.
4.2.4 Круговые швы выпуклых днищ, изготовленных из штампованных лепестков и шарового сегмента или заготовок с расположением сварных швов согласно рисунку 1 м, должны быть расположены от центра днища на расстоянии по проекции не более 1/3 внутреннего диаметра днища. Для полусферических днищ расположение круговых швов не регламентируется.
Наименьшее расстояние между меридиональными швами в месте их примыкания к шаровому сегменту или штуцеру, установленному по центру днища вместо шарового сегмента, а также между меридиональными швами и швом на шаровом сегменте, должно быть более трехкратной толщины днища, но не менее 100 мм по осям швов.
4.2.5 Основные размеры эллиптических днищ должны соответствовать ГОСТ 6533. Допускаются другие базовые диаметры эллиптических днищ при условии, что высота выпуклой части не менее 0,25 внутреннего диаметра днища.
4.2.6 Полусферические составные днища (см. рисунок 2) применяют в сосудах при выполнении следующих условий:
– нейтральные оси полушаровой части днища и переходной части обечайки корпуса должны совпадать; совпадение осей должно быть обеспечено соблюдением размеров, указанных в конструкторской документации;
– смещение t нейтральных осей полушаровой части днища и переходной части обечайки корпуса не должно превышать 0,5(S – S1);
– высота h переходной части обечайки корпуса должна быть не менее 3у.
Рисунок 2 – Узел соединения днища с обечайкой
4.2.7 Сферические неотбортованные днища допускается применять в сосудах 5-й группы, за исключением работающих под вакуумом.
Сферические неотбортованные днища в сосудах 1-й, 2-й, 3-й, 4-й групп и в сосудах, работающих под вакуумом, допускается применять только в качестве элемента фланцевых крышек.
Сферические неотбортованные днища (см. рисунок 3) должны:
– иметь радиус сферы R не менее 0,85D и не более D;
– привариваться сварным швом со сплошным проваром.
Рисунок 3 – Сферическое неотбортованное днище
4.2.8 Торосферические днища должны иметь:
– высоту выпуклой части, измеренную по внутренней поверхности, не менее 0,2 внутреннего диаметра днища;
– внутренний радиус отбортовки не менее 0,095 внутреннего диаметра днища;
– внутренний радиус кривизны центральной части не более внутреннего диаметра днища.
4.2.9 Конические неотбортованные днища или переходы допускается применять:
а) для сосудов 1-й, 2-й, 3-й, 4-й групп, если центральный угол при вершине конуса не более 45°. Допускается использование конических днищ и переходов с углом при вершине более 45° при условии дополнительного подтверждения их прочности расчетом по допускаемым напряжениям в соответствии с ГОСТ Р 52857.1, подраздел 8.10;
б) для сосудов, работающих под наружным давлением или вакуумом, если центральный угол при вершине конуса не более 60°.
Части выпуклых днищ в сочетании с коническими днищами или переходами применяют без ограничения угла при вершине конуса.
4.2.10 Плоские днища (см. рисунок 4), применяемые в сосудах 1-й, 2-й, 3-й, 4-й групп, следует изготовлять из поковок.
При этом следует выполнять следующие условия:
– расстояние от начала закругления до оси сварного шва не менее (D – внутренний диаметр обечайки, S – толщина обечайки);
– радиус закругления r ≥ 2,5S [см. рисунок 4а)];
– радиус кольцевой выточки r1 ≥ 2,5S, но не менее 8 мм [см. рисунок 4б)];
– наименьшая толщина днища [см. рисунок 4б)] в месте кольцевой выточки S2 ≥ 0,8S1, но не менее толщины обечайки S (S1 – толщина днища);
– длина отбортовки днищ h1 ≥ r;
– угол проточки γ должен составлять от 30° до 90°;
– зона А контролируется в направлениях Z согласно требованиям 5.4.2.
Рисунок 4 – Плоские днища
Допускается изготовление плоского днища (см. рисунок 4) из листа, если отбортовка выполняется штамповкой или обкаткой кромки листа с изгибом на 90°.
4.2.11 Основные размеры плоских днищ, предназначенных для сосудов 5-й группы, должны соответствовать ГОСТ 12622 или ГОСТ 12623.
4.2.12 Длина цилиндрического борта l (l – расстояние от начала закругления отбортованного элемента до окончательно обработанной кромки) в зависимости от толщины стенки S (см. рисунок 5) для отбортованных и переходных элементов сосудов, за исключением штуцеров, компенсаторов и выпуклых днищ, должна быть не менее указанной в таблице 2. Радиус отбортовки R ≥ 2,5S.
Рисунок 5 – Отбортованный и переходный элементы
Таблица 2 – Длина цилиндрического борта
Толщина стенки S, мм | Длина цилиндрического борта l, мм, не менее |
---|---|
До 5 включ. | 15 |
Св. 5 до 10 включ. | 2S + 5 |
Св. 10 до 20 включ. | S + 15 |
Св. 20 до 150 включ. | S/2 + 25 |
Св. 150 | 100 |
4.3 Люки, лючки, бобышки и штуцера
4.3.1 Сосуды должны быть снабжены люками или смотровыми лючками, обеспечивающими осмотр, очистку, безопасность работ по защите от коррозии, монтаж и демонтаж разборных внутренних устройств, ремонт и контроль сосудов. Количество люков и лючков определяет разработчик сосуда. Люки и лючки необходимо располагать в доступных для пользования местах.
4.3.2 Сосуды с внутренним диаметром более 800 мм должны иметь люки.
Внутренний диаметр люка круглой формы у сосудов, устанавливаемых на открытом воздухе, должен быть не менее 450 мм, а у сосудов, располагаемых в помещении, – не менее 400 мм. Размер люков овальной формы по наименьшей и наибольшей осям должен быть не менее 325×400 мм.
Внутренний диаметр люка у сосудов, не имеющих корпусных фланцевых разъемов и подлежащих внутренней антикоррозионной защите неметаллическими материалами, должен быть не менее 800 мм.
Допускается проектировать без люков:
– сосуды, предназначенные для работы с веществами 1-го и 2-го классов опасности по ГОСТ 12.1.007, не вызывающими коррозии и накипи, независимо от их диаметра, при этом следует предусмотреть необходимое количество смотровых лючков;
– сосуды с приварными рубашками и кожухотрубчатые теплообменные аппараты независимо от их диаметра;
– сосуды, имеющие съемные днища или крышки, а также обеспечивающие возможность проведения внутреннего осмотра без демонтажа трубопровода горловины или штуцера.
4.3.3 Сосуды с внутренним диаметром не более 800 мм должны иметь круглый или овальный лючок. Размер лючка по наименьшей оси должен быть не менее 80 мм.
4.3.4 Каждый сосуд должен иметь бобышки или штуцера для наполнения водой и слива, удаления воздуха при гидравлическом испытании. Для этой цели допускается использовать технологические бобышки и штуцера.
Штуцера и бобышки на вертикальных сосудах должны быть расположены с учетом возможности проведения гидравлического испытания как в вертикальном, так и в горизонтальном положениях.
4.3.5 Для крышек люков массой более 20 кг должны быть предусмотрены приспособления для облегчения их открывания и закрывания.
4.3.6 Шарнирно-откидные или вставные болты, закладываемые в прорези, хомуты и другие зажимные приспособления люков, крышек и фланцев должны быть предохранены от сдвига или ослабления.
4.4 Расположение отверстий
4.4.1 Расположение отверстий в эллиптических и полусферических днищах не регламентируется.
Расположение отверстий на торосферических днищах допускается в пределах центрального сферического сегмента. При этом расстояние от наружной кромки отверстия до центра днища, измеряемое по хорде, должно быть не более 0,4 наружного диаметра днища.
4.4.2 Отверстия для люков, лючков и штуцеров в сосудах 1-й, 2-й, 3-й, 4-й групп должны быть расположены, как правило, вне сварных швов.
Расположение отверстий допускается:
– на продольных швах цилиндрических и конических обечаек сосудов, если диаметр отверстий не более 150 мм;
– кольцевых швах цилиндрических и конических обечаек сосудов без ограничения диаметра отверстий;
– швах выпуклых днищ без ограничения диаметра отверстий при условии 100-процентной проверки сварных швов днищ радиографическим или ультразвуковым методом;
– швах плоских днищ.
4.4.3 Отверстия не разрешается располагать в местах пересечения сварных швов сосудов 1-й, 2-й, 3-й, 4-й групп.
Данное требование не распространяется на случай, оговоренный в 4.2.3.
4.4.4 Отверстия для люков, лючков, штуцеров в сосудах 5-й группы разрешается устанавливать на сварных швах без ограничения по диаметру.
4.5 Требования к опорам
4.5.1 Опоры из углеродистых сталей допускается применять для сосудов из коррозионно-стойких сталей при условии, что к сосуду приваривается переходная обечайка опоры из коррозионно-стойкой стали высотой, определяемой расчетом, выполненным разработчиком сосуда.
4.5.2 Для горизонтальных сосудов угол охвата седловой опоры, как правило, должен быть не менее 120°.
4.5.3 При наличии температурных расширений в продольном направлении в горизонтальных сосудах следует выполнять неподвижной лишь одну седловую опору, остальные опоры – подвижными. Указание об этом должно содержаться в технической документации.
4.6 Требования к внутренним и наружным устройствам
4.6.1 Внутренние устройства в сосудах (змеевики, тарелки, перегородки и др.), препятствующие осмотру и ремонту, как правило, должны быть съемными.
При использовании приварных устройств следует выполнять требования 4.1.1.
4.6.2 Внутренние и наружные приварные устройства необходимо конструировать так, чтобы были обеспечены удаление воздуха и полное опорожнение аппарата при гидравлическом испытании в горизонтальном и вертикальном положениях.
4.6.3 Рубашки и змеевики, применяемые для наружного обогрева или охлаждения сосудов, могут быть съемными и приварными.
4.6.4 Все глухие части сборочных единиц и элементов внутренних устройств должны иметь дренажные отверстия для обеспечения полного слива (опорожнения) жидкости в случае остановки сосуда.
<< назад / к содержанию ГОСТа Р 52630-2012 / вперед >>
Источник