Подрезы в сварных швах сосудов 1 и 2 групп
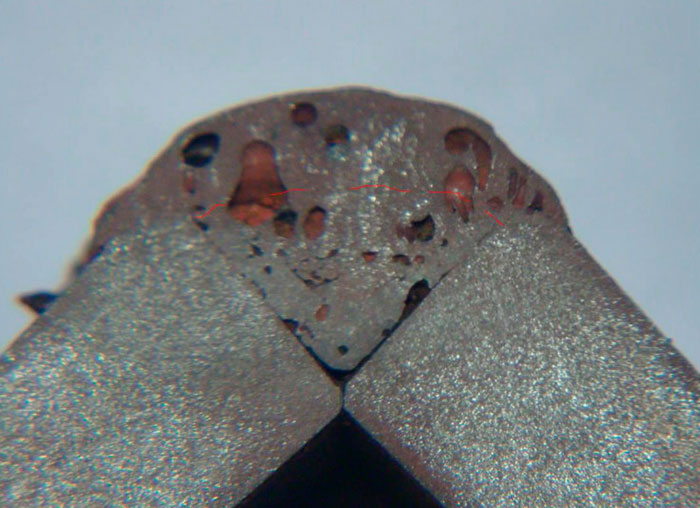
Изъян, называемый подрезом, это углубление, образующееся рядом со швом. Из-за уменьшения толщины металла на месте дефекта снижается прочность сварного соединения. Внешне подрезы выглядят как усадочные канавки по всей длине шва или на отдельных участках.
Причины возникновения
Чаще всего изъяны, называемые подрезами, получаются у неопытных сварщиков при неправильном выборе тока. Также причиной могут стать:
- плохая смачиваемость металла заготовок;
- изменение длины дуги при наложении сварного шва;
- значительные отклонения электрода от оси стыка;
- неудобное для сварки расположение заготовок;
- некачественная подготовка кромок;
- завышение скорости проведения работы;
- неправильный угол наклона электрода.
Способы предотвращения подрезов сварных швов
Риск образования дефектов сводится к минимуму, если подготовка стыка выполнена в полном объеме, а сварка проводится с соблюдением технологических правил:
- Чтобы не было подреза на сварном шве, заготовки для улучшения смачиваемости предварительно подогревают. Это улучшает растекание жидкого металла по ширине стыка, снижает вероятность образования очагов напряженности.
- При неправильном положении электрода дефекты появляются из-за неравномерного нагрева кромок. При соединении разных по толщине деталей большую часть тепла направляют на толстую кромку. Углеродистую сталь сваривают, наклоняя электрод углом вперед.
- При повышенной скорости сварки металл в центральной части шва быстро остывает, создавая по краям усадочные канавки. Однако чрезмерное снижение скорости не избавляет от проблемы. Поэтому оптимальное значение выбирают в соответствии с маркой свариваемого железа.
- Вероятность образования огрехов значительно возрастает при неверном выборе защитного газа. Углеродистую сталь сваривают в среде из смеси инертного и углекислого газа. Для работы с другими материалами тип газа выбирают в зависимости от вида свариваемого металла.
- У неопытных сварщиков дефекты чаще всего появляются при нарушении правил проведения сварочных работ. Когда диаметр электрода меньше ширины шва, приходится делать поперечные движения с большой амплитудой. После такой сварки образование подрезов неизбежно. Поэтому по возможности нужно уменьшать ширину соединения или сваривать его несколькими проходами. Чтобы не было перегрева основного металла, рабочий ток устанавливают в соответствии с толщиной заготовок. Сварку выполняют короткой дугой с постоянной скоростью.
- При наложении вертикальных швов огрехи образуются из-за сложности заполнения пространства стыка расплавленным металлом. Поэтому соединение заготовок, если есть такая возможность, следует выполнять в горизонтальном положении с меньшим расходом электродов. Чтобы исключить образование подрезов, угловые швы накладывают способом «в лодочку».
- Лучшим способом для предотвращения подрезов считается создание сварных соединений инверторами с функциями MIG/MAG. Кроме усадочных канавок эти аппараты позволяют избежать появления других изъянов на сварных швах.
Устранение подрезов
Для устранения такого дефекта участок изъяна очищают от шлака и грязи, а затем заваривают тонким швом. Желательно, чтобы у электрода был высокий показатель смачиваемости. Однако при этом увеличивается потребность в расходных материалах. Чтобы избежать непредусмотренных затрат, подрезы в сварных швах устраняют аргонодуговой сваркой неплавящимся электродом. После нагрева огрех замазывают расплавленным металлом. Однако такой метод исправления не рекомендуется, если соединение было выполнено другим видом сварки, так как внутри могут быть поры, посторонние включения и пр. Чтобы прочность не уменьшалась, участки сварного соединения с многочисленными подрезами вырубают или вырезают до основного металла и переваривают. Размер удаляемой части должен превышать длину изъяна на 1- 2 см с каждой стороны.
После исправления сварные соединения проходят повторную проверку. При выявлении дефектов отправляются на доработку. Один и тот же участок допускается исправлять в зависимости от сорта стали не более 2 — 3 раз. Это связано с изменением характеристик металла после повторной сварки. При исправлении следует учитывать, что при усилении сварного соединения снижается стойкость к вибрации.
Допускаются ли подрезы в сварных швах
Смонтированные конструкции принимают в эксплуатацию, если размеры подрезов в сварных швах не превышают указанных в ГОСТ30242-97 норм. Окончательное решение принимают после рассмотрения следующих факторов:
- размер конструкции и длина шва;
- как дефект влияет на прочность изделия с учетом начального и остаточного напряжения;
- вид и параметры изъяна;
- характеристики подреза по текучести, сопротивляемости, вязкости, пластичности;
- в каких условиях будет эксплуатироваться смонтированная конструкция;
- степень влияния дефекта на функциональность.
Прибор для замера изъянов должен иметь необходимый предел измерения. Поэтому следует внимательно изучить инструкцию, чтобы знать его возможности. Прибором с пределом до 5 мм не получится с необходимой точностью измерить дефект до 2 мм.
Даже у многоопытных сварщиков случаются подрезы, поэтому новичкам не следует расстраиваться, если не все швы получаются идеальными. Чтобы снизить количество огрехов в период обучения сварку лучше выполнять многофункциональными инверторами. Дополнительные опции такого оборудования компенсируют недостаток опыта.
Источник
Металлоконструкции, сваренные из металла, востребованы в разных сферах жизнедеятельности. Однако во время выполнения сварочных работ могут возникать разного рода дефекты сварных швов. Они сокращают возможный срок службы соединения и снижают уровень безопасности готового изделия.
Виды дефектов сварных швов
Все допуски по размерам шва регламентированы требованиями ГОСТа для каждого из видов сварки. Любые отклонения показаний от утвержденных нормативов принято считать дефектами. Они могут быть последствием ошибок в процессе как подготовки, так и выполнения сварочных работ.
Большинство изъянов сварочного соединения отрицательно сказываются на его прочностных характеристиках. Все дефекты делятся на три группы:
- наружные. Основными показателями являются неправильная форма стыка, трещины, наплывы, кратеры, подрезы шва, прожоги и прочие визуальные признаки, которые можно обнаружить на поверхности. Они видны при тщательном визуальном осмотре и только некоторые можно заметить с первого взгляда;
- внутренние. Дефекты представляют собой неполное или неравномерное сплавление металлов, трещины или пористость в структуре, наличие посторонних включений – шлак, оксид, неметаллические примеси; другие, находящиеся внутри шва, изъяны;
- сквозные. Трещины, подрезы, прожоги и прочие повреждения, которые носят сквозной характер и видные с обеих сторон.
Любые дефекты являются основанием для выбраковки работы и должны быть устранены. Это правило особенно актуально для металлоконструкций несущего плана – каркасов, рам, обрешеток и т.п. Они должны быть сварены безупречно, чтобы выдерживать предполагаемые нагрузки. В противном случае конструкции могут служить источником опасности для окружающих.
Классификация дефектов сварных соединений
Далеко не в каждом случае получается добиться идеального качества сварного соединения. При желании можно найти отклонения от установленных требований. Полностью классификация сварных соединений изложена в пунктах ГОСТа 30242-97. Документ содержит информацию обо всех возможных изъянах. Из них можно выделить часть, которые чаще других встречаются при контрольном осмотре соединительных стыков.
Трещины
Наибольшее негативное влияние на качество сварного шва оказывают трещины. Потенциально они наиболее опасны, поскольку могут стать причиной быстрого разрушения всей конструкции, что в свою очередь может привести к трагедии.
Появляются трещины по разным причинам:
- стыки расположены неправильно;
- место сварки было резко охлаждено;
- неправильно подобраны расходные материалы;
- металл кристаллизировался вследствие избыточно высокой температуры.
По способу образования трещины могут быть продольными, поперечными или радиальными, а по размеру принято различать макро- и микротрещины. Вне зависимости от вида, причин и способа образования трещина является недопустимым дефектом.
Подрезы
Визуально изъян представляет собой продольное углубление с наружной части шва. Из-за подреза уменьшается сечение шва и образуется внутреннее напряжение соединения. Прочность такого шва вызывает большие сомнения. Основная причина образования дефекта – завышенный показатель сварочного тока. Чаще всего подрезы характерны для горизонтальных швов.
Наплывы
Избыточный расплав натекает на поверхность заготовки, остывает и образует ложный валик. Это наплыв, не имеющий прочного сплавления с рабочей поверхностью. Чаще всего дефект образуется при горизонтальной сварке стыковых или угловых швов. Причиной их образования является недостаточный прогрев основного металла, из-за избытка присадочного материала или окалин на кромках стыкуемых поверхностей.
Прожоги
Изъян представляет собой сквозное отверстие, которое образуется из-за вытекания металла из сварочной ванны. Как правило, из обратной стороны образуется наплыв. Провоцирует прожог слишком медленное перемещение электрода по линии стыка, слишком большой ток, недостаточная толщина прокладки или же неплотное ее прилегание, большой зазор между деталями.
Непровары
Если между швов и основным металлом есть участки, где видно несплавление между ними, то это непровар. То есть, основной металл не прогрелся как следует, чтобы образовать с расплавом единое целое. Такой дефект сильно понижает прочностные характеристики соединения и все конструкции в целом. Причиной непровара может быть слишком высокая скорость перемещения электрода, плохая предварительная подготовка кромок, присутствие окалины, ржавчины и прочих загрязнений на поверхности соединяемых заготовок.
Кратеры
Небольшие углубления в сварном валике образуются в результате разрыва сварочной дуги. Изъяны приводят к уменьшению поперечного сечения стыка, что снижает степень его прочности. вторичная опасность кратера заключается в том, что его дно может иметь дополнительные рыхлые включения, приводящие к появлению трещин.
Свищи
Изъяны представляют собой поверхностные дефекты в виде полостей. Они снижает прочность стыка и дополнительно опасны тем, что могут провоцировать образование трещин. Свищи характеризуются произвольной формой, могут образовываться как на внешней стороне, так и на внутренней.
Поры в сварном шве
В процессе сварки могут образовываться наполненные газами поры. Причиной их возникновения являются разные загрязнения на поверхности заготовки, высокая скорость перемещения электрода, слишком высокое содержание углерода в присадочном материале.
Посторонние включения
Качество шва значительно снижается из-за посторонних включений – шлаковых, флюсовых, оксидных, вольфрамовых и прочих. Основной причиной, которая их вызывает, является неправильно выбранный режим сварки.
Причины возникновения дефектов сварных швов
Любой дефект образуется вследствие определенного фактора. Существуют разные причины образования дефектов сварного шва:
- во время работ применялись некачественные расходные материалы;
- не соблюдалась технология выполнения сварочных работ;
- низкого качества металл, используемый для создания сварной конструкции;
- неисправность оборудования или некачественная его работа;
- неправильно выбранный режим сварки;
- допущены технологические ошибки из-за низкой квалификации специалиста.
Чтобы получить металлоконструкцию высокого качества, требуется строгое соблюдения технологических параметров и норм сваривания, привлекать к работе специалистов с достаточным уровнем квалификации.
Методы выявления дефектов
Для выявления дефектов сварного шва применяются разные методы:
- замеры стыков и визуальный осмотр;
- проверка соединений на герметичность;
- поиск дефекта с использованием специальных приборов;
- лабораторные испытания образцов на прочность.
Визуальное определение качества сварного шва выполняется только после тщательной очистки его поверхности от шлака, устранения разных загрязнений и застывших брызг металла. Проверяются размеры, форма, наличие дефектов – прожогов, свищей, трещин, кратеров и прочих изъянов.
Благодаря испытаниям на герметичность удается определить наличие или отсутствие дефектов трубопроводов – пор, трещин, непроваров. На герметичность конструкции проверяются такими способами:
- обдувание воздухом;
- наполнение водой под давлением;
- обработка керосином.
При обнаружении дефекта требуется дополнительная обработка с целью его устранения.
Способы устранения дефектов сварных соединений
Вне зависимости от задействованного оборудования – инвертор, классический аппарат, трансформатор и прочее – образование дефектов не исключено. Принято различать так называемые допустимые и недопустимые дефекты сварки. В зависимости от типа и сложности изъянов определяется пригодность готового изделия к эксплуатации.
Не допущенные к использованию конструкции направляются на доработку. Каким способом будет устраняться дефект, зависит от типа изъяна:
- прожог заваривается после тщательной зачистки сварного соединения;
- подрезу устраняются путем наложения тонкого наплава по всей длине их образования;
- участок с трещиной рассверливается, тело шва вырубается, поверхность зачищается и обезжиривается. После этого углубление заваривается;
- непровары вырезаются и повторно завариваются;
- свищи и кратеры устраняются по одной схеме. Прежде всего все вырезается до основного металла. После этого стык варится по-новому;
- наплывы следует аккуратно срезать, проверив при этом есть ли непровары;
- деформированные участки выравниваются прогревом или же механическим путем;
- любой из дефектов, подразумевающий наличие посторонних включений, устраняется путем вырезания шва (участка) и наложением нового.
В случае, когда в процессе контроля обнаруживаются дефекты технологического характера соединений труб, то исправление выполняется одним из методов:
- механическим путем без сваривания;
- механическим путем в сочетании с завариванием дефектного участка;
- вырезание участка трубопровода, содержащего технологический дефект;
- шов полностью удаляется и стык проваривается по-новому.
Прочность и герметичность сетей газоснабжения восстанавливается дуговой сваркой. Применение газосварочных установок не допускается.
Методы контроля сварных соединений
Само собой разумеется, что любые дефекты сварного соединения увеличивают риск разрушения конструкции. Чтобы такую вероятность свести к минимуму, следует внимательно проверять качество сварных соединений. Весь процесс выполняется поэтапно:
- предварительный. Проверяется качество металла и расходных материалов;
- контроль в процессе выполнения сварочных работ. Постоянно проверяется режим сварки, работа оборудования, осматриваются и измеряются швы. В случаях, когда обнаруживаются отклонения от стандартов, дефекты сразу исправляются;
- прием готовой конструкции. Визуальным осмотром определяется наличие внешних изъянов. При необходимости проводятся лабораторные и испытательные проверки.
Применяемые сегодня методы контроля делятся на две группы – неразрушающие и разрушающие. Для выявления дефектов готовых конструкций применяются, как правило, неразрушающие методы контроля:
- визуальный осмотр;
- проверка ультразвуком (дефектоскопия);
- контроль при помощи магнитного поля;
- дефектоскопия цветная;
- дефектоскопия радиационная;
- дефектоскопия капиллярная;
- контроль на проницаемость;
- другие методы.
Разрушающий контроль используется в отношении отобранных для этого образцов. Он позволяет установить параметры прочности сварного шва и зоны термического влияния. В контроле задействованы химические, механические и металлографические методы проверки.
Источник
Версия для печати
6.10 Требования к качеству сварных соединений
6.10.1 Механические свойства сварных соединений должны быть не ниже норм, указанных в таблице 14.
Таблица 14
Наименование показателя | Минимальные нормы механических свойств сварных соединений | ||||
---|---|---|---|---|---|
для углеродистых сталей | для низколегированных марганцовистых и марганцево-кремнистых сталей | для хромистых, хромомолибденовых и хромованадиево-вольфрамовых сталей | для аустенитно-ферритных сталей | Для аустенитных сталей | |
Временное сопротивление разрыву при температуре плюс 20 °С | Не ниже нижнего значения временного сопротивления разрыву основного металла по стандарту или техническим условиям для данной марки стали | ||||
Минимальная ударная вязкость, Дж/см2 (кгс·м/см2): | |||||
– при температуре + 20 °С | |||||
на образцах KCV | 35 (3,5) | 35 (3,5) | 35 (3,5) | 30 (3,0) | – |
на образцах KCU | 50 (5,0) | 50 (5,0) | 50 (5,0) | 40 (4,0) | – |
– при температуре ниже минус 20 °С | |||||
на образцах KCV | 20 (2,0) | 20 (2,0) | 20 (2,0) | 20 (2,0) | – |
на образцах KCU | 30 (3,0) | 30 (3,0) | 30 (3,0) | 30 (3,0) | – |
Минимальный угол изгиба, …°: – при толщине не более 20 мм | |||||
100 | 80 | 50 | 80 | 100 | |
– при толщине более 20 мм | 100 | 60 | 40 | 60 | 100 |
Твердость металла шва сварных соединений НВ, не более | – | – | 240 | 220 | 200 |
Просвет между сжимаемыми поверхностями при сплющивании стыковых соединений труб | Не ниже норм установленных НД на трубы | ||||
Примечания 1. Твердость металла шва в коррозионно-стойком слое сварных соединений сосудов из двухслойных сталей не должна превышать 220 НВ. 2. Показатели механических свойств сварных соединений по временному сопротивлению разрыву и углу изгиба определяют как среднеарифметическое результатов испытаний отдельных образцов. Общий результат считают неудовлетворительным, если хотя бы один из образцов показал значение временного сопротивления разрыву более чем на 7 % и угла изгиба более чем на 10 % ниже норм, указанных в данной таблице. При испытании на ударный изгиб результат считают неудовлетворительным, если хотя бы один из образцов показал значение ниже норм, указанных в данной таблице. Допускается на одном образце (KCU) при температурах минус 40 °С и ниже получение значения ударной вязкости не менее 25 Дж/см2 (2,5 кгс·м/см2). 3. Виды испытаний и гарантированные нормы механических свойств по временному сопротивлению разрыву и ударной вязкости стыковых сварных соединений типа «лист+поковка», «лист+литье», «поковка+поковка», «поковка+труба», «поковка+сортовой прокат» должны соответствовать требованиям, предъявляемым к материалу с более низкими показателями механических свойств. Контроль механических свойств, а также металлографическое исследование или испытание на стойкость против межкристаллитной коррозии образцов этих соединений предусматриваются разработчиком технической документации. Для сварных соединений типа «лист+поковка», «лист+литье», «поковка+поковка», «поковка+труба», «поковка+сортовой прокат» угол изгиба должен быть не менее: – 70° – для углеродистых сталей и сталей аустенитного класса; – 50° – для низколегированных марганцовистых и марганцево-кремнистых сталей, высоколегированных сталей аустенитно-ферритного класса; – 30° – для низколегированных и среднелегированных (хромистых и хромомолибденовых) сталей и высоколегированных сталей ферритного класса. 4. Твердость металла шва сварных соединений из стали марки 12ХМ, выполненных ручной электродуговой сваркой ванадийсодержащими электродами, должна быть не более 260 НВ при условии, что относительное удлинение металла шва будет не менее 18 %. Твердость металла шва сварных соединений из стали марки 15Х5МУ должна быть не более 270 НВ. |
6.10.2 В сварных соединениях не допускаются следующие поверхностные дефекты:
– трещины всех видов и направлений;
– свищи;
– подрезы;
– наплывы, прожоги и незаплавленные кратеры;
– смещение и совместный увод кромок свариваемых элементов свыше норм, предусмотренных настоящим стандартом;
– несоответствие формы и размеров швов требованиям стандартов, технических условий или проекта;
– поры, выходящие за пределы норм, установленных таблицей 15;
– чешуйчатость поверхности и глубина впадин между валиками шва, превышающие допуск на усиление шва по высоте.
Допускаются местные подрезы в сосудах 3, 4-й и 5а, 5б групп, предназначенных для работы при температуре свыше 0 °С. При этом их глубина не должна превышать 5 % толщины стенки, но не более 0,5 мм, а протяженность – 10 % длины шва.
Допускаются в сварных соединениях из сталей и сплавов марок 03X21Н21М4ГБ, 03ХН28МДТ, 06ХН28МДТ отдельные микронадрывы протяженностью не более 2 мм.
Таблица 15. Нормы допустимых пор, выявляемых при визуальном контроле сварных соединений
Номинальная толщина наиболее тонкой детали, мм | Допустимый максимальный размер дефекта, мм | Допустимое число дефектов на любые 100 мм шва |
---|---|---|
От 2 до 3 включ. | 0,5 | 3 |
Св. 3 до 4 включ. | 0,6 | 4 |
Св. 4 до 5 включ. | 0,7 | 4 |
Св. 5 до 6 включ. | 0,8 | 4 |
Св. 6 до 8 включ. | 1,0 | 5 |
Св. 8 до 10 включ. | 1,2 | 5 |
Св. 10 до 15 включ. | 1,5 | 5 |
Св. 15 до 20 включ. | 2,0 | 6 |
Св. 20 до 40 включ. | 2,5 | 7 |
Св. 40 | 2,5 | 8 |
6.10.3 В сварных соединениях не допускаются следующие внутренние дефекты:
– трещины всех видов и направлений, в том числе микротрещины, выявленные при металлографическом исследовании;
– свищи;
– смещение основного и плакирующего слоев в сварных соединениях двухслойных сталей выше норм, предусмотренных настоящим стандартом;
– непровары (несплавления), расположенные в сечении сварного соединения;
– поры, шлаковые и вольфрамовые включения, выявленные радиографическим методом, выходящие за пределы норм, установленных допустимым классом дефектности сварного соединения по ГОСТ 23055-78 в соответствии с таблицей 16, или выявленные ультразвуковым методом по НД.
Таблица 16. Классы дефектности сварного соединения
Вид сварного соединения | Группа сосуда | |||
---|---|---|---|---|
1, 2, 3 | 4 | 5а | 5б | |
Класс дефектности по ГОСТ 23055-78 | ||||
Стыковые | 3 | 4 | 5 | 6 |
Угловые, тавровые | 4 | 5 | 5 | 6 |
Нахлесточные | 5 | 6 | 6 | 7 |
Примечание. Оценку единичных дефектов (пор и включений) по ширине (диаметру) при толщине свариваемых элементов до 45 мм, а также цепочек независимо от толщины свариваемых элементов допускается проводить по нормам 4-го класса вместо 3-го класса, 5-го класса вместо 4-го класса, 6-го класса вместо 5-го класса, 7-го класса вместо 6-го класса. Оценку единичных пор и включений для кольцевых сварных соединений толщиной не более 10 мм, выполняемых ручной электродуговой сваркой, допускается проводить по классу 5.
6.11 Термическая обработка
6.11.1 Сосуды (сборочные единицы, детали) из углеродистых и низколегированных сталей (за исключением сталей, перечисленных в 6.11.3), изготовленные с применением сварки, штамповки или вальцовки, подлежат обязательной термической обработке, если:
а) толщина стенки цилиндрического или конического элемента, днища, фланца или патрубка сосуда в месте их сварного соединения более 36 мм для углеродистых сталей и более 30 мм для низколегированных марганцовистых и марганцево-кремнистых сталей (марок 16ГС, 09Г2С, 17Г1С, 10Г2 и др.);
б) номинальная толщина стенки S цилиндрических или конических элементов сосуда (патрубка), изготовленных из листовой стали вальцовкой (штамповкой), превышает значение, вычисленное по формуле
S = 0,009(D + 1200),
где D – минимальный внутренний диаметр элемента, мм;
в) отношение номинальной толщины к номинальному внутреннему радиусу обечайки или к наименьшему радиусу кривизны днища превышает 0,02. Данное требование не распространяется на отбортованные рубашки;
г) сосуды (сборочные единицы, детали) предназначены для эксплуатации в средах, вызывающих коррозионное растрескивание (жидкий аммиак, аммиачная вода, растворы едкого натрия и калия, азотнокислого натрия, калия, аммония, кальция, этаноламина, азотной кислоты и др.), и об этом есть указание в проекте;
д) днища сосудов и их элементов независимо от толщины изготовлены холодной штамповкой или холодным фланжированием.
6.11.2 Сварные соединения из углеродистых, низколегированных марганцовистых, марганцево-кремнистых и хромомолибденовых сталей, выполненные электрошлаковой сваркой, подлежат нормализации и высокому отпуску. Для кольцевых швов сосудов из стали марки 12ХМ допускается проводить только высокий отпуск без нормализации при условии выполнения многослойной электрошлаковой сварки по документации, согласованной с разработчиком проекта. Для кольцевых швов сосудов толщиной до 100 мм, предназначенных для работы при температуре стенки не ниже минус 20 °С для стали марки 20К, не ниже минус 40 °С для сталей марок 16ГС, 20ЮЧ, не ниже минус 55 °С для стали марки 09Г2С и толщиной до 60 мм, предназначенных для работы при температуре стенки не ниже минус 60 °С для стали 09Г2С, допускается осуществлять только высокий отпуск без нормализации при условии комбинированного способа выполнения сварного соединения – автоматической сварки под флюсом и электрошлаковой сварки с регулированием термического цикла.
При электрошлаковой сварке заготовок штампуемых и вальцуемых элементов из сталей марок 16ГС, 09Г2С и 10Г2С1, предназначенных для работы при температуре не ниже минус 40 °С, нормализация может быть совмещена с нагревом под штамповку с окончанием штамповки при температуре не ниже 700 °С.
6.11.3 Сварные сосуды (сборочные единицы, детали) из сталей марок 12МХ, 12ХМ, 15ХМ, 12Х1МФ, 10Х2М1А-А, 10Х2ГНМ, 15Х2МФА-А, 1Х2М1, 15Х5, Х8, 15Х5М, 15Х5ВФ, 12Х8ВФ, Х9М и из двухслойных сталей с основным слоем из сталей марок 12МХ, 12ХМ, 20Х2М следует подвергать термической обработке по режиму, оговоренному в проекте.
6.11.4 Сосуды (сборочные единицы, детали) из сталей марок 08Х18Н10Т, 08Х18Н12Б и других аустенитных сталей, стабилизированных титаном или ниобием, предназначенные для работы в средах, вызывающих коррозионное растрескивание, а также при температурах свыше 350 °С в средах, вызывающих межкристаллитную коррозию, следует подвергать термической обработке по режиму, оговоренному в проекте.
6.11.6 Необходимость и вид термической обработки сосудов (сборочных единиц, деталей) из двухслойной стали следует определять в соответствии с требованиями 6.11.1 [перечисления а), б), в), д)], 6.11.2, 6.11.3.
При определении толщины свариваемого элемента принимается толщина основного слоя двухслойной стали.
При наличии в проекте требований на стойкость против межкристаллитной коррозии технология сварки и режим термообработки сварных соединений двухслойных сталей должны обеспечивать стойкость сварных соединений коррозионно-стойкого слоя против межкристаллитной коррозии.
6.11.6 Днища и детали из углеродистых и низколегированных марганцево-кремнистых сталей, штампуемые (вальцуемые) в горячую с окончанием штамповки (вальцовки) при температуре не ниже 700 °С, а также днища и детали из аустенитных хромоникелевых сталей, штампуемых (вальцуемых) при температуре не ниже 850 °С, термической обработке не подвергаются, если к указанным материалам не предъявлены другие требования в приложении А.
Днища и другие штампуемые (вальцуемые) в горячую элементы, изготовляемые из сталей марок 09Г2С, 10Г2С1, работающие при температуре от минус 40 °С до минус 70 °С, должны подвергать термической обработке – нормализации или закалке и высокому отпуску.
Днища и другие элементы из низколегированных сталей марок 12ХМ и 12МХ, штампуемые (вальцуемые) в горячую с окончанием штамповки (вальцовки) при температуре не ниже 800 °С, допускается подвергать только отпуску (без нормализации).
Технология изготовления днищ и других штампуемых элементов должна обеспечивать необходимые механические свойства, указанные в стандартах или технических условиях, а при наличии требования в проекте и стойкость против межкристаллитной коррозии.
6.11.7 Днища и другие элементы, выполненные из коррозионно-стойких сталей аустенитного класса методом холодной штамповки или холодным фланжированием, должны подвергать термической обработке (аустенизации или стабилизирующему отжигу), если они предназначены для работы в средах, вызывающих коррозионное растрескивание. В остальных случаях термообработку допускается не проводить, если относительное удлинение при растяжении в исходном состоянии металла не менее 30 % при степени деформации в холодном состоянии не более 15 %.
6.11.8 Гнутые участки труб из углеродистых и низколегированных сталей подлежат термообработке, если отношение среднего радиуса изгиба к номинальному наружному диаметру трубы составляет менее 3,5, а отношение номинальной толщины стенки трубы к ее номинальному диаметру превышает 0,05.
6.11.9 Приварку внутренних и наружных устройств к сосудам, подвергаемым термической обработке, следует проводить до термической обработки сосуда.
Допускается приварка внутренних и наружных устройств без последующей термической обработки к сосудам, термообработанным в соответствии с 6.11.1 [перечисления а), б)] при условии, что катет сварного шва не более 8 мм.
Допускается приварка наружных устройств на монтажной площадке к специальным накладкам, приваренным к корпусу сосуда и прошедшим вместе с ним термическую обработку на предприятии-изготовителе без последующей термической обработки монтажных сварных швов.
6.11.10 Допускается местная термическая обработка сварных соединений сосудов, при проведении которой должны быть обеспечены равномерный нагрев и охлаждение по всей длине шва и прилегающих к нему зон основного металла.
6.11.11 Объемную термическую обработку проводят в печах или нагревом сосуда (сборочной единицы, детали) путем ввода во внутреннюю полость теплоносителя.
При этом должны быть проведены мероприятия, предохраняющие сосуд (сборочную единицу, деталь) от деформаций, вызванных местным перегревом, неправильной установкой сосуда, действием собственной массы.
6.11.12 Свойства металла обечаек, днищ, патрубков, решеток после всех циклов термической обработки должны соответствовать требованиям настоящего стандарта.
<< назад / в начало / вперед >>
15 Мая 2012 г.
Источник